Ultra High Density Wiring Substrates Manufacturer.An Ultra High Density Wiring Substrates Manufacturer specializes in producing advanced circuit boards with exceptionally dense wiring. These substrates are crucial for high-performance electronic devices, enabling faster data transmission, improved miniaturization, and enhanced reliability. The manufacturer employs cutting-edge technology and precision engineering to meet the demanding requirements of industries such as telecommunications, computing, and medical devices, ensuring top-notch quality and innovation in every product.
Ultra High Density Wiring Substrates are a vital component of modern electronic devices. They are not only carriers of electronic components, but also bear key functions of electrical connection and signal transmission. This article will delve into the definition of ultra-high-density wiring substrates, their manufacturing processes, and their wide range of applications in various industries. By understanding the characteristics and advantages of ultra-high-density wiring substrates, we can better understand and apply this key technology and promote the development of the modern electronics industry.
What are Ultra High Density Wiring Substrates?
Ultra-high-density wiring substrates are key components in today’s electronic devices and play a vital role in modern technology. This type of printed circuit board (PCB) has an extremely high circuit density, which is characterized by extremely small circuit spacing and can accommodate more electronic components. Through advanced manufacturing technologies, such as micro-line processing and multi-layer stacking, ultra-high-density wiring substrates achieve a high degree of integration and excellent performance.
First of all, ultra-high-density wiring substrates use micro-circuit processing technology to minimize the line spacing. This means that more and denser electronic components can be accommodated in a limited space, thereby achieving a high degree of circuit integration. Micro circuit processing technology relies on advanced manufacturing equipment and precise processing technology to achieve sub-micron level circuit accuracy and ensure the stability and reliability of the circuit.
Secondly, ultra-high-density wiring substrates usually adopt multi-layer stack structures. By stacking multiple thin layers together and making electrical connections through internal connections, more circuit layers are achieved in a limited space. This multi-layer stacked structure not only increases circuit density, but also helps reduce circuit noise and crosstalk, and improves circuit signal integrity and performance stability.
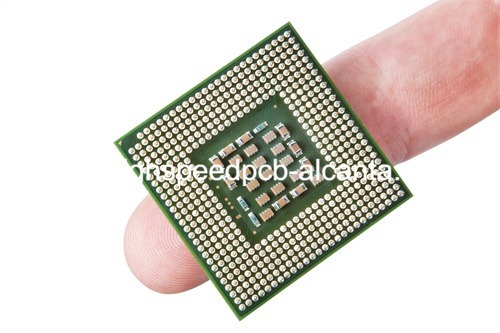
Ultra High Density Wiring Substrates Manufacturer
To sum up, the emergence of ultra-high-density wiring substrates has brought revolutionary changes to modern electronic technology. It not only plays an important role in the fields of communications, computers and consumer electronics, but also promotes the development and application of new generation electronic devices. With the continuous advancement and innovation of manufacturing technology, ultra-high-density wiring substrates will continue to play an important role, injecting new vitality and power into the development of the electronics industry.
Ultra High Density Wiring Substrates design Reference Guide.
The Ultra-High Density Wiring Substrate Design Reference Guide is an important reference resource for engineers when designing wiring substrates. During the design process, many factors need to be considered to ensure that the final product has excellent performance and reliability. Here are some key principles and best practices to help engineers effectively design ultra-high-density wiring substrates:
Line layout
In the design of wiring substrate, reasonable circuit layout is crucial. Engineers should consider factors such as signal transmission path, length, and mutual interference to minimize signal noise and delay. By optimizing routing paths and reducing line lengths, signal integrity and interference immunity can be improved.
Signal integrity
Signal integrity is one of the important considerations in the design of ultra-high-density wiring substrates. Engineers need to pay attention to issues such as signal transmission speed, waveform quality, and crosstalk to ensure that signals are not lost or distorted during the wiring process. Using appropriate signal extraction and terminal matching technology can effectively improve signal stability and reliability.
