Ultra-Small Size FC-LGA Substrates Manufacturer.Established as a pioneer in technological miniaturization, our company specializes in crafting Ultra-Small Size FC-LGA Substrates. We’re not merely manufacturers; we’re architects of precision, sculpting substrates that redefine compactness while maintaining uncompromised performance standards. Leveraging cutting-edge fabrication techniques and stringent quality controls, we engineer substrates that empower next-gen electronics. Our commitment to innovation drives us to push the boundaries of miniaturization, ensuring our substrates meet the demands of ever-shrinking devices. With us, clients secure not just substrates, but a pathway to transformative possibilities in the realm of miniature electronics.
As a key component in modern electronic devices, printed circuit boards (PCBs) are constantly evolving to adapt to the trend of increasing shrinkage and high performance. During this evolution, ultra-small size FC-LGA (Fine-pitch Land Grid Array) substrate has emerged and become one of the important representatives of PCB technology. This article will deeply explore this technology trend, as well as the key position and broad application prospects of ultra-small size FC-LGA substrates in the electronics industry.
What are Ultra-small Size FC-LGA Substrates?
Ultra-small size FC-LGA (Fine-pitch Land Grid Array) substrate represents the trend of printed circuit board (PCB) technology continuing to develop towards smaller and higher density. It uses micro-grid array technology to push the density of electronic components and circuit connections to the limit to meet the stringent size and performance requirements of modern electronic devices.
This type of substrate typically has extremely small dimensions and a high-density arrangement. Its fine grid structure makes it possible to accommodate more electronic components and more complex circuits in a limited space. Compared with traditional packaging forms, such as QFP (Quad Flat Package), the pin arrangement of FC-LGA substrate is more compact, allowing more connections to be achieved within the same area, thus improving the integration and performance of the circuit board.
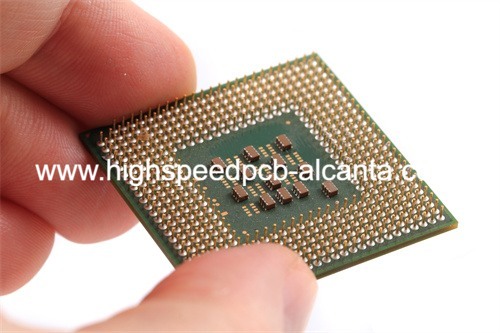
Ultra-Small Size FC-LGA Substrates Manufacturer
To achieve this high density and performance, ultra-small size FC-LGA substrates use advanced materials and manufacturing processes. Commonly used materials include high-temperature ceramics, polyimide and other high-performance materials, which have excellent electrical properties, high temperature resistance and mechanical strength. In terms of manufacturing process, advanced micro circuit board manufacturing technology is adopted, including laser drilling, film etching, precision drilling, etc., to ensure the accuracy and reliability of the circuit.
The emergence of ultra-small size FC-LGA substrate has brought new possibilities to the design and manufacturing of electronic products. It not only enables a more compact design, reducing the size and weight of electronic devices, but also improves the performance and functionality of the device. For example, in the fields of smartphones, wearable devices, medical devices and other fields, the application of ultra-small size FC-LGA substrates has become a mainstream trend in the industry, promoting technological innovation and product upgrades in these fields.
In short, ultra-small size FC-LGA substrate represents the development direction of PCB technology towards smaller and higher density. As the requirements for size and performance of electronic devices continue to increase, this substrate will play an increasingly important role in the future, opening up a broader space for the development of electronic products.
Ultra-small Size FC-LGA Substrates design Reference Guide.
Designing ultra-small size FC-LGA substrates is a complex and critical task, and designers need to consider multiple factors to ensure the performance and reliability of the final product. First, dimensional constraints are one of the important considerations in the design process. Since ultra-small size FC-LGA substrates are usually used in compactly designed electronic devices, designers must arrange all necessary electronic components within a limited space and ensure that the spacing between them is small enough to achieve high-density integration.
Secondly, signal integrity is an aspect that cannot be ignored during the design process. Designers need to consider issues such as the length of the signal transmission path, impedance matching, and crosstalk to ensure stable signal transmission on the substrate and avoid interference and distortion.
