Ultra-Multilayer FC-BGA Substrates Manufacturer.An industry-leading manufacturer specializing in Ultra-Multilayer FC-BGA Substrates, our company employs cutting-edge technology and stringent quality control measures to deliver exceptional products. With a focus on innovation and reliability, we craft substrates that meet the highest standards of performance and durability. Our state-of-the-art facilities and experienced team ensure precision engineering at every stage of production. Whether for telecommunications, automotive, or aerospace applications, our substrates provide the foundation for reliable electronic systems. Trust in our expertise and commitment to excellence for your most demanding substrate needs.
In today’s era of rapid technological development, printed circuit boards (PCBs) have become an indispensable core component of electronic equipment. As a new generation of printed circuit board technology, ultra-multilayer FC-BGA substrate is leading the development trend of the industry with its excellent performance and innovative design. Its highly integrated features and advanced ball grid array welding technology provide strong support for the performance improvement and function expansion of electronic equipment. With the continuous evolution of technology, ultra-multilayer FC-BGA substrates will play an increasingly important role in the electronic field.
What are Ultra-Multilayer FC-BGA Substrates?
Ultra-Multilayer FC-BGA Substrates represent the latest progress in printed circuit board technology. Its high degree of integration and advanced design provide a solid foundation for the performance improvement and innovation of electronic equipment. This substrate uses a special lamination design that stacks multiple layers of circuit boards together to form a complex and compact structure. Compared with traditional printed circuit boards, ultra-multilayer FC-BGA substrates have higher signal density and stronger electrical performance, making them ideal for a variety of high-performance electronic devices.
The core features of the ultra-multilayer FC-BGA substrate are its multi-layered structure and advanced ball grid array welding (BGA) technology. In this structure, multi-layer circuit boards are combined together in a special stacking method to form a three-dimensional circuit layout. This design not only maximizes the signal transmission efficiency of the circuit board, but also effectively reduces the length and complexity of circuit wiring, thereby reducing the occurrence of signal delay and crosstalk.
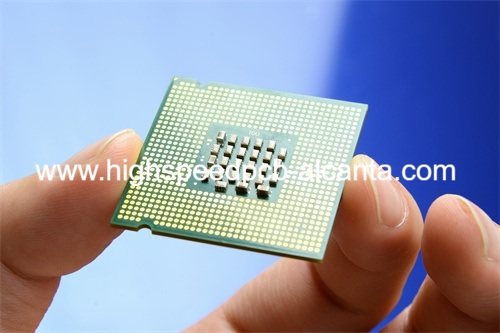
Ultra-Multilayer FC-BGA Substrates Manufacturer
In addition to the stacked design, the ultra-multilayer FC-BGA substrate also uses advanced BGA technology to connect components to the motherboard. BGA technology achieves a more reliable connection and more stable performance by soldering the components’ solder balls directly to the motherboard’s pads. Compared with traditional surface mount technology, BGA technology can provide higher soldering density and lower resistance, further improving the performance and reliability of the circuit board.
In general, ultra-multilayer FC-BGA substrate represents the latest development trend of printed circuit board technology. Its high degree of integration and advanced design provide new possibilities for the design and manufacturing of various high-performance electronic devices. With the continuous advancement and innovation of technology, it is believed that super multi-layer FC-BGA substrate will play an increasingly important role in the future electronic field, promoting the continuous progress and development of electronic equipment.
Ultra-Multilayer FC-BGA Substrates design Reference Guide.
As a highly integrated and advanced printed circuit board technology, the design process of ultra-multilayer FC-BGA substrate requires comprehensive consideration of many factors to ensure optimal performance and reliability. The following is a reference guide for ultra-multilayer FC-BGA substrate design to help engineers better understand and apply this technology.
When designing ultra-multilayer FC-BGA substrates, special attention must be paid to signal integrity to ensure that signals are not lost or interfered with during high-speed transmission. This involves correct wiring planning, reducing signal crosstalk, controlling the impedance matching of signal transmission lines, etc.
