RF PCB Manufacturer.As an RF PCB manufacturer, we specialize in crafting high-quality printed circuit boards optimized for radio frequency applications. Our expertise lies in creating PCBs tailored to meet the demanding requirements of wireless communication systems, radar systems, satellite communication, and more. With precision engineering and cutting-edge technology, we ensure optimal performance, signal integrity, and reliability in every RF PCB we produce.
With the continuous advancement of wireless communication technology, RF (radio frequency) PCB design is crucial to ensure the performance of wireless devices. This article will focus on the key steps and considerations in RF PCB design, aiming to assist engineers in optimizing the performance and reliability of wireless communication systems.
What is RF PCB?
RF PCB, or Radio Frequency printed circuit board, is an electronic component specially designed for radio frequency signal transmission and processing. Compared with traditional printed circuit boards (PCBs), RF PCBs have higher requirements and complexity in design and manufacturing. Its main features include a strong focus on signal integrity, impedance matching, signal coupling, and factors such as electromagnetic interference (EMI) and electromagnetic compatibility (EMC).
First of all, the design of RF PCB needs to consider signal integrity, that is, minimizing signal distortion and loss during signal transmission. Radio frequency signals have the characteristics of high frequency and short wavelength. Therefore, the signal transmission path, layout and connection method need to be carefully designed to ensure the stability and reliability of the signal.
Secondly, impedance matching is one of the key issues in RF PCB design. The impedances of various components in RF circuits, including signal sources, transmission lines, and receivers, need to be matched to each other to minimize signal reflection and transmission losses. Therefore, a series of measures need to be taken in the design of RF PCB, such as optimizing the width, spacing and interlayer structure of the transmission lines to ensure the impedance matching of the entire circuit.
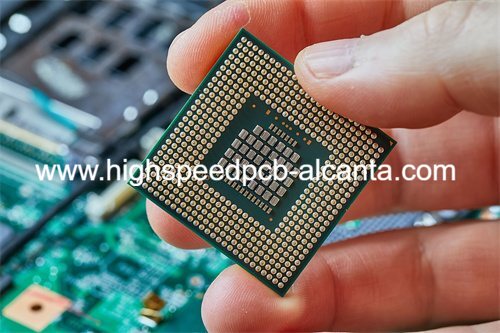
RF PCB Manufacturer
In addition, RF PCB also needs to consider signal coupling and electromagnetic interference issues. Radio frequency signals may interfere with each other during transmission, resulting in signal distortion and system performance degradation. Therefore, a series of shielding and isolation measures need to be taken in the design of RF PCB to reduce interference and coupling effects between signals, while reducing the impact of electromagnetic radiation and interference.
To sum up, RF PCB is a printed circuit board specially designed for radio frequency signal transmission and processing. Its design and manufacturing need to consider many factors, including signal integrity, impedance matching, signal coupling, electromagnetic interference and compatibility, etc. , to ensure the stability and reliability of the wireless communication system.
RF PCB design Reference Guide.
RF (Radio Frequency) PCB design is an important step in optimizing the performance and reliability of wireless communication systems. This guide is intended to provide key points of RF PCB design to help engineers effectively design and implement high-performance RF circuit boards.
Good layout design is the key to RF PCB design. Reasonably arrange RF circuit components and transmission lines to minimize signal path length and crossover, and reduce signal loss and crosstalk. At the same time, pay attention to the design of the ground plane to provide a low-impedance path to reduce signal backflow and interference.
Ensure that the impedance of the PCB matches the impedance of the RF circuit components and transmission lines to minimize signal reflections and transmission losses. Use appropriate high-frequency materials and standardized manufacturing processes to ensure the accuracy and stability of impedance matching.
Choose high-frequency materials suitable for RF applications, such as PTFE (Polytetrafluoroethylene) and FR-4 high-frequency dielectric materials to ensure good signal transmission and performance stability. Consider factors such as the material’s dielectric constant, loss factor, and thermal properties to meet the system’s requirements for signal quality and stability.
Use appropriate shielding measures and wiring techniques to reduce electromagnetic interference and compatibility issues. Optimize PCB layout and ground plane design to reduce signal radiation and electromagnetic coupling between sensitive devices.
Consider the thermal coupling and heat dissipation design of RF components to ensure system stability and reliability. Use appropriate heat dissipation components and heat conduction paths to effectively manage the temperature distribution of RF circuit boards to prevent overheating damage.
The manufacturing process of RF PCB requires high precision and control. Key steps include material preparation, printed circuit diagrams, chemical etching, assembly and testing. Strictly follow manufacturing standards and specifications to ensure the quality and stability of PCBs.
RF PCB is widely used in fields such as communication base stations, satellite communications, radar systems, wireless network equipment, automotive radar and medical diagnostic equipment, providing reliable signal transmission and processing functions for various radio frequency applications.
By following the key points listed above, engineers can design and implement high-performance RF PCBs that optimize the performance and reliability of wireless communication systems to meet evolving RF application needs.
