Wire Bond Substrate Manufacturer, BGA package substrates will be made with Wire Bonding. The best surface treatment process is ENEPIG. the Wire Bonding result will be more better than other surface treatment process. We will produce the surface treatment process according to your requirements.
Wire Bond Substrate is a vital technology in the field of electronic engineering. It connects chips and other electronic components through wire bonding technology, bringing unique value to circuit board design.
This technology’s essence lies in its capacity to establish dependable connections between chips and circuit boards within a compact space. Utilizing a meticulous wire bonding process, the Wire Bond Substrate ensures precise connections to chip pins, facilitating rapid and stable signal transmission among electronic components. This technology not only is pivotal for achieving highly integrated circuit designs but also offers robust assistance in the miniaturization and lightweighting of electronic devices.
First, it enables reliable connections between chips of different sizes and types, promoting the collaborative work of various electronic components. Secondly, wire bonding technology can achieve more connections in a limited space, thereby improving the integration of the circuit board. This is critical given the complexity and performance requirements of modern electronic devices.
Another significant advantage is the excellent performance of Wire Bond Substrate in heat dissipation. The design and material selection during the wire bonding process allows heat to be efficiently transferred and dissipated, helping to maintain the good working condition of the chip and the entire electronic device. This is especially important for high-performance devices and long-running applications.
Wire Bond Substrate is a crucial driver of innovation in contemporary electronic engineering. It utilizes wire bonding technology to connect chips and electronic components, enabling high integration, miniaturization, lightweight design, and efficient heat dissipation on circuit boards. As electronic devices become more complex, the continued use of Wire Bond Substrate will be instrumental in advancing technology and fostering development in electronic engineering.
What types of Wire Bond Substrate are there?
In the electronic field, various wire bond substrates are utilized, with prominent types being BGA (Ball Grid Array) and CSP (Chip Scale Package). BGA features a layer of small solder balls on the chip’s bottom, offering increased connection points and reduced component size. Widely applied in high-density integrated circuits and microprocessors, BGA’s three-dimensional structure enhances device integration and reliability.
In comparison, CSP is a packaging technology that reduces the chip size as much as possible. The characteristic of CSP is that the package fits the real size of the chip as much as possible, avoiding the extra space waste that may occur in traditional packages. This makes CSP widely used in thin and light electronic devices, such as smartphones, wearable devices, etc. Its compact design reduces device size and improves system performance.
When selecting a wire bonding substrate type, the specific application scenario needs to be considered. BGA is suitable for applications that require a high degree of integration, such as central processing units that process large amounts of data. For devices that emphasize thin and light design, CSP is the ideal choice. In addition, different types of wire bonding substrates also have differences in thermal management, maintainability, etc., which need to be weighed according to specific project requirements.
Overall, BGA and CSP, as the two mainstream types of wire bonding substrates, have shown strong application potential in different fields. Engineers and designers should carefully select the appropriate wire bonding substrate type based on factors such as project requirements, performance needs, and space constraints to achieve optimal electronic device designs.
What are the advantages of Wire Bond Substrate?
Wire Bond Substrate is a crucial element in modern electronic engineering, offering distinct advantages over traditional circuit boards. Its higher level of integration, facilitated by wire bonding technology, allows for tighter connections of electronic components in a smaller space. This enables more intricate and compact circuit layouts, resulting in smaller devices with improved overall performance and efficiency compared to traditional circuit boards.
As electronic devices develop towards thinner, lighter and more portable devices, Wire Bond Substrate has significant size advantages. Compared with traditional circuit boards, its size is smaller and provides greater design freedom for equipment. This makes it possible to implement more functions in a limited space, facilitating the design of various consumer electronics and portable devices.
The Wire Bond Substrate demonstrates exceptional thermal performance. Utilizing wire bonding technology, chips and other electronic components can efficiently transfer heat, thereby reducing the operating temperature of the equipment and prolonging the lifespan of the components. This superior heat dissipation capability not only enhances device stability but also addresses the heat dissipation challenges associated with high-performance electronic systems.
Designers can more flexibly lay out electronic components to achieve more advanced functionality and performance. This design flexibility provides electronic engineers in various fields with greater room for innovation and promotes the continuous development of electronic technology.
In general, Wire Bond Substrate, characterized by high integration, small size, and excellent heat dissipation performance, offers electronic engineers greater design flexibility, resulting in more advanced, compact, and efficient electronic devices. With the ongoing progress of technology, Wire Bond Substrate is poised to maintain a crucial role in the electronics industry.
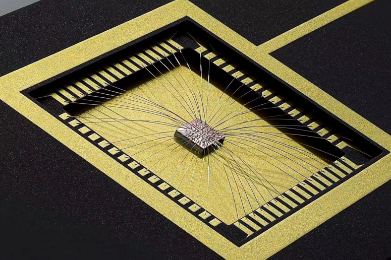
Wire Bond Substrate
Why choose Wire Bond Substrate in your design?
