What are Ultra-thin CPU Substrates?
Ultra-thin CPU Substrates Manufacturer.We specialize in manufacturing ultra-thin CPU substrates, delivering cutting-edge solutions for high-performance computing needs. Our expertise lies in crafting substrates that enhance thermal management and signal integrity, meeting the demands of advanced electronic devices.
Ultra-thin CPU substrates are a vital component in modern electronic devices. It is a flat plate made of insulating material on which electronic components are mounted and circuits are connected through wires, pads and other connecting features precisely etched from the copper plate. These substrates are typically made from highly reliable materials such as FR4 (fiberglass reinforced epoxy laminate), which offer excellent electrical insulation properties and mechanical strength while being suitable for operation in a wide range of environmental conditions.
The design and manufacturing process of ultra-thin CPU substrates is very complex and precise. First, the surface of the substrate must be specially treated to ensure that it will receive the mounting of electronic components and be able to withstand the load required for various circuit connections. Then, through photolithography and etching techniques, fine circuit patterns are formed on the surface of the substrate. These patterns determine the connection methods and electrical paths between different components.
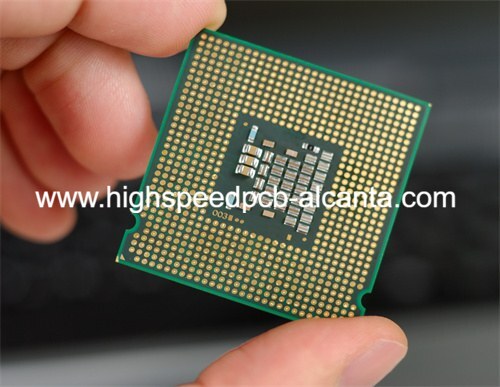
Ultra-thin CPU Substrates Manufacturer
In practical applications, the size and shape of ultra-thin CPU substrates can vary according to specific device requirements. They can effectively realize the compact layout of electronic components and support the miniaturization and functional integration of devices. This compactness not only saves space, but also improves the performance and reliability of the device.
Ultra-thin CPU substrates are widely used in various high-end electronic devices, including smartphones, tablets, portable electronics, medical equipment and aerospace systems. They are not only key support structures for electronic devices, but also an important driving force for the development of modern technology.
In short, ultra-thin CPU substrates have become an indispensable and important part of the modern electronics industry with their precise design, efficient manufacturing processes and wide range of applications, providing a solid foundation for various innovations and technological progress.
Ultra-thin CPU Substrates design Reference Guide.
The Ultra-Thin CPU Substrate Design Reference Guide is an important manual designed to provide comprehensive guidance to electronic designers. In today’s rapidly developing technological environment, ultra-thin CPU substrates play a key role, and their design quality directly affects the performance and reliability of electronic devices. Covering everything from basic principles to advanced techniques, this guide is designed to help designers master the best practices and methods for making ultra-thin CPU substrate layouts.
First, the best practices for ultra-thin CPU substrate design include layout optimization and signal integrity assurance. Designers need to consider how electronic components are arranged to maximize space utilization and ensure efficient and stable signal transmission. In addition, with the trend of increasingly miniaturized electronic devices, the design requirements of ultra-thin CPU substrates are becoming increasingly demanding, requiring precise inter-layer connections and complex wiring planning to meet the needs of high-density component integration.
Secondly, design rules are crucial in the production of ultra-thin CPU substrates. These rules cover line width, spacing, pad design, interlayer connections, etc., and are designed to ensure the stability and reliability of the circuit. Properly setting design rules can not only simplify the manufacturing process, but also effectively reduce production costs and time delays caused by design errors.
In terms of software tools and technologies, modern ultra-thin CPU substrate design relies on advanced CAD software and simulation tools. CAD software can provide an intuitive design interface and powerful layout functions to help designers achieve complex wiring and component arrangement. Simulation tools can predict how a circuit will perform in actual operation, optimizing designs and reducing the need for later adjustments.
In summary, the Ultra-Thin CPU Substrate Design Reference Guide is not only a technical manual, but also an important tool for designers to achieve innovation and technological progress. By following best practices, applying design rules flexibly, and using advanced software tools and techniques, designers can stand out in a highly competitive market and provide ultra-thin CPU substrate design solutions with superior performance and high reliability for electronic devices.
What material is used in Ultra-thin CPU Substrates?
Ultra-thin CPU substrate is an indispensable key component in modern electronic equipment, and the materials used play a vital role in its performance and applicability. Usually, materials with excellent electrical insulation properties and good mechanical strength are selected for ultra-thin CPU substrates to ensure a stable and reliable working environment.
Among them, one of the most common materials is FR4, which is fiberglass reinforced epoxy laminate. FR4 material is composed of fiberglass cloth and epoxy resin. Its excellent insulation properties make it widely used in the electronic field. It can effectively prevent the conduction of current between the surface of the board and between layers, thereby ensuring the stable operation of the circuit. In addition, FR4 also has good mechanical strength and can withstand physical pressure and vibration during assembly, ensuring that the substrate is not easily damaged during use.
