Ultra-thin BGA Substrate Manufacturer.An innovative leader in electronic manufacturing, our company specializes in crafting ultra-thin Ball Grid Array (BGA) substrates. With cutting-edge technology and precision engineering, we produce substrates that push the boundaries of miniaturization in electronic devices. Our commitment to excellence ensures that each substrate meets the highest standards of quality and reliability. By leveraging advanced materials and processes, we enable our clients to create next-generation electronics with unparalleled performance and compactness. Trust in our expertise to deliver ultra-thin BGA substrates that pave the way for the future of electronic innovation.
With the rapid development of electronic technology, the smart devices around us are becoming smaller and more sophisticated at an alarming rate, and at the same time, their functions are becoming increasingly powerful. In this ubiquitous electronic revolution, ultra-thin BGA substrates are leading the development direction of future electronic products with their excellent performance and advanced design. As a key connectivity and integration solution, it is redefining our expectations for electronic devices and opening up new possibilities for the development of next-generation smart products.
What is Ultra-thin BGA Substrate?
Ultra-thin BGA (Ball Grid Array) packaging substrate is an important technological innovation in today’s electronic equipment design field. With its excellent performance and ultimate design flexibility, it has injected new vitality into the manufacturing and development of modern electronic devices. So, what exactly is an ultra-thin BGA packaging substrate?
Ultra-thin BGA packaging substrate is a packaging solution based on printed circuit board (PCB) technology. Compared with traditional packages, it is characterized by its extremely thin thickness and high-density solder ball array. This enables ultra-thin BGA packaging substrates to achieve a more compact packaging structure while maintaining high reliability, making it suitable for various high-performance applications.
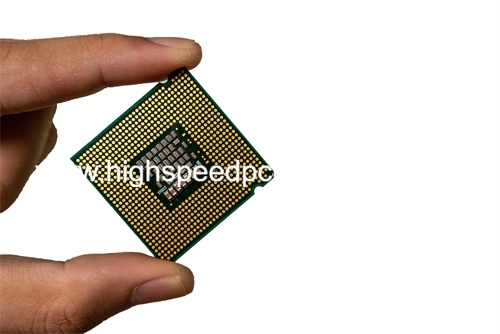
Ultra-Thin BGA Substrate Manufacturer
In the ultra-thin BGA package substrate, the density and arrangement of the solder ball array are carefully designed to ensure the connection of multiple pins in a small space. This design not only makes it easier to automate the electronic device packaging process, but also improves the reliability and stability of the connection, providing a solid foundation for the long-term stable operation of electronic equipment.
Ultra-thin BGA packaging substrates are widely used in various high-performance electronic devices, such as smartphones, tablets, laptops, drones, etc. Its excellent electrical performance and compact packaging structure make it one of the core components in these devices. At the same time, the flexibility and customizability of ultra-thin BGA packaging substrates also provide electronic equipment designers with more possibilities, allowing them to customize more suitable solutions according to specific needs.
In general, ultra-thin BGA packaging substrates not only represent cutting-edge technology in the field of electronic device design, but are also an important driving force for the development of electronic equipment manufacturing in the direction of thinner, lighter and higher performance. Its emergence and application show us the pinnacle of the development of electronic technology, and also bring broader prospects and possibilities for the design and manufacturing of future electronic equipment.
Ultra-thin BGA Substrate design Reference Guide.
As electronic products increasingly pursue thinner, lighter and higher performance, the design of ultra-thin BGA (Ball Grid Array) packaging substrates has become crucial. This guide will provide reference guidance on ultra-thin BGA package substrate design to help you make the most of this critical technology.
Design Principles
When designing ultra-thin BGA packaging substrates, the primary consideration is to meet the performance requirements of electronic devices and the limitations of packaging space. Ensure that the package substrate has the proper size, layering, and routing for optimal electrical performance and thermal dissipation.
Material selection
Selecting the appropriate substrate material is critical to the performance of ultra-thin BGA package substrates. Commonly used substrate materials include FR-4, high-frequency materials and ceramic substrates. Each material has its specific advantages and disadvantages and needs to be selected according to specific application scenarios.
Placement and routing
Reasonable layout and wiring are the keys to ensuring stable performance of ultra-thin BGA package substrates. Optimized layout can minimize signal interference and electromagnetic radiation while ensuring good connections for power distribution and ground loops.
Laminated design
Through reasonable lamination design, the signal integrity and heat dissipation performance of ultra-thin BGA packaging substrate can be effectively improved. Using appropriate laminate structures and vertical connection technologies, higher integration and lower transmission delays can be achieved.
Thermal management
Effective thermal management is an important consideration in the design of ultra-thin BGA package substrates. By rationally designing heat dissipation holes, heat dissipation copper layers and heat sinks, the heat dissipation efficiency of the packaging substrate can be effectively improved and the electronic devices can work stably for a long time.