In the contemporary field of electronic engineering, engineers are increasingly focusing on innovative circuit board selection to achieve technological breakthroughs and enhance performance. Among these choices, Wire Bond Substrate has become a preferred option for many projects due to its distinctive advantages.
One of its main advantages is its high level of integration. Wire Bond Substrate distinguishes itself by its capacity to accommodate a greater number of components and connections in comparison to conventional circuit boards. This leads to a more condensed and efficient design, a critical factor for compact electronic devices like smartphones and portable computers. In situations where space is restricted, optimizing integration becomes vital to fulfill functional necessities.
Wire Bond Substrate not only offers design flexibility but also excels in adapting to diverse scenarios. It is compatible with various chip packaging methods, including BGA and CSP, allowing engineers to choose based on the specific requirements of their projects. This adaptability makes Wire Bond Substrate well-suited for a wide range of electronic devices, spanning from consumer products to industrial applications.
Improve production efficiency
During the manufacturing process, Wire Bond Substrate’s high degree of integration and design integration helps streamline the production process. With fewer assembly steps and a more compact design, manufacturers are able to produce large quantities of devices more quickly and efficiently. This has significant competitive advantages in meeting market demand and accelerating product launch.
To sum up, the selection of the Wire Bond Substrate in the design is intentional and not arbitrary. Its distinct advantages, such as high integration, compact size, exceptional heat dissipation performance, flexibility, adaptability, and enhanced production efficiency, render it an indispensable asset in contemporary electronic engineering projects. Capitalizing on these strengths enables engineers to innovate, enhance performance, and meet the increasing demands of the market more effectively.
What is the manufacturing process for Wire Bond Substrate?
The following will provide an in-depth understanding of the manufacturing process of Wire Bond Substrate, focusing on the unique features of the motherboard and base plate throughout the process and the advanced technologies and processes used.
The process of manufacturing Wire Bond Substrate typically includes the following key steps:
Material preparation: First, select high-quality substrate materials, usually special conductive materials, to ensure good electrical properties and mechanical strength.
Motherboard design and preparation: The motherboard is the core component of the wire bonding substrate. Designers draw motherboards based on specific application requirements and circuit designs.
Backplane Preparation: Backplanes are commonly employed to provide support and safeguard the motherboard. Select the appropriate baseboard material and ensure compatibility with the motherboard for optimal performance.
Wire Bonding: Wire bonding is a crucial step in the manufacturing of Wire Bond Substrates. This technology establishes connections between chips and the motherboard using metal wires. Achieving a robust and reliable connection necessitates the use of high-precision equipment and technology during this process.
Encapsulation: After wire bonding is completed, the entire assembly is encapsulated to improve mechanical strength and protective performance. This helps prevent external environmental effects on the wire bond.
Testing and quality inspection are crucial steps following the completion of Wire Bond Substrate manufacturing. These processes encompass electrical performance testing, mechanical strength testing, and other essential performance verifications.
Throughout the manufacturing of Wire Bond Substrate, a diverse range of advanced technologies and processes are employed to enhance product performance and reliability. Microelectronics technology enables the integration of more components on a compact motherboard, achieving higher levels of integration.
The implementation of automated production lines serves to boost manufacturing efficiency and mitigate the risk of human error. Furthermore, advanced conductive materials and packaging materials are meticulously chosen to meet stringent requirements for high performance and durability.
Three-dimensional packaging technology plays a pivotal role, facilitating increased connections and optimal component layout within confined spaces. The amalgamation of these advanced technologies and processes enables the manufacturing of Wire Bond Substrate to seamlessly align with the demands of contemporary electronic equipment, particularly in the realm of small, high-performance components. This, in turn, provides dependable electronic connection solutions for diverse application scenarios.
In what areas is Wire Bond Substrate used?
The Wire Bond Substrate, a crucial electronic component, plays a vital role in a variety of electronic devices across diverse industries. Its widespread use, especially in smartphones, computers, and communication devices, is pivotal for improving the performance and functionality of these devices.
Smartphones stand out as a prominent application area for Wire Bond Substrate. In contemporary mobile phone designs, the emphasis on space efficiency is paramount, making Wire Bond Substrate highly preferred due to its compact size and advanced integration capabilities. This substrate facilitates a reliable connection between the chip and the circuit board through wire bonding technology, resulting in improved performance and reduced device size for mobile phones. Additionally, the application of Wire Bond Substrate contributes to enhanced heat dissipation in smartphones, ensuring stable operation even with high integration levels.
Wire Bond Substrate plays a pivotal role in the field of computers. In the development of high-performance computers and servers, wire bonding substrates provide reliable support for processors and other chips, thanks to their outstanding electrical connectivity and heat dissipation capabilities. This not only enhances the overall performance of computer systems but also enables them to efficiently tackle demanding computing tasks.
Another important application area is communication equipment. In wireless communication equipment, base stations and network equipment, Wire Bond Substrate enables these devices to achieve more functions in a limited space through its highly integrated features. The use of wire bonding technology improves the signal transmission speed and reliability of devices and helps meet growing communication needs.
