What is ultra-thin rigid PCB?
Ultra-Thin Hard PCB Manufacturer.An “Ultra-Thin Hard PCB Manufacturer” specializes in crafting printed circuit boards (PCBs) that are exceptionally slim yet robust. These cutting-edge PCBs are engineered with precision, utilizing advanced materials and manufacturing techniques to achieve unparalleled thinness without compromising durability or functionality. The company’s expertise lies in creating ultra-thin PCBs tailored to specific applications where space constraints are critical, such as wearable devices, medical implants, or aerospace components. With a focus on innovation and quality, they lead the industry in delivering solutions that push the boundaries of what’s possible in electronic design and manufacturing.
Ultra-thin rigid PCB, a type of printed circuit board (PCB), is becoming a popular choice in the design of modern electronic devices. Known for its exceptional thinness and excellent durability, this PCB facilitates the streamlined design of modern electronic devices. So, what is ultra-thin rigid PCB?
Ultra-thin rigid PCB refers to printed circuit boards that offer exceptional thinness without compromising on durability and stiffness. These PCBs are precision engineered to meet the space constraints and performance expectations of modern electronic devices. Ultra-thin rigid PCBs typically have smaller thicknesses than traditional PCBs, ranging from 0.2mm to 0.8mm, making them ideal for compact and lightweight electronic devices.
The manufacturing of ultra-thin rigid PCBs involves advanced processes and materials. Typically, they use high-quality substrate materials such as FR-4 fiberglass epoxy to ensure electrical insulation and mechanical strength. During the manufacturing process, special processing techniques and equipment are used to control the thickness of the copper foil and substrate to ensure the uniformity and stability of the PCB.
Ultra-thin rigid PCBs are widely used in modern electronic equipment. For example, smartphones, tablets, wearables, and other portable devices often require ultra-thin rigid PCBs to achieve thinner and lighter designs. In the fields of automotive electronics, medical equipment and aerospace, ultra-thin rigid PCBs are also favored for their high performance and reliability.
Overall, ultra-thin rigid PCBs are a vital component in the design of modern electronic devices. They pave the way for the development and manufacturing of innovative products by providing superior thinness and durability.
How to design ultra-thin rigid PCB?
When designing ultra-thin rigid PCBs, engineers need to invest a lot of professional knowledge and skills to ensure that the final product meets performance and reliability requirements. Here are the key steps and considerations for designing ultra-thin rigid PCBs:
Circuit Layout: The first step in the design process is laying out the circuit components and connection paths on the PCB. Engineers use professional PCB design software, such as Altium Designer, Cadence Allegro, etc., to lay out the circuit in a compact and effective space. During the layout process, it is necessary to consider the distance between circuit components, optimization of wiring paths, and the best path for signal transmission.
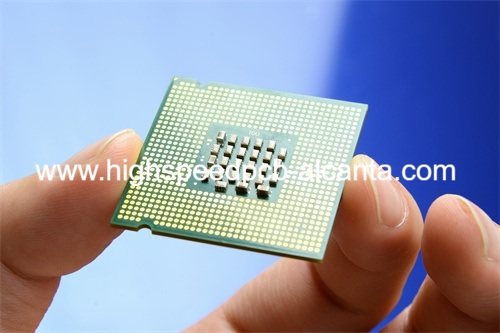
Ultra-thin hard PCB Manufacturer
Signal Integrity: Maintaining signal integrity is one of the keys to designing ultra-thin rigid PCBs. Engineers need to avoid problems such as signal interference, crosstalk and reflection to ensure stable signal transmission on the PCB. The use of technologies such as differential signaling, ground line planning, and signal layer separation can effectively improve signal integrity.
Thermal management: Due to the small size and high integration of ultra-thin rigid PCBs, thermal management has become an important consideration in the design process. Engineers need to reasonably design heat dissipation structures, such as heat dissipation holes, heat sinks, etc., to ensure that the heat on the PCB can be effectively dispersed and discharged to avoid the impact of overheating on electronic components.