Ultra-multilayer FC-BGA substrates tend to generate a lot of heat in high-performance applications, so the heat dissipation system must be properly designed to ensure that components operate within a safe temperature range. This includes substrate material selection with excellent thermal conductivity, heat sink design, fan cooling and other measures.
Correct BGA arrangement can maximize PCB layout density and signal transmission efficiency. In the design of ultra-multilayer FC-BGA substrates, the location and number of BGAs should be reasonably planned to avoid wiring difficulties and signal crosstalk problems caused by overly dense layout.
The interlayer connection of ultra-multilayer FC-BGA substrate is one of the key design considerations. Proper inter-layer connection design can ensure the stability and reliability of signal transmission while minimizing wiring complexity and cost.
In the design of ultra-multilayer FC-BGA substrates, environmental protection and sustainability factors should be considered, and materials and processes that meet environmental standards should be selected to reduce the impact on the environment and extend the service life of the product.
Finally, manufacturing feasibility must be considered when designing ultra-multilayer FC-BGA substrates. The design should be consistent with existing manufacturing processes and equipment capabilities to ensure that the product can be successfully brought into volume production and maintain a consistent level of quality.
By comprehensively considering the above factors, engineers can design an ultra-multilayer FC-BGA substrate with excellent performance, reliability and stability, providing strong support and guarantee for various high-performance electronic devices.
What material is used in Ultra-Multilayer FC-BGA Substrates?
The performance and reliability of ultra-multilayer FC-BGA substrates depend on the materials selected, so material selection is crucial during the design and manufacturing process. The following are the key materials commonly used in ultra-multilayer FC-BGA substrates:
Substrate material: Ultra-multilayer FC-BGA substrates usually use high-performance substrate materials to ensure electrical performance and stability. Among them, polytetrafluoroethylene (PTFE) is a common substrate material with excellent high-frequency characteristics and low dielectric loss, making it suitable for high-speed data transmission and radio frequency applications. In addition, special ceramics are also widely used in ultra-multilayer FC-BGA substrates, which have good high-temperature resistance and dimensional stability and are suitable for applications in high-temperature environments.
Copper foil: Copper foil is the main material used for conductive layers in ultra-multilayer FC-BGA substrates. High-purity copper foil has excellent electrical conductivity and mechanical strength, enabling high-density wiring and stable signal transmission. By controlling the thickness and surface treatment of copper foil during the manufacturing process, more precise electrical performance and reliable soldering connections can be achieved.
Solder mask material: Solder mask material is used to cover the surface of printed circuit boards, protect circuit structures and provide protection. Common solder resist materials include epoxy resin, polyimide (PI) and polyvinyl alcohol (PVA), etc., which have excellent heat resistance, adhesion and mechanical strength, and can effectively prevent oxidation and damage to the circuit board surface. .
Solder: Solder is the key material for connecting components and circuit boards, affecting the quality and reliability of welding connections. In ultra-multilayer FC-BGA substrates, commonly used solders include lead-free solder, tin-lead alloy, etc., which have good soldering performance and thermal stability, and can achieve reliable soldering connections and excellent heat resistance.
By carefully selecting and optimizing these key materials, ultra-multilayer FC-BGA substrates can achieve higher performance and reliability, meet the needs of various complex electronic devices, and provide strong support for industry development and innovation.
What size are Ultra-Multilayer FC-BGA Substrates?
The size of ultra-multilayer FC-BGA substrates is diverse due to its wide range of applications. Generally speaking, their size can range from micro dimensions of a few millimeters to large panels of tens of centimeters. For large systems such as high-end communications equipment or computer servers, larger substrate sizes are often required to accommodate more electronic components and complex circuit designs. For small systems, such as portable devices or medical imaging equipment, smaller sized substrates may be required to meet volume and weight constraints.
The size of the ultra-multilayer FC-BGA substrate is not only limited by the size of the equipment, but also affected by the manufacturing process and technology. With the continuous advancement of printed circuit board manufacturing technology, the size of the substrate is becoming more and more miniaturized and compact. The application of fine line width, narrow spacing, high-density layout and multi-layer stacking technology makes it possible to accommodate more circuits and functions in the same size.