In addition, thermal management is also something that needs to be focused on during the design process. Since electronic components generate heat during operation, the compact design of ultra-small size FC-LGA substrates may lead to heat accumulation and difficulty in heat dissipation. Therefore, designers need to take effective thermal management measures, such as rational layout of radiators or heating ducts, to ensure stable operation of the substrate in high-temperature environments.
Finally, manufacturing feasibility is also an important factor to consider during the design process. Designers need to understand the limitations of the chosen materials and manufacturing processes to ensure smooth translation of designs into actual products. In addition, designers should also work closely with manufacturers to promptly solve problems that may arise during the manufacturing process to ensure the quality and reliability of the final product.
In summary, designing ultra-small size FC-LGA substrates requires designers to comprehensively consider size constraints, signal integrity, thermal management, and manufacturing feasibility to ensure that the final product can meet performance requirements and have good reliability . Only through careful design and careful debugging can the excellent performance and stable operation of ultra-small size FC-LGA substrate be achieved.
What material is used in Ultra-small Size FC-LGA Substrates?
The material selection of ultra-small size FC-LGA substrate is crucial and directly affects its performance in high-density and high-frequency applications. Typically, such substrates use high-performance materials, mainly including high-temperature ceramics, polyimide and metal substrates.
First of all, high-temperature ceramics are one of the commonly used substrates for ultra-small size FC-LGA substrates. High-temperature ceramics have excellent heat resistance and mechanical strength, allowing them to maintain stable performance in extreme working environments. Its low dielectric constant and low loss tangent make high-frequency signal transmission more reliable and help improve the signal integrity of the system.
Second, polyimide is also a common substrate material option. Polyimide has excellent high temperature resistance, chemical stability and mechanical properties, making it suitable for the manufacture of high-density circuits. Its low dielectric constant and low dielectric loss make it excellent in high-frequency applications, helping to reduce attenuation and distortion during signal transmission.
In addition, metal base substrates are also widely used in the manufacture of ultra-small size FC-LGA substrates. The metal base substrate has excellent heat dissipation performance and mechanical strength, which can effectively remove heat and maintain a stable operating temperature of electronic components. At the same time, the thermal conductivity of the metal base substrate also helps to improve the thermal management efficiency of the entire system and ensure the reliability and long-term stability of electronic components.
In general, the high-performance materials used in ultra-small size FC-LGA substrates, such as high-temperature ceramics, polyimide and metal substrates, not only have excellent electrical properties, thermal properties and mechanical strength, but also can meet their requirements in high-temperature applications. stringent requirements in density and high frequency applications. The selection of these materials provides a solid foundation for performance improvement and application expansion of ultra-small size FC-LGA substrates.
What size are Ultra-small Size FC-LGA Substrates?
The size of ultra-small FC-LGA substrates is crucial for modern electronic devices. These substrates are designed to achieve the smallest possible size to accommodate the trend of increasing shrinkage and high performance. Products such as smartphones, wearable devices, and medical devices require compact designs, and ultra-small size FC-LGA substrates are ideal for meeting this demand.
Mobile devices such as smartphones have extremely high size requirements. With the continuous advancement of technology, the components inside mobile phones are becoming more and more compact, and the emergence of ultra-small size FC-LGA substrates allows mobile phone designers to achieve more functions and stronger performance in a limited space. These substrates can be precisely customized in size and shape to fit the needs of various mobile phone designs, allowing for more flexible layouts and higher performance.
Wearable devices are another important application area, which often require small, lightweight and comfortable designs. The emergence of ultra-small size FC-LGA substrate enables wearable devices to achieve a more refined appearance and a more comfortable wearing experience without affecting its functionality and performance. The size of these substrates can be customized based on where the device is worn and the needs of the user, allowing for optimal design results.
In the field of medical devices, ultra-small size FC-LGA substrates also play an important role. Medical devices often need to feature compact designs and high performance to meet the requirements of clinical use. Ultra-small size FC-LGA substrate can realize precise control and data processing in medical equipment, thereby improving the functionality and reliability of the equipment, while reducing the overall volume and weight of the equipment, making it easy to carry and operate.
