Radio Frequency PCB Manufacturer.A Radio Frequency PCB Manufacturer specializes in designing and producing printed circuit boards (PCBs) tailored for radio frequency (RF) applications. These manufacturers ensure that PCBs can handle high-frequency signals with minimal interference and signal loss, crucial for devices like wireless communications, radar systems, and satellite technology. They employ advanced materials and precision engineering to meet stringent performance and reliability standards, making them essential partners for cutting-edge RF technology development.
Radio Frequency PCB plays a vital role in the field of modern communications. They are not only carriers that connect various components of electronic equipment together, but more importantly, they provide a stable and efficient signal transmission platform for wireless communication systems. Due to the sensitivity of radio frequency signals to frequency and interference, the design and manufacturing of Radio Frequency PCB must follow strict standards and technical requirements. Therefore, the excellent performance of Radio Frequency PCB directly affects the reliability and performance of the wireless communication system.
What is Radio Frequency PCB?
Radio Frequency PCB (radio frequency printed circuit board) is a circuit board specially designed to handle wireless communication signals. In wireless communication systems, high-frequency signal transmission requires circuit boards with excellent performance and stability to ensure reliable transmission of data and maintenance of communication quality. Therefore, Radio Frequency PCB uses special materials and layout to meet these needs.
First of all, Radio Frequency PCB usually uses materials with low dielectric constant and low loss characteristics, such as polytetrafluoroethylene (PTFE), etc. These materials can effectively reduce energy loss and signal distortion during signal transmission, thereby improving the signal-to-noise ratio and transmission efficiency of the system. In addition, Radio Frequency PCB may also use ceramic substrates because of its excellent high-frequency characteristics and high-temperature resistance.
Secondly, the layout and design of Radio Frequency PCB are also very critical. To minimize signal interference and crosstalk, circuit board routing and placement of distributed components need to be carefully designed and optimized. At the same time, the design of grounding technology and power distribution network is also crucial to ensure the electrical performance and stability of the entire system.
In short, Radio Frequency PCB plays a vital role in modern wireless communication systems. They can not only achieve reliable transmission of high-frequency signals, but also meet the performance, stability and size requirements of different application scenarios. Therefore, Radio Frequency PCB is an indispensable key component for various wireless communication devices, from mobile phones to satellite communication systems to IoT devices.
Radio Frequency PCB design Reference Guide.
When designing Radio Frequency PCB, special attention needs to be paid to signal transmission frequency and minimizing interference. Below are some key recommendations to optimize your design and ensure its performance stability in high-frequency environments.
Circuit layout
When designing an RF PCB, good circuit layout is crucial. To minimize signal transmission path lengths and current loops, signal lines should be kept as short and straight as possible. In addition, avoid crossing and parallel arrangement of signal lines to reduce crosstalk and mutual influence.
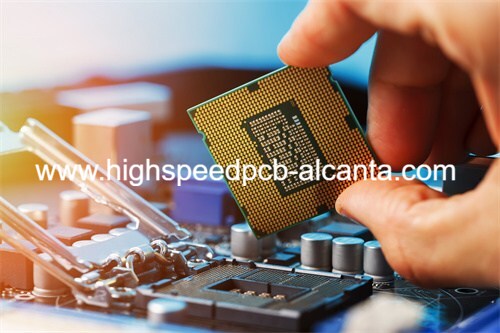
Radio Frequency PCB Manufacturer
Grounding technology
Effective grounding is an integral part of RF PCB design. Using a large ground plane can help reduce the impedance of the ground loop and reduce the signal noise introduced by the ground loop. At the same time, good ground connection and laying should be ensured to reduce the instability of ground loops and electromagnetic interference.
Antenna design
For wireless communication applications, antenna design is a crucial part. Select the appropriate antenna type and layout to ensure the best match to the expected frequency range. Optimize the impedance matching and radiation efficiency of the antenna to maximize signal transmission and reduce power consumption.
Thermal management
High-frequency circuits often generate large amounts of heat, so effective thermal management is critical. Consider heat sink layout and materials during the design process to ensure that circuit components can maintain stable temperatures during long periods of high-load operation.
Material selection
Choosing the right materials is critical to RF PCB performance. Materials with low dielectric constant and low loss factor are preferred to reduce loss and distortion during signal transmission. For high-frequency applications, special materials such as PTFE (polytetrafluoroethylene) are often used to improve performance.
By following the above guidelines and recommendations, designers can ensure that Radio Frequency PCBs perform well in high-frequency environments and meet the requirements and performance standards of their applications.
What material is used in Radio Frequency PCB?
