Ultrathin BGA Substrates Manufacturer.Ultrathin BGA Substrates Manufacturer specializes in producing cutting-edge, ultra-thin ball grid array (BGA) substrates used in advanced electronic devices. Our innovative technology ensures exceptional precision and reliability, catering to the high demands of modern semiconductor applications. We prioritize quality and performance, making us a trusted partner for leading electronics manufacturers worldwide.
In today’s era of rapid development of electronic technology, ultra-thin BGA substrates (Ball Grid Array Substrates) have become the core components of many innovative electronic devices. These thin yet powerful substrates not only provide compact connectivity solutions but also provide critical support for the performance and reliability of electronic devices. This article will delve into the importance of ultra-thin BGA substrates in modern electronic devices and their widespread use in various industries.
What are Ultrathin BGA Substrates?
Ultra-thin BGA substrate is a special form of printed circuit board (PCB) that has extremely thin thickness and high-density ball grid array (BGA) connection points compared with traditional PCB. These substrates use advanced manufacturing techniques that place the connection points for electronic components on the surface of the board, resulting in a more compact and efficient design. Compared with traditional wire connection methods, the use of ultra-thin BGA substrates can greatly improve the performance and reliability of electronic equipment.
First, the ultra-thin design of the ultra-thin BGA substrate enables electronic devices to integrate more functions in a smaller space. This compact design is especially important in smartphones, tablets, and other portable devices, which often have very limited internal space. By arranging component connection points on the surface of the substrate, the ultra-thin BGA substrate effectively reduces the thickness of the circuit board, providing the possibility for thin and light design of the device.
Secondly, the high-density BGA connection points of the ultra-thin BGA substrate make the wiring of electronic devices simpler and more efficient. Traditional PCB designs often use wires to connect components, which limits the density and layout of connection points. However, ultra-thin BGA substrates utilize tiny solder balls to connect components, allowing for higher density layouts and thus more complex circuit designs. This high-density connection method not only saves space, but also improves the speed and stability of signal transmission, further improving the performance of the device.
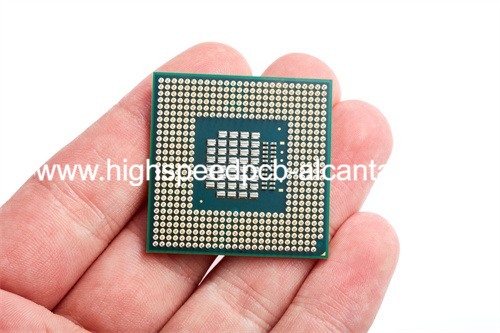
Ultrathin BGA Substrates Manufacturer
Most importantly, the design and manufacturing process of ultra-thin BGA substrates have undergone precise process control to ensure the quality and stability of the substrates. Using high-performance materials and advanced manufacturing techniques, these substrates offer excellent heat, impact and corrosion resistance, making them suitable for use in a variety of harsh working environments. Therefore, ultra-thin BGA substrate not only provides superior circuit connection solutions, but also guarantees the reliability and durability of electronic equipment.
To sum up, ultra-thin BGA substrate, as a key component in modern electronic equipment, provides important support for equipment performance improvement and design innovation. Its compact design, high density of connections and excellent stability make it one of the preferred solutions for many innovative products.
Ultrathin BGA Substrates design Reference Guide.
During the design process of ultra-thin BGA (Ball Grid Array) substrates, engineers need to comprehensively consider multiple key factors to ensure that the final design can meet performance requirements and improve production efficiency. Here are some design reference guides to help engineers optimize the design of ultra-thin BGA substrates:
Circuit layout
Good circuit layout is the key to designing ultra-thin BGA substrates. Engineers should ensure signal paths are as short as possible and reduce interference between signal lines. It is also critical to use ground and power planes to provide good ground and power distribution. By optimizing the layout, signal distortion can be reduced and the stability and performance of the circuit improved.
Thermal management
Ultra-thin BGA substrates often bear large thermal loads in high-performance electronic devices. Therefore, effective thermal management is an integral part of the design process. Engineers can ensure thermal dissipation from the substrate by including thermal management measures such as heat sinks, thermal pads, and thermal vias in the design. In addition, optimizing component layout to promote air flow and selecting appropriate materials to improve heat dissipation efficiency is also crucial.
Signal integrity
In ultra-thin BGA substrate designs, maintaining signal integrity is critical. Engineers should consider factors such as signal transmission speed, electromagnetic compatibility (EMC) and crosstalk to ensure stable signal transmission on the substrate. Adopting proper interlayer connection and ground design, as well as analysis using impedance matching and signal simulation tools, can help engineers optimize the design and reduce the occurrence of signal integrity problems.
Manufacturing feasibility
When designing ultra-thin BGA substrates, engineers should also consider manufacturing feasibility to ensure that the design can be smoothly transformed into actual production. Reasonable selection of materials and processes, avoiding overly complex layouts and special processing requirements, and working closely with manufacturers are key steps to ensure smooth design conversion.
