What is Ultrathin LED PCB?
A leading innovator in electronics, our company stands out as a premier Ultrathin LED PCB Manufacturer. With cutting-edge technology and meticulous craftsmanship, we specialize in crafting ultra-slim printed circuit boards that power the next generation of LED displays. Our expertise lies in precision engineering, enabling us to create PCBs that are not only remarkably thin but also robust and reliable. From concept to production, we are dedicated to delivering unparalleled quality, ensuring our clients receive products that exceed expectations in performance, durability, and efficiency. Trust us to illuminate the future with our advanced LED PCB solutions.
Ultrathin LED PCB is a specially designed printed circuit board built specifically for LED lighting applications. They lead the innovation path of the LED lighting industry with their excellent performance and innovative design. Ultrathin LED PCBs have significant advantages over traditional PCBs, making them the first choice for many LED lighting projects.
First of all, one of the most notable features of Ultrathin LED PCB is its ultra-thin and ultra-light design. This extreme thinness and lightweight make LED lighting equipment more compact and lightweight, making it suitable for various application scenarios with limited space. Whether it is indoor lighting or outdoor lighting, Ultrathin LED PCB can be perfectly integrated into the design, bringing users a more convenient and comfortable experience.
Secondly, Ultrathin LED PCB excels in thermal conductivity and electrical characteristics. LED lighting equipment generates a large amount of heat during operation, so good thermal conductivity is crucial to maintaining the stability and lifespan of LEDs. Ultrathin LED PCB uses high-performance thermally conductive materials and designs to effectively dissipate heat and maintain the stability and long-term reliability of the LED. At the same time, the excellent electrical characteristics also ensure the efficient operation of the LED lighting system, providing users with long-lasting and stable lighting effects.
In the continuous development and progress of the LED lighting industry, Ultrathin LED PCB is gradually becoming the standard configuration of the industry. Its innovative design and excellent performance make it popular in various LED lighting applications. From home lighting to commercial lighting, from automotive lighting to outdoor landscape lighting, Ultrathin LED PCB has demonstrated unparalleled advantages and potential. They not only improve the performance and quality of LED lighting products, but also bring users a better and more comfortable lighting environment.
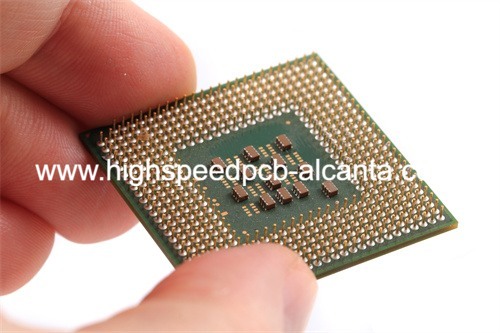
Ultrathin LED PCB Manufacturer
All in all, Ultrathin LED PCB is an important innovation in the LED lighting industry. Its ultra-thin and ultra-light design, excellent thermal conductivity and electrical characteristics make it the first choice for LED lighting projects. With the continuous advancement of technology and the continuous expansion of applications, Ultrathin LED PCB will continue to lead the innovation of the LED lighting industry and bring people more intelligent, efficient and environmentally friendly lighting solutions.
Ultrathin LED PCB design Reference Guide.
The design of Ultrathin LED PCB is a critical step in ensuring the performance and reliability of LED lighting systems. In this design reference guide, we will explore some key elements to help you design Ultrathin LED PCB effectively.
Determine LED layout
Before designing Ultrathin LED PCB, you must first determine the layout of the LEDs. This involves the number, arrangement, and positional relationship of LEDs to other components. Reasonable LED layout can ensure that the lighting system has uniform light distribution and good lighting effects.
Consider thermal design
Since LEDs generate heat when working, heat dissipation design is crucial. During the design process of Ultrathin LED PCB, the layout and material selection of the heat sink should be taken into consideration to effectively conduct heat away and ensure the stability and long life of the LED.
Choose the right material
In the design of Ultrathin LED PCB, choosing the right material is crucial. High-performance substrate materials, thermal conductive materials and cover layer materials can ensure that the PCB has good thermal conductivity, electrical properties and mechanical strength, thereby improving the performance and reliability of the LED lighting system.
Optimize circuit layout
When designing Ultrathin LED PCB, attention should be paid to optimizing circuit wiring and reducing signal interference and electromagnetic radiation. Reasonable wiring can reduce circuit losses and improve circuit efficiency and stability.
Consider environmental factors
Finally, when designing Ultrathin LED PCB, environmental factors such as temperature, humidity, and vibration should be taken into consideration. Appropriate protective measures and packaging design can ensure the reliability and stability of PCB in harsh environments.
By following the above guide, you can better design your Ultrathin LED PCB to meet the requirements of your LED lighting system and ensure its performance and reliability. Good luck with your design work!
What material is used in Ultrathin LED PCB?
