LED Ceramic Substrate Manufacturer.A leading LED Ceramic Substrate Manufacturer, we pioneer the fusion of cutting-edge technology with precision engineering. Our state-of-the-art facilities ensure the highest standards of quality, reliability, and performance. With an unwavering commitment to innovation, we craft substrates that empower next-generation LED applications. Through meticulous research and development, we optimize thermal management and electrical properties, delivering solutions that redefine industry benchmarks. Trusted by top-tier clients worldwide, our expertise spans various sectors, from automotive to telecommunications. Embrace the future of illumination with our bespoke ceramic substrates, driving efficiency and brilliance in every LED endeavor.
LED ceramic substrate is an indispensable component of modern electronic equipment and plays an important role in LED lamps, automotive lighting and other fields. As the basic material that supports and connects LED chips, LED ceramic substrates have excellent heat dissipation and electrical insulation properties. This article will delve into the manufacturing process of LED ceramic substrates, from design, process to cost, to provide readers with a comprehensive perspective.
What is LED ceramic substrate?
LED ceramic substrate is a basic material used to support and connect LED chips, which plays a key role in the modern electronics industry. Compared with traditional substrate materials, such as FR4 (fiberglass), metal substrates, etc., LED ceramic substrates have unique advantages. First of all, LED ceramic substrate has excellent heat dissipation performance, which is determined by its material characteristics. Common LED ceramic substrate materials include aluminum oxide (Al2O3) and silicon nitride (Si3N4). These materials have good thermal conductivity and can effectively conduct the heat generated by the LED chip to the surrounding environment, thereby maintaining the normal operation of the LED chip. temperature to extend its service life.
Secondly, LED ceramic substrate has excellent electrical insulation properties. LED chips need to be protected by reliable electrical insulation when working to avoid short circuits and electrical failures. Since the ceramic material itself has good insulation properties, the LED ceramic substrate can effectively isolate the circuit and ensure the safe and stable operation of the LED chip.
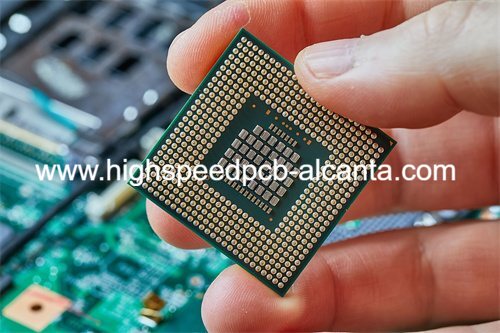
LED Ceramic Substrate Manufacturer
Due to its excellent heat dissipation and electrical insulation properties, LED ceramic substrates are an ideal choice for LED lamps. LED lamps usually need to run continuously for a long time, and the excellent characteristics of LED ceramic substrates can ensure that LED lamps work stably in high-temperature environments, while improving the reliability and service life of LED lamps.
In addition to applications in LED lamps, LED ceramic substrates are also widely used in other fields, such as automotive lighting, electronic displays, communication equipment, etc. With the continuous development and popularization of LED technology, the demand for LED ceramic substrates is gradually increasing, providing reliable basic support for the further development of the LED industry.
In short, LED ceramic substrates have become an important part of the LED industry with their excellent heat dissipation and electrical insulation properties, providing key support for the performance and reliability of LED products and promoting the widespread application and development of LED technology.
How to design LED ceramic substrate?
The design of LED ceramic substrate is an important part of ensuring the performance and reliability of LED lamps. When designing, multiple factors need to be considered, including circuit layout, thermal requirements, and mechanical suitability. This article will delve into the design process of LED ceramic substrates and how to conduct design and simulation analysis through CAD software to ensure the high-quality performance and reliability of LED ceramic substrates.
First of all, circuit layout is a crucial part of LED ceramic substrate design. A good circuit layout can optimize the signal transmission path to the greatest extent and reduce signal interference and power loss. Designers need to reasonably lay out various components and connection lines based on the functions and requirements of LED lamps to ensure the stability and reliability of the circuit.
Secondly, the heat dissipation requirements of LED ceramic substrates are also one of the key factors that need to be considered during the design process. LED chips generate a large amount of heat when working. If the heat cannot be dissipated effectively, the performance of the LED lamps will be reduced or even damaged. Therefore, when designing an LED ceramic substrate, the design and layout of the heat sink need to be considered to improve heat dissipation efficiency and ensure the normal operating temperature range of the LED chip.
