Ultra-small Size Package Substrates Manufacturer.An Ultra-small Size Package Substrates Manufacturer specializes in producing highly compact substrates essential for advanced electronics. These miniature substrates enable the development of cutting-edge devices, enhancing performance and efficiency while reducing overall size. The manufacturer’s expertise lies in precision engineering and innovative technology, ensuring that their products meet the demanding requirements of modern microelectronics, from smartphones to medical devices.
Welcome to our latest guest post! In today’s discussion, we will delve into the critical role of Ultra-small Size Package Substrates in modern electronics. These compact substrates play an important role in connecting micro-components and chips, providing critical support for high-performance, high-density design of electronic devices. Let’s explore their importance and how they advance electronics!
What are Ultra-small Size Package Substrates?
Ultra-small size packaging substrates are an indispensable and critical component in today’s modern electronic devices. They carry tiny components and chips and are at the heart of high-density, high-performance electronic devices. Compared with traditional packaging, ultra-small size packaging substrates are specially designed to adapt to the increasingly shrinking size and higher performance requirements of modern electronic devices.
These substrates are structurally sophisticated and complex, enabling efficient implementation of complex functions in electronic devices through precise layout and connection of micro-components and chips. They are usually made of materials such as high-performance polymers, metal substrates or special ceramics, with excellent thermal conductivity, electrical properties and mechanical strength, ensuring the stability and reliability of electronic devices.
One of the key features of ultra-small package substrates is their compact size. They are generally smaller than traditional packages, allowing for higher integration and smaller device size, making electronic products lighter and more portable while improving design flexibility and aesthetics.
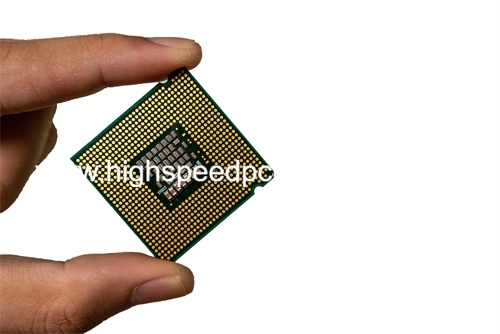
Ultra-small Size Package Substrates Manufacturer
In the manufacturing process of electronic devices, ultra-small size packaging substrates play a vital role. They undergo precise design and manufacturing processes to ensure stable connections and effective transmission between electronic components, providing a solid foundation for the normal operation of the equipment.
In general, the emergence and widespread application of ultra-small size packaging substrates not only promotes the continuous improvement of the performance and functions of electronic devices, but also brings more convenience and possibilities to modern life. In the future, with the continuous advancement and innovation of technology, ultra-small size packaging substrates will continue to play an important role, injecting new vitality and power into the development of the electronic field.
Ultra-small Size Package Substrates design Reference Guide.
When designing ultra-small size packaging substrates, many factors need to be considered to ensure that the final product has high performance, high reliability, and meets the needs of specific applications. Here are some key principles, considerations, and best practices for designers to consider:
Packaging density and layout optimization
Ultra-small package substrates often require a large number of components and connections to be accommodated in a limited space. Therefore, designers should optimize component layout and minimize wiring length to reduce signal transmission delay and electromagnetic interference.
Thermal management
Due to high packaging density, ultra-small size packaging substrates may generate a large amount of heat during operation. Therefore, effective thermal management solutions, such as heat sinks, heat sinks, heat pipes, etc., need to be considered during the design process to ensure that components operate within a safe temperature range.
Signal integrity
High-speed signal and power lines on ultra-small package substrates require strict layout and layer planning to minimize crosstalk and signal distortion. During the design process, proper interlayer pin routing, differential signal layout, and impedance matching techniques should be used to ensure signal integrity.
Material selection
Selecting the appropriate substrate material is critical to the performance of ultra-small package substrates. Commonly used materials include high-performance FR-4 fiberglass composite panels, polyimide (PI) and polyetheretherketone (PEEK), etc., which have good electrical properties, thermal properties and mechanical strength.
Manufacturing feasibility
Manufacturing feasibility and cost-effectiveness need to be taken into consideration during the design process. Reasonable selection of component size and spacing reduces special process requirements, helping to reduce manufacturing costs and improve production efficiency.
Reliability design
Ultra-small size packaging substrates are often used in high-end electronic devices, so designers must consider the long-term reliability of the product. Use appropriate packaging technology, pin layout and welding process to improve the product’s resistance to shock, vibration and corrosion.
