Ultra-small Size BGA/IC Substrates Manufacturer.NanoTech Electronics is a leading Ultra-small Size BGA/IC Substrates Manufacturer, specializing in high-precision, miniaturized solutions for the semiconductor industry. Our advanced manufacturing techniques and cutting-edge technology ensure superior performance and reliability, catering to the evolving demands of modern electronics. Partner with NanoTech Electronics for innovative and efficient substrate solutions tailored to your needs.
In today’s electronic field, the emergence of ultra-small size BGA/IC substrates has become an important driving force for technological innovation and the development of miniaturized equipment. These substrates not only provide the compact connectivity platforms required for microelectronic devices, but also enable the implementation of advanced technologies. This article will deeply explore the design concept, manufacturing technology and wide application fields of ultra-small size BGA/IC substrates, and present the cutting-edge trends and future development trends in this field to readers.
What are Ultra-small Size BGA/IC Substrates?
BGA/IC substrate (Ball Grid Array/Integrated Circuit Substrates) is a flat plate made of non-conductive material, whose surface is covered with a dense grid arranged in spherical pads. These spherical pads are often called “Ball Grid Array” (BGA for short). They cover the bottom of the substrate in a high-density and evenly distributed manner and are used to connect integrated circuits (IC for short) and external circuit.
BGA/IC substrates play a vital role in the modern electronics industry. They provide a reliable platform for the installation and connection of integrated circuits, while achieving a high degree of integration and compact design of the circuit. Compared with traditional surface mount technology, BGA/IC substrates have significant advantages in connection density, reliability and performance, and therefore are widely used in various electronic devices and systems.
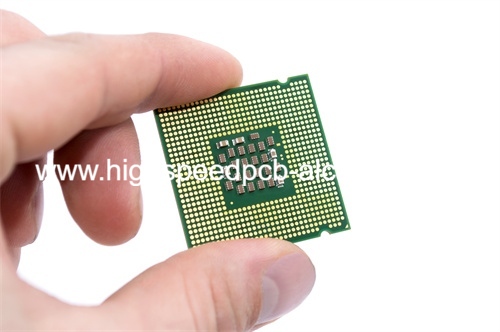
Ultra-Small Size BGA/IC Substrates Manufacturer
There are several key factors to consider in the design and manufacturing of BGA/IC substrates. The first is the choice of substrate material, which is typically fiberglass-reinforced epoxy (FR4) or other high-performance materials. The second is the design of the ball grid array, including the size, spacing and arrangement of the balls, which directly affects the connection density and signal transmission performance. In addition, factors such as substrate hierarchy, wire path design, and thermal and electromagnetic compatibility need to be considered.
BGA/IC substrates have a wide range of applications, covering many fields such as smartphones, tablets, wearable devices, automotive electronics, and industrial control systems. As electronic products develop towards miniaturization, high performance and multi-function, the demand for BGA/IC substrates is also increasing.
In general, BGA/IC substrates, as a key component of modern electronic equipment, provide important support for the realization of smaller, higher performance and more reliable electronic products. Through continuous technological innovation and process improvement, BGA/IC substrates will continue to play an important role in promoting the progress and development of the electronics industry.
Ultra-small Size BGA/IC Substrates design Reference Guide.
Ultra-small size BGA/IC substrates play an important role in the modern electronics field, and their design requires comprehensive consideration of multiple key factors to ensure the performance and reliability of the final product. The following is a reference guide when designing ultra-small size BGA/IC substrates:
Component layout optimization
During the design process, the layout of individual components needs to be carefully considered to minimize substrate size and ensure the shortest possible signal paths. Through reasonable component placement, signal delay and power consumption can be reduced, and system efficiency and performance can be improved.
Signal integrity
Maintaining good signal integrity is critical for ultra-small size BGA/IC substrates. Issues such as anti-interference ability, crosstalk and reflection of signal transmission should be considered in the design, and appropriate wiring and shielding measures should be taken to ensure stable and reliable signal transmission.