In addition, the mechanical suitability of the LED ceramic substrate is also one of the important factors to be considered during the design process. LED lamps usually need to be assembled with other mechanical components or housings, so the size, shape and mounting hole positions of the LED ceramic substrate need to match other components to ensure a smooth assembly process and minimize assembly costs and process difficulties.
In order to achieve the above design goals, engineers usually use CAD (computer-aided design) software to design LED ceramic substrates. CAD software has powerful modeling and simulation functions, which can help designers quickly draw three-dimensional models of LED ceramic substrates and conduct circuit simulation and thermal simulation analysis. Through simulation analysis, designers can evaluate the performance and reliability of different design solutions and optimize design parameters, thereby improving the quality and efficiency of LED ceramic substrates.
To sum up, the design of LED ceramic substrate is a complex process that takes multiple factors into consideration. It requires engineers to have rich experience and professional knowledge, and use CAD software for simulation and analysis to ensure that the LED ceramic substrate has excellent performance and reliability.
What is the manufacturing process of LED ceramic substrate?
The manufacturing process of LED ceramic substrates is a complex and precise process involving multiple key steps, each of which has a direct impact on the performance and quality of the final product. The manufacturing process of LED ceramic substrates will be introduced in detail below.
The first is the material preparation stage. The materials required for the manufacture of LED ceramic substrates mainly include high thermal conductivity ceramic substrate materials, conductive materials and other auxiliary materials. These materials need to undergo strict quality control and inspection to ensure compliance with product design and manufacturing requirements.
Next comes the printed circuit board (PCB) manufacturing stage. At this stage, the ceramic substrate will be processed into the shape and size that meets the design requirements, and the surface will be coated with a layer of conductive material, usually metal or conductive ink. This step requires high-precision equipment and process control to ensure the uniformity and quality of the conductive layer.
Then comes the circuit patterning stage. At this stage, manufacturers will print or etch specific circuit patterns on the conductive layer according to product design requirements. The precision and accuracy of this step is critical for subsequent welding and testing work.
Next comes the welding stage. At this stage, the LED chips and other electronic components will be soldered to the corresponding locations on the circuit board. The quality of the welding process directly affects the reliability and stability of the circuit connection, so precision welding equipment and technology are required.
Finally comes the testing phase. At this stage, the manufacturer will conduct comprehensive functional testing and performance evaluation of the soldered LED ceramic substrate. By using various test equipment and methods, we ensure that the product meets the design requirements and has good electrical performance and reliability.
In general, the manufacturing process of LED ceramic substrates includes multiple key steps such as material preparation, PCB manufacturing, circuit patterning, welding and testing. Each step requires precise process control and quality management to ensure the performance and quality of the final product meet expected standards.
How to control the manufacturing cost of LED ceramic substrates?
The manufacturing cost of LED ceramic substrates is a complex and important consideration, which is affected by many factors. First, material costs are one of the major components of manufacturing costs. LED ceramic substrates are usually made of high thermal conductivity materials, such as aluminum oxide or silicon nitride, and the cost of these materials is relatively high. Secondly, process complexity will also directly affect manufacturing costs. The manufacturing process requires multiple steps such as printed circuit board (PCB) manufacturing, circuit patterning, and soldering, and the complexity of these steps will affect the required manpower, equipment, and time costs.
Another influencing factor is the scale of production. Generally speaking, large-scale production can bring about economies of scale, thereby reducing the manufacturing cost of a unit product. Conversely, small-scale production may increase the cost per unit of product because fixed costs need to be spread over fewer products.
To control the manufacturing cost of LED ceramic substrates, the key is to optimize design, process and supply chain management. First, optimized design can reduce costs by reducing material usage and simplifying manufacturing processes. Secondly, optimizing the process can improve production efficiency and reduce scrap rates, thereby reducing manufacturing costs. Finally, optimizing supply chain management can reduce manufacturing costs by finding lower-cost material suppliers and improving the flexibility and reliability of the supply chain.
In summary, by comprehensively considering factors such as material cost, process complexity, production scale, and optimized design, process, and supply chain management, the manufacturing cost of LED ceramic substrates can be effectively reduced, thereby improving the competitiveness and market share of the product.
What is the material of LED ceramic substrate?
As a key component in the LED lighting industry, LED ceramic substrate plays a vital role in achieving stable operation of LED chips and extending their service life. It not only needs to provide a reliable electrical connection, but also needs to dissipate heat effectively to ensure that the LED chip is within a suitable operating temperature range. Therefore, the material selection of LED ceramic substrate is crucial.