To sum up, designing ultra-small size packaging substrates requires comprehensive consideration of packaging density, thermal management, signal integrity, material selection, manufacturing feasibility and reliability design. By following the above principles and best practices, designers can ensure that ultra-small size packaging substrates have excellent performance and reliability to meet the needs of different application scenarios.
What material is used in Ultra-small Size Package Substrates?
Material selection for ultra-small package substrates is a key factor in ensuring device performance and reliability. When selecting materials, aspects such as thermal conductivity, electrical properties, mechanical strength, and cost need to be considered. Here are some common material options:
High performance polymers
High-performance polymers are one of the common materials for ultra-small package substrates. These polymers often have excellent thermal conductivity and electrical insulation properties, enabling them to meet the needs of high-density integrated circuits. For example, polymer materials such as polyimide (PI) and polytetrafluoroethylene (PTFE) have good high temperature resistance and chemical stability and are suitable for various harsh environmental conditions.
Metal substrate
Metal substrate is another common ultra-small size packaging substrate material. Aluminum substrates and copper substrates are commonly used metal substrate materials. They have excellent thermal conductivity and mechanical strength and are suitable for applications that require heat dissipation and circuit protection. Metal substrates can also provide good electromagnetic shielding effects and reduce circuit interference and noise.
Special ceramics
Special ceramic materials are also widely used in ultra-small size packaging substrates. For example, ceramic materials such as aluminum oxide (Al2O3) and silicon nitride (Si3N4) have excellent insulation properties and chemical stability, and can maintain stability in high-temperature and high-pressure environments. These specialty ceramic materials are often used in the packaging of high-frequency circuits and power electronics to achieve high performance and reliability.
Proper material selection is critical to the performance and reliability of ultra-small package substrates. Manufacturers should carefully evaluate the characteristics of different materials during the design and manufacturing process and make appropriate choices based on specific application needs to ensure that the product can achieve expected performance indicators and service life.
What size are Ultra-small Size Package Substrates?
Ultra-small size packaging substrates play a vital role in modern electronic devices, and their unique compact size provides huge flexibility and innovation space for the design and functionality of electronic products. These substrates are often highly customized and can be precisely designed and manufactured according to the needs of a specific application to achieve optimal performance and efficiency.
Compared with traditional packaging, ultra-small size packaging substrates are smaller and more compact, which allows them to achieve higher integration levels in limited space. This means that more electronic components and functions can be integrated into the same device, enabling more diverse and complex functions without increasing the overall size of the device. Especially in the field of portable devices, such as smartphones, tablets and wearable devices, the application of ultra-small size packaging substrates is particularly prominent, providing these devices with thinner, lighter and more portable design solutions.
In addition, the compact size of ultra-small package substrates brings many other advantages. For example, they can reduce wiring lengths between circuit boards, reduce signal transmission delays and energy losses, thereby improving device performance and efficiency. In addition, due to their smaller size, these substrates can also reduce the overall weight of the device and improve the carrying comfort and portability of the device.
In general, the size advantage of ultra-small size packaging substrates is not only reflected in its compact appearance, but also in that it provides higher integration, smaller volume and superior performance for electronic products. With the continuous advancement of technology and changing market demands, ultra-small size packaging substrates will continue to play an important role in the electronic field and bring more innovation and possibilities to various application scenarios.
The Manufacturer Process of Ultra-small Size Package Substrates.
The manufacturing process of ultra-small size packaging substrates is a precise and complex process involving multiple key steps, from design to testing. The first is the design stage, where design engineers use CAD software to convert circuit diagrams into PCB layout designs. At this stage, taking into account the special requirements of ultra-small size, designers need to accurately determine the layout, spacing and connection methods of components to ensure the stability and performance of the final product. This is followed by the manufacturing phase, one of the most critical steps being the creation of the printed circuit board (PCB). This involves transferring a designed layout onto a substrate, often using chemical etching or mechanical engraving to strip away unnecessary copper foil to form a pattern of circuit connections. Next comes the process of adding components, which requires highly sophisticated machinery and technology to ensure accurate placement and soldering of components. In ultra-small package substrates, the size and pitch of components are smaller, so higher manufacturing precision is required. Finally, there is the testing phase, where the manufactured PCB is functionally tested and performance evaluated using automatic test equipment to ensure that it meets the design requirements. Many challenges need to be faced in this process, such as how to improve production efficiency while ensuring accuracy, and how to deal with assembly difficulties caused by too small component sizes. In addition, the manufacturing of ultra-small size packaging substrates also needs to take into account environmental factors and process improvements to improve product quality and reliability. In summary, the manufacturing process of ultra-small size packaging substrates requires sophisticated technology and professional equipment to ensure the quality and performance of the final product.
