Ultrathin BGA Package Substrates Manufacturer.The Ultrathin BGA Package Substrates Manufacturer specializes in crafting cutting-edge substrates for Ball Grid Array (BGA) packaging solutions. With precision engineering and advanced materials, they fabricate ultra-thin substrates that optimize space utilization while ensuring robust performance. Their expertise lies in creating substrates that meet stringent industry standards, catering to the demands of high-density electronic applications. Utilizing state-of-the-art manufacturing processes, they deliver reliable solutions for a diverse range of electronic devices, enabling sleeker designs and enhanced functionality in modern technology.
Ultrathin BGA (Ball Grid Array) packaging substrate is a vital part of today’s electronic equipment. Its special design and manufacturing process make it an important representative of modern electronic technology. This article will comprehensively discuss the characteristics, manufacturing process and wide range of application fields of Ultrathin BGA packaging substrates, aiming to provide readers with a deeper understanding and application guidance to help them better apply this key technology in practice.
What are Ultrathin BGA Package Substrates?
Ultrathin BGA packaging substrate is a specially designed packaging form that uses a ball grid array (BGA) connector and is characterized by its extremely thin thickness. Compared with traditional packaging substrates, the thickness of Ultrathin BGA packaging substrates is significantly reduced, usually between tens of microns and hundreds of microns, which enables higher component integration and smaller package size.
Traditional BGA packaging substrates usually use rigid substrates, while Ultrathin BGA packaging substrates are more often made of flexible substrates or special materials to achieve their extremely thin characteristics. This extremely thin design makes Ultrathin BGA packaging substrates have broad application prospects in various fields.
First of all, Ultrathin BGA packaging substrates are of great significance in the field of mobile devices. With the rapid development of mobile devices such as smartphones and tablets, the requirements for the size and weight of packaging substrates are getting higher and higher. The thickness of the Ultrathin BGA packaging substrate is extremely thin, which can help achieve thinner and lighter designs of devices and improve user experience.
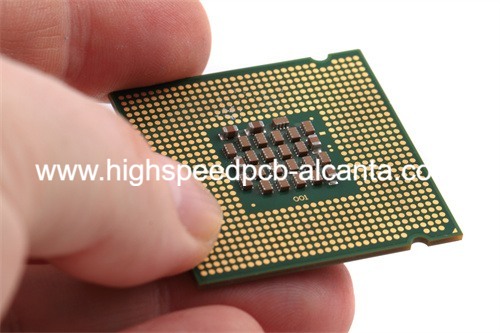
Ultrathin BGA Package Substrates Manufacturer
Secondly, consumer electronics are also important application areas for Ultrathin BGA packaging substrates. Nowadays, people have higher and higher requirements for the appearance design and portability of electronic products, and the small size and lightweight characteristics of Ultrathin BGA packaging substrates make it an ideal choice for digital cameras, portable game consoles and other products.
In addition, the medical equipment field is also an important market for Ultrathin BGA packaging substrates. Medical equipment usually needs to be miniaturized, lightweight and highly reliable, and Ultrathin BGA packaging substrates can meet these requirements and facilitate the design and manufacturing of medical equipment.
Finally, the industrial control field is also a widespread application scenario for Ultrathin BGA packaging substrates. Industrial control equipment has high requirements for the stability and reliability of packaging substrates, and Ultrathin BGA packaging substrates can meet the various needs of industrial control equipment through advanced manufacturing processes and material selection.
In general, Ultrathin BGA packaging substrate, with its extremely thin thickness, small size and lightweight characteristics, provides new solutions for the design and manufacturing of various electronic devices, and promotes the continuous development and innovation of electronic technology. With the continuous advancement of technology, Ultrathin BGA packaging substrates will continue to play an important role in various fields, bringing more convenience and possibilities to people’s lives and work.
Ultrathin BGA Package Substrates design Reference Guide.
Ultrathin BGA (Ball Grid Array) packaging substrate design is a complex and critical process, which directly affects the performance and reliability of electronic products. This guide will introduce you to key considerations and best practices in Ultrathin BGA package substrate design to help you develop a high-quality design.
Thickness and size
Ultrathin BGA package substrate thickness and size are important considerations in the design process. The thin design of the packaging substrate can achieve lightweight and compact electronic products, but on the premise of ensuring sufficient mechanical strength and heat dissipation performance, the choice of thickness and size needs to be balanced.
