Ultra-thin RF/Microwave PCB Manufacturer.As an ultra-thin RF/microwave PCB manufacturer, we specialize in producing high-performance, precision-engineered printed circuit boards for radio frequency and microwave applications. Our advanced manufacturing techniques ensure minimal signal loss, superior thermal management, and compact designs, catering to industries like telecommunications, aerospace, and defense. We prioritize quality and innovation to meet the rigorous demands of cutting-edge technology sectors.
Ultra-thin RF/Microwave PCBs are specialized printed circuit boards designed to operate at radio frequencies (RF) and microwave frequencies, typically ranging from 3 kHz to 300 GHz. These PCBs are crucial in a variety of applications, including telecommunications, radar systems, satellite communications, and wireless networks. The ultra-thin profile of these PCBs offers significant advantages in terms of weight, size, and performance, making them ideal for modern high-frequency electronic devices.
What is an Ultra-thin RF/Microwave PCB?
An ultra-thin RF/Microwave PCB is a printed circuit board with a significantly reduced thickness, designed to handle high-frequency signals efficiently. These PCBs use advanced materials and fabrication techniques to ensure minimal signal loss, excellent thermal management, and high reliability.
Thin Profile:Typically less than 0.5 mm thick, allowing for compact and lightweight designs.
High-Frequency Performance:Capable of operating efficiently at RF and microwave frequencies.
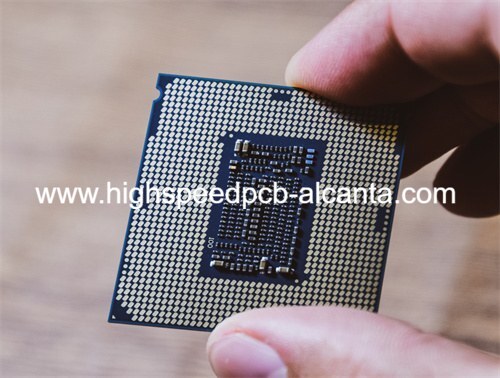
Ultra-thin RF/Microwave PCB Manufacturer
Advanced Materials:Use of low-loss, high-performance materials to ensure signal integrity.
Precision Engineering: Meticulous design and manufacturing processes to meet stringent performance standards.
Design Reference Guide for Ultra-thin RF/Microwave PCBs
Designing ultra-thin RF/Microwave PCBs requires careful consideration of various factors to ensure optimal performance and reliability.
Dielectric Materials:Low-loss materials such as PTFE (Polytetrafluoroethylene), Rogers laminates, or ceramic-filled substrates are preferred for their excellent electrical properties.
Conductive Materials:High-conductivity metals like copper or silver are used for the conductive layers to minimize signal loss.
Core Layer: The central dielectric layer provides structural stability while being extremely thin.
Signal Layers:Ultra-thin layers with precise trace widths and spacings to maintain consistent impedance.
Ground and Power Planes: Essential for minimizing noise and maintaining signal integrity.
Heat Dissipation: Incorporation of materials and design elements that efficiently dissipate heat generated by high-frequency operations.
Thermal Vias: Use of vias to conduct heat away from critical components.
Controlled Impedance:Careful design of trace widths and spacings to maintain consistent impedance and reduce signal reflections.
Isolation Techniques:Shielding and isolation structures to prevent crosstalk and electromagnetic interference (EMI).
Board Thickness:Ultra-thin profile to meet application-specific requirements.
Drilling and Plating:Precise drilling for vias and microvias, with appropriate plating for durability and performance.
Component Placement:Strategic placement of RF components to optimize performance and ease of testing.
What Materials are Used in Ultra-thin RF/Microwave PCBs?
The materials used in ultra-thin RF/Microwave PCBs are selected for their ability to handle high-frequency signals with minimal loss and interference, while also maintaining the thin profile of the board.
PTFE (Polytetrafluoroethylene): Known for its excellent electrical properties and low dielectric constant.
Rogers Laminates:High-performance materials specifically designed for RF and microwave applications.
Ceramic-Filled Substrates: Provide superior thermal stability and low dielectric loss.
Copper:Widely used for its high electrical conductivity and ease of processing.
Silver:Employed in certain applications where superior conductivity is required.
Gold:Often used for plating contacts and cavities due to its excellent conductivity and resistance to oxidation.