The Application area of Ultra-small Size Package Substrates.
Ultra-small size packaging substrates play a vital role in the modern electronics field. Their wide range of applications cover many fields, providing high-performance and high-reliability solutions for various electronic devices.
First, let’s look at the smartphone space. In the context of today’s rapid development of mobile communication technology, smartphones have become an indispensable part of people’s lives. The application of ultra-small size packaging substrate allows mobile phones to have higher integration and smaller size, thus achieving a lighter and more portable design. At the same time, this substrate also provides a stable and reliable electronic connection for the mobile phone, ensuring normal communication between the various functional modules of the mobile phone and ensuring a smooth and stable user experience.
Secondly, the field of wearable devices is also one of the important application scenarios for ultra-small size packaging substrates. As people’s demands for health monitoring and life records increase, wearable devices such as smart watches and health monitors are gradually becoming the focus of public attention. The application of ultra-small size packaging substrates allows these devices to be thinner, lighter and more comfortable while maintaining high performance and reliability, providing users with convenient health management and life assistance functions.
In the field of medical devices, ultra-small size packaging substrates also play an important role. Medical equipment has extremely high requirements for stable and reliable performance, and ultra-small size packaging substrates are ideal for meeting this demand. For example, medical monitoring instruments, diagnostic equipment, etc. often require electronic components with high precision and sensitivity, and ultra-small size packaging substrates can ensure the tight connection and stable operation of these components, providing reliable data support for medical diagnosis.
Finally, in the field of industrial control, ultra-small size packaging substrates also play an important role. Industrial automation, robotics and other fields have increasingly higher requirements for electronic equipment. The high performance and high reliability of ultra-small size packaging substrates enable industrial control systems to operate more stably and accurately, improving production efficiency and product quality. .
In short, ultra-small size packaging substrates play an irreplaceable role in many fields such as smartphones, wearable devices, medical equipment, and industrial control. They provide key support for the development and application of modern electronic equipment and promote technological progress and society. develop.
What are the advantages of Ultra-small Size Package Substrates?
Ultra-small Size Package Substrates (Ultra-small Size Package Substrates) have shown unparalleled advantages in today’s electronics industry. Compared with traditional packaging methods, their advantages are more obvious.
First, the ultra-small size packaging substrate enables higher integration. As modern electronic devices have increasingly strict requirements on volume and weight, ultra-small size packaging substrates can accommodate more components and functional modules in a limited space. This highly integrated design not only increases circuit complexity, but also reduces overall system cost and power consumption.
Secondly, the ultra-small size packaging substrate can achieve smaller device size. By using advanced packaging technologies and materials, ultra-small size packaging substrates can significantly reduce the size of electronic devices, making the devices lighter, more portable, and easier to embed in various application scenarios. This is an extremely attractive feature for portable devices such as smartphones, tablets, and wearable devices.
In addition, the ultra-small size packaging substrate can also achieve lower power consumption. Because electronic components are closer together, signals travel shorter distances, reducing energy loss. At the same time, the design of ultra-small size packaging substrates is also more refined, which can better optimize circuit layout, reduce power consumption and improve energy efficiency. This low-power design not only extends battery life, but also helps reduce device heat and improves the stability and reliability of the overall system.
To sum up, ultra-small size packaging substrates provide strong support for the performance and competitiveness of electronic products with their advantages such as high integration, small size and low power consumption. With the continuous development of technology and the advancement of packaging technology, it is believed that ultra-small size packaging substrates will play an increasingly important role in the future electronics industry, bringing more convenience and innovation to our lives.
FAQ
What is the difference between ultra-small size packaging substrate and traditional packaging?
Ultra-small size packaging substrates are more compact than traditional packaging and usually use advanced manufacturing processes to achieve higher integration and smaller size. This makes them particularly suitable for the design and manufacture of high-density electronic devices.
Is the manufacturing cost of ultra-small size packaging substrate high?
The cost of manufacturing ultra-small package substrates is typically higher because of the advanced materials and manufacturing techniques required. However, with the continuous development of technology and the increase of market demand, the related manufacturing costs are gradually decreasing.
How reliable are ultra-small size packaging substrates?
Ultra-small size packaging substrates usually take various factors into consideration during the design and manufacturing process to ensure high reliability. These substrates typically use high-quality materials and rigorous manufacturing processes to meet the needs of a variety of application environments.
What applications can ultra-small package substrates be used for?
Ultra-small size packaging substrates can be widely used in smartphones, wearable devices, medical equipment, industrial control, automotive electronics and other fields. They play a key role in these areas, supporting the performance and functionality of electronic products.