By following the above design reference guide, engineers can better understand the key principles of ultra-thin BGA substrate design, optimize the design in practice, and improve production efficiency and product quality.
What material is used in Ultrathin BGA Substrates?
The material selection of ultra-thin BGA substrate is crucial because it directly affects the performance and stability of the substrate. Typically, ultra-thin BGA substrates use high-performance materials, the two most common of which are polyimide (PI) film and special glass fiber reinforced resin.
First, polyimide (PI) films are widely used in ultra-thin BGA substrates. Polyimide is a high-performance polymer material with excellent mechanical properties and chemical stability. Its characteristics include high strength, high modulus and excellent heat resistance, allowing it to remain stable in high-temperature environments. In addition, the polyimide film also has good chemical resistance and can resist the erosion of various chemical substances, thus protecting the stability and reliability of the circuit board. Therefore, polyimide film is one of the ideal choices for manufacturing ultra-thin BGA substrates.
Secondly, special glass fiber reinforced resin is also one of the commonly used materials for ultra-thin BGA substrates. This resin has fiberglass reinforcement, giving the substrate greater strength and stiffness. One of the reasons why special glass fiber reinforced resin is widely used in ultra-thin BGA substrates is its excellent heat resistance and chemical stability. It can withstand long-term operation in high-temperature environments and is not susceptible to corrosion by chemical substances, ensuring the long-term stability and reliability of the substrate.
In general, the high-performance materials used in ultra-thin BGA substrates, such as polyimide film and special glass fiber reinforced resin, not only have excellent mechanical properties, but also have excellent heat resistance and chemical resistance, and can adapt to various Harsh application environment. The selection of these materials provides a solid foundation for the manufacturing of ultra-thin BGA substrates, and also provides an important guarantee for the high performance and reliability of modern electronic equipment.
What size are Ultrathin BGA Substrates?
The size of ultra-thin BGA substrates plays a vital role in modern electronic devices. They are popular mainly because their compact design meets the stringent space requirements of modern electronic devices. As consumer demand for thin, light and portable devices continues to increase, the small size of ultra-thin BGA substrates has become the first choice of designers.
Small devices such as smartphones, tablets, and wearables often need to save as much space as possible to accommodate more functions and components while maintaining the thin and light appearance of the device. In these devices, the compact design of ultra-thin BGA substrates plays a vital role. Their extremely small size allows electronic devices to accommodate more functional components inside a smaller body, resulting in better performance and user experience.
Take smartphones for example, they are so small that every millimeter of space is extremely precious. The small size of the ultra-thin BGA substrate means that the circuit board can be laid out more compactly, saving space to accommodate important components such as batteries, processors, cameras, etc. This highly integrated design not only makes the phone thinner and lighter, but also improves the performance and efficiency of the device.
Tablets also benefit from the small size of ultra-thin BGA substrates. As a portable device, a tablet needs to have adequate performance and functionality while remaining lightweight and portable. The compact design of the ultra-thin BGA substrate allows the tablet to achieve higher performance and longer battery life while maintaining thinness, providing users with a more convenient mobile office and entertainment experience.
Wearable devices are another typical application scenario, and they need to be as small as possible so that they can be worn comfortably on the body. The small size of ultra-thin BGA substrates can make wearable devices lighter and more flexible without placing unnecessary burden on users. At the same time, the compact design can also provide better performance and longer battery life for wearable devices, thereby meeting the various needs of users in daily life.
In summary, the small size of ultra-thin BGA substrates plays an indispensable role in modern electronic devices. Their compact design allows electronic devices to achieve more functions and higher performance in a limited space, bringing users a more convenient and comfortable experience. As technology continues to advance and market demand continues to grow, ultra-thin BGA substrates will continue to play an important role and play an increasingly important role in future electronic devices.
The Manufacturer Process of Ultrathin BGA Substrates.
The manufacturing process of ultra-thin BGA substrate plays a vital role in modern electronic manufacturing. It needs to go through a series of precise process steps to ensure the quality and stability of the final product.
First, manufacturing ultra-thin BGA substrates requires thin film stacking. This step involves stacking thin film layers of different materials together to create a multilayer structure. These film layers usually include polyimide (PI) films and special glass fiber reinforced resins, which have excellent mechanical properties and heat resistance, providing good physical support for the substrate.
Next is micro-circuit manufacturing. Manufacturing fine circuits on ultra-thin BGA substrates requires the use of advanced photolithography and chemical etching processes. The circuit pattern is transferred to the substrate surface through photolithography, and then chemical etching is used to remove the unnecessary parts to form precise conductive paths. The manufacturing of these tiny lines requires extremely high precision and stability to ensure the reliability and stability of signal transmission.
The last step is precision machining. In this step, ultra-thin BGA substrates are precision cut and shaped to meet the needs of different sizes and shapes. The precision machining process requires highly precise equipment and process control to ensure the flatness and dimensional accuracy of the substrate.
