Cavity PCB Technology Manufacturing.Cavity PCB Technology Manufacturing involves the creation of printed circuit boards with cavities or recesses that allow for the integration of various components at different heights. This advanced technique enhances performance by minimizing signal loss and optimizing thermal management, making it ideal for high-frequency and power electronics applications. The precise manufacturing process ensures reliable, efficient, and compact electronic solutions.
In today’s modern electronics world, printed circuit boards (PCBs) play a vital role in ensuring the functionality and efficiency of electronic devices. Among various PCB manufacturing technologies, Cavity PCB technology stands out as an innovative approach with its unique advantages in performance, reliability and miniaturization. In this comprehensive guide, we dive into the complexities of Cavity PCB technology manufacturing, exploring its key components, manufacturing processes, materials, cost factors, and the companies driving its development.
What is Cavity PCB Technology?
Cavity PCB Technology is an innovative PCB manufacturing technology, also known as embedded component PCB or Cavity board. Compared to traditional PCBs, Cavity PCBs embed components within the layers of the PCB substrate rather than simply mounting them on the surface. This unique manufacturing method allows Cavity PCB to create more compact, lightweight and high-performance electronic devices, especially for applications with strict space and weight requirements.
In traditional PCB design, components are usually mounted on the surface of the PCB through surface mount technology (SMT) or plug-ins. However, this surface-mounting approach limits board density and performance because the size and shape of components limits how they can be arranged on the PCB surface. In contrast, Cavity PCB Technology allows components to be embedded into the internal space of the PCB, thereby freeing up space on the PCB surface, allowing designers to arrange components more efficiently and achieve higher density and more complex circuit designs.
By embedding components into the internal layers of the PCB, Cavity PCB enables a more compact and lightweight design. This compact design is crucial for modern electronic devices, especially in mobile devices and portable electronics where space and weight are often the most precious resources. Cavity PCBs also improve the performance and reliability of electronic devices because the embedded components are better protected from the external environment, such as moisture, dust, and mechanical damage.
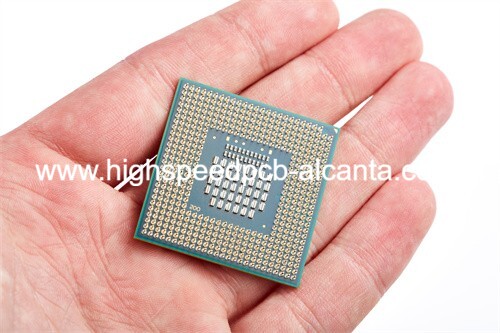
Cavity PCB Technology Manufacturing
Due to its unique design and manufacturing methods, Cavity PCB Technology is widely used in many industries. From aerospace to medical devices, automotive to communications systems, Cavity PCB provides designers with a powerful tool that enables them to design smaller, lighter, and more reliable electronic products to meet growing market demands. and customer expectations.
Overall, Cavity PCB Technology represents a major innovation in PCB manufacturing, taking the performance and reliability of electronic devices to a new level. With the continuous development of technology and the expansion of applications, Cavity PCB will continue to play an important role in future electronic design and manufacturing, driving progress and innovation in the industry.
How to design Cavity PCB?
Designing a Cavity PCB requires careful planning, taking into account multiple factors to ensure the performance and reliability of the final product. First, component placement is one of the key considerations in the design process. Reasonable component layout can not only save space to the greatest extent, but also ensure that short circuits and electromagnetic interference in the signal transmission path are minimized. By placing components in the right locations, more efficient thermal management is achieved, improving overall performance and reliability.
Secondly, thermal management is an aspect that needs to be focused on during the design process. Since Cavity PCBs typically have higher integration and power densities, heat generation and conduction need to be effectively controlled. Designers need to consider the heat generation of each component and take appropriate heat dissipation measures, such as heat sinks, heat dissipation holes, etc., to ensure overall thermal balance and stability.
At the same time, signal integrity is also one of the factors that cannot be ignored in the design process. In Cavity PCB, the signal transmission path may be affected by electromagnetic interference, causing signal distortion or reducing the transmission rate. Therefore, designers need to take measures to reduce the length and intersection of signal transmission paths, as well as adopt appropriate shielding measures in critical areas, such as ground planes, shielding layers, etc., to improve signal stability and reliability.