Thermal management
Ultra-high-density wiring substrates often generate large amounts of heat in high-performance applications. Therefore, effective thermal management is an important consideration in the design process. Engineers should rationally arrange device layout, select appropriate heat dissipation materials, and design heat dissipation structures to ensure that the wiring substrate can maintain a stable operating temperature during high load operation.
Material selection
In ultra-high-density wiring substrate design, material selection is crucial. Engineers should select appropriate substrate materials, conductive layer materials, and cladding materials based on application needs and performance requirements. High-performance materials can provide good electrical properties, mechanical strength and high temperature resistance, ensuring excellent performance and reliability of wiring substrates.
Environmental adaptability
Ultra-high-density wiring substrates are commonly used in a variety of harsh application environments, such as industrial control, aerospace, and medical equipment. Therefore, the environmental adaptability of the wiring substrate needs to be taken into consideration during the design process to ensure that it can operate stably under different working conditions and have long-term reliability.
By following the above principles and practices, engineers can effectively design ultra-high-density wiring substrates with excellent performance, reliability and stability to meet the needs of various application fields. Continuous practice and experience accumulation will also help engineers continuously improve and optimize the performance and reliability of wiring substrates during the design process.
What material is used in Ultra High Density Wiring Substrates?
Ultra High Density Wiring Substrates (Ultra High Density Wiring Substrates) are the core components of modern electronic devices, and their material selection is crucial. Typically, ultra-high-density wiring substrates use a range of high-performance materials to meet various demanding application environments and design requirements.
First of all, a material commonly used in ultra-high-density wiring substrates is FR-4 (Flame Retardant 4). FR-4 is a glass fiber reinforced epoxy resin material with good mechanical strength and heat resistance, suitable for the manufacture of most conventional electronic equipment. Its advantages include corrosion resistance, insulation and cost-effectiveness, making it one of the widely used standard substrate materials.
Secondly, polyimide (PI) is also one of the common choices for ultra-high-density wiring substrates. Polyimide has excellent high temperature resistance and chemical stability, making it suitable for manufacturing electronic devices in high temperature environments and extreme working conditions. Its excellent mechanical properties and dimensional stability make it the material of choice for some special applications, such as aerospace and automotive electronics.
In addition, polyetherketone (PEEK) is also widely used in the manufacture of ultra-high-density wiring substrates. PEEK has excellent high temperature resistance, chemical stability and mechanical strength, and can be used in applications requiring high performance and durability. It also has low water absorption and excellent electrical insulation properties, making it suitable for electronic equipment in environments with humidity and chemicals.
In addition to substrate materials, the conductive layer of ultra-high-density wiring substrates usually uses highly conductive metal materials, such as copper or silver. These metal materials have good electrical conductivity and welding properties, which can ensure the stability and reliability of the circuit. They are often applied to the surface of the substrate through methods such as electroplating to form conductive paths and connection points to achieve signal transmission and electrical connections between electronic components.
In general, the materials used in ultra-high-density wiring substrates have excellent mechanical properties, high temperature resistance and chemical stability, and are suitable for various harsh application environments. The selection and application of these materials provide key support for the design and manufacturing of modern electronic devices and promote the continuous progress and innovation of electronic technology.
What size are Ultra High Density Wiring Substrates?
The size of ultra-high-density wiring substrates is critical to the performance and functionality of electronic devices. Typically, these wiring substrates have smaller sizes and thicknesses to meet the compactness and high integration requirements of modern electronic devices. Compared with traditional PCBs, ultra-high-density wiring substrates can accommodate more lines and components, allowing for more complex circuit designs and functions. Its size usually ranges from a few square centimeters to tens of square centimeters, and its thickness can range from tens of microns to several millimeters.
This small size and thin design enable ultra-high-density wiring substrates to be widely used in microelectronic devices. For example, consumer electronics products such as smartphones, tablets, and wearable devices require highly integrated circuit boards to achieve more functions in a limited space. The compact design of ultra-high-density wiring substrates allows these devices to be lighter and more portable while delivering greater performance and functionality.