In short, the size design of ultra-small size FC-LGA substrate is crucial to meet the compactness and high-performance needs of modern electronic equipment. The flexible customization and high-performance characteristics of these substrates make them ideal for smartphones, wearable devices, medical devices and other fields, driving continuous innovation and development in these fields. As technology advances and demand continues to grow, ultra-small size FC-LGA substrates will play an increasingly important role in the future, bringing more possibilities and opportunities to the electronics industry.
The Manufacturer Process of Ultra-small Size FC-LGA Substrates.
The manufacturing of ultra-small size FC-LGA substrates is a complex and precise process that requires multiple key steps to ensure that the final product has high quality, high reliability and high performance.
The first is the substrate preparation stage. At this stage, the manufacturer selects an appropriate substrate material, usually a high-performance dielectric material such as FR-4 fiberglass reinforced epoxy, to ensure adequate mechanical strength and electrical performance. The substrate is then cut to the required size and surface treated for subsequent process steps.
Next comes layer alignment and formation of conductive paths. In this step, manufacturers precisely lay together the different layers of a multilayer substrate through a layer alignment process. Then, through processes such as chemical etching or photolithography, conductive paths, that is, lines on the circuit board, are formed on the surface of the substrate. This process requires high-precision equipment and process control to ensure the accuracy and stability of the line.
This is followed by drilling of component holes. In this step, manufacturers use a drilling machine to precisely drill holes into the substrate for mounting electronic components. The location and size of these holes must exactly match the design specifications to ensure a smooth subsequent assembly process.
Next comes the coating of solder film. Soldermask is a protective coating, usually a thermoset resin, used to cover conductive paths and component holes. The coating of solder film can be completed by printing, spraying or coating to protect the circuit board from environmental corrosion and mechanical damage.
Finally comes the assembly and testing of components. At this stage, electronic components are precisely mounted on the substrate and connected to conductive paths through soldering or other connections. The assembled circuit board is then subjected to rigorous functional testing and performance verification to ensure it meets design requirements and is highly reliable.
Overall, the manufacturing process of ultra-small size FC-LGA substrates requires a high degree of process precision and strict quality control to ensure that the quality and performance of the final product reaches the expected level. Manufacturers need to continuously optimize process processes and adopt advanced manufacturing technologies to meet changing market needs and customer requirements.
The Application area of Ultra-small Size FC-LGA Substrates.
The wide application of ultra-small size FC-LGA substrates in various fields demonstrates its important position in the modern electronics industry. First of all, consumer electronics is one of its main application areas. From smartphones and tablets to smart home devices and wearable devices, ultra-small size FC-LGA substrates are used in almost all modern consumer electronics products. The compact design of these substrates enables electronic devices to be thinner and lighter while maintaining high performance and feature richness, meeting consumer demands for portable and powerful devices.
Secondly, the automotive industry is also one of the important application areas for ultra-small size FC-LGA substrates. Modern cars are equipped with a large number of electronic control units (ECUs) for controlling engines, body electronic systems, safety systems, etc. The high performance and reliability of ultra-small size FC-LGA substrate make it an ideal choice for automotive electronic systems, helping to improve vehicle performance, safety and driving experience.
In the field of medical equipment, ultra-small size FC-LGA substrates also play an important role. Medical equipment has very high requirements for performance, reliability and accuracy, and ultra-small size FC-LGA substrates can meet these requirements. For example, this substrate is widely used in medical equipment such as medical imaging equipment, life monitoring instruments, and surgical auxiliary systems, providing medical staff with accurate and reliable data and operational support, helping to improve the efficiency and effectiveness of medical diagnosis and treatment.
The communications field is another important application field for ultra-small size FC-LGA substrates. With the promotion of 5G technology and the development of the Internet of Things, communication equipment has increasingly higher requirements for high-speed data transmission, low latency and large capacity. Ultra-small size FC-LGA substrate can meet these requirements and is widely used in various communication equipment such as communication base stations, routers, and optical fiber communication equipment to provide users with stable and fast communication services.
