Ultrathin PCB Manufacturer.A leading ultrathin PCB manufacturer, renowned for its precision engineering and cutting-edge technology, specializes in crafting printed circuit boards of unparalleled slimness and superior performance. With state-of-the-art facilities and a team of skilled experts, they meticulously design and fabricate PCBs to meet the demanding requirements of modern electronic devices. Their commitment to innovation and quality ensures that each product delivers exceptional reliability and efficiency. From ultra-compact wearables to sleek consumer electronics, their ultrathin PCBs empower the next generation of technology, driving progress and innovation across industries.
What is ultra-thin PCB?
Ultra-thin PCB (Printed Circuit Board) is a special type of printed circuit board, which is characterized by extremely thin thickness, usually less than half the thickness of traditional PCB, sometimes even less than 0.4 mm. This extreme thinness makes ultra-thin PCBs play a vital role in today’s electronic devices, especially those that require lightweight, thin designs. Ultra-thin PCBs offer some significant differences and advantages over traditional PCBs.
First, ultra-thin PCBs use more advanced materials and manufacturing processes. Traditional PCBs usually use glass fiber reinforced epoxy resin (FR-4) as the base material, while ultra-thin PCBs often use flexible materials such as polyimide (PI) or liquid crystal polymer (LCP) as the base material, which makes ultra-thin PCBs Thin PCBs have better performance in areas such as bending and folding.
Secondly, the design and manufacturing process of ultra-thin PCBs is more complex. Because ultra-thin PCBs are extremely thin, they require more precise control and operation during the design and manufacturing process. From component layout to circuit routing to optimization of the stacked structure, every step requires engineers to carefully design and adjust to ensure the stability and performance of the final product.
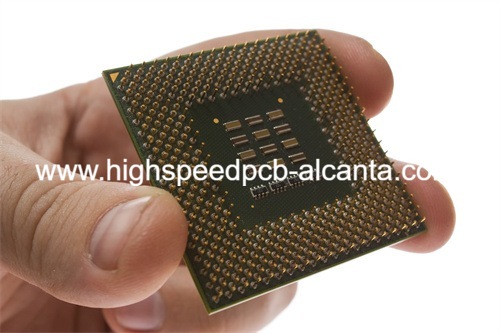
Ultrathin PCB manufacturer
Additionally, ultra-thin PCBs have a higher ability to bend and twist. Due to the use of flexible substrates, ultra-thin PCBs can more flexibly adapt to various curved surface designs and space constraints in electronic products, providing greater space for product innovation and diversification.
Finally, ultra-thin PCBs have wider application areas in electronic products. Traditional PCBs are mainly used in some relatively large and bulky electronic equipment, such as computers, servers, etc., while ultra-thin PCBs are widely used in fields such as smartphones, wearable devices, and medical devices that require thin and light designs to improve the performance of these products. and functional innovation provided technical support.
In general, ultra-thin PCB represents the cutting-edge level of modern electronic technology, and its application will open up new possibilities for the development of electronic products. By in-depth understanding of the characteristics and manufacturing processes of ultra-thin PCBs, we can better grasp the opportunities in this field and promote the progress and development of the industry.
How to design ultra-thin PCB?
Designing ultra-thin PCBs is a delicate and complex task that requires the consideration of multiple factors to ensure the performance and reliability of the final product. Here are the key factors to consider when designing ultra-thin PCBs:
Thickness limitation: The main feature of ultra-thin PCB is its thinness, so the thickness of the board must be strictly controlled during the design process. Specific thickness requirements are met by selecting the appropriate substrate material and tailoring the layer stack.
Material selection: It is crucial to select a high-performance substrate material, such as polyimide (PI) or liquid crystal polymer (LCP). These materials not only have excellent thermal stability and mechanical strength, but also meet the flexibility needs of ultra-thin PCBs.
Thermal Management: Due to the size constraints of ultra-thin PCBs, thermal management becomes an important consideration in the design process. Effective thermal design and thermal conduction paths can help reduce the temperature of electronic components and improve system performance and reliability.
Component Layout: When laying out electronic components on an ultra-thin PCB, careful planning is required to ensure optimal circuit performance and signal integrity. Optimizing component layout can minimize signal interference and crosstalk and improve system stability.