In addition to FR4, flexible ultra-thin CPU substrates may also be made of materials such as polyimide. Polyimide is known for its excellent high-temperature properties and flexibility, making it suitable for applications that require folding or bending. This material maintains stable electrical performance in high-temperature environments while allowing substrates to function in complex structures and miniaturized designs.
Overall, the choice of ultra-thin CPU substrate depends on specific application requirements and design considerations. Designers need to consider factors such as electrical properties, mechanical strength, processing performance, and cost when deciding on materials to ensure that the final product meets expected performance and reliability requirements. With the continuous development and innovation of electronic equipment, ultra-thin CPU substrates, as their core components, will continue to play a key role in the path of technological progress.
What size are Ultra-thin CPU Substrates?
As an indispensable core component of electronic equipment, ultra-thin CPU substrates have significant changes in size due to the diversity of application requirements. From tiny smartphones and wearable devices to large industrial equipment and power electronics equipment, ultra-thin CPU substrates exhibit flexible size characteristics in different fields.
In the field of consumer electronics, such as smartphones and wearable devices, ultra-thin CPU substrates are usually very small because these devices need to save space as much as possible to accommodate other functional components and batteries. These tiny substrate sizes, typically a few square centimeters to tens of square centimeters, can accommodate highly integrated processors, memories, sensors, and wireless communication modules, enabling compact designs and high-performance output of devices.
In contrast, in industrial equipment and power electronics equipment, ultra-thin CPU substrates tend to be larger in size. These devices typically require more power management and thermal solutions, so the substrate size can reach tens to hundreds of square centimeters or even larger. These large substrates can not only accommodate more electronic components, but also support more complex circuit designs and higher power transmission requirements to meet various challenges and needs in industrial environments.
The size of ultra-thin CPU substrates is also affected by the limitations of the internal space of the device. Whether it is consumer electronics or industrial applications, the physical size and internal structural layout of the device will impose specific requirements on the substrate size. Therefore, the design of ultra-thin CPU substrates must take into account physical space utilization efficiency and overall system reliability while meeting performance and functional requirements.
To sum up, the size of ultra-thin CPU substrates varies depending on the specific application, ranging from tiny to large. This diversity reflects the importance and wide applicability of ultra-thin CPU substrates in modern electronic devices, providing a solid foundation for technological innovation and progress in various industries.
The Manufacturer Process of Ultra-thin CPU Substrates.
The manufacturing process of ultra-thin CPU substrates is a precise and complex project, covering multiple key steps to ensure that the final product has excellent electrical performance and reliability. Here is a detailed description of its main steps:
First, the manufacturing process begins with the substrate preparation stage. This includes selecting an appropriate substrate material, typically one with a high degree of electrical insulation and mechanical strength such as FR4 or polyimide (PI), to meet the design requirements of the device.
Next comes the deposition of the copper layer. A layer of copper is applied to the surface of the substrate to provide conductivity for subsequent circuit connections.
Photoresist application and exposure is one of the critical steps in the manufacturing process. At this stage, photoresist is coated on the copper layer, and the designed circuit pattern is transferred to the photoresist through exposure. These patterns will determine future conductive paths and the layout of electronic components.
After the exposure is completed, the etching process is performed. Etching is the removal of parts of the copper layer that are not protected by photoresist through a chemical solution to form the wires and pads in the circuit. Precise control of the timing and conditions of the etching process is critical to ensure circuit accuracy and reliability.
Drilling operations then proceed. Drilling is used to create holes in the substrate for mounting electronic components and making circuit connections. The location and size of the drilled holes need to match the design requirements exactly to ensure correct installation and connection of subsequent components.
After drilling is completed, proceed to the component installation stage. This involves mounting the electronic components on the substrate exactly as designed. Modern manufacturing processes often employ surface mount technology (SMT), which uses automated equipment to precisely mount small electronic components on the surface of a substrate, increasing production efficiency and component density.
Next comes the welding process. Soldering connects electronic components to wires or pads on a substrate, ensuring the integrity and stability of the circuit. Soldering can use techniques such as wave soldering or hot air fusion soldering, with the specific choice depending on component type and process requirements.
Finally, conduct testing and quality control. After completion of manufacturing, each ultra-thin CPU substrate needs to undergo rigorous testing procedures to ensure that its electrical performance, reliability and operating stability meet design requirements and industry standards.
Overall, the manufacturing process of ultra-thin CPU substrates relies on advanced process technology and strict quality management to ensure that the final product can meet the strict requirements for high performance and stability of modern electronic equipment.
The Application area of Ultra-thin CPU Substrates.
As an indispensable and key component of modern electronic equipment, ultra-thin CPU substrates are widely used in multiple industries, including consumer electronics, communications, automobiles, aerospace, medical equipment, and industrial automation. Their application range is extremely wide, from daily-use smartphones and personal computers to medical equipment and satellite communication systems in high-tech fields, all relying on the precision design and reliability of ultra-thin CPU substrates.
In the field of consumer electronics, ultra-thin CPU substrates are widely used in products such as mobile phones, tablets, and smart home devices. These devices require small size and powerful functions. Ultra-thin CPU substrates can meet the needs of compact design and support various complex circuits and processing capabilities.