Material selection
Selecting the appropriate substrate material is critical to the performance of Ultrathin BGA package substrates. Commonly used materials include polyimide (PI) and flexible substrate materials, which have good electrical properties and flexibility and are suitable for thin package designs.
Conductor layout
In Ultrathin BGA package substrate design, reasonable conductor layout can achieve compact layout and high-density connections of the circuit, ensuring signal integrity and power integrity. Pay attention to avoid interference and crossover between conductors and optimize the signal transmission path.
Thermal management
Due to the thin design of the Ultrathin BGA package substrate, thermal management is a special concern during the design process. Design measures such as heat dissipation holes and heat dissipation layers are adopted to effectively improve heat dissipation efficiency and ensure the stability and reliability of electronic components during work.
Packaging process
Selecting the appropriate packaging process is critical to the manufacturing quality and performance of Ultrathin BGA packaging substrates. Ensure that the packaging process can meet the thickness and size requirements, and use advanced micro-assembly technology and patch technology to ensure the reliability and stability of the packaging connection.
Design verification and simulation
After the Ultrathin BGA package substrate design is completed, design verification and simulation are important steps to ensure the reliability of the design solution. Use tools such as Electrical Rule Checking (ERC), Design Rule Checking (DRC), and Signal Integrity Simulation to verify whether the design meets requirements and make necessary adjustments and optimizations.
In summary, Ultrathin BGA packaging substrate design is a complex and critical process that requires comprehensive consideration of thickness and size, material selection, conductor layout, thermal management, packaging process and other factors. Through reasonable design and strict verification, high-quality Ultrathin BGA packaging substrates can be achieved, providing strong support for the performance and reliability of electronic products.
What material is used in Ultrathin BGA Package Substrates?
Ultrathin BGA packaging substrate plays an important role in electronic devices, and its material selection is crucial, directly affecting the performance and reliability of the packaging substrate. Materials commonly used for Ultrathin BGA packaging substrates mainly include polyimide (PI) and flexible substrate materials.
Polyimide (PI) is a high-performance engineering plastic with excellent high temperature resistance, corrosion resistance and chemical resistance, so it is widely used in the manufacture of Ultrathin BGA packaging substrates. Its low dielectric constant and low dielectric loss characteristics enable it to have excellent signal transmission performance in high-frequency circuits. In addition, polyimide (PI) also has good flexibility and mechanical strength, which can meet the thinness and flexibility requirements of Ultrathin BGA packaging substrates while ensuring its reliability and stability.
In addition to polyimide (PI), flexible substrate materials are also one of the important choices for Ultrathin BGA packaging substrates. Flexible substrate materials are usually composed of polyester film, polyimide film, etc., which have excellent flexibility and bendability and can achieve a higher degree of curved surface packaging and space utilization. Flexible substrate materials perform well in coping with multi-axis bending and high-frequency signal transmission, and are suitable for application scenarios that have strict requirements on the thickness and weight of packaging substrates, such as portable devices, smart wearable devices, etc.
In general, polyimide (PI) and flexible substrate materials are commonly used materials in Ultrathin BGA packaging substrate manufacturing. They have good high-temperature performance, chemical stability and flexibility, and can meet the packaging substrate’s requirements for thickness, weight and The requirements for signal transmission performance provide reliable support for the miniaturization, lightweight and high performance of electronic equipment.
What size are Ultrathin BGA Package Substrates?
Ultrathin BGA package substrate size generally depends on application requirements and design needs. Due to its special thin design, Ultrathin BGA packaging substrate has a smaller size and lighter weight than traditional packaging substrates, making it suitable for applications that have strict requirements on packaging size.
Generally speaking, Ultrathin BGA package substrates can range in size from a few millimeters to tens of millimeters, depending on the size, layout and connection needs of the chip and other components. In compact products such as mobile devices, the common Ultrathin BGA package substrate size is generally between 5mm x 5mm and 20mm x 20mm to meet product miniaturization and lightweight design requirements.
At the same time, Ultrathin BGA packaging substrates can also be customized in size and design according to the needs of specific applications to achieve better adaptation and integration. For example, for medical devices or portable consumer electronics, smaller, thinner packaging substrates may be required to meet the strict volume and weight requirements of the product.