Layer stack design: Proper layer stack design is critical to the performance of ultra-thin PCBs. With proper layer stack layout, good electrical performance, impedance control, and signal integrity can be achieved.
Process Feasibility: It is critical to consider the feasibility of the manufacturing process during the design phase. Designers need to understand the constraints in the manufacturing process and choose appropriate design methods and processes to ensure the manufacturability of the final product.
What is the manufacturing process for ultra-thin PCBs?
The manufacturing process of ultra-thin PCB is a complex and precise process involving multiple key steps, each step is crucial and directly affects the quality and performance of the final product. The main steps in ultra-thin PCB manufacturing are described below:
The first step in manufacturing an ultra-thin PCB is choosing the right material and preparing it. Typically, the main substrate materials used for ultra-thin PCBs include polyimide (PI) films or liquid crystal polymers (LCP). These materials have excellent flexibility and high temperature resistance and can meet the special requirements of ultra-thin PCBs. After the material is selected, it needs to be machined and treated to ensure surface flatness and dimensional accuracy.
Before proceeding with PCB design, engineers must carefully analyze the functional requirements and layout requirements of the product. Using professional PCB design software, such as Altium Designer or Cadence Allegro, engineers convert circuit graphics into PCB layouts. In the design process of ultra-thin PCB, special attention needs to be paid to the compactness of the circuit layout and the limitation of board thickness to ensure the size and performance requirements of the final product.
Ultra-thin PCBs often feature multi-layer designs to meet high-density circuit routing and packaging requirements. During the stack-up design stage, engineers need to determine the number and stacking methods of board layers, and conduct appropriate circuit tracing to ensure the stability and reliability of signal transmission. In the design of ultra-thin PCB, the line width and line spacing are usually small, so special attention needs to be paid to the isolation and coupling effects between lines.
Once the PCB design is complete, the next step is to create the graphics layers. This involves using photolithography to transfer circuit patterns to the PCB material surface, and removing unwanted portions through chemical etching or machining. During the manufacturing process of ultra-thin PCBs, special attention must be paid to the control of the etching process to ensure the integrity and accuracy of the film.
After completing the graphic layer, drilling and metallization are next. The drilling process is used to create connection holes and component mounting holes, requiring high-precision drilling equipment and process control. After drilling is completed, a conductive layer is formed in the connection holes and metallized areas through chemical or physical methods to achieve circuit connections and component soldering.
The final step is surface coating and final processing. In ultra-thin PCB manufacturing, spray or dip coating techniques are often used to coat the PCB surface to protect circuit patterns and enhance mechanical strength. After surface coating is completed, the PCB undergoes final processing, including cutting, deburring, and inspection steps to ensure that the final product meets design requirements and quality standards.
How to make ultra-thin PCB?
The manufacturing of ultra-thin PCBs is a complex and precise process that requires special equipment and technology to ensure their quality and performance. Here are the key steps and related techniques for manufacturing ultra-thin PCBs:
The equipment required for ultra-thin PCB manufacturing is typically high-precision and highly automated to ensure precise processing and assembly on thin boards. These devices may include:
Lithography machine: The photolithography process used to transfer circuit patterns to PCB boards.
High-Precision CNC Drilling Machine: Used for drilling holes in PCB boards, often requiring precise positioning and drilling in thin boards.
Automated SMT equipment: used to precisely mount tiny SMD components on the PCB surface, ensuring accuracy and consistency.
Precision thin plate processing equipment: used to precisely control the thickness and flatness of thin plates during ultra-thin PCB manufacturing.
Ultra-thin PCB manufacturing involves a series of advanced technologies to ensure precision and efficiency of the manufacturing process:
Precision imaging technology: The imaging technology used in the photolithography process must be able to achieve high resolution and precise pattern transfer to ensure that the fine structures and lines on the circuit board are accurately reproduced.
Precise positioning and alignment technology: Precise positioning and alignment technology are required at various stages of PCB manufacturing, such as photolithography and drilling, to ensure alignment accuracy between different layers and accuracy of hole locations.
Highly automated production process: Using automated production lines and processes can greatly improve production efficiency and reduce the occurrence of human errors. Automated equipment also maintains consistency and stability in the manufacturing process.