What material is used in RF PCB?
The material selection of RF PCB (radio frequency printed circuit board) is crucial and directly affects its performance and reliability in wireless communication systems. The following are the main materials commonly used in RF PCB manufacturing:
PTFE (polytetrafluoroethylene): PTFE is a high-frequency dielectric material with excellent insulation properties and low loss characteristics. Due to its stability and reliability at high frequencies, PTFE is often used to manufacture high-performance RF PCBs, such as RF systems and antennas in the microwave band.
FR-4 high-frequency dielectric material: FR-4 is a glass fiber reinforced epoxy resin composite material commonly used in PCB manufacturing with lower general performance requirements. However, for RF applications, specially treated FR-4 materials can provide better high-frequency performance, including lower losses and better impedance control.
RO (Radio Frequency Polychlorotrifluoroethylene): RO material is a high frequency dielectric material specially designed for radio frequency applications, with excellent high frequency performance and stability. RO materials typically use different filler and resin combinations to achieve specific dielectric and mechanical properties, making them suitable for high-frequency, high-speed and high-reliability RF systems.
PTFE Glass Composite: PTFE glass composite combines the low-loss properties of PTFE with the mechanical strength of glass fiber to provide an optimized high-frequency dielectric material. This material is often used to manufacture RF PCBs that require higher performance, such as microwave communication equipment and satellite communication systems.
Metal substrate: For certain RF applications with high power, high temperature, or special environmental conditions, metal substrates (such as aluminum substrates or copper substrates) are also an option. Metal substrates have good heat dissipation properties and mechanical stability, making them suitable for RF systems that require higher power density and temperature management.
In summary, RF PCB material selection should be optimized based on specific application needs and performance requirements. During the design process, engineers need to consider factors such as dielectric properties, loss characteristics, impedance control, mechanical strength, and manufacturing costs to ensure that the RF PCB achieves optimal performance and reliability in wireless communication systems.
What size are RF PCB?
RF PCB dimensions can vary based on specific application needs. Compared with traditional PCBs, RF PCBs generally require higher design accuracy and dimensional control to ensure signal integrity and performance stability. Generally speaking, RF PCBs can come in various sizes, from small ones of a few millimeters to large ones of tens of centimeters, depending on the following factors:
Frequency range: The size of an RF PCB is often closely related to the frequency range in which it operates. For higher frequency applications, the PCB size may be relatively smaller to reduce signal transmission paths and minimize signal attenuation.
System integration: Some applications may require the integration of multiple RF functions or devices, so the RF PCB may require a larger size to accommodate these components and ensure good layout between them.
Environmental requirements: In some special environments, such as aerospace or military fields, the RF PCB may need to be smaller in size to accommodate space constraints or weight requirements.
Heat dissipation requirements: For higher power RF applications, the RF PCB may need to be larger in size to provide sufficient heat dissipation surface area to ensure system stability and reliability.
To sum up, the size of RF PCB depends on the comprehensive consideration of multiple factors, including frequency range, system integration, environmental requirements and heat dissipation needs. Therefore, when designing an RF PCB, engineers need to consider these factors and determine the most appropriate size based on specific application requirements.
The Manufacturer Process of RF PCB.
The manufacturing process of RF PCB is a complex and critical process, which directly affects the performance and reliability of the RF circuit board. The following are the main steps of the RF PCB manufacturing process:
High frequency materials such as PTFE (polytetrafluoroethylene) and FR-4 high frequency dielectric materials are often used in the manufacturing of RF PCBs. Strict quality control and preparation of these materials is required before the manufacturing process begins to ensure that they meet the design requirements and have good properties.
RF PCB design and layout is a critical step in the manufacturing process. Design engineers use professional design software to create circuit diagrams and layout designs, taking into account factors such as signal integrity, impedance matching, ground plane layout and EMI/EMC management to ensure optimal RF performance.
Once the design is complete, the manufacturing process enters the photolithography and etching stages. At this stage, the desired circuit pattern is formed by covering the PCB surface with photoresist, then using a photolithography machine to project the design pattern onto the photoresist, and using chemical etching to remove the unnecessary copper layer.
Next comes the metallization and surface treatment stage. Circuit connections are formed by plating a layer of metal (usually copper) on the PCB surface. Then, a surface treatment, such as gold or tin plating of the soldering pads, is performed to facilitate assembly and soldering of the components.
Once the circuit pattern and metallization on the PCB is complete, component assembly can begin. This involves soldering RF components (such as antennas, amplifiers, filters, etc.) and other electronic components to the PCB, often using automated surface mount technology (SMT) for efficient assembly.
Finally, the completed RF PCB requires rigorous testing and quality control. This includes performing performance testing of the circuit using high-frequency test equipment to ensure it meets design requirements and specifications. Any defects or poor circuitry will be identified and corrected to ensure the quality and reliability of the final product.
Overall, the manufacturing process of RF PCB is a complex and precise process that requires highly specialized knowledge and skills to ensure that the final product has excellent performance and reliability.