In addition, manufacturability is also one of the important factors to consider during the design process. Designers need to fully understand the characteristics of PCB manufacturing processes and materials to ensure that the design plan can be successfully implemented in actual production. Reasonable design layout and wiring methods can not only simplify the manufacturing process, but also reduce manufacturing costs and improve product quality and reliability.
To sum up, designing Cavity PCB requires comprehensive consideration of multiple factors such as component layout, thermal management, signal integrity and manufacturability, and using advanced PCB design software and simulation tools to optimize layout and routing to ensure Optimization of performance and reliability. Through careful planning and design, the high performance, high reliability and high integration of Cavity PCB can be achieved to meet the needs of different application scenarios.
What is the Cavity PCB manufacturing process?
The manufacturing process of Cavity PCB is a complex and precise project involving multiple key steps, each step is crucial and affects the quality and performance of the final product. Below we take a deep dive into the Cavity PCB manufacturing process to reveal its complexity and sophistication.
First, the first step in manufacturing Cavity PCB is substrate preparation. At this stage, it is crucial to select the appropriate substrate material. Commonly used materials include FR-4, Rogers, etc. Substrates need to undergo rigorous inspection and processing to ensure smooth surfaces and accurate dimensions.
Next comes layering. In the lamination stage, the substrate and other materials will be laminated together in a certain order according to the design requirements to form a complete structure. This process requires a high degree of precision and expertise to ensure that the layers are firmly bonded without voids or bubbles.
This is followed by cavity milling. This is one of the critical steps in the Cavity PCB manufacturing process. At this stage, advanced processing equipment is used to mill cavities or grooves in the substrate according to the design requirements for subsequent component embedding. The milling process requires precise control and a high level of skill to ensure that the shape, size and position of the cavity are as desired.
Then comes component embedding. After the cavity is milled, the electronic components need to be embedded into the cavity. This process requires precise position control and professional techniques to ensure that the connection between the component and the substrate is strong and reliable, and does not cause damage or interference to the surrounding structure.
Next comes lamination. After the component embedding is complete, the substrate is placed in a laminator for lamination. During the lamination process, high temperature and high pressure are used to tightly combine the materials of each layer to form a stable structure. This process requires strict temperature and pressure control to ensure optimal lamination results.
Finally comes the final finishing. After lamination is completed, Cavity PCB needs final finishing, including trimming, drilling, anti-corrosion treatment, etc. These steps are designed to make the final product look perfect and have a smooth surface that meets the customer’s requirements and standards.
In general, the manufacturing process of Cavity PCB is a highly complex and precise project that requires professional technology and strict quality control. Only Cavity PCB that has been carefully designed and manufactured can meet the performance, reliability and miniaturization requirements of modern electronic equipment and provide customers with excellent products and services.
How is Cavity PCB made?
Manufacturing Cavity PCBs involves integrating advanced manufacturing technologies and processes to achieve superior quality and performance. This process is a highly precise engineering, from the selection of raw materials to the final finished product, every step is carefully considered and executed to ensure product reliability and performance.
First, the first step in manufacturing Cavity PCB is to prepare the substrate. The selection of high-quality substrate materials is crucial to ensuring the quality of Cavity PCB. These substrates are typically constructed of fiberglass-reinforced resin, such as FR-4, which has excellent insulation properties and mechanical strength and is able to withstand complex environmental conditions.
Next, the substrate is laminated, pressing the inner circuit board together with the pre-designed cavity layer. This step requires a high degree of precision and technology to ensure precise alignment of the cavity and circuit board and the stability of the lamination process.
After reserving space on the cavity layer, the next step is to use an advanced CNC milling machine to precisely mill the cavity. This requires highly precise control and programming to ensure that the shape and size of the cavity meet the design requirements and to maintain the flatness and smoothness of the surface.
Subsequently, the electronic components are embedded into the cavity. This process requires sophisticated automated equipment and technology to ensure precise alignment and fixation of components and cavities while maintaining electrical and thermal properties between components and circuit boards.
After the components are embedded, the substrate is laminated and pressed again to hold all the layers together. This ensures a secure hold of the components and overall structural stability of the board.
Finally, the finished product is inspected and tested through strict quality control procedures. This includes a comprehensive assessment of electrical, thermal and mechanical properties to ensure Cavity PCB meets industry standards and customer requirements.
Overall, manufacturing Cavity PCB is a complex and precise process that requires the integration of multiple advanced technologies and processes to ensure the highest level of product quality and performance. Through strict quality control and continuous technological innovation, manufacturers can continuously improve the production efficiency and product quality of Cavity PCB to meet the growing needs of customers.
