Cavity Substrate| Package Substrate Manufacturing.Cavity substrate and package substrate manufacturing involve intricate processes pivotal to electronic component production. Cavity substrate fabrication typically includes etching, deposition, and bonding, forming precise recesses for integrated circuits. Meanwhile, package substrate manufacturing entails intricate layering, often using materials like fiberglass or laminate, meticulously crafted to host and interconnect electronic components. These substrates serve as the structural foundation for semiconductor devices, enabling efficient signal transmission and thermal management. In both processes, precision is paramount, ensuring optimal performance and reliability in diverse electronic applications.
In today’s digital society, where electronics dominate every aspect of our lives, understanding the complexities of cavity substrate manufacturing (CSM) has become critical. Although CSM is ubiquitous in modern electronics, the manufacturing process behind it remains mysterious to many. This comprehensive guide aims to demystify the mystery surrounding CSM, especially for beginners eager to master its essentials.
What is CSM?
CSM, or Cavity Substrate Manufacturing, is a manufacturing process specifically used to create printed circuit boards (PCBs) for specific design requirements. In CSM, an ideal placement space is provided for specific electronic components or systems by embedding cavities or grooves. These cavities or grooves not only provide mechanical support but also play a key role in electrical connections. By optimizing layout, CSM is able to maximize the performance of electronic devices and efficiently utilize available space.
The core concept of CSM is to solve the limitations and challenges in traditional PCB design. In traditional designs, electronic components are often placed on flat surfaces, which can lead to wasted space and poor performance. In CSM, designers can take advantage of the flexibility of embedded cavities to place components in a more compact and optimized space, thereby maximizing device functionality and efficiency.
The cavity substrate manufacturing process typically involves several key steps. First, designers use CAD software to design the layout and structure of the cavity substrate based on specific project needs and requirements. Next, the manufacturer will prepare the substrate based on the design files and use specialized milling or cutting techniques to create the required cavities or grooves in the substrate. Copper wires are then deposited onto the surface of the substrate to form circuit connections and surface treated to ensure conductivity and durability.
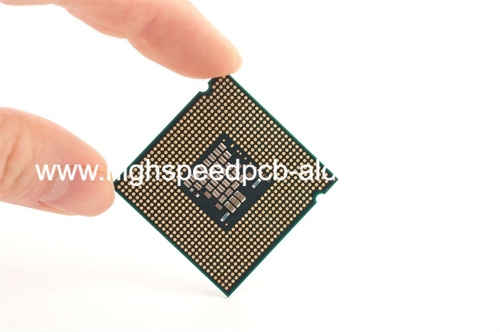
Cavity Substrate| Package Substrate Manufacturing
Cavity substrates fabricated by CSM offer many advantages. First, they provide more flexible design options, allowing designers to better optimize the layout and performance of electronic devices. Second, cavity substrates can significantly reduce the size and weight of electronic devices, allowing for more compact and lightweight designs. In addition, CSM can improve thermal management and electromagnetic compatibility, increasing equipment reliability and stability.
To sum up, CSM is an innovative manufacturing process that provides more efficient and compact solutions for electronic devices through the design of embedded cavities. Not only does it optimize performance and space utilization, it also provides designers with greater flexibility and creativity. As technology continues to develop and advance, CSM will continue to play an important role in the electronics manufacturing field and drive the industry forward.
How to design a cavity substrate?
Designing cavity substrates is a complex and delicate process that requires careful planning and execution. From concept to actual design, every step is critical to ensure the final cavity substrate meets the customer’s needs and requirements.
First, designing the cavity substrate requires thorough planning. This includes determining the size, shape, and location of the cavity, as well as determining the components or systems to be embedded within it. At this stage, the design team needs to work closely with the client to understand their needs and expectations to ensure the accuracy and feasibility of the design solution.
Next, the design team will begin conceptual layout. At this stage, they will integrate the design of the cavity with the overall layout, ensuring interaction and connectivity of the cavity with other components. This may involve multiple revisions and adjustments to achieve the best possible design effect.
Once the conceptual layout is determined, the design team will begin precisely placing components within the cavity. This requires taking into account the size, shape and location of each component, as well as their relationship to each other. By using CAD software such as Altium Designer or Mentor Graphics, design teams can perform layout designs in a virtual environment, ensuring each component is accurately placed within the cavity.