The Application area of RF PCB.
RF PCBs are widely used in various radio frequency (RF) applications and provide key signal transmission and processing functions for wireless communication systems and devices. The following are the main application areas of RF PCB:
Communication base station: RF PCB is widely used in mobile communication base stations, microwave communication equipment and satellite communication systems. They support the sending and receiving, modulation, demodulation and processing of radio frequency signals to ensure the stability and coverage of the communication network.
Wireless network equipment: RF PCB is used in wireless local area networks (WLAN), Bluetooth devices, Zigbee communications and other wireless network equipment. They enable data transmission and communication connections between wireless devices, supporting various application scenarios such as home networks, industrial automation and the Internet of Things (IoT).
Radar systems: Radar systems require high-frequency radio frequency signal processing and analysis to achieve target detection, tracking and positioning. RF PCBs play a key role in radar antennas, receivers, and signal processing modules to ensure the sensitivity and accuracy of radar systems.
Automotive radar: With the development of autonomous driving technology, automotive radar systems have become an important part of vehicle perception and safety. RF PCB is used in automotive radar sensors and modules to support communication and environmental awareness between vehicles, improving driver safety and comfort.
Medical diagnostic equipment: In the medical field, RF PCBs are used in various medical diagnostic equipment such as magnetic resonance imaging (MRI), ultrasound equipment, and vital signs monitors. They support data transmission, signal processing and image display of medical devices, helping doctors make accurate diagnosis and treatment decisions.
Satellite communications: Satellite communications systems require reliable RF signal transmission and processing to support communication links between satellites and data reception at ground stations. RF PCB plays an important role in satellite antennas, communication modules and ground station equipment to ensure the stability and coverage of satellite communication networks.
In general, the application fields of RF PCB cover various fields such as communications, automobiles, medical, military and aerospace, providing key technical support and solutions for various radio frequency applications. As wireless technology continues to develop and application requirements increase, RF PCB will continue to play an important role in promoting the innovation and development of wireless communication systems.
What are the advantages of RF PCB?
RF PCB has many advantages over traditional printed circuit boards (PCB) in radio frequency (RF) applications. These advantages include but are not limited to:
Optimized signal transmission performance: The design of RF PCB is optimized for high-frequency signal transmission, which can provide lower transmission loss, more stable signal transmission and better impedance matching, thereby ensuring high fidelity and reliability of signals.
Reduce signal interference and crosstalk: Optimization of RF PCB layout design, ground plane planning, and shielding technology can effectively reduce signal interference and crosstalk, and improve the system’s anti-interference capability and signal-to-noise ratio.
High-frequency characteristic stability: RF PCB uses high-frequency dielectric materials, such as PTFE (polytetrafluoroethylene), which has lower dielectric loss and higher dielectric constant, which can ensure stable transmission of signals in high-frequency environments and processing.
Flexibility and customizability: RF PCB can be customized and designed according to specific application requirements, including layout, material selection, impedance matching and shielding design, to meet the performance requirements of different RF systems.
Cost-effectiveness: Although the manufacturing and design process of RF PCB may be relatively complex, its optimized signal transmission performance and stability can reduce system maintenance costs and failure rates, and improve the overall cost-effectiveness of the system.
System integration and density improvement: RF PCB allows a high degree of integration of radio frequency components and functional modules, thereby reducing the connection lines, device spacing and volume in the system, achieving compactness and lightweight of the system.
Fast delivery and production: With the development of RF PCB manufacturing technology, modern manufacturing processes and automated production lines can improve the production efficiency and quality control level of RF PCB, shorten the delivery cycle, and meet market demand.
In summary, RF PCB has many advantages in wireless communication systems, which can improve the performance, stability and reliability of the system and promote the further development and application of wireless technology.
FAQ
What are the best layout practices for RF PCB?
In RF PCB design, best layout practices include reducing signal path length, minimizing signal crossing and circulation, avoiding cross-interference between RF signals and high-speed digital signals, rational placement of RF components and antennas, and optimizing ground plane design.
How to choose materials suitable for RF applications?
Materials suitable for RF applications typically have low loss, high frequency stability, and good impedance matching. Common materials include PTFE (polytetrafluoroethylene), FR-4 high-frequency dielectric materials and PTFE glass fiber composite materials.
What issues need to be paid attention to during the RF PCB manufacturing process?
During the RF PCB manufacturing process, special attention needs to be paid to maintaining high precision and control. Key issues include material selection, accurate printed circuit pattern production, control of the chemical etching process, accuracy and quality control of the assembly process, and final testing and validation.
How to manage signal interference and EMI issues in RF PCB design?
Managing signal interference and EMI issues in RF PCB design requires comprehensive consideration of factors such as layout, ground plane design, shielding measures, and signal coupling. Adopting good layout practices, optimizing ground plane design, using shields and isolation structures, and rationally selecting filters and attenuators can effectively reduce the impact of signal interference and EMI problems.