In addition to size, the thickness of the Ultrathin BGA package substrate is an important consideration. Typically, the thickness of Ultrathin BGA packaging substrates can range from tens to hundreds of microns, depending on the substrate material and manufacturing process used. Thinner substrates enable smaller designs, but factors such as the mechanical strength and thermal management of the substrate also need to be taken into consideration.
In general, Ultrathin BGA packaging substrate has flexible size design and customization capabilities, which can be adjusted and optimized according to the needs of specific applications, providing more possibilities for product design and manufacturing. As technology advances and market demands continue to change, the size and characteristics of Ultrathin BGA packaging substrates will continue to innovate and develop, promoting the advancement and intelligence of electronic products.
The Manufacturer Process of Ultrathin BGA Package Substrates.
The manufacturing process of Ultrathin BGA packaging substrate is a complex and precise project that requires multiple process steps to ensure the quality and performance of the final product. The following are the key steps of the manufacturing process:
Substrate material selection
The first step in manufacturing Ultrathin BGA package substrates is selecting the appropriate substrate material. High-performance, thin substrate materials are usually used, such as polyimide (PI) or flexible substrate materials. These materials have excellent thermal stability and mechanical strength, ensuring the thinness and flexibility of packaging substrates while meeting the requirements of high-density circuit designs.
Conductor layer preparation
After selecting the appropriate substrate material, the next step is to prepare the conductor layer on the substrate. Conductor layers are usually prepared using thin film deposition or thin film patching processes to achieve high-density, high-reliability electrical connections. The preparation of the conductor layer requires strict control of process parameters to ensure uniform thickness and stable quality of the conductor layer to improve the reliability and stability of the connection.
BGA connector preparation
The BGA connector is a key component of the Ultrathin BGA package substrate, and its accuracy and reliability directly affect the performance and quality of the entire package substrate. When preparing BGA connectors, precise processing equipment and process technology are required to ensure that the ball grid arrangement of the connector is accurate to ensure the stability and reliability of the connection.
Packaging process
The packaging process is the core link in Ultrathin BGA packaging substrate manufacturing, and its quality and accuracy directly affect the performance and reliability of the final product. Using advanced thin packaging technology and micro assembly technology, chips and other components are precisely packaged on the substrate and connected to the BGA connector. The packaging process requires precision equipment and strict process control to ensure packaging accuracy and stability.
Testing and Quality Control
After the Ultrathin BGA package substrate is manufactured, rigorous electrical testing and quality control are required. Ensure compliance with design requirements and manufacturing standards by conducting electrical testing and visual inspection of each package substrate. At the same time, reliability testing and environmental adaptability testing are also required to verify the performance and stability of the product under different environmental conditions.
To sum up, the manufacturing process of Ultrathin BGA packaging substrate involves multiple key steps and complex processes, which requires precision equipment and strict process control to ensure that the quality and performance of the final product meet the design requirements. With the continuous development and innovation of electronic technology, Ultrathin BGA packaging substrate will show broader application prospects and development space in various fields.
The Application area of Ultrathin BGA Package Substrates.
As a key electronic component, Ultrathin BGA (Ball Grid Array) packaging substrate is widely used in many fields. Its small size, high performance and reliability make it ideal for a variety of electronic products. The following are the applications of Ultrathin BGA packaging substrates in different fields:
Mobile device
In the field of mobile devices, such as smartphones, tablets, etc., Ultrathin BGA packaging substrates play a key role. Since these devices have stringent size and weight requirements, the miniaturized nature of Ultrathin BGA packaging substrates makes them an ideal packaging solution. At the same time, its high performance and reliability ensure the stable operation of the equipment in complex application scenarios.
Consumer Electronics
Consumer electronics products such as digital cameras and portable game consoles also widely use Ultrathin BGA packaging substrates. These products usually require compact design and high performance requirements. The miniaturization and high integration characteristics of Ultrathin BGA packaging substrates can meet these needs while ensuring product stability and reliability.