The design and manufacturing of Ultrathin LED PCBs requires carefully selected materials to ensure excellent performance and reliability. In LED lighting systems, material selection is crucial because they directly affect the thermal conductivity, mechanical strength, and overall performance of the PCB. Here are some common high-performance materials used for Ultrathin LED PCBs:
FR-4
FR-4 is a common glass fiber reinforced epoxy resin-based material that is widely used in PCB manufacturing. It has excellent mechanical strength and heat resistance, can effectively support LED components and protect the circuit from the external environment.
Metal substrate
Metal substrate is another common Ultrathin LED PCB material choice. Aluminum substrate and copper substrate are two commonly used types of metal substrates. Aluminum substrate has good thermal conductivity and lightweight properties, and is suitable for LED lighting products that require good heat dissipation. The copper substrate has excellent electrical conductivity and mechanical strength, and is suitable for LED lighting systems with high electrical performance requirements.
Thermal conductive material
In addition to substrate materials, Ultrathin LED PCBs often use special thermal conductive materials to improve heat dissipation. These thermally conductive materials are usually filled in the interlayer gaps of the PCB to enhance the PCB’s ability to conduct heat. Common thermally conductive materials include aluminum oxide (Alumina), silicone (Silicone), polytetrafluoroethylene (PTFE), etc., which can effectively transfer the heat generated by the LED to the PCB surface and dissipate it to the surrounding environment through the heat sink.
The selection and application of these high-performance materials give Ultrathin LED PCB excellent thermal conductivity and mechanical strength, which can meet the stability, reliability and long-term operation requirements of LED lighting systems. Through reasonable material matching and process control, Ultrathin LED PCB manufacturers can provide customized solutions to meet customer needs in different application scenarios.
What size are Ultrathin LED PCB?
Ultrathin LED PCB plays a vital role in the modern LED lighting industry. However, compared to traditional PCBs, their size is critical. why? Because they usually need to be used with compact LED lighting equipment.
When we talk about LED lighting, we often think of lighting fixtures of all shapes and sizes such as bulbs, light strips, or light panels. As the core component of these devices, Ultrathin LED PCB must work closely with them to ensure the performance and reliability of the lighting system.
With this in mind, Ultrathin LED PCB manufacturers often offer customized solutions to meet customer needs. They can customize the size of the PCB according to the customer’s requirements to ensure that it perfectly fits the required application scenario.
For example, for scenarios where LED lighting equipment needs to be installed in a small space, a smaller size Ultrathin LED PCB may be required to ensure that it can be installed easily and work well with other components. For LED lighting systems that need to be used in large light boxes or displays, a larger PCB size may be required to support more LED chips and circuit layouts.
In addition to size customization, Ultrathin LED PCB manufacturers can also adjust the shape, thickness and other parameters of the PCB according to customer requirements to meet the needs of different application scenarios. This ability to customize makes Ultrathin LED PCB ideal for a variety of LED lighting projects.
In summary, size is critical for Ultrathin LED PCBs as they must fit closely with various LED lighting fixtures. Through customized solutions provided by manufacturers, the PCB can be ensured to perfectly adapt to the required application scenarios, thereby achieving high performance and reliability of the LED lighting system.
Hope this extension meets your needs! If you require further information or have any other questions, please feel free to let me know.
The Manufacturer Process of Ultrathin LED PCB.
When it comes to the manufacturing process of Ultrathin LED PCB, every step is crucial, from design to final testing, directly affecting the quality and performance of the PCB. Below is a detailed explanation of the manufacturing process:
Design
The design of Ultrathin LED PCB is the basis of the entire manufacturing process. During the design phase, engineers use CAD software to create the layout of the PCB and ensure that it meets the customer’s requirements and technical specifications. This includes determining the PCB size, number of layers, routing, electrical characteristics, and other key parameters.
Printing
After the design is complete, the PCB layout is converted into an actual printed circuit board. This is usually accomplished by printing the circuit pattern onto a substrate of fiberglass composite material (usually FR-4). This process involves printing a conductive layer (usually copper) onto the surface of a substrate to form the desired circuit pattern.
Plating
Once the conductive pattern is printed on the substrate, the next step is electroplating. In this step, manufacturers cover the conductive pattern with copper to increase the circuit’s conductive properties. Electroplating typically uses chemical methods to deposit copper onto a conductive pattern, creating a uniform layer of metal.
Drilling
After plating is completed, the PCB needs to be drilled. These holes are used to connect circuits between different layers, as well as to mount components. Manufacturers use high-precision drill bits to drill holes in PCBs to ensure precise hole location and size.
Assemble
After drilling is completed, the PCB enters the assembly stage. At this stage, electronic components (such as LEDs, resistors, capacitors, etc.) are mounted onto the PCB. This is typically accomplished via surface mount technology (SMT) or plug-in assembly, depending on the PCB design and application requirements.
Test
Finally, the assembled PCB needs to undergo rigorous testing. This includes electrical testing, connectivity testing, functional testing and possibly environmental testing (such as temperature and humidity testing). Only PCBs that pass all tests and meet industry standards and customer requirements will be considered qualified.
Throughout the manufacturing process, manufacturers use advanced production equipment and technology to ensure the quality and stability of PCBs. Strict quality control processes ensure that each PCB achieves expected performance levels to meet customer needs and remain competitive in the industry.