Performance verification
After completing the design, be sure to conduct rigorous performance verification and testing. Through simulation and actual testing, the electrical performance, thermal characteristics and reliability of the ultra-thin BGA packaging substrate are verified to ensure that it meets the design requirements.
Ultra-thin BGA packaging substrate design is a key link in modern electronic device design. Reasonable design and optimization can significantly improve product performance and reliability. By following the design principles and suggestions provided in this guide, you can better apply ultra-thin BGA packaging substrate technology and realize the innovation and development of electronic products.
What material is used in Ultra-thin BGA Substrate?
The material selection of ultra-thin BGA (Ball Grid Array) packaging substrate is crucial and directly affects its performance and reliability. Typically, ultra-thin BGA packaging substrates use a range of high-performance materials to meet stringent requirements for packaging density, electrical performance and thermal management.
First, the main material of the substrate is usually a multi-layer film substrate. Common materials include fiberglass-reinforced epoxy resin (FR-4) or polyimide (PI). These materials have excellent mechanical strength, dimensional stability and high temperature resistance, and are suitable for the manufacture of ultra-thin BGA packages.
Secondly, the choice of conductive layer is also crucial. Conductive layers, usually made of copper, are used to form electrical connections and signal transmission paths. In ultra-thin BGA packages, the design and layout of the conductive layer need to be precisely controlled to ensure the stability and reliability of signal transmission.
In addition, ultra-thin BGA packaging substrates may also use other auxiliary materials, such as filling materials and protective coatings, to enhance their performance. Filler materials are used to fill voids and enhance the mechanical strength of the substrate, while protective coatings provide additional protection against chemical attack or environmental damage.
In general, the material selection for ultra-thin BGA packaging substrates needs to comprehensively consider multiple factors, including mechanical properties, electrical properties, thermal management and manufacturing costs. Through reasonable selection of materials, combined with precise manufacturing processes, the ultra-thin BGA packaging substrate can be ensured to have excellent performance and reliability, thereby meeting the needs of various high-performance electronic devices.
What size are Ultra-thin BGA Substrate?
Ultra-thin BGA packaging substrates are typically relatively small in size but feature high-density connections and layout as they are designed for high-performance and compact electronic devices. Dimensional accuracy and compactness are essential to meet the requirements of modern electronic devices.
Typically, the size of the ultra-thin BGA package substrate depends on the requirements of the specific application. Although there is no standard size, in smartphones, tablets, and other mobile devices, they are usually designed to be smaller and thinner to meet the trend of thinner devices. For other applications, such as industrial control systems or medical equipment, the dimensions may be slightly larger to accommodate more connections and components.
The size design of ultra-thin BGA packaging substrates must balance multiple factors, including layout density, thermal requirements, electrical performance and manufacturing feasibility. Therefore, these factors need to be carefully considered during the design process and ensure that the final dimensions can meet the required performance specifications.
Although the ultra-thin BGA packaging substrate is relatively small in size, its importance in modern electronic devices cannot be ignored. They provide critical electrical connections and packaging solutions for devices while helping to achieve high performance and compact designs for devices.
The size of ultra-thin BGA packaging substrates may change with the development of technology and changes in market demand, but they are always an integral part of the design of electronic devices, providing a solid foundation for the performance and functionality of the device.
The Manufacturer Process of Ultra-thin BGA Substrate.
The manufacturing process of ultra-thin BGA (Ball Grid Array) packaging substrate is a complex and precise process that requires the integration of advanced process and material technologies. From substrate design to final packaging, each step is critical and requires precise control and highly automated production lines.
First, the manufacturing process begins with the substrate design phase. At this stage, engineers use CAD software to design an ultra-thin BGA package substrate layout that meets specific requirements. Design considerations include size, layering, electrical characteristics, and thermal management.
Next comes the lamination process. This step involves laminating pre-designed substrates together and pressing them together in an environment of high temperature and pressure. Through lamination, the various layers of the substrate are tightly fixed together to form a strong whole.
Copper plating is another critical step in the manufacturing process. In this process, the surface of the substrate needs to be plated with a layer of copper to form a surface with good conductivity. Copper layer uniformity and thickness control are critical to the quality of the final package.
Finally, there is the packaging stage. During the packaging process, electronic components are mounted on the substrate and connected to the substrate through soldering and other methods. Encapsulation materials, such as resins, are applied around encapsulated electronic components to provide protection and mechanical support.
The entire manufacturing process requires highly automated production lines to ensure production efficiency and product quality. A sophisticated control system monitors every step to ensure that each ultra-thin BGA package substrate meets specifications.
In general, the manufacturing process of ultra-thin BGA packaging substrates involves multiple key steps, each of which requires precise control and a highly automated production line. This highly engineered manufacturing process is key to ensuring the quality and performance of ultra-thin BGA packaging substrates.