Finally, in the field of industrial automation, ultra-small size FC-LGA substrates also play an important role. Industrial automation systems require high performance, reliability and stability to ensure the normal operation of production lines and increase production efficiency. Ultra-small size FC-LGA substrates are widely used in various automation equipment such as industrial controllers, sensors, and machine vision systems, providing reliable control and monitoring support for industrial production.
Overall, ultra-small size FC-LGA substrates play an important role in various fields such as consumer electronics, automobiles, medical equipment, communications, and industrial automation. Their compact design and high performance make them indispensable in many electronic products. missing component. With the continuous advancement of technology and the continuous expansion of application fields, ultra-small size FC-LGA substrates will continue to play an important role and play an even more important role in the future electronics industry.
What are the advantages of Ultra-small Size FC-LGA Substrates?
Ultra-small size FC-LGA substrates exhibit unique advantages in modern electronic devices, making them an ideal choice to meet the needs of evolving electronic devices.
First, the compact size of the ultra-small FC-LGA substrate enables a high degree of integration within a limited space. In today’s electronic devices, space is often a precious and limited resource, and the small size design of ultra-small size FC-LGA substrate allows it to function in small devices such as smartphones, wearable devices, and medical devices. This compact design enables a lighter, more portable product while improving its appearance and ease of use.
Secondly, the ultra-small size FC-LGA substrate has the characteristics of high performance and high-density integration. Through advanced manufacturing processes and material technologies, ultra-small size FC-LGA substrates can achieve higher signal transmission rates and lower power consumption. This high-performance feature makes it perform well when handling complex computing tasks and multimedia applications. It also helps extend battery life and improve the overall performance and user experience of the device.
In addition, the ultra-small size FC-LGA substrate also has excellent signal integrity and thermal performance. Due to its compact design, the signal transmission path is shorter, which reduces the possibility of signal attenuation and interference and improves the stability and reliability of the system. At the same time, the optimized thermal management design ensures the stable operation of electronic components under high load conditions and avoids performance degradation or damage caused by overheating, thereby extending the service life of the equipment.
In general, ultra-small size FC-LGA substrate has become an ideal choice to meet the needs of modern electronic equipment due to its compact size, high performance, high-density integration, excellent signal integrity and thermal performance. With the continuous development and evolution of electronic equipment, ultra-small size FC-LGA substrates will continue to play an important role and show broader application prospects in various fields.
FAQ
What are the advantages of ultra-small size FC-LGA substrate compared to traditional PCB?
Ultra-small size FC-LGA substrates have higher integration density and more compact size than traditional PCBs, which means they can accommodate more electronic components in a limited space, thereby achieving more powerful functions. In addition, the design of the FC-LGA substrate uses micro-grid array technology, which can provide higher signal integrity and lower resistance and inductance, thus improving overall performance.
Is the manufacturing process of ultra-small size FC-LGA substrate complicated?
Manufacturing ultra-small size FC-LGA substrates requires the use of advanced manufacturing equipment and processes, so the manufacturing process may be more complex than traditional PCBs. The steps involved include precise layer alignment, micro-aperture drilling, high-precision solder film coating, and precise component assembly and testing. However, with the continuous advancement of manufacturing technology, these complex steps can be completed efficiently in modern manufacturing plants.
What applications are ultra-small size FC-LGA substrates suitable for?
Ultra-small size FC-LGA substrate is suitable for electronic devices that require high integration and compact design, such as smartphones, tablets, portable medical equipment, drones and wearable devices. Its small size and high performance make it a critical component in these devices, enabling more functionality and better performance.
How to choose the material of ultra-small size FC-LGA substrate?
Many factors need to be considered when selecting materials for ultra-small size FC-LGA substrates, including electrical properties, thermal properties, mechanical strength, processability and cost. Commonly used materials include high-temperature ceramics, polyimide and metal substrates, which have excellent performance and adaptability to meet the needs of different applications.
What are the design software for ultra-small size FC-LGA substrate?
Designing ultra-small size FC-LGA substrates usually requires the use of professional PCB design software, such as Altium Designer, Cadence Allegro, and Mentor Graphics PADS. These software provide a wealth of functions and tools to help designers implement complex layout and routing, and perform simulation and verification