After the components are placed, the design team performs verification. This includes rigorous inspection and testing of the design to ensure that the cavity substrate functions and performs as expected. At this stage, any potential issues or defects will be promptly identified and resolved to ensure that the final cavity substrate meets the customer’s needs and standards.
Overall, designing cavity substrates is a complex and delicate process that requires careful planning and execution. Through comprehensive planning, conceptual layout, precise component placement and rigorous verification, the design team can ensure that the final cavity substrate will meet the customer’s needs and requirements, providing customers with a quality solution.
What is the manufacturing process of CSM?
The fabrication of cavity substrates is a complex multi-step process designed to ensure excellent performance and reliability of the final product. The key steps of cavity substrate manufacturing will be introduced in detail below:
The first step in fabricating a cavity substrate is to prepare the substrate material. Typically, the substrate is made of high-quality ceramic-filled polymer materials or other high-performance substrate materials. These materials require strict quality control and pre-treatment to ensure surface smoothness and chemical stability.
Next, specialized milling or cutting techniques are used to create cavities or grooves in the surface of the substrate. This step requires precision operations and a high degree of technical skill to ensure that the size and shape of the cavity meet the design requirements. Cavities are typically formed on one or both sides of the substrate to accommodate specific electronic components or systems.
After the cavity is formed, copper deposition needs to be performed on the substrate surface. Copper is an excellent conductive material that can effectively transmit electrical signals and energy. Through techniques such as chemical deposition or electrochemical deposition, a uniform layer of copper is formed on the surface of the substrate to build conductive paths and connection points.
Finally, the cavity substrate is surface treated to ensure optimal conductivity and durability. This may involve processes such as surface cleaning, anti-corrosion treatment or surface coating. The purpose of surface treatment is to protect the copper layer from the external environment while providing good solderability and reliability.
Through the above steps, after the cavity substrate is manufactured, it will undergo strict quality inspection and testing to ensure that it meets the design specifications and customer needs. This complex manufacturing process requires highly specialized techniques and sophisticated equipment to ensure the quality and performance of the final product meets industry standards.
In this process, manufacturers continue to strive to improve technology and processes to meet the growing market demand and provide customers with more reliable and high-performance cavity substrate solutions.
How is the fabrication of cavity substrates performed?
Once the design is finalized, the files are sent to the trusted CSM manufacturer, which marks the beginning of a critical stage of the manufacturing process. At this stage, manufacturers play a vital role. They not only have advanced machinery and equipment, but also have rich professional knowledge and experience, and can transform design files into actual cavity substrate products.
First, the manufacturer carefully reviews the design documents to ensure they match the customer’s requirements and specifications. This includes checking details such as layout, dimensions, material selection, etc. to ensure that the cavity substrate is produced to fully meet the customer’s needs.
The manufacturer will then utilize its advanced machinery and equipment for production. These include sophisticated CNC machine tools, automated assembly lines, and highly controllable chemical processing equipment. Through the cooperation of these devices, manufacturers can efficiently process, form and assemble cavity substrates.
During the manufacturing process, manufacturers strictly follow quality standards and schedules. They conduct multiple inspections and tests to ensure that each manufacturing step reaches the expected quality level. This includes inspection of substrate materials, accuracy testing of cavity processing, testing of electrical connections, etc.
At the same time, manufacturers also focus on communication and collaboration with customers. They regularly provide customers with production progress and quality reports to ensure customers understand and control the entire manufacturing process. If any problems or changes occur during the manufacturing process, the manufacturer will communicate with the customer in a timely manner and seek solutions to ensure the smooth progress of the project.
Overall, the manufacturer performs the cavity substrate manufacturing process in a precise, efficient and reliable manner, thereby providing customers with high-quality products and excellent services. Their professional knowledge and experience are key factors in ensuring the smooth progress of the manufacturing process and are also one of the important reasons why customers choose to cooperate.
Find out how much cavity substrates cost?
The cost of cavity substrates is a complex issue involving multiple factors. First, substrate material is one of the key factors that determine cost. Different types of materials have different costs, and the quality and performance of the materials will also affect the final price. For example, ceramic-filled polymer substrates are generally more expensive than traditional FR-4 materials, but also offer better thermal management and mechanical stability, so may be a more worthwhile investment in certain applications.