The communications industry requires ultra-thin CPU substrates to support various communications equipment, including base stations, network routers, satellite communication systems, etc. These devices have extremely high requirements on the performance and stability of the circuit board. The ultra-thin CPU substrate ensures the stable operation of communication equipment in various environments through its superior electrical characteristics and reliability.
In the automotive field, ultra-thin CPU substrates are widely used in vehicle electronic systems, such as vehicle navigation, vehicle entertainment systems, driving assistance systems, etc. These systems have high anti-interference requirements for high temperature, vibration and electromagnetic interference. The ultra-thin CPU substrate ensures reliability and stability under harsh conditions through special design and material selection.
In the aerospace field, ultra-thin CPU substrates are used in satellites and avionics equipment to support key applications such as satellite communications, navigation systems, and radar systems. These applications have extremely stringent requirements for lightweight and high performance. Ultra-thin CPU substrates can not only meet these requirements, but also maintain high reliability in space constraints and radiation-resistant environments.
In the field of medical equipment, ultra-thin CPU substrates are used in various types of medical imaging equipment, monitoring equipment, implantable medical equipment, etc. to support precise control and data processing of medical equipment, ensuring the accuracy and safety of medical diagnosis and treatment. .
Finally, in the field of industrial automation, ultra-thin CPU substrates are widely used in control systems, sensor networks, robotics, etc., supporting the development of factory automation and intelligent manufacturing, and improving production efficiency and product quality.
In short, as a core component of modern electronic technology, ultra-thin CPU substrates play an irreplaceable role in multiple industries, promote technological progress and application expansion, and provide a solid foundation for performance improvement of various devices and systems. Base.
What are the advantages of Ultra-thin CPU Substrates?
Ultra-thin CPU substrates have significant advantages in modern electronic equipment. Compared with traditional wiring methods, their advantages are mainly reflected in the following aspects.
First of all, ultra-thin CPU substrates can achieve extremely compact layouts, effectively promoting the miniaturization and lightweighting of electronic devices. This compactness not only makes the device easier to carry and integrate, but also helps optimize the internal space utilization of the device, improving overall performance and design flexibility.
Secondly, the ultra-thin CPU substrate uses a standardized manufacturing process to ensure consistent product quality and reliability. Through precise process control and strict quality management, each ultra-thin CPU substrate can stably meet the design specifications, ensuring long-term stable operation of electronic equipment and reducing maintenance and failure rates.
In addition, the ultra-thin CPU substrate uses advanced automated assembly processes to greatly simplify the production process, significantly reduce labor costs and improve production efficiency. This not only speeds up time to market, but also reduces possible human errors during the production process, ensuring consistency and repeatability of production.
Ultra-thin CPU substrates also have a high degree of customization capabilities and can be designed and manufactured according to customers’ specific needs. Whether it is complex circuit layout or specific component integration, ultra-thin CPU substrates can flexibly respond to the specific needs of different industries and application fields, and provide customers with customized solutions.
Finally, because ultra-thin CPU substrates can reduce unit costs through mass production, they have significant economic advantages in mass manufacturing. This cost-effectiveness makes ultra-thin CPU substrates not only suitable for high-end electronic products, but also widely used in consumer electronics, communication equipment, automotive electronics, industrial control and other fields, promoting the technological progress and market competitiveness of the entire industry.
In short, ultra-thin CPU substrates, with their compact layout, high reliability, convenient assembly process, flexible customization capabilities and affordable cost-effectiveness, have become an indispensable and key component in the design of modern electronic equipment, laying the foundation for innovation and technology. development provides important support and guarantee.
FAQ
What is the difference between ultra-thin CPU substrate and traditional PCB?
Compared with traditional PCB, ultra-thin CPU substrate is mainly thinner in thickness. Traditional PCBs are usually thicker and suitable for general electronic devices, while ultra-thin CPU substrates are designed for high-end electronic products that require extremely thin and light designs, such as smartphones, tablets, and wearable devices. Its design requires special consideration of the balance of thermal conductivity, mechanical strength and electrical performance.
What are the material options for ultra-thin CPU substrates?
Common ultra-thin CPU substrate materials include FR4 (fiberglass reinforced epoxy laminate), polyimide (PI) and flexible substrate materials. Each material has its own unique advantages and applicable scenarios. For example, FR4 is suitable for general rigid PCBs, while polyimide is suitable for applications that require flexibility and high-temperature stability.
What key factors need to be paid attention to in the design of ultra-thin CPU substrate?
When designing ultra-thin CPU substrates, key factors include compactness of circuit layout, optimization of heat dissipation, maintenance of signal integrity, and considerations of mechanical strength. Especially when dealing with the trend of thinning, designers need to pay special attention to material selection and process optimization to ensure a balance between performance and reliability.
What are the special features of the manufacturing process of ultra-thin CPU substrates?
Compared with traditional PCB manufacturing, the manufacturing process of ultra-thin CPU substrates requires higher-precision process control and stricter material selection. For example, etching of thin substrates, copper layer deposition, and precise component positioning and soldering techniques all require special attention to ensure overall performance and reliability.