Optimize space utilization: Ultra-thin rigid PCBs are often used in space-constrained applications, so optimizing space utilization is crucial. Engineers need to accurately calculate and plan circuit layouts to minimize the size and weight of PCBs while ensuring reasonable layout and connections between various electronic components.
Separation of analog and digital signals: Analog signals and digital signals often exist on ultra-thin rigid PCBs. Engineers need to design a suitable circuit structure to ensure good isolation between the two and avoid mutual interference.
Simulation and verification: After completing the preliminary design, engineers need to conduct simulation and verification to ensure that the design meets performance and reliability requirements. Through simulation analysis of circuits through simulation software, potential problems can be discovered and solved in advance, reducing the cost and time of later modification and debugging.
Special processing: Due to the particularity of ultra-thin hard PCB, some special processing may be required, such as thin plate processing, etching technology, etc. Engineers need to select the appropriate process and work closely with manufacturers to ensure the quality and stability of the final product.
To sum up, designing ultra-thin rigid PCB is a complex and precise task that requires engineers to have rich experience and expertise. Meticulous design and rigorous verification ensure that the final product reaches the expected performance and reliability levels.
What is the manufacturing process of ultra-thin rigid PCB?
The manufacturing process of ultra-thin rigid PCB is a precise and complex process involving multiple key steps, each of which is crucial. Let’s take a closer look at this process.
First of all, the first step in manufacturing ultra-thin rigid PCB is to prepare the substrate material. Glass fiber reinforced epoxy resin is usually used as the substrate material. This material has excellent electrical insulation and mechanical strength, making it ideal for use in PCB manufacturing.
Next, copper foil is layered onto the substrate. Copper foil is the main material of the conductive layer, and its good electrical conductivity and mechanical properties make it an ideal choice for manufacturing PCBs. The thickness of the copper foil can be adjusted as needed to meet the requirements of a specific application.
Subsequently, the circuit pattern is etched. This step uses chemical etching or mechanical etching to gradually remove unnecessary parts of the copper foil, leaving the required circuit pattern. This step requires a high degree of precision and accuracy to ensure that the functionality and performance of the circuit are not affected.
In some cases, advanced technology such as laser drilling may also be used. Laser drilling enables higher precision and finer hole diameters to meet the needs of some special applications. This technology is often used to manufacture ultra-thin PCBs to achieve the required thickness and precision.
The entire manufacturing process requires strict quality control and precision operations to ensure that the quality and performance of the final product are up to standard. Each step requires careful planning and execution, and any slight error may lead to unstable product quality or substandard performance.
To sum up, manufacturing ultra-thin rigid PCB is a precise and complex process involving multiple key steps and the use of advanced technology. Through careful design and strict execution, high-quality, high-performance ultra-thin rigid PCBs can be produced, providing strong support for the development of modern electronic equipment.
How to make ultra-thin rigid PCB?
Manufacturing ultra-thin rigid PCBs is a complex process that requires a high degree of expertise and support from advanced equipment. At every manufacturing stage, precision operations and strict quality control are key to ensuring final product performance and durability.
First, the process of manufacturing ultra-thin rigid PCB begins with material selection. High-quality substrate materials are the basis for ensuring PCB stability and reliability. Generally, fiberglass reinforced epoxy (FR-4) is a commonly used substrate material with excellent electrical insulation and mechanical strength. As a material for the conductive layer, copper foil must have good conductivity and corrosion resistance.
Next, the copper foil is laminated layer by layer on the substrate through special mechanical equipment, and pressure and heat are used to ensure that the copper foil and the substrate are firmly bonded. During this process, the thickness of the copper foil and substrate must be precisely controlled to ensure that the overall thickness of the PCB meets the design requirements and maintains uniformity to avoid any defects that may affect performance.
Subsequently, using advanced etching technology, the unnecessary parts of the copper foil are etched away layer by layer through chemical solutions to form the required circuit pattern. Precision and accuracy in this step are critical, as any errors may result in failed circuit connections or degraded performance.