What are the cost considerations for Cavity PCB?
Cavity PCB technology has attracted much attention due to its superior advantages in performance and miniaturization. However, the manufacturing cost of Cavity PCB may be higher compared to traditional PCB. This cost difference is primarily influenced by several key factors, which are explored in detail below:
Material Selection: The materials used in the manufacture of Cavity PCBs often require special properties and characteristics to meet high performance and reliability requirements. Compared to traditional PCBs, Cavity PCBs may require the use of higher-grade materials, such as high-frequency laminates or materials with specific thermal characteristics, which will increase manufacturing costs.
Design complexity: The design of Cavity PCB is usually more complex because factors such as component embedding, thermal management, signal integrity, etc. need to be considered. Increased design complexity can lead to longer design cycles and increased input from design engineers, thereby increasing manufacturing costs.
Production volume: Production volume is another important factor that affects Cavity PCB manufacturing costs. Typically, the higher the production volume, the lower the cost of a single PCB because fixed costs can be spread over more products. In contrast, for Cavity PCBs produced in small batches or custom-made, the unit cost may be higher.
Technical requirements: Manufacturing Cavity PCB may require more advanced technology and equipment, such as special laminators, precision cavity milling equipment, and high-precision assembly lines. These advanced technologies and equipment usually bring higher investment and operating costs, thus increasing manufacturing costs.
In summary, although Cavity PCB offers unparalleled advantages in terms of performance and miniaturization, it may face some challenges in terms of manufacturing cost. By carefully considering factors such as material selection, design complexity, production volume and technical requirements, and working closely with professional manufacturing partners, manufacturing costs can be effectively controlled, thereby achieving commercial application and market competitiveness of Cavity PCB.
What materials are used in Cavity PCB?
Cavity PCBs are typically manufactured from a range of premium materials including but not limited to FR-4, Rogers and high frequency laminates. These materials were chosen primarily for their excellent electrical properties, thermal stability, and mechanical strength, making them ideal for demanding applications in industries such as aerospace, automotive, medical, and communications.
FR-4 is a glass fiber reinforced epoxy resin substrate widely used in PCB manufacturing with excellent insulation properties, heat resistance and mechanical strength. This material not only has high electrical properties, but can also withstand stress in high-temperature environments, so it is often used in electronic devices that require stable performance and reliability.
Rogers material is a high-performance dielectric material with low dielectric loss, excellent high-frequency characteristics and stable dielectric constant. This material is often used in high-frequency applications, such as radar systems, radio frequency communication equipment, and satellite communication systems, and can effectively improve the stability and reliability of signal transmission.
High-frequency laminates are special materials specially manufactured for high-frequency circuit design and have excellent high-frequency characteristics and signal transmission performance. This material usually uses PTFE (polytetrafluoroethylene) as the base material, combined with special reinforcement materials and lamination processes, to meet application scenarios with extremely high signal integrity and stability requirements, such as wireless communication base stations, microwave Equipment etc.
In general, these high-quality materials used in Cavity PCB can not only meet the strict requirements of various industries, but also provide a solid foundation for the performance improvement and reliability guarantee of electronic equipment. Through careful selection and application of these materials, manufacturers can ensure that Cavity PCB can operate stably and reliably in various extreme environments, providing customers with excellent products and services.
Who are the leading manufacturers of Cavity PCB?
Cavity PCB manufacturing is a complex and precise process designed to create embedded component PCBs with high performance and reliability. Following are the main steps in Cavity PCB manufacturing:
Material preparation: First, you need to prepare the required PCB substrate materials as well as materials required for embedded components and other components. Choosing high-quality substrate materials is critical to ensuring the quality of the final product.
Design planning: Detailed design planning is required before Cavity PCB manufacturing. This includes determining the location of components, sizing and shaping cavities, and optimizing PCB layout to maximize performance and reliability.
Cavity Preparation: One of the key steps in the manufacturing process is the accurate preparation of the cavity. This involves using precision machining equipment and tools to create cavities in the internal layers of the PCB to accommodate embedded components.
Component embedding: Once the cavity is prepared, components can be embedded into it. This usually involves fitting the components precisely into the internal layers of the PCB and taking steps to ensure they are well connected and secured to the rest of the PCB.