Manufacturing ultra-thin PCBs also requires strict quality control and inspection techniques to ensure that the quality of the final product meets specifications:
Online inspection and automated inspection equipment: used to monitor and detect the quality and performance of PCBs in real time during the production process, and to detect and correct possible problems in a timely manner.
Precision measuring instruments: used to accurately measure and monitor key parameters during the manufacturing process to ensure that products meet specification requirements.
Visual inspection and manual sampling inspection: In addition to automated inspection, visual inspection and manual sampling inspection are also required to ensure that the appearance and performance of the product meet customer requirements.
By employing advanced equipment and technology, as well as strict quality control measures, ultra-thin PCB manufacturers are able to ensure product quality and performance meet industry standards and meet customer needs and expectations.
How much does an ultra-thin PCB cost?
The cost of ultra-thin PCBs is one of the important factors that need to be carefully considered during the manufacturing process. These costs are affected by a variety of factors, including design complexity, material selection, manufacturing processes, and production scale. Compared with traditional PCB, the cost of ultra-thin PCB is usually higher, mainly due to the following reasons:
Design complexity: The design of ultra-thin PCBs often involves higher technical requirements and stricter engineering standards. As more components need to be accommodated in a limited space, the design process may be more complex, resulting in increased design costs.
Material selection: The materials used in ultra-thin PCBs tend to be more advanced and special, such as flexible substrates such as polyimide (PI) or liquid crystal polymer (LCP). These materials have a higher cost and may require additional processing steps to ensure their performance and reliability.
Manufacturing process: Manufacturing ultra-thin PCBs requires more sophisticated processes and equipment to ensure the thinness and surface flatness of the board. Ultra-thin PCB manufacturing may require more processes and more complex operations than traditional PCB manufacturing, thereby increasing manufacturing costs.
Production scale: Typically, the production scale of ultra-thin PCBs is relatively small because they are usually used in high-end electronic products or specific application scenarios. In comparison, traditional PCBs can be produced on a much larger scale, allowing for economies of scale and cost savings.
Although ultra-thin PCBs cost more, they also bring many advantages, including being lighter, more flexible, and offering higher performance. With the continuous advancement of technology and improvement of manufacturing processes, it is believed that the cost of ultra-thin PCBs will gradually become more reasonable, providing better solutions for applications in more fields.
When deciding whether to choose ultra-thin PCBs, manufacturers and designers should consider cost, performance and application requirements to ensure the best solution and final product quality.
What materials are ultra-thin PCBs made of?
The material selection of ultra-thin PCB is crucial, as it directly affects the flexibility, stability and performance of the board. It is mainly composed of the following materials:
Polyimide (PI) substrate: Polyimide substrate, also called PI substrate, is one of the commonly used substrate materials in ultra-thin PCB. It has excellent high temperature stability and excellent mechanical strength, making it suitable for applications in a variety of extreme environmental conditions. Due to its high degree of flexibility and plasticity, PI substrates can be easily bent and folded, making them ideal for applications that require curved PCBs, such as flexible electronics and wearable devices.
Liquid crystal polymer (LCP) substrate: Liquid crystal polymer substrate is another common ultra-thin PCB material with excellent electrical properties and chemical stability. LCP substrates not only have a high degree of thermal stability, but also have excellent corrosion resistance and low water absorption, making them ideal for processing high-frequency signals and microwave applications. In addition, the LCP substrate also has excellent dimensional stability and can maintain the same size over a wide temperature range, ensuring the reliability and stability of the PCB in different temperature environments.
Conductive Materials: The conductive layers of ultra-thin PCBs are usually made of copper foil. Copper foil has excellent electrical conductivity and processability, and can effectively transmit current and maintain good contact. In ultra-thin PCBs, the thickness of the copper foil is usually very thin to reduce the overall board thickness and ensure the flexibility and lightweight of the board.
The characteristics of these materials allow ultra-thin PCBs to provide excellent performance and reliability in applications. Their flexibility, high-temperature stability, and electrical properties make ultra-thin PCBs ideal for many advanced electronic products. Through reasonable material selection and precise manufacturing processes, ultra-thin PCBs can meet the requirements of various complex applications and promote the continuous development and innovation of electronic technology.
