Organic Substrate FC-BGA Design Guideline.The Organic Substrate FC-BGA Design Guideline Manufacturing process is crucial in ensuring the reliability and performance of semiconductor packages. This process involves meticulous attention to material selection, substrate layering, and precise adherence to design guidelines to optimize thermal and electrical performance. It ensures robust interconnections, enhancing the functionality and longevity of advanced electronic devices.
In today’s electronics field, Printed Circuit Boards (PCBs) play a vital role. They are not only carriers of electronic devices, but also key components that connect and support various electronic components. Especially when designing high-performance and high-density electronic devices, proper PCB design is critical. This article will delve into the design guidelines for organic substrate FC-BGAs, providing engineers and enthusiasts with valuable guidance to help them avoid common pitfalls during the design process and ensure product performance and reliability.
What is organic substrate FC-BGA?
Organic substrate FC-BGA (Flip Chip Ball Grid Array) is an advanced electronic packaging technology that combines organic substrate and ball grid array technology. In this kind of package, the electrodes of the chip are directly connected to the pads on the substrate, and the electrical and mechanical connections are achieved through micro-ball solder joints. Organic substrate FC-BGA plays a vital role in electronic design as it provides a high-performance, high-density packaging solution for the increasingly complex circuit requirements in modern electronic devices.
The importance of organic substrate FC-BGA is reflected in many aspects. First of all, it has excellent electrical performance and signal integrity, can meet the requirements of high-speed and high-frequency circuits, and ensures the reliability and stability of signal transmission. Secondly, the organic substrate FC-BGA has a compact structure and high packaging density, which enables high integration and compact layout of circuits, helping to improve the performance and functionality of the device. In addition, due to the direct connection of solder joints, organic substrate FC-BGA has excellent thermal performance and heat dissipation, which can effectively reduce circuit temperature and improve device stability and reliability. Most importantly, the manufacturing process of organic substrate FC-BGA is mature, the cost is relatively low, and it is suitable for mass production, providing reliable technical support for the commercial application of electronic products.
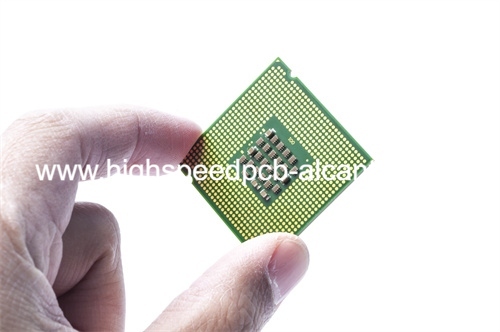
Organic Substrate FC-BGA Design Guideline
In summary, organic substrate FC-BGA is an advanced electronic packaging technology with excellent electrical performance, compact packaging structure and good thermal performance, providing an important solution for modern electronic design. It plays an irreplaceable role in high-performance, high-density circuit design and promotes the development and innovation of electronic products.
How to design organic substrate FC-BGA?
When designing an organic substrate FC-BGA, several key factors need to be considered to ensure the reliability and performance of the design. Here are some important considerations:
Circuit Layout and Routing Planning: Good circuit layout and routing planning are the keys to a successful design. Reasonable layout can minimize signal interference and crosstalk and improve the stability and reliability of the circuit.
Thermal Management: FC-BGA packages often face high-temperature environments in high-performance electronic devices. Therefore, effective thermal management measures, such as heat sinks, heat pipes, etc., must be considered in the design to ensure the normal operating temperature of the chip and circuit board.
Signal integrity: For high-speed signals and differential pair signals, special attention needs to be paid to signal integrity. Proper line width/line spacing, impedance control, and differential pair routing will all affect signal transmission quality.
Power distribution and stability: Reasonable power distribution is crucial to the performance and stability of the entire system. It is necessary to ensure that the power lines are evenly distributed to avoid the impact of voltage drops and voltage noise on the system.
Mechanical design and packaging selection: The mechanical design of FC-BGA packaging must take into account the convenience of assembly and maintenance, and at the same time, select packaging materials and packaging forms that suit the design requirements.
Manufacturability and testability: The convenience of production and testing should be taken into consideration when designing, including avoiding overly complex structures and layouts, and ensuring that the equipment can easily be automated for production and testing.
During the design process, simulation and circuit analysis tools can be used to evaluate the performance of the design, identify potential problems and optimize them. In addition, close cooperation with suppliers and manufacturers is also important to ensure the success of the design. Through careful design planning and effective collaboration, the high performance, high reliability and high stability of organic substrate FC-BGA can be achieved to meet the needs of various application scenarios.
What is the manufacturing process of organic substrate FC-BGA?
In the process of manufacturing organic substrate FC-BGA, there are many key steps to go through, each step is crucial and affects the quality and performance of the final product. Below we will introduce the manufacturing process of organic substrate FC-BGA in detail and discuss how to ensure that each step proceeds smoothly.
Before manufacturing begins, the required materials need to be prepared, including substrate material (such as FR-4), copper foil, solder mask, etc. The selection and quality of these materials will directly affect the performance and reliability of the final product.