Medical equipment
In the field of medical equipment, such as medical monitoring equipment, portable medical instruments, etc., the requirements for packaging substrates are more stringent. Ultrathin BGA packaging substrates are ideal for packaging medical devices due to their high reliability and miniaturization. Its stable electrical performance and mechanical strength ensure the safe operation of the device in the medical environment.
Industrial control
In the field of industrial control, such as industrial automation equipment, instrumentation, etc., the requirements for packaging substrates mainly focus on high-density, high-performance electrical connections and control functions. Ultrathin BGA packaging substrate, with its high integration and reliability, can meet the complex requirements of industrial control equipment for packaging substrates and improve the performance and reliability of the equipment.
In summary, Ultrathin BGA packaging substrates have broad application prospects in mobile devices, consumer electronics, medical equipment, industrial control and other fields. As electronic technology continues to develop and innovate, Ultrathin BGA packaging substrates will continue to play an important role in promoting technological progress and product innovation in various fields.
What are the advantages of Ultrathin BGA Package Substrates?
Ultrathin BGA (Ball Grid Array) packaging substrate is a technology that has attracted much attention in today’s electronics industry. It brings many advantages and helps product design and manufacturing reach new heights. The following are the advantages of Ultrathin BGA packaging substrate:
Miniaturization
Ultrathin BGA packaging substrates are thinner than traditional packaging substrates, which allows products to be smaller and lighter in size. Especially in the field of mobile devices and portable electronic products, miniaturized design can greatly improve the portability and comfort of the product.
High integration
Using high-density circuit design and advanced packaging technology, Ultrathin BGA packaging substrates can accommodate more components and implement more functions in limited space. This not only improves the performance of the product, but also reduces the power consumption of the overall system, providing users with a more superior experience.
High reliability
Ultrathin BGA packaging substrate uses high-quality materials and adopts advanced manufacturing processes to ensure its excellent electrical performance and mechanical strength. This means that the product can maintain stable working conditions in various extreme environments, thereby improving product reliability and stability and reducing the frequency of repairs and replacements.
Flexibility
Due to its thin, flexible nature, Ultrathin BGA packaging substrates offer excellent flexibility and adaptability. This enables them to adapt to different application scenarios and complex working environments, bringing greater flexibility and creativity to product design.
Cost-effectiveness
By optimizing the design and manufacturing process, the manufacturing cost of Ultrathin BGA packaging substrates can be effectively controlled, thereby improving the product’s competitiveness and market share. This results in higher profit margins for manufacturers and more affordable product options for consumers.
To sum up, Ultrathin BGA packaging substrate has become an important part of today’s electronic product design and manufacturing due to its advantages of miniaturization, high integration, high reliability, flexibility and cost-effectiveness, driving the continuous advancement of electronic technology. Innovation and development.
FAQ
What is the difference between Ultrathin BGA packaging substrate and traditional packaging substrate?
Compared with traditional packaging substrates, the biggest difference between Ultrathin BGA packaging substrates is that they are thinner and smaller in size, allowing for higher component integration and more compact product designs. Traditional packaging substrates are usually thicker and suitable for products with general performance requirements, while Ultrathin BGA packaging substrates are suitable for high-performance products that have strict requirements on package size and weight.
What is the thickness range for Ultrathin BGA package substrates?
Ultrathin BGA packaging substrate thickness typically ranges from tens to hundreds of microns, depending on application requirements and manufacturing processes. Generally speaking, its thickness is much smaller than that of traditional packaging substrates, allowing higher miniaturization and integration.
What applications are Ultrathin BGA packaging substrates suitable for?
Ultrathin BGA packaging substrates are suitable for a variety of applications, including mobile devices, consumer electronics, medical equipment, industrial controls, and more. Its miniaturization, lightweight and high-performance characteristics make it have broad application prospects in high-end electronic products.
How to choose a suitable Ultrathin BGA package substrate material?
Selecting the appropriate Ultrathin BGA package substrate material requires consideration of electrical performance, thermal performance, mechanical strength and cost. Common materials include polyimide (PI) and flexible substrate materials, selected based on specific application needs.
What is the manufacturing lead time for Ultrathin BGA packaging substrates?
The manufacturing lead time for Ultrathin BGA package substrates typically ranges from days to weeks depending on complexity and volume. The manufacturing cycle includes multiple stages such as design verification, process debugging, and mass production, and time and cost factors need to be fully considered.