Wire Bonding IC Substrates Manufacturer.As a leading Wire Bonding IC Substrates manufacturer, we specialize in producing high-quality substrates that ensure reliable and efficient interconnections for integrated circuits. Our advanced manufacturing processes and stringent quality control measures guarantee superior performance and durability, catering to the diverse needs of the electronics industry. Trust us to deliver cutting-edge solutions for your wire bonding IC substrate requirements.
Wire bonding IC substrates are integral components in the packaging of integrated circuits (ICs). These substrates facilitate the electrical connections between the IC and the package leads or other components through wire bonding, a process that uses fine wires to connect the semiconductor die to the external circuitry. This article explores the properties, structure, materials, manufacturing processes, applications, advantages, and frequently asked questions (FAQs) related to wire bonding IC substrates.
Structure of Wire Bonding IC Substrates
The structure of wire bonding IC substrates is meticulously designed to ensure reliable electrical connections and robust mechanical support:
The substrate typically consists of high-performance materials such as FR-4, BT (Bismaleimide-Triazine) resin, or ceramic, chosen for their mechanical strength, thermal stability, and electrical insulation properties.
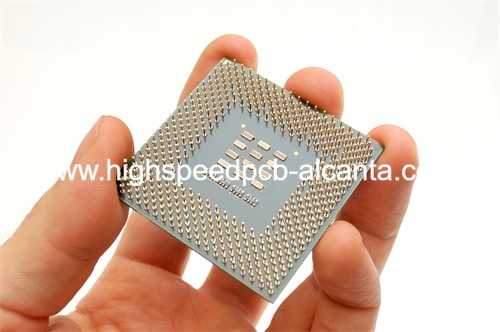
Wire Bonding IC Substrates Manufacturer
Copper is the primary material used for conductive layers. These layers are patterned to form the necessary circuit traces and pads for wire bonding.
A designated area on the substrate where the semiconductor die is attached using adhesives or solder. This area must have excellent thermal conductivity to dissipate heat generated by the IC.
Specific areas on the substrate designed for wire bonding. These pads are typically coated with a finish such as gold to enhance bondability and prevent oxidation.
High-performance dielectric materials separate the conductive layers, ensuring electrical isolation and maintaining signal integrity.
Dedicated planes within the substrate provide stable reference points for signals and distribute power efficiently across the IC.
Materials Used in Wire Bonding IC Substrates
Key materials used in wire bonding IC substrates include:
A widely used, cost-effective material with good mechanical strength and thermal stability, suitable for many electronic applications.
Known for its excellent thermal and mechanical properties, BT resin is often used in high-reliability applications requiring robust performance.
Provides superior thermal conductivity and electrical insulation, making it ideal for high-power and high-frequency applications.
Used for conductive traces and bonding pads due to its excellent electrical conductivity and reliability.
Gold, ENIG (Electroless Nickel Immersion Gold), and OSP (Organic Solderability Preservatives) are common finishes applied to bonding pads to enhance wire bonding performance and prevent oxidation.
Manufacturing Process of Wire Bonding IC Substrates
The manufacturing process for wire bonding IC substrates involves several precise steps:
Selection and preparation of base materials and conductive layers based on performance requirements.
Stacking and bonding multiple layers of conductive and dielectric materials under controlled conditions to form a stable substrate.
Using photolithography and chemical etching to define the circuit patterns and bonding pads.
Creating vias to connect different layers of the substrate, enabling complex routing and high-density designs.
Electroplating copper onto the substrate and inside vias to establish reliable electrical connections.
Applying protective coatings to bonding pads and exposed copper surfaces to enhance bondability and protect against oxidation.
Attaching the semiconductor die to the designated area on the substrate using adhesives or solder.
Using fine wires, typically gold or aluminum, to connect the die bonding pads to the substrate bonding pads, establishing electrical connections.
Rigorous testing for electrical performance, bond integrity, and adherence to design specifications.
Applications of Wire Bonding IC Substrates
Wire bonding IC substrates are used in a wide range of applications, including:
Smartphones, tablets, and other portable devices that require compact, reliable IC packaging.
Engine control units, sensors, and infotainment systems that demand high reliability and robust performance.
Base stations, network equipment, and other communication devices that require high-frequency signal transmission and reliable connections.
Control systems, sensors, and other electronic components used in manufacturing and process automation.
Diagnostic equipment, imaging systems, and other medical devices that require precise and reliable electronic components.
Advantages of Wire Bonding IC Substrates
Wire bonding IC substrates offer several significant advantages:
Wire bonding is a cost-effective method for making electrical connections in IC packaging, suitable for high-volume production.
Robust construction and reliable bonding techniques ensure long-term performance and durability in demanding applications.
Suitable for a wide range of applications across various industries, from consumer electronics to medical devices.
Effective heat dissipation through substrate materials and design features, ensuring stable operation under high-power conditions.
Supports complex and high-density routing, enabling advanced semiconductor designs.
FAQ
What materials are typically used for wire bonding IC substrates, and why?
Wire bonding IC substrates commonly use materials like FR-4, BT resin, and ceramic for their excellent thermal stability, mechanical strength, and electrical insulation properties. These materials are essential for maintaining reliability and performance in various applications.
How do wire bonding IC substrates differ from other types of IC substrates?
Wire bonding IC substrates are specifically designed for wire bonding techniques, with bonding pads and surface finishes optimized for this process. Other types of IC substrates, such as flip-chip substrates, may use different interconnection methods and materials tailored to their specific requirements.
What industries benefit the most from the use of wire bonding IC substrates?
Industries such as consumer electronics, automotive electronics, telecommunications, industrial automation, and medical devices benefit significantly from the use of wire bonding IC substrates due to their reliability, cost-effectiveness, and versatility.
How are wire bonding IC substrates tested to ensure reliability?
Wire bonding IC substrates undergo rigorous testing processes, including electrical testing for signal integrity and performance, bond integrity testing, and thermal cycling to ensure they meet stringent performance and durability standards required for high-reliability applications.