Thermal management
Since ultra-small size BGA/IC substrates usually integrate a large number of components and functions, thermal management is an aspect that must be considered during the design process. Reasonable heat dissipation design can effectively reduce the temperature and improve the reliability and life of the system.
Manufacturing feasibility
The feasibility of manufacturing needs to be fully considered during the design process, including substrate material selection, layer alignment, welding processes, etc. Reasonable design can reduce manufacturing costs and improve product production efficiency and quality.
Design tools and techniques
The use of advanced design tools and technologies can help designers better complete the design tasks of ultra-small size BGA/IC substrates. Tools such as CAD software, simulation tools, and automated routing technology can improve design efficiency and reduce errors and duplication of work.
By comprehensively considering the above factors, designers can better complete the design task of ultra-small size BGA/IC substrates and maximize their performance and potential. With the continuous advancement and innovation of technology, ultra-small size BGA/IC substrates will play an increasingly important role in future electronic products.
What material is used in Ultra-small Size BGA/IC Substrates?
Material selection for ultra-small size BGA/IC substrates is critical to their performance and reliability. In these high-density, miniaturized electronic devices, materials must have excellent electrical properties, mechanical strength, and thermal conductivity properties to ensure stable operation of the system. The following are materials commonly used for ultra-small size BGA/IC substrates:
Organic glass fiber composite material (FR4)
FR4 is a common substrate material with good insulation properties, mechanical strength and processability, and is suitable for most application scenarios. For ultra-small size BGA/IC substrates, choosing high-quality FR4 materials can ensure the stability and reliability of the substrate.
Polyimide (PI)
PI has excellent high temperature resistance and chemical stability, making it suitable for applications in high temperature environments, such as aerospace and automotive electronics. PI is an ideal choice for ultra-small size BGA/IC substrates that need to withstand extreme temperatures and environmental conditions.
Metal base material
Metal base materials such as aluminum substrates and copper substrates have excellent thermal conductivity, which can effectively improve the heat dissipation performance of the substrate and are suitable for applications with high heat dissipation requirements, such as LED lighting and power modules.
Ceramics
Ceramic substrates have good heat resistance and chemical stability and are suitable for applications in high-frequency and microwave electronic equipment. For ultra-small size BGA/IC substrates that require high-performance signal transmission and package sealing, ceramics are an option worth considering.
Flexible substrate materials
Flexible substrate materials such as polyamide film (PI) and polyester film (PET) have good flexibility and bendability and are suitable for applications in curved and flexible electronic devices. Flexible substrates are an ideal choice for ultra-small size BGA/IC substrates that require compact design and high flexibility.
When selecting materials, various factors need to be considered based on specific application scenarios and performance requirements, including electrical properties, mechanical properties, thermal properties, cost and manufacturability, etc. Through reasonable material selection, it can be ensured that ultra-small size BGA/IC substrates can achieve expected performance indicators in various application scenarios, promoting the continuous innovation and development of electronic technology.
What size are Ultra-small Size BGA/IC Substrates?
The size of ultra-small size BGA/IC substrates varies depending on what they are designed to do and the specific application, but generally have very compact dimensions. These substrates may be only a few millimeters on a side, or even smaller. Their size is primarily determined by the required circuit complexity, component density, and space constraints of the device in which they are located. In modern miniature electronic devices, such as smartphones, wearable devices and medical implants, there is an increasing demand for ultra-small size BGA/IC substrates.
With the development of technology, the ability to manufacture ultra-small size BGA/IC substrates is also constantly improving. Miniaturized manufacturing processes and advanced material technologies allow components and connections on the substrate to be laid out more compactly, allowing for smaller-sized designs. Despite shrinking sizes, these substrates still need to maintain a high degree of reliability and performance, which poses challenges to manufacturing processes and materials, but also presents tremendous opportunities for advancements in the electronics industry.