The exquisite application of these manufacturing processes ensures the quality and stability of ultra-thin BGA substrates. They provide a reliable foundation for the manufacturing of high-performance electronic equipment and promote the development and innovation of the electronics industry. In the evolving technological environment, the process of manufacturing ultra-thin BGA substrates is also constantly innovating and improving to meet increasingly stringent application requirements.
The Application area of Ultrathin BGA Substrates.
Ultra-thin BGA substrates are not only widely used in consumer electronics, but also play an important role in communications, medical, aerospace and other fields. Their high level of integration and reliability makes them a key component of innovative products in various industries, driving industry development.
In the field of consumer electronics, ultra-thin BGA substrates have a wide range of applications. From smartphones and tablets to smart home devices and wearable technology, ultra-thin BGA substrates serve as core components of electronic devices, providing people with a more convenient and efficient lifestyle. Their compact design and high level of integration make consumer electronics products thinner, lighter and more powerful.
In the field of communications, ultra-thin BGA substrates play an important role in connection and data processing. Whether it is a mobile communication base station or a satellite communication system, ultra-thin BGA substrates can meet the needs of high-speed data transmission and complex signal processing, providing reliable support for the stable operation of communication networks.
In the medical field, ultra-thin BGA substrates are widely used in medical diagnostic equipment, health monitors, medical imaging systems and other equipment. Their high degree of integration and stability ensures the accuracy and reliability of the equipment, providing important support for the development of the healthcare industry and the treatment of patients.
In the aerospace field, ultra-thin BGA substrates play a key role in avionics, spacecraft control systems and navigation systems. They can work in extreme environments and are resistant to radiation and vibration, ensuring the safe operation of aerospace vehicles and the stability of data transmission.
In general, ultra-thin BGA substrate, as an advanced electronic connection technology, is not only widely used in the field of consumer electronics, but also plays an important role in communications, medical, aerospace and other fields. Their high degree of integration and reliability provide strong support for innovative products in various industries and promote the continuous development and progress of the industry.
What are the advantages of Ultrathin BGA Substrates?
The advantage of ultra-thin BGA substrates is the significant improvement they bring compared to traditional connection solutions. First, ultra-thin BGA substrates are known for their compact size. In today’s electronic devices, space is often a precious resource, so components that are as small as possible are required to achieve a higher level of functional integration. Through their thin design, ultra-thin BGA substrates can accommodate more connection points and circuit components in a limited space, making it possible to miniaturize and lighten equipment.
Secondly, the ultra-thin BGA substrate has the characteristics of high-density connections. Compared to traditional connection methods such as soldering or plugging, BGA connections provide more connection points and distribute them throughout the bottom of the substrate, resulting in denser and more reliable connections. This high-density connection not only improves the performance of the device, but also reduces the size of the circuit board, making the device more compact.
Another significant advantage is the excellent thermal management capabilities of the ultra-thin BGA substrate. Modern electronic devices often need to handle large amounts of heat, and the design of ultra-thin BGA substrates can effectively conduct and disperse heat to maintain stable performance of the device. By arranging heat-sensitive components and heat sinks on the substrate, the efficiency of thermal management can be further improved to ensure that the equipment can still maintain good working condition during high-load operation.
Finally, ultra-thin BGA substrates also offer excellent signal integrity. Because its design makes the signal path shorter and more compact, it can reduce interference and loss during signal transmission. This helps ensure stable performance and high-quality signal transmission of the device, thereby improving the overall performance and reliability of the device.
Overall, ultra-thin BGA substrates have become one of the preferred solutions for modern electronic devices due to their compact size, high-density connections, excellent thermal management and good signal integrity. Its advantages in all aspects provide a solid foundation for the performance, reliability and stability of the equipment, and promote the continuous innovation and development of electronic technology.
FAQ
What is the difference between ultra-thin BGA substrate and traditional PCB?
Ultra-thin BGA substrates have thinner thickness and higher density of ball grid array (BGA) connection points than traditional printed circuit boards (PCBs). Traditional PCBs usually use thicker substrates and ordinary connection methods, while ultra-thin BGA substrates use more advanced materials and processes, making them more compact in size and higher in integration.
How to deal with thermal management of ultra-thin BGA substrate?
Ultra-thin BGA substrates are often designed with good thermal management in mind. By selecting appropriate materials and designing the heat dissipation structure, heat can be effectively conducted from key components to the radiator or enclosure, maintaining the stability and reliability of the device.
What special environments are ultra-thin BGA substrates suitable for?
Due to its excellent mechanical properties and heat resistance, ultra-thin BGA substrates are suitable for applications in various special environments, including high temperature, high humidity, high vibration and corrosive environments. Therefore, they are often used in fields such as automotive electronics, aerospace, and industrial control.
What should we pay attention to when maintaining ultra-thin BGA substrates?
The maintenance of ultra-thin BGA substrates is relatively simple, mainly including regular cleaning and checking whether the connections are tight. Avoid using too many chemical cleaners during maintenance to avoid damaging the substrate surface or causing short circuits.