Who makes ultra-thin PCBs?
Choosing the right supplier is crucial in the manufacturing of ultra-thin PCBs. As one of the industry leaders, our company has rich experience and expertise and is committed to providing high-quality ultra-thin PCB solutions. Here are the key advantages of our company in manufacturing ultra-thin PCBs:
The company has advanced production equipment and technology to meet customers’ various requirements for ultra-thin PCBs. We continuously introduce the latest manufacturing technology and continue to optimize the production process to ensure that product quality and performance reach industry-leading levels.
We understand that each customer’s needs are unique, so we provide customized ultra-thin PCB solutions. Whether it is size, material or workmanship requirements, we are able to adjust according to our customers’ needs to ensure the product exactly meets their expectations.
As an ISO certified enterprise, our company strictly follows international standards and conducts comprehensive control and supervision of product quality. We adopt strict quality inspection procedures to ensure that each ultra-thin PCB meets customer requirements and has stable performance and reliability.
We are well aware that our customers value delivery time, so we strictly implement production plans to ensure on-time delivery of products. Whether it is a small batch order or large-scale production, we are able to meet our customers’ needs in a timely manner and ensure the smooth progress of the project.
Customer satisfaction is always at the core of our work. Our team consists of experienced professionals who are ready to provide customers with technical support and consulting services. Whether it’s product selection, design advice or after-sales service, we are dedicated to helping our customers.
By choosing our company as a manufacturing supplier of ultra-thin PCBs, customers can confidently deliver their projects to us and enjoy the worry-free experience of high-quality products and excellent service. We look forward to working with you to jointly promote the development and innovation of the industry.
What are the key attributes of good ultra-thin PCB customer service?
Quality Ultra Thin PCB Customer service is key to customer satisfaction and product quality. In the highly competitive PCB manufacturing industry, providing quality customer service is not only a competitive advantage, but also an important means of establishing brand image and maintaining customer relationships. The following are key attributes that ensure quality ultra-thin PCB customer service:
Professional knowledge and experience: The customer service team should have deep professional knowledge and extensive industry experience. They need to understand all aspects of ultra-thin PCB manufacturing and be able to provide accurate answers and effective guidance to technical questions raised by customers.
Responsiveness: Excellent customer service requires prompt response to customer inquiries, complaints or needs. Resolving issues quickly and effectively increases customer trust in the brand and improves customer satisfaction.
Personalized service: The customer service team should provide personalized solutions to the needs of different customers. Understanding customers’ business and technical requirements and providing customized services based on their specific circumstances can better meet customer needs.
Transparent communication: Establishing transparent communication channels is crucial to maintaining good customer relationships. The customer service team should communicate important information such as order progress, product quality and delivery time to customers in a timely manner to ensure that customers are always aware of the latest status of the project.
Problem-solving skills: A good customer service team should have good problem-solving skills. When customers encounter problems or have special needs, being able to find solutions quickly and effectively and ensuring that the problem is solved satisfactorily will help improve customer satisfaction and brand reputation.
Frequently Asked Questions
How is ultra-thin PCB different from traditional PCB?
Ultra-thin PCB has a thinner thickness than traditional PCB, usually less than 0.4mm. They use special materials and processes to meet the needs of compact electronic devices. Traditional PCBs are thicker and are typically used in general electronic devices.
What factors need to be paid attention to in the design of ultra-thin PCB?
Designing ultra-thin PCBs requires special attention to factors such as thickness, wiring density, material selection, and heat dissipation. Due to limited space, designers must minimize PCB size while maintaining performance.
What are the difficulties in manufacturing ultra-thin PCBs?
The difficulty in manufacturing ultra-thin PCBs mainly lies in the selection and processing of materials, as well as the accuracy requirements during the manufacturing process. Ultra-thin PCBs are more susceptible to temperature and pressure, requiring more sophisticated production equipment and processes.
Is the cost of ultra-thin PCB higher than traditional PCB?
Yes, typically, ultra-thin PCBs will cost a bit more. This is because ultra-thin PCBs require the use of special materials and processes, and the production process is also more expensive, such as more sophisticated equipment and technology.