The Application area of Ultrathin LED PCB.
Ultrathin LED PCB, as an important electronic component, has a wide range of applications in the field of LED lighting. Its thinness and excellent performance make it the first choice for many LED lighting products. Below we will delve into the application of Ultrathin LED PCB in various fields:
Indoor lighting
Ultrathin LED PCB is widely used in indoor lighting systems in homes, businesses and offices. Their thin and light design allows them to be easily embedded into various lighting fixtures to provide even, bright lighting effects.
Outdoor lighting
In the field of outdoor lighting, Ultrathin LED PCB’s high performance and reliability enable it to cope with various harsh environmental conditions, such as moisture, high temperature and vibration. They are often used in street lights, billboards, landscape lighting and other projects to provide high-efficiency lighting solutions for cities and scenic spots.
Automotive lighting
In the automotive industry, Ultrathin LED PCBs’ thin, lightweight design and high-efficiency characteristics make them ideal for components such as car lights, dashboard backlights, and interior lighting. Not only do they provide high-quality lighting effects, they also help reduce the overall weight of the car and improve fuel efficiency.
Display
Ultrathin LED PCB is widely used in LED displays and electronic information display systems. Its high integration and stability ensure the high definition and long-term stability of the display, while its thin and light design also helps reduce the size and weight of the display.
Backlight module
As an important component of LED backlights, Ultrathin LED PCB plays a key role in products such as TVs, computer monitors, and tablets. Its uniform light distribution and high-efficiency characteristics enable the product to present a clearer and brighter picture.
In general, Ultrathin LED PCB has demonstrated its unique advantages and value in various fields of application. Its high performance, reliability and flexible design features have made it the first choice in many industries, driving the continuous development and innovation of LED lighting technology.
What are the advantages of Ultrathin LED PCB?
Ultrathin LED PCB (Printed Circuit Board), as an important part of the LED lighting industry, has many advantages, making it the first choice for many applications. Compared with traditional LED PCB, Ultrathin LED PCB has significant advantages in many aspects, these advantages include:
Lighter and thinner
The design of Ultrathin LED PCB focuses on thinness and lightness, allowing it to occupy less space in various LED lighting applications. Due to their thin structure, they can be easily integrated into a variety of compact LED devices, such as panel lights, light strips, and displays. This thin and lightweight design also helps reduce the weight of the entire device, improving portability and installation flexibility.
Higher thermal conductivity
Thermal conductivity is critical to LED lighting systems because the high temperature of the LED chip affects its performance and lifespan. Ultrathin LED PCB uses high-performance thermally conductive materials and designs that can effectively dissipate heat, reduce the operating temperature of the LED chip, extend its life and improve performance stability. This optimized thermal conductivity helps improve the reliability and efficiency of LED lighting systems.
Better electrical characteristics
Ultrathin LED PCB is not only superior in thermal conductivity, but also in electrical characteristics. They have the advantages of low resistance, low loss and high electrical stability, ensuring stable operation and high-efficiency output of LED lighting systems. This excellent electrical characteristic enables Ultrathin LED PCB to perform excellently in various application scenarios.
Higher integration
Due to its thin and light design and advanced manufacturing process, Ultrathin LED PCB is able to achieve a higher level of integration. This means that more functions and components can be integrated in a limited space, allowing for more complex LED lighting system designs. This high level of integration not only saves space and cost, but also improves system reliability and stability.
More flexible design options
Ultrathin LED PCB manufacturers usually provide customized design services to meet customers’ different needs and application scenarios. This flexible design option includes PCB size, number of layers, wiring method, surface treatment and impedance control, allowing customers to customize the PCB according to specific needs to achieve the best performance and effects.
Overall, Ultrathin LED PCB provides excellent performance and flexible design options through being lighter, thinner, higher thermal conductivity and better electrical characteristics, making it the preferred solution for the LED lighting industry. As LED technology continues to develop and market demand increases, Ultrathin LED PCB will continue to play an important role and push the LED lighting industry to a higher level.
FAQ
What are the design considerations for Ultrathin LED PCB?
When designing Ultrathin LED PCB, many factors need to be considered, including size, thermal conductivity, electrical characteristics, material selection, and layout of adapted LED components. Proper design can ensure the stability and performance of PCB.
What is the difference between Ultrathin LED PCB and traditional LED PCB?
Ultrathin LED PCB is thinner and lighter than traditional LED PCB, and has better thermal conductivity and electrical characteristics. They are often used in applications that have strict size and weight requirements, such as mobile phones, tablets, and automotive lighting.
How long is the production cycle of Ultrathin LED PCB?
Production lead time depends on the specific requirements of the project and the manufacturer’s capabilities. Typically, the production lead time can be anywhere from a few days to a few weeks from design to delivery. However, customized needs or special technical requirements may increase the production cycle.
What is the heat dissipation effect of Ultrathin LED PCB?
Ultrathin LED PCB is made of high thermal conductivity materials and usually has excellent heat dissipation effect. In addition, good design and layout can also improve the heat dissipation effect and ensure the stable operating temperature of LED components.