Ultra-Multilayer FC-LGA Substrates Manufacturer.As a leading RF SIP (System-in-Package) substrate manufacturer, we specialize in producing high-performance substrates for advanced RF applications. Our expertise ensures superior signal integrity, miniaturization, and thermal management, meeting the demands of modern wireless communication, IoT, and 5G technologies. Our state-of-the-art manufacturing processes and rigorous quality control guarantee reliable and efficient RF SIP substrates tailored to your specific needs.
Ultra-multilayer Flip Chip Land Grid Array (FC-LGA) substrates are advanced components crucial for modern electronic devices, particularly in high-performance computing and telecommunications. These substrates are designed to support complex and high-density interconnections necessary for flip chip packaging technology. Their multi-layer structure provides enhanced electrical performance, thermal management, and miniaturization, making them ideal for applications requiring high speed, high power, and high frequency.
What is an Ultra-Multilayer FC-LGA Substrate?
An ultra-multilayer FC-LGA substrate is a sophisticated type of printed circuit board (PCB) that forms the foundation for mounting flip chip ICs using Land Grid Array (LGA) technology. These substrates consist of multiple conductive and insulating layers, allowing for dense and complex routing of electrical signals and power distribution. The “ultra-multilayer” designation indicates a significant number of layers, typically more than ten, which are essential for accommodating the high interconnect density required by advanced semiconductor devices.
Ultra-Multilayer FC-LGA Substrate Design Reference Guide
Designing ultra-multilayer FC-LGA substrates involves several critical steps and considerations to ensure optimal performance and reliability.
Signal Integrity: Ensuring high signal integrity involves careful impedance matching, minimizing parasitic inductance and capacitance, and using differential signaling where applicable.
Thermal Management: Effective thermal management is achieved through the use of thermal vias, heat spreaders, and advanced cooling techniques to prevent overheating of critical components.
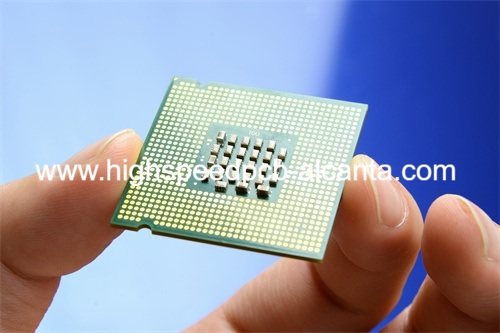
Ultra-Multilayer FC-LGA Substrates Manufacturer
Mechanical Stability: The substrate must provide robust mechanical support to withstand the stresses of assembly and operation, including thermal cycling and mechanical shock.
Reliability: The design must account for long-term reliability, ensuring that materials and construction methods prevent issues such as electromigration, delamination, and warping.
What Materials are Used in Ultra-Multilayer FC-LGA Substrates?
The materials used in FC-LGA substrates are selected to meet the demanding requirements of high-performance applications:
High-Performance Laminates: BT resin and ABF are commonly used due to their excellent electrical insulation properties and thermal stability.
Conductive Metals: Copper is the preferred choice for conductive traces and vias due to its high conductivity and reliability.
Substrate Core: FR-4, a glass-reinforced epoxy laminate, is often used for its balance of cost, mechanical strength, and electrical performance. For higher performance needs, ceramic cores may be used.
Dielectric Materials: Advanced dielectric materials with low loss tangent and high dielectric constant are used to support high-frequency signal transmission.
What Size are Ultra-Multilayer FC-LGA Substrates?
The size of ultra-multilayer FC-LGA substrates varies depending on the specific application and device requirements:
Thickness: The thickness of FC-LGA substrates can range from 0.1 mm to several millimeters, depending on the number of layers and the specific design requirements.
Length and Width: These dimensions are determined by the size of the chip and the layout of the interconnections. Typical sizes range from a few millimeters for small ICs to several centimeters for larger packages.
The Manufacturing Process of Ultra-Multilayer FC-LGA Substrates
The manufacturing process for FC-LGA substrates involves several precise and controlled steps to ensure high quality and performance:
High-performance laminates, conductive materials, and substrate cores are prepared and cut into appropriate sizes for processing.
Layers are fabricated by laminating conductive and insulating materials in a stack. Each layer is patterned using photolithography to define the circuitry.
Microvias and through-holes are drilled using laser or mechanical drilling techniques. These holes are then plated with copper to create electrical connections between layers.
Photolithography and etching processes are used to create fine-pitch circuitry on each layer. This step requires high precision to ensure accurate and reliable interconnections.
After layer fabrication, the layers are laminated together under heat and pressure. The assembled substrate undergoes rigorous testing, including electrical testing, thermal cycling, and mechanical stress tests, to ensure performance and reliability.
The Application Area of Ultra-Multilayer FC-LGA Substrates
Ultra-multilayer FC-LGA substrates are used in a variety of high-performance applications:
In servers, data centers, and supercomputers, FC-LGA substrates support powerful processors and memory modules, enabling fast data processing and storage.
These substrates are essential in telecommunications infrastructure, including base stations and network equipment, providing reliable and high-speed connectivity.
In smartphones, tablets, and other consumer devices, FC-LGA substrates enable compact and efficient integration of advanced ICs, enhancing performance and functionality.
In advanced driver assistance systems (ADAS) and in-vehicle infotainment systems, FC-LGA substrates provide the necessary reliability and performance for critical applications.
In medical imaging and diagnostic equipment, FC-LGA substrates support high-speed data acquisition and processing, improving accuracy and efficiency in medical procedures.
What are the Advantages of Ultra-Multilayer FC-LGA Substrates?
Ultra-multilayer FC-LGA substrates offer several advantages that make them indispensable for advanced electronic applications:
High Density: The multi-layer structure allows for high-density interconnections, enabling complex and compact designs.
Enhanced Performance: Optimized materials and design ensure high signal integrity, low power loss, and effective thermal management.
Miniaturization: The ability to integrate multiple functions into a single, compact package supports the trend towards miniaturization in electronic devices.
Reliability: Advanced manufacturing processes and materials provide high reliability, ensuring long-term performance in demanding environments.
Scalability: These substrates can be customized to meet the specific needs of various applications, from small consumer devices to large industrial systems.
FAQ
What are the key considerations in designing ultra-multilayer FC-LGA substrates?
Key considerations include material selection for electrical and thermal properties, layer structure optimization for signal integrity and thermal management, and ensuring mechanical stability and reliability.
How do ultra-multilayer FC-LGA substrates differ from standard PCBs?
Ultra-multilayer FC-LGA substrates have more layers, higher interconnect density, and are designed to handle higher frequencies and power levels compared to standard PCBs, making them suitable for advanced applications.
What is the typical manufacturing process for ultra-multilayer FC-LGA substrates?
The process involves material preparation, layer fabrication, drilling and plating, circuit patterning, assembly, and rigorous testing to ensure high performance and reliability.
What are the main applications of ultra-multilayer FC-LGA substrates?
These substrates are used in high-performance computing, telecommunications, consumer electronics, automotive electronics, and medical devices, providing advanced functionality and reliability in these fields.