In general, the size of ultra-small size BGA/IC substrates may range from a few millimeters to several centimeters, depending on its specific design requirements and application scenarios. With the continuous advancement and innovation of technology, we can expect to see the emergence of more miniaturized and powerful BGA/IC substrates, bringing more possibilities to the development of electronic equipment.
The Manufacturer Process of Ultra-small Size BGA/IC Substrates.
The process of manufacturing ultra-small size BGA/IC substrates is a complex and precise process involving multiple critical steps, each of which plays a vital role in the quality and performance of the final product.
The first is substrate preparation. At the beginning of the manufacturing process, selecting the appropriate substrate material is critical. High-performance non-conductive materials such as fiberglass-reinforced epoxy (FR4) are typically used to ensure substrate stability and reliability. The substrate is then surface treated and cleaned to prepare it for subsequent manufacturing steps.
Next is layer alignment. For multi-layer BGA/IC substrates, alignment between different layers is critical. Precise layer alignment ensures that the conductive paths between different layers are correctly aligned, avoiding bad connections and short circuits in the circuit.
The shaping or printing of conductive paths is one of the key steps in the manufacturing process. This step makes connections between components by printing or forming conductive paths—metal wires or coils on the circuit board. This requires highly sophisticated equipment and processes to ensure the accuracy and stability of conductive paths.
Next comes the drilling of component holes. This step is used to drill holes into the substrate to accommodate pins or connectors for electronic components. The location and size of drilled holes must be precisely controlled to ensure proper installation and connection of components.
Pad coating is the next important step. The solder pad is a key part of connecting electronic components to the substrate, and is usually composed of solder paste or solder coating. In this step, solder pads are applied to the appropriate locations on the substrate in preparation for subsequent component mounting and soldering.
Component assembly is one of the key stages of the manufacturing process. In this step, electronic components are precisely mounted on a substrate, with their pins or connectors aligned with conductive paths, and connected to the substrate through soldering or other connections. Accurate installation of components is critical to the functionality and performance of the final product.
Finally, there is the testing phase. After component assembly is completed, the substrate will undergo a series of rigorous tests to verify that its functionality and performance meet requirements. These tests include electrical testing, signal integrity testing, temperature cycling testing, etc. to ensure the quality and reliability of the final product.
In general, manufacturing ultra-small size BGA/IC substrates is a process that requires highly specialized knowledge and technology, and each step has a direct impact on the quality and performance of the final product. Through precise manufacturing processes and strict quality control, the stability, reliability and excellent performance of ultra-small size BGA/IC substrates can be ensured.
The Application area of Ultra-small Size BGA/IC Substrates.
Ultra-small size BGA/IC substrate plays an indispensable role in today’s technology field. Its applications cover many fields and provide key connections and support for various micro electronic devices and systems. Among them, smartphones are one of the most widely used fields for ultra-small size BGA/IC substrates. These substrates are responsible for connecting the processor, memory, communication modules and various sensors in smartphones, achieving a high degree of integration and compact design of the device, providing users with powerful functions and a convenient user experience.
In addition to smartphones, wearable devices are also one of the important application areas for ultra-small size BGA/IC substrates. For example, devices such as smart watches, health monitors, and smart glasses use these substrates to achieve highly integrated functions while maintaining a lightweight and compact design, allowing users to carry them around and monitor health data or receive notifications in real time.
In the field of medical devices, the application of ultra-small size BGA/IC substrates is also increasing. For example, portable medical equipment, remote monitoring systems and medical imaging equipment require highly integrated electronic components to achieve accurate data collection, processing and transmission, and the design of ultra-small size BGA/IC substrates meets this demand. Bringing more innovation and convenience to the medical industry.
In the field of industrial automation, the application of ultra-small size BGA/IC substrates is also becoming increasingly popular. Equipment and systems such as industrial control systems, robotics, and sensor networks require highly reliable and high-performance electronic components to achieve precise control and monitoring. Ultra-small size BGA/IC substrates meet this demand and provide the basis for industrial automation. The development of the field has injected new vitality.