When designing and manufacturing Radio Frequency PCBs, it is crucial to choose appropriate materials because these materials directly affect the performance and stability of the circuit board in high-frequency environments. Typically, Radio Frequency PCB will use a ceramic substrate or a special low dielectric constant material, of which PTFE (polytetrafluoroethylene) is a common choice.
Ceramic substrates have excellent electrical properties and thermal stability, providing excellent signal transmission and anti-interference capabilities at high frequencies. They are commonly used in RF applications that require extremely high performance, such as radar systems, satellite communications, and antenna arrays.
PTFE, on the other hand, is a very low dielectric constant material with excellent dielectric properties and high temperature resistance. It can reduce signal loss and crosstalk, thereby improving the performance and stability of Radio Frequency PCB in high-frequency environments. PTFE is often used as a base material or dielectric spacer for RF circuit boards to support the design of microstrip antennas and high-frequency circuits.
These special materials were chosen to ensure that Radio Frequency PCBs can provide optimal signal transmission and performance at high frequencies while minimizing signal loss, crosstalk and other undesirable effects. Through appropriate material selection and design optimization, Radio Frequency PCB can meet the strict performance and reliability requirements of various wireless communication systems, providing a reliable foundation for the development of modern wireless communication technology.
What size are Radio Frequency PCB?
Radio Frequency PCB size is a crucial factor in design and application, which directly affects the performance and efficiency of the circuit board. RF circuit board size typically depends on the application requirements and the wavelengths of the specific frequency bands being processed. During the design process, engineers must consider the impact of board size on signal transmission and reception, as well as the impact on the overall system.
For some miniature wireless devices, such as smartphones, Bluetooth headsets, etc., RF circuit boards usually need to be very small in size to accommodate the compact design and space constraints of the device. These tiny RF circuit boards may be chip-sized or even smaller because they need to integrate as many functions and components as possible in a limited space. In this case, the size of the RF PCB is crucial to achieve high performance and stable wireless connections.
However, in some large communication systems, such as base stations, radar systems, etc., the size of the RF circuit board may be relatively large. This is because these systems need to handle higher frequency signals, requiring more antenna elements and circuit components to support the transmission and reception of signals. In this case, the RF PCB is usually designed as a large base station antenna array to ensure adequate signal coverage and performance.
Regardless of the size of the RF circuit board, careful design and optimization is required to ensure optimal signal transmission and reception within a specific frequency band. This includes considering factors such as circuit layout, antenna design, signal transmission lines, etc. to minimize signal loss and interference and improve system performance and stability.
Therefore, the size of the RF circuit board is not just a simple number, but an important parameter closely related to the overall system design and performance, which requires careful consideration and optimization during the design process.
The Manufacturer Process of Radio Frequency PCB.
The manufacturing process of Radio Frequency PCB is a complex and precise process that covers multiple key steps, each of which directly affects the performance and reliability of the final product. The following is a detailed introduction to the Radio Frequency PCB manufacturing process:
Design
First, designers need to design the circuit based on customer needs and application requirements. In RF applications, the design process is particularly critical because the frequency and wavelength of signal transmission must be taken into account. Designers use professional design software to draw circuit diagrams and determine layout and connections.
Material selection
For Radio Frequency PCB, material selection is crucial. Usually materials with low dielectric constant and low loss are used, such as PTFE (polytetrafluoroethylene) or FR-4 substrate. The choice of materials directly affects the quality and stability of signal transmission.
Printing
Once the design is complete and the appropriate materials selected, the next step is the process of printing the design pattern onto the substrate. This is usually accomplished through techniques such as layer-by-layer stacking, photolithography, and etching, ensuring that circuit patterns are accurately transferred to the substrate.
Chemical etching
After printing is complete, chemical etching techniques are used to remove unwanted metal, exposing the required wires and connectors for the circuit board. This step requires precise control to ensure that the details and subtle connections on the circuit board are preserved.
Metalization
After etching, the circuit board needs to be metallized to enhance conductivity and protect the circuit pattern. This usually involves coating the circuit pattern with a layer of metal, such as copper or gold plating, to ensure good conductivity and durability.
Assemble
Finally, the completed circuit boards are sent to the assembly line for assembly. This includes soldering components, connecting wiring and conducting final testing. In RF applications, the assembly process is especially important because any loose connections or poor soldering can cause signal loss or interference.
The manufacturing process of Radio Frequency PCB requires sophisticated equipment and technology to ensure that the quality and performance of the final product meet expectations. Each step must be strictly controlled to meet the requirements for high-frequency signal transmission, thereby providing reliable support for wireless communication systems.