In this step, multiple stacked substrate materials and copper foil are pressed together to form a multi-layer structure. This process requires ensuring uniform bond strength and thickness between each layer to avoid problems during subsequent processing.
Photolithography technology is used to pattern the circuits on the inner copper foil to form the basis for circuit connections. During this process, the parameters of the lithography equipment need to be precisely controlled to ensure the accuracy and clarity of the graphics.
Similar to the inner layer circuit pattern generation, this step patterns the circuits on the outer copper foil, including the positions and connections of components such as pads and connectors.
In this step, a solder mask is covered on the PCB surface, and photolithography is used to form patterns on the solder mask to protect the circuit from the external environment and provide accurate locations for soldering.
Use drilling equipment to drill holes in the PCB to provide through-holes for component mounting and connections. This step requires precise control of the location and size of the drilled holes to ensure consistency with design requirements.
The drilled surface and circuit pattern surface are electroplated to increase their conductivity and corrosion resistance. This step requires strict control of the composition and process parameters of the electroplating solution to ensure the stability of electroplating quality.
Use a chemical etchant to remove excess copper foil, leaving the desired trace pattern intact. This process requires strict control of the etchant concentration and etching time to avoid over-etching or under-etching problems.
Apply solder paste to the pads to provide solder points for component installation and connection. This step is required to ensure the uniformity and adhesion of the solder paste to ensure soldering quality.
In the final step, the PCB is put into molding and final inspection, including visual inspection, electrical testing, soldering quality inspection, etc. This step requires ensuring that the product meets design requirements and standards to ensure its performance and reliability.
By strictly controlling the quality and process parameters of each step, we can ensure that the organic substrate FC-BGA manufacturing process proceeds smoothly and ultimately obtain high-quality products.
How much does it cost to design an organic substrate FC-BGA?
The cost of designing an organic substrate FC-BGA is a critical issue that directly affects the project budget and the economics of the final product. Typically, the design cost of organic substrate FC-BGA will be affected by multiple factors, including but not limited to material selection, number of layers, line width/line spacing requirements, impedance control, pad shape, etc. The following will further explore how these factors affect design costs and provide some methods to control costs.
The design cost of organic substrate FC-BGA is closely related to the selected substrate material. Generally speaking, the cost of a substrate material depends on its performance characteristics and manufacturing difficulty. Common substrate materials such as fiberglass reinforced epoxy (FR-4) are relatively low in cost, while high-performance materials such as polyimide (PI) are higher in cost. Therefore, choosing the appropriate substrate material in design is one of the important factors in controlling costs.
The number of layers and complexity of organic substrate FC-BGA directly affects the manufacturing cost of the design. Typically, a multi-layer design costs more than a single-layer design because it involves more processing steps and material usage. In addition, high-complexity designs, such as high-density wiring and multi-layer board-to-board connections, also increase manufacturing costs. Therefore, during the design process, there is a trade-off between complexity and cost to ensure the desired performance and functionality are achieved.
The design cost of organic substrate FC-BGA is also affected by the design specifications and requirements. For example, strict line width/line spacing requirements, impedance control and pad shape can increase manufacturing costs. During the design process, it is necessary to fully understand the customer’s needs and make trade-offs based on the actual situation to achieve the goal of balancing cost and quality.
Although the design cost of organic substrate FC-BGA is affected by many factors, some measures can be taken to control the cost without sacrificing product quality. For example, rationally selecting substrate materials, selecting the appropriate number of layers and complexity based on project needs, optimizing design specifications and requirements, and working with suppliers to find cost-effective solutions, etc. In addition, using advanced design tools and technologies to improve design efficiency can also effectively reduce design costs.
In summary, the design cost of organic substrate FC-BGA is a complex and variable issue that requires comprehensive consideration of multiple factors. Through reasonable design and management, we can control costs and achieve successful project implementation without sacrificing product quality.
What materials are used in organic substrate FC-BGA?
Several key materials are involved in the design of organic substrate FC-BGA, each of which plays an important role in ensuring circuit performance, reliability and manufacturing cost. The following are the main materials used and their characteristics:
Organic substrate material: Organic substrate FC-BGA mainly uses glass fiber reinforced epoxy resin (FR-4) as the substrate material. FR-4 is a standard substrate material widely used in PCB manufacturing with good mechanical strength, heat resistance and chemical stability. Its insulating properties and processability make it an ideal substrate choice for electronic devices.
Copper foil: Copper foil is a common conductive material used in PCB manufacturing to form the wires, pads, and ground planes in circuits. The organic substrate FC-BGA uses high-purity copper foil, which has excellent electrical conductivity and good processability, ensuring the stability and reliability of the circuit.
Solder Mask: Solder mask is a polymer film that covers the surface of a PCB and is used to cover the pad area to prevent short circuits and oxidation. The organic substrate FC-BGA uses a high-quality solder mask with good corrosion resistance and heat resistance to ensure welding quality and circuit stability.