Secondly, the complexity of the cavity will also have an impact on cost. If the cavity design requires more processing steps or uses more advanced technology, manufacturing costs will likely increase. For example, deep cavities or very small cavities may require more precise machining processes, which may result in additional costs.
In addition, manufacturing volume is also one of the important factors affecting costs. Generally speaking, mass production can reduce the cost of each cavity substrate because manufacturers can save costs by purchasing raw materials in bulk and improving production efficiency. In contrast, low-volume production typically results in higher unit prices because fixed costs need to be spread over fewer products.
Although cavity substrates can be mid- to high-priced, the performance enhancement and space optimization benefits they bring often justify the investment. By using cavity substrates, electronic devices can use space more efficiently and achieve higher performance and reliability. And, if designed properly and the manufacturing process tightly controlled, cavity substrates can provide long-term stable performance, resulting in higher value and returns for customers.
So while cost may be a consideration, it should be considered a factor balanced against other factors such as performance and quality. By selecting the appropriate materials, design, and manufacturing processes, you can ensure the best cavity substrate solution for long-term success and satisfaction.
What materials are used in CSM?
In Cavity Substrate Manufacturing (CSM), the materials used are crucial as they directly affect the performance, reliability and durability of the cavity substrate. Typically, cavity substrates are made from high-quality materials, including ceramic-filled polymer substrates, copper for conductivity, and advanced dielectric materials for insulation and thermal management.
First, the polymer substrate is one of the main constituent materials of the cavity substrate. These substrates are typically made from polymer composites filled with ceramic particles. Ceramic-filled polymer substrates have good mechanical strength and stability and can withstand high-temperature and high-pressure environments, making them ideal for manufacturing cavity substrates.
Secondly, the conductive layer in the cavity substrate usually uses copper material. Copper is an excellent conductive material with good electrical and thermal conductivity, making it an ideal choice for manufacturing circuit connections in electronic devices. During the manufacturing process of the cavity substrate, copper is deposited on the surface of the substrate and the required circuit paths are formed through precise processing.
Finally, advanced dielectric materials for insulation and thermal management play a key role in the fabrication of cavity substrates. These materials have excellent insulating properties, effectively isolating circuits between conductive layers, and provide good thermal conductivity to help manage the temperature inside the cavity. By selecting the appropriate dielectric material, you can ensure that the cavity substrate maintains stable performance under a variety of operating conditions.
In summary, ceramic-filled polymer substrates, conductive copper, and advanced dielectric materials are the key materials necessary to create cavity substrates. Their selection and use directly affects the quality and performance of the cavity substrate, so these materials must be carefully selected and handled during the CSM process. Through reasonable material selection and precise manufacturing processes, the cavity substrate can be ensured to have excellent performance and reliability and meet the needs of various application scenarios.
Who are the key players in CSM manufacturing?
In the Cavity Substrate Manufacturing (CSM) ecosystem, key players include raw material suppliers, technology developers and manufacturers. However, manufacturers play a vital role in this process, shouldering the responsibility of converting design concepts into actual products and ensuring that the products meet quality standards and customer needs. Let’s take a closer look at the manufacturer’s role in CSM manufacturing.
In CSM manufacturing, a manufacturer usually refers to a company with advanced equipment, technology and expertise that can transform customers’ design concepts into actual cavity substrate products. These manufacturers have extensive experience and professional teams capable of handling a variety of complex manufacturing tasks and ensuring product quality and reliability.
The manufacturer’s role covers the entire production process, from raw material procurement and preparation to the production and assembly of cavity substrates. In CSM manufacturing, manufacturers must be able to understand customer needs and develop detailed manufacturing plans based on design specifications. They are responsible for selecting appropriate materials and utilizing advanced production equipment and technology to ensure product accuracy and consistency.
Manufacturers also assume strict quality control responsibilities by implementing rigorous inspection and testing procedures to ensure that each cavity substrate meets expected quality standards. They maintain close contact with customers, communicate production progress and project updates in a timely manner, and respond flexibly to any changes or requests made by customers.
In CSM manufacturing, choosing the right manufacturer is crucial. Excellent manufacturers are not only able to provide high-quality products, but also provide professional technical support and excellent customer service to help customers solve various technical and manufacturing challenges.