The Application area of Radio Frequency PCB.
Radio Frequency PCB (radio frequency printed circuit board) plays a vital role in modern wireless communication systems. Its application fields are very wide, covering various wireless communication equipment and systems. Here are some of the main application areas:
Cell phone communication
In smartphones and other mobile communication devices, Radio Frequency PCB is used to process and transmit wireless signals, including baseband processing of mobile phones, radio frequency transceiver modules, antenna connections and power amplification functions.
Satellite Communications
Satellite communication systems rely on highly reliable radio frequency circuits to enable two-way communication between ground stations and satellites. Radio Frequency PCB is used for key components such as radio frequency front-end, power amplifier and antenna driver of ground stations.
Radar system
Radar systems require high frequency, high speed and high precision signal processing. Radio Frequency PCB plays an important role in the radar antenna array, signal processor and control unit to ensure the performance and accuracy of the radar system.
Wireless LAN (Wi-Fi)
Wi-Fi networks use radio frequency technology to provide high-speed Internet access within a wireless local area. Radio Frequency PCB is used in Wi-Fi routers, wireless access points and wireless client devices to ensure stable signal transmission and high-speed data transmission.
IoT devices
IoT devices connect various smart sensors, controllers and devices, enabling wireless communication and data exchange between devices. Radio Frequency PCB plays a key role in IoT devices, including sensor nodes, data collectors, and IoT gateways.
Overall, Radio Frequency PCB has a wide range of applications in wireless communication systems, ranging from personal devices to large infrastructure. Their high performance, reliability and flexibility make them a core component of modern wireless communication technology, driving continued development and innovation in the field of wireless communications.
What are the advantages of Radio Frequency PCB?
The advantages of Radio Frequency PCB (radio frequency printed circuit board) become particularly significant when we consider the design and manufacturing of modern wireless communication systems. Radio Frequency PCB brings a number of important advantages over traditional wiring technologies that make it the preferred choice.
First, Radio Frequency PCB has better performance. At high frequencies, traditional wiring techniques are prone to signal loss, crosstalk and attenuation. The use of radio frequency printed circuit boards can effectively reduce these problems, thereby improving the performance and reliability of wireless communication systems. This means clearer and more stable signal transmission, better communication coverage and faster data transmission speeds.
Secondly, Radio Frequency PCB has a higher level of integration. Because its design and manufacturing process are highly controllable, multiple functional modules, such as RF amplifiers, filters, tuners and antennas, can be integrated on the same circuit board. This level of integration can not only reduce the size and weight of the device, but also reduce the complexity and power consumption of the system and improve overall performance.
Finally, Radio Frequency PCB has a smaller size. In modern wireless communication systems, device size requirements are becoming increasingly stringent, especially in mobile devices and embedded systems. RF printed circuit boards can be designed in very compact sizes to accommodate a variety of space constraints, providing greater flexibility and freedom in device design and layout.
To sum up, Radio Frequency PCB has significant advantages in modern wireless communication systems. Its better performance, higher integration and smaller size make it the preferred technology in wireless communications. With the continuous development of wireless communication technology and the expansion of its application scope, the importance of RF printed circuit boards will be further highlighted, bringing more possibilities and opportunities to our communication world.
FAQ
How is Radio Frequency PCB different from traditional PCB?
Radio Frequency PCBs are specifically designed to handle high frequency signals, using special materials and layout to minimize signal loss and interference. In contrast, traditional PCB is more suitable for low-frequency signals and general electronic equipment.
What aspects need special attention in the design of Radio Frequency PCB?
When designing a Radio Frequency PCB, special attention needs to be paid to the frequency of signal transmission, impedance matching, ground wire layout, and the transmission path of RF energy. Any oversight may result in performance degradation or signal distortion.
What applications are Radio Frequency PCB suitable for?
Radio Frequency PCB is widely used in wireless communication systems, including mobile phones, satellite communications, radar, wireless LAN, Internet of Things equipment, etc. They are also used in areas such as radio frequency identification (RFID) systems and medical equipment.
Is the manufacturing process of Radio Frequency PCB complicated?
Yes, the manufacturing process of Radio Frequency PCB is relatively complex and requires the use of special materials and processes to meet the requirements in high-frequency environments. In addition, precision design and manufacturing steps ensure the quality and performance of the final product.
How much does Radio Frequency PCB cost?
Because Radio Frequency PCB requires the use of special materials and processes, its manufacturing cost is usually higher. However, as technology develops and production scale increases, costs are gradually falling, making it more popular and affordable.