In addition, with the rise of flexible electronics technology, the size of ultra-multilayer FC-BGA substrates has become more flexible. The use of flexible substrates allows the substrates to be bent, folded or rolled to adapt to more complex and special application scenarios. This flexibility not only saves space, but also improves equipment reliability and durability.
In general, the size of ultra-multilayer FC-BGA substrate depends on many factors, including application requirements, manufacturing technology and design requirements. Whether it is a micro size or a large panel, ultra-multilayer FC-BGA substrates are constantly evolving and innovating, providing more possibilities and choices for the design and production of various types of electronic equipment.
The Manufacturer Process of Ultra-Multilayer FC-BGA Substrates.
The manufacturing process of ultra-multilayer FC-BGA substrate is a precise and complex process involving multiple key steps. Each step is crucial and directly affects the performance and quality of the final product.
The first is multi-layer stacking, which involves stacking multiple layers of pre-coppered substrates together. These layers can include internal signal, ground, and power layers, depending on the requirements and complexity of the design. Each layer must be precisely aligned to ensure proper connection in subsequent steps.
Next comes the internal interlayer connections, a critical step in establishing the electrical connections between the layers. Electrical connections are made between different layers for signal transmission and power distribution through techniques such as drilling and applying conductive paint.
Drilling is another critical manufacturing step used to create vias in the substrate to connect the component’s pins to different layers. These holes are usually very small and dense, requiring high-precision drilling equipment and control technology.
Copper foil etching is the process of removing unwanted copper foil from the surface of a substrate to form the desired circuit pattern. This step ensures the accuracy and stability of the circuit and provides a good foundation for subsequent soldering and assembly.
Solder mask coating is to apply a layer of solder mask material on the surface of the substrate to protect the circuit and pads from the external environment. Solder mask also helps reduce shorts and leakage between circuits and provides a surface for component mounting.
Finally, there is component mounting, which is the step of precisely mounting the electronic components onto the substrate. Modern manufacturing processes often use automated equipment and precise positioning techniques to ensure the correct location and secure connection of components.
Through advanced production technology and equipment, the manufacturing process of ultra-multilayer FC-BGA substrates has become efficient and precise. Strict quality control measures ensure product reliability and stability, making it ideal for a variety of high-performance electronic devices.
The Application area of Ultra-Multilayer FC-BGA Substrates.
Ultra-multilayer FC-BGA substrates are widely used in high-performance electronic equipment, such as communication equipment, computer servers, industrial automation systems, and medical imaging equipment. In the field of communication equipment, ultra-multilayer FC-BGA substrates are widely used in manufacturing base stations, routers, switches and optical fiber communication equipment to support high-speed data transmission and stable network connections. Its high-density layout and reliable electrical performance enable communication equipment to achieve continuous and stable operation in extreme environments, meeting the stringent requirements for speed and reliability of modern communication networks.
In the field of computer servers, ultra-multilayer FC-BGA substrates are widely used in manufacturing high-performance servers and data center equipment. These devices need to handle massive data streams and provide reliable computing and storage capabilities. The high degree of integration and excellent signal transmission performance of the ultra-multilayer FC-BGA substrate make it an ideal choice for building large-scale computing clusters and cloud computing platforms. They enable high-speed data exchange and collaborative work between servers, thereby improving data processing efficiency and the overall performance of the system.
In the field of industrial automation systems, ultra-multilayer FC-BGA substrates are widely used in control systems, sensors, industrial robots and other equipment. These devices require real-time data processing and precise control to ensure the stability and efficiency of the production process. The high-speed data transmission and low-latency characteristics of the ultra-multilayer FC-BGA substrate enable it to meet the strict real-time and reliability requirements of industrial automation systems, thus improving the automation level and production efficiency of the production line.