Strict quality control measures are integral throughout the entire manufacturing process. Every step of the operation must follow standardized procedures and be verified through reliable detection and testing methods. Any defects discovered must be corrected promptly to ensure the quality of the final product is of the highest standard.
Overall, manufacturing ultra-thin rigid PCBs requires a combination of expertise, advanced equipment, and strict quality control measures. Only when these aspects reach the highest level can ultra-thin rigid PCB products with stable performance, durability and reliability be produced.
How Much Does a Ultra Thin Rigid PCB Cost?
The manufacturing cost of ultra-thin rigid PCB is a complex issue affected by many factors. Among them, size, complexity and quantity are among the main factors that determine the cost.
First of all, size is one of the important factors affecting the cost of ultra-thin rigid PCB. Generally speaking, larger size PCBs require more raw materials and production processes, so their manufacturing costs will be relatively high. On the contrary, a smaller PCB size can save material and process costs, thereby reducing the overall cost.
Secondly, the complexity of PCB will also directly affect manufacturing costs. Complex circuit designs require more production steps and process controls, which may require the use of more materials and labor costs. For example, PCBs with multi-layer stacking, high-density layouts and special processing requirements often require more time and resources to manufacture, so the cost will increase accordingly.
In addition, the order quantity is also one of the factors that determine the cost of ultra-thin rigid PCB. Generally speaking, large-volume orders enable mass production and automation, thereby reducing unit costs. Conversely, small batch orders may require more manpower and machine time, resulting in higher costs.
Although ultra-thin rigid PCBs may incur higher manufacturing costs due to their specialized characteristics, the space savings and performance improvements they provide often justify the investment. By reducing device size, improving performance efficiency and optimizing layout, ultra-thin rigid PCBs can bring greater flexibility and competitive advantages to the design and manufacturing of electronic devices.
In summary, understanding the key factors of ultra-thin rigid PCB cost is critical to developing effective production and procurement strategies. By weighing factors such as size, complexity and order quantity, companies can minimize costs while ensuring product quality and performance.
What materials are used in ultra-thin rigid PCB?
The design and manufacturing of ultra-thin rigid PCBs is a precise and complex process, and its performance and reliability depend on the materials selected. In this article, we will explore the materials commonly used in ultra-thin rigid PCBs and explain their importance and role in PCB manufacturing.
FR-4 fiberglass epoxy resin is one of the commonly used substrate materials in manufacturing ultra-thin rigid PCBs. It has excellent electrical insulation and mechanical strength, making it one of the ideal choices for manufacturing PCBs. The addition of fiberglass enhances the material’s durability, allowing it to withstand the stress and pressure of a variety of environmental conditions. At the same time, epoxy resin has good heat resistance and chemical stability, which helps protect the circuit components in the PCB from the external environment.
Copper is a commonly used conductive material in ultra-thin rigid PCBs, mainly used to make conductive paths and circuit connections. Its excellent electrical conductivity and good thermal conductivity make it one of the preferred materials in PCB manufacturing. Copper is highly malleable and corrosion-resistant, capable of forming stable connections in PCBs and ensuring fast transmission and stability of electrical signals. In addition, copper also has good welding properties, allowing it to be firmly combined with other materials to form reliable circuit structures.
In addition to FR-4 fiberglass epoxy resin and copper, other auxiliary materials may also be used in ultra-thin rigid PCB manufacturing, such as solder films, cover layers, and solder mask inks. These materials play an important role in the PCB manufacturing process. For example, solder films are used to protect circuit components from thermal stress during soldering, covering layers are used to enhance the wear resistance and corrosion resistance of PCBs, and solder mask inks are used to Prevent short circuits between soldering pins, etc.
Overall, the performance and reliability of ultra-thin rigid PCBs depend on the materials chosen. By selecting high-quality materials and combining them with exquisite manufacturing processes, ultra-thin rigid PCBs with excellent performance and stability can be produced to meet the needs of various high-end electronic products.