Overall, the wide application of Wire Bond Substrate plays a vital role in electronic devices. Whether it is to pursue smaller size, higher performance, or to cope with high-load computing and communication needs, wire bonding substrates are driving the continuous innovation and development of the electronics industry. Its successful application in fields such as smartphones, computers, and communication equipment further confirms its importance in modern electronic engineering.
How do I find the Wire Bond Substrate manufacturer?
When seeking a reliable Wire Bond Substrate manufacturer, selecting the right partner is paramount. The following recommendations can assist you in identifying suppliers recognized in the industry to ensure optimal support for your project.
Evaluate production capacity and delivery timelines as they are crucial to project progression. Confirm that the chosen manufacturer has sufficient production capacity to meet your requirements and can adhere to specified delivery schedules. Understand their production processes and equipment to ensure alignment with the size and time constraints of your project.
Identify which Wire Bond Substrate manufacturers have been selected by companies in your industry and gather insights from their experiences. This information can be obtained through participation in industry events, forums, or direct communication with industry professionals. Leveraging the experiences of other companies can assist in selecting the manufacturer that best aligns with your needs.
Finally, direct communication with potential suppliers is very important. Discuss your project needs, expectations and standards with them, understand their perspective on the collaboration, and ensure there is clear communication and understanding between both parties. This helps build strong partnerships and ensure successful project implementation.
When looking for a Wire Bond Substrate manufacturer, the above suggestions can help you choose a reliable and technically capable partner to ensure the smooth progress of your project.
How to get a quote for Wire Bond Substrate?
In the manufacturing and application of Wire Bond Substrate, understanding its quotation is a key part of formulating feasible solutions. This article will guide readers on how to obtain a quote for Wire Bond Substrate, explore general market pricing and the main factors that affect the price.
For individuals seeking a quote on Wire Bond Substrate, the most direct approach is to reach out to the relevant manufacturer or supplier.Additionally, valuable information and contacts can be obtained through online resources and industry exhibitions.
The market pricing of Wire Bond Substrate is influenced by various factors, with material cost, manufacturing process complexity, market demand, competition, and technological innovation being the most significant. While there exists a general price range in the market, specific pricing varies among manufacturers and geographical locations.
The cost of materials significantly influences the pricing of Wire Bond Substrates, as employing high-performance materials and specialized procedures can escalate production expenses. Pricing is further influenced by the intricacy of the manufacturing process, with more complex procedures commanding higher prices due to increased difficulty.
Market demand serves as a pivotal determinant; heightened demand may prompt manufacturers to increase prices, whereas reduced demand could result in price reductions. The dynamic element of competition among manufacturers also shapes pricing trends. Intense competition typically exerts downward pressure on prices, while monopolistic trends may lead to upward price adjustments.
However, these innovations may contribute to higher production costs, influencing overall prices. Understanding these factors when obtaining a quote empowers buyers to comprehend the dynamics of Wire Bond Substrate price formation and make informed purchasing decisions.
The quotation of Wire Bond Substrate is an important consideration when formulating an electronic engineering plan. By proactively contacting manufacturers, understanding market pricing trends, and understanding the factors that affect price, readers will be able to better understand the actual cost of Wire Bond Substrate and make informed decisions in their projects.
What are the frequently asked questions about Wire Bond Substrate?
What advantages does Wire Bond Substrate offer compared to traditional circuit boards?
Wire Bond Substrate boasts several advantages, such as higher integration levels, smaller form factors, and excellent thermal performance. Exploring these benefits provides insight into why it is preferred over traditional circuit boards in many electronic designs.
Why should one choose Wire Bond Substrate in electronic design?
This section delves into the specific reasons and unique advantages that make Wire Bond Substrate a preferable choice in electronic design over other types of circuit boards.
How can individuals obtain quotes for Wire Bond Substrate, and what factors influence pricing?
This section guides readers on the practical steps to obtain quotes for Wire Bond Substrate, offering insights into general market pricing and the factors that can influence the overall costs.
What are some common questions and concerns related to Wire Bond Substrate?
This FAQ section addresses common questions and concerns, providing clarity on various aspects of Wire Bond Substrate to help readers navigate its applications more effectively.
Wire Bond Substrate FAQs
What advantages does Wire Bond Substrate offer?
Wire Bond Substrate presents several advantages over traditional circuit boards, such as higher integration levels, smaller form factors, and superior heat dissipation capabilities. These attributes make it a preferred choice in many electronic device designs.
Why choose Wire Bond Substrate in design?
Comparatively, why opt for Wire Bond Substrate over other circuit boards in practical engineering scenarios? Understanding its unique advantages in real-world applications is crucial for informed decision-making.
What is the manufacturing process of Wire Bond Substrate?
Explore the key steps in the manufacturing process of Wire Bond Substrate, encompassing both main and bottom boards. Discover the advanced technologies and processes employed during production.