In the field of medical imaging equipment, ultra-multilayer FC-BGA substrates are widely used in manufacturing medical imaging equipment, such as CT scanners, MRI equipment, and ultrasound imaging systems. These devices need to process large amounts of imaging data and provide clear and accurate imaging results to assist doctors in diagnosis and treatment. The high-speed data transmission and low-noise characteristics of the ultra-multilayer FC-BGA substrate enable it to achieve high-resolution image acquisition and fast data processing, thus improving the imaging quality and diagnostic efficiency of medical imaging equipment.
In general, ultra-multilayer FC-BGA substrate plays a vital role in high-performance electronic equipment. Its excellent performance and reliability provide reliable support for the design and manufacturing of various complex circuits and high-speed data transmission systems. The foundation promotes the continuous innovation and progress of electronic technology.
What are the advantages of Ultra-Multilayer FC-BGA Substrates?
Ultra-multilayer FC-BGA substrates have many advantages over traditional printed circuit boards. These advantages are not only reflected in performance improvements, but also extend to the promotion of product innovation and development.
First of all, the ultra-multilayer FC-BGA substrate has a higher integration level. Through multi-layer stacking design, they can accommodate more electronic components and circuit functions in a limited space. This highly integrated design greatly reduces the size of the circuit board, allowing electronic devices to be more compact and lightweight, while improving the overall performance and functionality of the system.
Secondly, the ultra-multilayer FC-BGA substrate exhibits better electrical performance. Using advanced materials and manufacturing processes, these substrates have lower resistance, higher signal transmission rates and better signal integrity. This excellent electrical performance ensures the stable operation of electronic equipment in application scenarios such as high frequency and high-speed data transmission, thereby improving product reliability and performance.
Secondly, the super multi-layer FC-BGA substrate has stronger anti-interference ability. Due to more compact circuit layout, shorter signal transmission paths, and optimized designs of ground planes and power planes, these substrates can effectively reduce electromagnetic interference and signal crosstalk, improving the system’s anti-interference capability and electromagnetic compatibility.
Finally, the ultra-multilayer FC-BGA substrate has smaller size and weight. They are thinner and lighter than traditional printed circuit boards, making them suitable for a variety of space-constrained or weight-sensitive applications. This small size and lightweight design not only improves the portability of electronic products, but also helps reduce the cost and energy consumption of the overall system.
In general, the advantages of ultra-multilayer FC-BGA substrate in terms of integration, electrical performance, anti-interference ability, and size and weight enable it to meet the needs of increasingly complex and diversified electronic equipment, and contribute to product performance improvement and innovation. A solid foundation was laid. With the continuous advancement and innovation of technology, super multi-layer FC-BGA substrate will surely play a more important role in the future electronics industry and promote the continued development and progress of electronic products.
FAQ
What are the advantages of ultra-multilayer FC-BGA substrate compared to traditional printed circuit boards?
The ultra-multilayer FC-BGA substrate has a higher integration level and can realize more complex circuit designs. Its excellent electrical performance and anti-interference ability make it perform better in high-frequency and high-speed data transmission environments. In addition, the advanced materials and manufacturing processes used make it smaller in size and weight, making it more suitable for lightweight and compact equipment applications.
How to ensure the reliability and stability of ultra-multilayer FC-BGA substrate?
The key to ensuring reliability and stability lies in strict quality control and manufacturing process management. The manufacturing process of ultra-multilayer FC-BGA substrates needs to follow strict standards and specifications, including material selection, stacking design, welding processes and component installation. In addition, strict quality inspection and testing are also important means to ensure product reliability.
In which industries and applications are ultra-multilayer FC-BGA substrates widely used?
Ultra-multilayer FC-BGA substrate is widely used in communications, computers, industrial control, medical imaging and other fields. They play an important role in high-performance servers, network equipment, automated control systems, medical diagnostic equipment, etc., providing reliable support and connections for various complex electronic systems.
What is the future development direction of ultra-multilayer FC-BGA substrate technology?
In the future, ultra-multilayer FC-BGA substrate technology will continue to develop in the direction of high integration, high density, high-speed transmission and multi-functionality. With the continuous emergence of new materials, new processes and new technologies, super multi-layer FC-BGA substrates will continue to innovate and make breakthroughs, playing an important role in a wider range of application fields.