Nickel:Sometimes used as a barrier layer beneath gold plating.
What Size are Ultra-thin RF/Microwave PCBs?
The size of ultra-thin RF/Microwave PCBs can vary significantly based on the application and the specific design requirements. Factors influencing the size include:
Higher frequencies typically require more precise and smaller features, impacting the overall size of the PCB.
The number and type of RF components placed on the board will determine the required size.
Different applications, such as mobile devices, satellite systems, or radar equipment, have unique size constraints and performance requirements.
The limitations of the manufacturing process can also influence the size and complexity of ultra-thin RF/Microwave PCBs.
The Manufacturing Process of Ultra-thin RF/Microwave PCBs
The manufacturing process of ultra-thin RF/Microwave PCBs involves several precise and controlled steps to ensure they meet the specific requirements of high-frequency applications.
CAD Design: Detailed CAD models are created, incorporating all layers, traces, and components.
Simulation: Electromagnetic simulations are conducted to optimize the design for signal integrity and performance.
Lamination: Multiple layers of dielectric and conductive materials are laminated together to form the ultra-thin substrate.
Drilling and Plating:Vias and microvias are precisely drilled and plated to establish electrical connections and enhance performance.
Photo-Etching: The circuit pattern is transferred onto the substrate using photo-etching techniques.
Plating:Conductive traces and cavities are plated with materials like copper or gold to enhance performance.
Surface Mount Technology (SMT):RF components are mounted onto the PCB using automated SMT equipment.
Reflow Soldering: The board undergoes reflow soldering to solidify connections.
Electrical Testing:Rigorous tests are conducted to ensure all connections are intact and the PCB functions as intended.
Thermal Testing:Thermal tests verify the PCB’s ability to dissipate heat and maintain performance.
Final Inspection:A thorough inspection ensures the PCB meets all design specifications and quality standards.
The Application Area of Ultra-thin RF/Microwave PCBs
Ultra-thin RF/Microwave PCBs are used in a variety of high-frequency applications where performance and reliability are crucial:
Telecommunications:Used in mobile phones, base stations, and other communication devices for signal transmission and reception.
Radar Systems:Essential for radar applications in aviation, military, and weather monitoring systems.
Satellite Communications:Used in satellite transceivers and receivers to handle high-frequency signals.
Wireless Networks:Employed in Wi-Fi routers, Bluetooth devices, and other wireless communication systems.
Medical Devices:Used in diagnostic and therapeutic devices that rely on RF technology for operation.
What are the Advantages of Ultra-thin RF/Microwave PCBs?
Ultra-thin RF/Microwave PCBs offer several advantages that make them suitable for high-frequency applications:
Improved Signal Integrity: The thin profile and advanced materials ensure superior signal integrity and minimal loss.
Enhanced Thermal Management:Advanced materials and design techniques help dissipate heat effectively, maintaining device performance.
Compact and Lightweight Design:The ultra-thin profile saves space and reduces weight, making these PCBs ideal for portable and compact devices.
Durability and Reliability: High-quality materials and rigorous manufacturing processes ensure that these PCBs are durable and reliable, even under demanding conditions.
Customizability: The ability to create custom designs allows for tailored solutions that meet specific application requirements.
FAQ
What are the main benefits of using ultra-thin RF/Microwave PCBs in high-frequency applications?
Ultra-thin RF/Microwave PCBs provide improved signal integrity, enhanced thermal management, compact and lightweight design, durability, reliability, and customizability, making them ideal for high-frequency applications.
How are ultra-thin RF/Microwave PCBs manufactured?
These PCBs are manufactured through processes such as CAD design, electromagnetic simulation, material lamination, precise drilling and plating, photo-etching, and surface mount technology. Rigorous testing ensures their performance and reliability.
What materials are commonly used in ultra-thin RF/Microwave PCBs?
Common materials include PTFE, Rogers laminates, ceramic-filled substrates for dielectric layers, and copper or silver for conductive layers. Gold and nickel are often used for plating.
In which industries are ultra-thin RF/Microwave PCBs most commonly used?
These PCBs are commonly used in telecommunications, radar systems, satellite communications, wireless networks, and medical devices.
How do ultra-thin RF/Microwave PCBs improve signal integrity?
These PCBs improve signal integrity through the use of advanced materials, precise trace designs, controlled impedance, and effective thermal management.