What are 5 qualities of a good customer service?
Excellent customer service is a crucial consideration when choosing an ultra-thin rigid PCB manufacturer. A manufacturer with excellent customer service will not only provide high-quality products, but also maintain good communication and collaboration with customers throughout the entire transaction. Here are five key qualities that can help you find such a manufacturer:
Speed of response: In a fast-paced business environment, responding quickly to customer inquiries and needs is crucial. Quality manufacturers promptly respond to customers’ emails, phone calls, or online messages and provide immediate support and solutions.
Reliability: Reliability is the basis for customers to trust manufacturers. A quality manufacturer will deliver products on time and ensure that the quality and performance of the product are as expected. They proactively resolve any issues that arise and ensure customers are satisfied with the products and services.
Expertise: Expertise is one of the key factors that sets manufacturers apart in the industry. High-quality manufacturers have rich experience and expertise and can provide customers with professional advice and support in PCB design, material selection, manufacturing processes, etc.
Flexibility: Flexibility means that manufacturers can adapt to customer needs and changes. They are able to flexibly adjust production plans, provide customized solutions, and modify and adjust them according to customer requirements to meet the needs of different projects.
Transparency: Transparency is the foundation for long-term relationships. Quality manufacturers maintain transparent communication with customers, provide clear quotations and contract terms, fully disclose product costs and delivery times, and promptly update customers on order status.
Manufacturers with the above qualities will provide customers with a smooth, efficient and satisfying working experience. They are not only product suppliers, but also partners, jointly promoting the successful realization of projects. Therefore, when choosing an ultra-thin rigid PCB manufacturer, be sure to consider these key attributes and choose a partner that can meet your needs in all aspects.
FAQs
What is the typical thickness of an ultra-thin rigid PCB?
The thickness of ultra-thin rigid PCBs often depends on specific application needs and design requirements. Generally speaking, their thickness can vary from 0.2mm to 0.8mm. For some special applications, such as mobile phones, tablets and wearable devices, thinner PCBs may be adopted to meet the strict requirements on device size and weight.
Can ultra-thin rigid PCBs withstand harsh environmental conditions?
Yes, although ultra-thin rigid PCBs are thin in thickness, they are designed and manufactured to ensure reliability and stability in a variety of harsh environmental conditions. These PCBs typically have excellent heat, moisture, and chemical resistance and can work well in high temperatures, high humidity, and corrosive environments. In addition, they have excellent mechanical strength and can resist vibration and shock, ensuring that the equipment can function properly under various conditions.
Does the manufacturing process of ultra-thin rigid PCB affect its electrical performance?
In the manufacturing process of ultra-thin rigid PCB, advanced processes and technologies are used to ensure the best electrical performance of the circuit board. Manufacturers will strictly control each step, including material selection, lamination, etching, drilling and coating, etc., to ensure that the conductivity, insulation and signal transmission performance of the PCB meet the design requirements. Therefore, even if the thickness of the PCB is very thin, they can still provide excellent electrical performance to ensure stable operation of the device.
What is the cost of ultra-thin rigid PCB?
The cost of ultra-thin rigid PCBs is affected by many factors, including size, number of layers, complexity, material selection and production volume. Generally speaking, due to its specialized characteristics and the complexity of the manufacturing process, the manufacturing cost of ultra-thin rigid PCB may be slightly higher than that of conventional PCB. However, compared with these additional costs, the space savings and performance advantages brought by ultra-thin rigid PCBs can often effectively balance and compensate for these costs.
How long is the design and manufacturing cycle for ultra-thin rigid PCB?
The design and manufacturing cycle times for ultra-thin rigid PCBs vary by manufacturer and specific project. Generally speaking, the entire process from design to production delivery can take anywhere from weeks to months, depending on the PCB’s complexity, size, and manufacturer’s production capabilities. Manufacturers typically work closely with clients to ensure projects are delivered on time and provide necessary support and feedback during the design and manufacturing process.