In short, the application of ultra-small size BGA/IC substrates is not limited to the above fields, but also involves many fields such as automotive electronics, aerospace, consumer electronics, etc. With the continuous advancement and innovation of technology, ultra-small size BGA/IC substrates will surely show their huge potential and value in more fields, making greater contributions to the development and progress of human society.
What are the advantages of Ultra-small Size BGA/IC Substrates?
Ultra-small size BGA/IC substrates have demonstrated obvious technical advantages in electronic equipment design, and these advantages make them the first choice for today’s electronic equipment design. Compared with traditional circuit connection methods, ultra-small size BGA/IC substrates have significant advantages in many aspects.
First, the ultra-small size BGA/IC substrate has a smaller size. Because BGA/IC substrates use a dense grid of spherical pads, they can achieve higher device integration and more compact designs than traditional connection methods, making the overall electronic device smaller and more suitable for use. Suitable for various space-constrained application scenarios.
Secondly, ultra-small size BGA/IC substrates have higher reliability. Improvements in welding connection methods and optimization of substrate materials enable ultra-small size BGA/IC substrates to maintain stable performance in harsh working environments, frequent vibrations or large temperature changes, greatly improving the reliability of electronic equipment. and durability.
In addition, ultra-small size BGA/IC substrates are easy to mass produce. The use of advanced manufacturing processes and automated production equipment can greatly improve production efficiency and product quality, thereby reducing manufacturing costs and meeting the needs of mass production.
In addition, due to the low assembly errors of ultra-small size BGA/IC substrates, precision control and automated assembly technology during the manufacturing process can reduce connection errors between components and improve product consistency and repeatability.
In addition, the ultra-small size BGA/IC substrate has good signal integrity. By optimizing the layout and signal path design, signal interference and crosstalk can be minimized, ensuring the stability and reliability of signal transmission, thereby improving the performance and work efficiency of electronic equipment.
Finally, the ultra-small size BGA/IC substrate has superior heat dissipation performance. Its dense layout and optimized heat dissipation design can effectively conduct heat away from electronic devices, keep the temperature of the system stable, and improve the efficiency and life of electronic equipment.
In summary, ultra-small size BGA/IC substrates have become the first choice for today’s electronic equipment design due to their many advantages such as small size, high reliability, easy mass production, low assembly errors, good signal integrity, and superior heat dissipation performance, promoting Continuous innovation and development of electronic technology.
FAQ
What are the differences between ultra-small size BGA/IC substrates and traditional substrates?
Ultra-small size BGA/IC substrates use a dense grid of spherical pads, which allow them to have a higher level of integration and a more compact design than traditional substrates. This makes them more suitable for space-constrained applications and provides better performance and reliability.
How to choose suitable materials to manufacture ultra-small size BGA/IC substrates?
Factors such as substrate performance requirements, environmental conditions and manufacturing costs need to be taken into consideration when selecting materials. Commonly used materials include FR4 fiberglass reinforced epoxy resin, polyimide, etc. Each material has its specific advantages and disadvantages and needs to be selected according to the specific situation.
How to deal with thermal management of ultra-small size BGA/IC substrates?
The compact design of ultra-small size BGA/IC substrates may cause heat dissipation difficulties, so effective thermal management measures are required. This includes the use of heat sinks, well-designed vents and optimized heat dissipation materials to ensure that the system maintains a stable temperature when operating under high loads.
What are the design software for ultra-small size BGA/IC substrates?
There are many professional PCB design software on the market to choose from, such as Altium Designer, Cadence Allegro, Mentor Graphics PADS, etc. These software provide a wealth of functions and tools to help engineers achieve efficient and accurate designs.
How to ensure the reliability of ultra-small size BGA/IC substrates?
Ensuring the reliability of ultra-small size BGA/IC substrates requires comprehensive consideration from design, manufacturing to testing. Reasonable design layout, high-quality material selection, precise manufacturing processes, and strict testing and verification are the keys to ensuring substrate quality and performance.