All in all, manufacturers play a key role in CSM manufacturing. They provide customers with customized cavity substrate solutions through professional technology and excellent services, promoting the development and innovation of the electronics industry.
What are the characteristics of excellent customer service in CSM?
In Cavity Substrate Manufacturing (CSM), excellent customer service is a key factor in ensuring customer satisfaction and building long-term relationships. The following are the characteristics of great customer service in CSM:
In the CSM manufacturing process, timely and effective communication is crucial to meeting customer needs. Quality service providers ensure timely responses to customer inquiries and feedback to resolve issues and maintain customer trust and satisfaction. Whether it is about order status, design modifications or technical support, rapid response to customers can reflect the professionalism and responsibility of the service provider.
Quality customer service providers have in-depth industry knowledge and technical expertise to provide customers with accurate guidance and advice. They understand their customers’ needs and challenges and are able to provide tailored solutions to ensure optimal manufacturing results. By establishing a close working relationship with customers, service providers can help customers optimize their designs and meet their requirements to the greatest extent possible.
CSM projects often face changing customer needs and project specifications. In this situation, quality customer service providers demonstrate flexibility and adaptability, being able to quickly adjust programs and schedules to meet new customer requirements. They maintain close communication with customers, keep abreast of changes and make corresponding adjustments to ensure that the project proceeds smoothly and achieves expected goals.
Quality customer service providers always put quality first and are committed to providing high-quality cavity substrates that meet or exceed industry standards. They use advanced manufacturing technology and strict quality control processes to ensure that every step is of the highest standard. Through continuous monitoring and improvement, they continuously improve product quality and provide customers with reliable solutions.
In CSM projects, clear and transparent pricing, timelines, and project updates are critical to building trust and confidence. A quality customer service provider will maintain open communication with their clients and provide detailed information and reports to keep them informed of project progress and expected results. Transparency not only helps customers understand project status, but also helps reduce misunderstandings and disputes and establish good cooperative relationships.
To sum up, excellent customer service plays a vital role in the CSM field. Through prompt response, expertise, flexibility, quality assurance and transparency, service providers are able to meet their customers’ needs and build long-term relationships to jointly achieve business goals.
Frequently Asked Questions
What are the advantages of using cavity substrates in electronic design?
Cavity substrates offer several advantages in electronic design, primarily centered around improved performance and efficiency. Firstly, cavity substrates facilitate enhanced thermal management by providing a dedicated space for heat dissipation, thereby reducing the risk of component overheating and extending device lifespan. Additionally, the embedded cavities minimize electromagnetic interference (EMI) by isolating sensitive components from external electromagnetic fields, resulting in improved signal integrity and reliability. Moreover, cavity substrates enable greater design flexibility, allowing for compact and streamlined electronic devices without compromising functionality. Overall, the utilization of cavity substrates in electronic design enhances both the performance and reliability of electronic systems.
How long does it take to manufacture custom cavity substrates?
The manufacturing lead time for custom cavity substrates can vary depending on several factors, including complexity, design specifications, and production volume. Typically, the process involves multiple stages such as design validation, substrate fabrication, cavity formation, metallization, and quality testing. As such, the lead time may range from several weeks to a few months, with more intricate designs and larger quantities requiring longer production durations. However, many manufacturers offer expedited services for urgent orders or prioritize certain projects based on client requirements. It’s essential to communicate closely with the chosen manufacturer to establish realistic timelines and ensure timely delivery of custom cavity substrates.
Are there any eco-friendly practices in cavity substrate manufacturing?
Yes, there is a growing emphasis on incorporating eco-friendly practices into cavity substrate manufacturing to minimize environmental impact and promote sustainability. One common approach is the adoption of green materials and processes, such as utilizing recycled or biodegradable substrate materials and eco-friendly surface finishes. Additionally, manufacturers are implementing energy-efficient manufacturing technologies and optimizing resource utilization to reduce waste generation and energy consumption. Furthermore, some companies prioritize environmentally responsible disposal methods for waste materials and strive to minimize carbon emissions throughout the production process. By embracing eco-friendly practices, cavity substrate manufacturers aim to balance technological advancement with environmental stewardship, contributing to a greener and more sustainable future.