Solder: Solder is the material used to connect electronic components to the surface of a PCB, usually a tin-lead alloy or a lead-free alloy. Organic substrate FC-BGA uses high-quality solder to ensure good soldering connections and electrical performance.
Other auxiliary materials: In addition to the above main materials, the manufacturing process of organic substrate FC-BGA may also involve other auxiliary materials, such as surface treatment agents, barrier glue and protective films. These materials play an important supporting role in the PCB manufacturing process, ensuring manufacturing quality and final product reliability.
To sum up, the materials used in organic substrate FC-BGA have excellent mechanical properties, electrical conductivity and heat resistance, and can meet the strict requirements of high-performance electronic devices for PCBs. Choosing the right materials and ensuring the stability of the manufacturing process are one of the key factors to ensure the success of FC-BGA designs on organic substrates.
Who manufactures organic substrate FC-BGA?
The manufacturing of organic substrate FC-BGA involves critical supply chain collaboration, and the main responsibility falls on our company. As a company specializing in the manufacturing of high-performance electronic devices, we are committed to providing high-quality organic substrate FC-BGA and ensuring that it meets customer needs and industry standards.
Our company has advanced manufacturing equipment and technical teams, able to achieve full process control from design to manufacturing. In the process of manufacturing organic substrate FC-BGA, we use the most advanced production technology and strictly control each manufacturing step to ensure product quality and reliability.
In addition to in-house manufacturing, we work closely with our supply chain partners to ensure high-quality raw materials and components. The suppliers we select have been strictly screened and have good reputations and reliable quality assurance systems.
In the process of manufacturing organic substrate FC-BGA, we pay attention to details and quality control, and are committed to providing customers with high-performance, high-reliability products. We know that every link in the manufacturing process has an important impact on the quality of the final product, so we have adopted strict quality management measures to ensure that our products meet or exceed customer expectations.
In short, as a manufacturer of organic substrate FC-BGA, we will spare no effort to provide high-quality products and services to provide customers with solid support and guarantee for their electronic equipment design.
What are the five qualities of great customer service?
As a customer service provider, ensuring customer satisfaction is crucial. In a highly competitive market, excellent customer service can help companies build a good reputation, enhance customer loyalty, and achieve sustained business growth. Here are five key qualities that ensure great customer service:
Prompt response to customer inquiries and questions is one of the basic requirements for providing excellent customer service. Customers often expect their issues to be resolved quickly, so prompt responses to phone calls, emails, or online messages are crucial. When facing customer complaints or emergencies, you should act quickly and proactively solve the problem to avoid unnecessary delays or dissatisfaction.
Understanding your customers’ needs and treating their problems with compassion is the key to building great customer relationships. Customers want to feel respected and understood, not just treated as a transaction object. By listening to customer feedback and providing targeted solutions, you can effectively build trust and resonance and improve customer satisfaction.
Customers want to be able to rely on your product or service and expect you to consistently deliver on your promises. Whether it is about product delivery time, service quality or after-sales support, ensuring that your promises are fully realized is a basic requirement for providing excellent customer service. Building a solid reputation earns a business the trust and loyalty of its customers.
Clear, transparent communication is an important part of great customer service. When communicating with customers, make sure your messaging is clear and clear to avoid misunderstandings or unnecessary confusion. Timely informing customers of project progress, explaining product or service-related issues, and being willing to listen to customer feedback and suggestions will help establish good communication channels and enhance customer satisfaction.
Great customer service is not just about responding when customers ask questions, but more importantly about proactively seeking solutions to ensure that customers’ needs are met. Train employees to have problem-solving skills and provide the necessary support and resources to ensure that problems encountered by customers can be effectively resolved. Proactively solving problems not only meets customer expectations, but also builds a good reputation for the company and enhances its competitive advantage.
As customer service providers, we should emphasize the importance of the above traits and integrate them into our daily work by training and motivating our employees. By continuously improving service levels and continuously improving and improving the customer service system, we can ensure customer satisfaction and win a dominant position in market competition.
FAQS
What distinguishes organic substrate FC-BGA from traditional BGA packaging?
Organic substrate FC-BGA utilizes organic materials as its substrate, offering improved performance and thermal characteristics compared to traditional BGA packaging.
What is the typical design cycle for organic substrate FC-BGA?
The design cycle for organic substrate FC-BGA varies depending on project complexity, ranging from several weeks to a few months.
What soldering techniques are used for organic substrate FC-BGA?
Common soldering techniques for organic substrate FC-BGA include hot air reflow soldering, infrared reflow soldering, and wave soldering.
How do we evaluate the performance of organic substrate FC-BGA?
Evaluating the performance of organic substrate FC-BGA involves comprehensive electrical testing, thermal analysis, and reliability testing.
What is the environmental impact of organic substrate FC-BGA?
The environmental impact of organic substrate FC-BGA depends on the materials used and the manufacturing process. Adherence to relevant standards and certifications ensures environmental compliance.
How do we address signal integrity concerns in organic substrate FC-BGA designs?
Signal integrity concerns in organic substrate FC-BGA designs are addressed through careful layout planning, impedance control, and noise mitigation strategies.