The Application area of Ultra-thin BGA Substrate.
Ultra-thin BGA packaging substrate is an important technology in the field of electronic equipment today. Its application range is wide, covering various electronic equipment such as smartphones, tablets, laptops, and drones. Its excellent electrical performance and compact package structure make it an ideal choice for those pursuing high performance and thin and light designs.
In the field of smartphones, ultra-thin BGA packaging substrates are widely used in the packaging of motherboards and core components, providing stable and reliable electrical connections and compact size designs for mobile phones. This not only helps improve the overall performance and stability of the phone, but also meets users’ needs for thinness, lightness and portability.
In the fields of tablets and laptops, the application of ultra-thin BGA packaging substrates also plays an important role. Due to the high volume and weight requirements of this type of equipment, ultra-thin BGA packaging substrates can effectively reduce the size of electronic components, thereby achieving a thinner and lighter design without sacrificing performance and stability.
In addition, ultra-thin BGA packaging substrates are also widely used in drones and other aerospace fields. Since UAVs have very strict weight and space restrictions, ultra-thin BGA packaging substrates can help UAV systems achieve higher performance indicators and longer flight times.
In general, the application of ultra-thin BGA packaging substrates in the field of electronic equipment has become a trend. Its excellent electrical performance, compact packaging structure and strong adaptability make it play an irreplaceable role in electronic products that pursue high performance and thin and light design. With the continuous advancement of technology and the expansion of application fields, ultra-thin BGA packaging substrates will surely show a broader development space in the future.
What are the advantages of Ultra-thin BGA Substrate?
Ultra-thin BGA packaging substrate is an important innovation in modern electronic device design. It has many advantages over traditional packaging solutions and provides a reliable solution for performance improvement and volume compression of electronic devices.
First, the ultra-thin BGA packaging substrate is small in size and light in weight. As consumers’ demands for thinner, lighter and more portable electronic devices continue to increase, traditional packaging solutions are often unable to meet this demand. The ultra-thin BGA packaging substrate uses advanced materials and processes to achieve a more compact packaging structure, making the overall electronic device smaller and lighter, providing users with a more portable experience.
Secondly, the ultra-thin BGA packaging substrate has the characteristics of fast transmission speed. In modern high-performance electronic equipment, data transmission speed is a crucial indicator. The ultra-thin BGA packaging substrate adopts high-quality conductive materials and design, which can achieve higher signal transmission speed, improve the data processing efficiency of the device, and meet users’ needs for high-speed data transmission.
In addition, the ultra-thin BGA packaging substrate has good heat dissipation performance. As the performance of electronic devices continues to improve, heat also increases accordingly. If heat dissipation is poor, the performance of the device will decrease or even be damaged. The ultra-thin BGA packaging substrate adopts advanced heat dissipation design and materials, which can effectively conduct heat to the external environment, maintain the stable working condition of the equipment, and extend the service life of the equipment.
In general, ultra-thin BGA packaging substrates can not only improve the performance of electronic devices, but also achieve volume compression to meet consumers’ needs for thinness, lightness and portability. Its small size, light weight, fast transmission speed, and good heat dissipation performance make it an indispensable part of the design of modern electronic equipment.
FAQ
How reliable is the ultra-thin BGA packaging substrate?
The ultra-thin BGA packaging substrate undergoes strict design and manufacturing processes to ensure its stability and reliability. The use of advanced materials and process technologies, as well as strict quality control standards, ensures that each packaging substrate can provide reliable electrical connections and performance under various environmental conditions.
Is the ultra-thin BGA package substrate easy to maintain?
Ultra-thin BGA package substrates are usually designed to be soldered to the motherboard of electronic devices, so professional technology and equipment may be required for maintenance. However, once installed correctly, ultra-thin BGA package substrates usually require no additional maintenance and can operate stably for a long time.
What is the impact of ultra-thin BGA packaging substrates on the environment?
Ultra-thin BGA packaging substrates usually use environmentally friendly materials and comply with relevant environmental regulations and standards. Automation technologies and resource optimization measures used in the manufacturing process help reduce energy consumption and waste generation, thereby reducing environmental impact.
What types of electronic equipment are ultra-thin BGA packaging substrates suitable for?
Ultra-thin BGA packaging substrates are suitable for various types of electronic devices, including smartphones, tablets, laptops, drones, etc. Due to its compact packaging structure and excellent electrical performance, ultra-thin BGA packaging substrates are particularly suitable for high-performance devices that have strict requirements on volume and weight.
What are the advantages of ultra-thin BGA packaging substrate compared with traditional packaging solutions?
Compared with traditional packaging solutions, ultra-thin BGA packaging substrates have the advantages of small size, light weight, fast transmission speed, and good heat dissipation performance. Its compact design can achieve higher integration and better performance, thereby meeting the needs of modern electronic devices for thinness, lightness and high performance.