Lamination and shaping: After the components are embedded, the various layers of the PCB are laminated, shaped and processed. This ensures the robustness and reliability of the PCB and prepares it for subsequent process steps.
Final Finishing: The last step is to do the final finishing and processing of the PCB. This includes the necessary cleaning and inspection of the PCB to ensure it meets quality standards and customer requirements.
Our company has advanced equipment and technology and specializes in Cavity PCB manufacturing. Our team is experienced in customizing high-quality Cavity PCB products according to our customers’ needs and specifications. We are committed to providing our customers with the best solutions and remaining at the forefront of the industry. If you are interested in our Cavity PCB manufacturing services, please feel free to contact our sales team and we will be happy to assist and support you.
What are the qualities of good customer service?
In Cavity PCB manufacturing, excellent customer service is a key factor in ensuring customer satisfaction and loyalty. Effective customer service not only meets your customers’ needs, it also builds good relationships and promotes long-term business success. Here are the key attributes of good customer service:
Effective communication is the basis for building good customer relationships. Manufacturers should actively listen to customers’ needs and opinions and promptly respond to customer inquiries and feedback. Clear communication can avoid misunderstandings and dissatisfaction and promote the smooth development of cooperative relationships.
Responding quickly to customer needs and questions is key to providing excellent customer service. Manufacturers should promptly respond to customers’ emails, phone calls, or online messages to ensure that customers receive timely support and solutions. Prompt responses show importance and respect for the customer and help build trust and loyalty.
In the field of Cavity PCB manufacturing, customers are often interested in technical issues and challenges. Therefore, manufacturers need to have sufficient technical expertise to be able to provide accurate and useful advice on design, material selection, manufacturing processes, etc. A strong technical background contributes to customer trust and dependence on the manufacturer.
Customers expect to be able to rely on manufacturers to provide stable and reliable products and services. Manufacturers should keep their promises, deliver products on time, and ensure product quality meets customer expectations. Reliability is the foundation for building trust and loyalty, helping manufacturers win long-term customer support and cooperation.
Quality is one of the important considerations for customers when choosing a manufacturer. Manufacturers should adhere to strict quality requirements and continuously strive to improve the quality level of their products and services. Actively adopt quality control measures to ensure that products comply with industry standards and customer requirements, thereby winning customer trust and satisfaction.
In conclusion, in Cavity PCB manufacturing, good customer service is the key to achieving customer satisfaction and loyalty. Through effective communication, quick response, technical expertise, reliability and commitment to quality, manufacturers are able to build great relationships and drive long-term business success.
Frequently Asked Questions
What industries commonly utilize Cavity PCBs in their products?
Cavity PCBs find applications across various industries, including aerospace, automotive, medical, telecommunications, and consumer electronics. In the aerospace industry, Cavity PCBs are used in avionics systems, satellite communications, and unmanned aerial vehicles (UAVs) due to their lightweight construction and reliability. In the automotive sector, Cavity PCBs are employed in advanced driver assistance systems (ADAS), electric vehicles (EVs), and infotainment systems. Similarly, the medical industry utilizes Cavity PCBs in diagnostic equipment, patient monitoring devices, and medical imaging systems for their compact size and high performance.
What factors influence the cost of manufacturing Cavity PCBs?
The cost of manufacturing Cavity PCBs is influenced by several factors, including the complexity of the design, the number of layers, the type of materials used, the production volume, and the technology requirements. Designs with intricate layouts and high component density may require specialized manufacturing processes and equipment, resulting in higher production costs. Additionally, the choice of materials, such as high-frequency laminates or specialized substrates, can impact the overall cost of manufacturing. Production volume plays a significant role in determining unit costs, with larger volumes often leading to economies of scale and lower per-unit costs.
What are the primary advantages of using Cavity PCB Technology?
Cavity PCB Technology offers several key benefits, including enhanced miniaturization, improved thermal management, increased reliability, and reduced electromagnetic interference (EMI). By embedding components within the layers of the PCB substrate, Cavity PCBs enable the creation of compact and lightweight electronic devices with improved performance and functionality.
How does Cavity PCB Technology differ from conventional PCB manufacturing?
Unlike conventional PCB manufacturing methods where components are mounted on the surface of the substrate, Cavity PCB Technology involves embedding components within the layers of the PCB. This approach allows for better utilization of available space, reduced signal losses, and improved mechanical stability, resulting in superior performance and reliability.