LED ceramic substrates are usually made of high thermal conductivity materials to ensure that the LED chip can dissipate heat quickly and effectively when working. The two most commonly used materials are aluminum oxide and silicon nitride.
First of all, alumina is one of the commonly used materials for LED ceramic substrates. It has good thermal conductivity and electrical insulation properties, and can effectively conduct the heat generated by the LED chip to the external environment. The advantages of alumina also include its relatively low cost and ease of processing, making it one of the preferred materials in LED ceramic substrate manufacturing.
Secondly, silicon nitride is also a commonly used LED ceramic substrate material. Compared with aluminum oxide, silicon nitride has higher thermal conductivity and lower thermal expansion coefficient, which makes it widely used in some application scenarios that require higher heat dissipation performance. Silicon nitride substrates are often used in high-power LED lamps, automotive lighting and other fields to meet stringent requirements for heat dissipation performance.
Taken together, the material selection for LED ceramic substrates must take into account not only heat dissipation performance, but also cost and processing performance. Aluminum oxide and silicon nitride, as two main materials, play an important role in the LED lighting industry. Their different characteristics are suitable for different application scenarios, providing reliable support for the performance improvement and cost control of LED products.
Who makes LED ceramic substrates?
In the complex process of LED ceramic substrate manufacturing, supplier selection is a crucial step. As a leading LED ceramic substrate manufacturer, we are committed to providing high-quality products and excellent customer service. Our supply chain partners include many excellent companies with rich experience and expertise in the field of LED ceramic substrates.
We have established long-term and stable cooperative relationships with our suppliers to ensure that the purchased materials and equipment meet strict quality standards. Whether it is substrate materials, printing equipment or welding processes, we strictly control every aspect to ensure product stability and reliability.
Cooperation with suppliers is not just a procurement relationship, but also a kind of technical cooperation. We work closely with our suppliers to jointly solve technical problems in the production process, optimize the production process, and improve product quality.
Our suppliers not only provide standardized products but also provide customized solutions based on customer needs. Whether it is the selection of special materials, the application of special processes, or the optimization of product design, we can work with suppliers to provide customers with satisfactory solutions.
We value cooperation with our suppliers as part of sustainable development. Together with our suppliers, we are committed to the green and environmentally friendly production concept, promote the sustainable development of the LED ceramic substrate industry, and contribute to environmental protection.
In the process of LED ceramic substrate manufacturing, supplier selection is crucial to product quality and customer satisfaction. As your trustworthy partner, we will continue to cooperate with excellent suppliers to provide you with excellent LED ceramic substrate products and services.
FAQS
What is the key to LED ceramic substrate manufacturing?
The key to the manufacturing of LED ceramic substrates lies in the exquisite craftsmanship and material selection. High-quality LED ceramic substrates need to have good heat dissipation performance, electrical insulation performance and mechanical strength, which requires manufacturers to strive for excellence in technology to ensure that every link reaches the best state. At the same time, appropriate material selection is also crucial. High thermal conductivity materials such as aluminum oxide and silicon nitride can meet the heat dissipation needs of LED chips and ensure the performance and reliability of LED ceramic substrates.
How is the LED ceramic substrate designed?
The design of LED ceramic substrates needs to consider many factors, including circuit layout, heat dissipation requirements, mechanical suitability, etc. Designers typically use CAD software to design and perform simulations and analyzes to ensure the design meets performance and reliability requirements. During the design process, the working environment and application scenarios of the LED chip need to be fully considered to achieve the best design solution.
What are the steps involved in the manufacturing process of LED ceramic substrates?
The manufacturing process of LED ceramic substrates includes multiple steps such as material preparation, printed circuit board (PCB) manufacturing, circuit patterning, welding, and testing. Among them, PCB manufacturing is a key link and requires precise process control. In the manufacturing process, every step is critical, and any failure in any link may affect the quality and performance of the final product.
What factors affect the manufacturing cost of LED ceramic substrates?
The manufacturing cost of LED ceramic substrates is affected by many factors, including material cost, process complexity, production scale, etc. In terms of manufacturing cost control, optimizing design, process and supply chain management are key. By improving production efficiency, reducing material costs and optimizing processes, the manufacturing cost of LED ceramic substrates can be effectively reduced.
What material is the LED ceramic substrate made of?
LED ceramic substrates are usually made of high thermal conductivity materials, such as aluminum oxide, silicon nitride, etc. These materials have good heat dissipation and electrical insulation properties, can meet the working requirements of LED chips, and ensure the performance and reliability of LED ceramic substrates.