In addition to consumer electronics, ultra-high-density wiring substrates are widely used in high-performance systems. For example, computer servers, network equipment, industrial automation systems and other fields need to process large amounts of data and complex computing tasks, so circuit boards with high integration and high-speed signal transmission capabilities are needed. The small size and high level of integration of ultra-high-density wiring substrates make them ideal for these systems, enabling higher performance and lower energy consumption.
In short, the size design of ultra-high-density wiring substrates fully takes into account the compactness, high integration and performance requirements of modern electronic equipment. They not only play an important role in consumer electronics products, but also play a key role in various high-performance systems, driving the continuous progress and innovation of electronic technology.
The Manufacturer Process of Ultra High Density Wiring Substrates.
The manufacturing of ultra-high-density wiring substrates is a complex and precise process that requires multiple processes to achieve high-precision and high-quality production.
Multi-layer stacking
First, the manufacturing process begins with a multi-layer stack. This means layering multiple substrate layers together to form an overall structure. Each layer of substrate may contain circuit patterns and conductive layers. The connections between these layers are made through holes (vias), allowing electrical current and signals to travel between the different layers.
Line graphics
Next is line graphics. This step involves printing or fabricating a circuit pattern onto a specific layer on the surface of the substrate. Using photolithography and chemical etching methods, the unnecessary parts are removed, leaving the required conductive lines and connection points.
Chemical etching
During the chemical etching process, a layer of photosensitizer (photoresist) is coated on the surface of the circuit-patterned substrate, and then photolithography technology is used to expose the photosensitizer to form a photolithography pattern. The substrate is then immersed in a chemical solution, which erodes away the parts not protected by the photosensitizer, creating the desired circuit pattern.
Surface treatment
Finally, there is the surface treatment. In this step, the manufactured circuit pattern is protected and processed. This may include applying protective overlays to prevent oxidation and corrosion, as well as adding solder paste or metal overlays to connection points for subsequent assembly and connection.
Manufacturing technology and equipment
The manufacturing of ultra-high-density wiring substrates relies on advanced technology and equipment. High-precision photolithography equipment, chemical processing equipment and automated production lines all play a key role. These devices are capable of achieving micron-level precision and ensure the production of wiring substrates with stable performance and reliable quality.
Through the above manufacturing process, ultra-high-density wiring substrates can achieve the high degree of complexity and integration required for their design. These substrates are widely used in high-end electronic products, such as communication equipment, computer servers, medical diagnostic instruments, etc., providing solid support for the development of modern technology.
The Application area of Ultra High Density Wiring Substrates.
Ultra High Density Wiring Substrates play a key role in today’s various industries. Their wide range of applications cover communications, computers, medical and military fields, providing key support for performance improvement and functional innovation of modern electronic equipment.
In the field of communications, ultra-high-density wiring substrates are widely used in various communications equipment, such as base stations, routers, switches, etc. These devices need to support high-speed data transmission and complex signal processing, and ultra-high-density wiring substrates provide compact circuit layout and efficient signal transmission, helping to achieve fast, stable and reliable operation of communication networks.
In the computer field, ultra-high-density wiring substrates are used to manufacture high-performance computer systems, such as servers, workstations, and supercomputers. These systems need to process large amounts of data and complex computing tasks, and ultra-high-density wiring substrates can support complex circuit design and high-density integration, providing key support for performance improvement and functional expansion of computer systems.
In the medical field, ultra-high-density wiring substrates are used in various medical equipment, such as medical imaging equipment, monitoring instruments, and implantable medical devices. These devices require highly reliable and precise electronic control systems, and ultra-high-density wiring substrates can achieve complex circuit design and high-precision signal processing, helping to improve the diagnosis and treatment effects of medical equipment.
In the military field, ultra-high-density wiring substrates are used to manufacture various military electronic equipment, such as radar systems, navigation equipment, and communication equipment. These devices need to work in harsh environments and have a high degree of anti-interference and reliability, and ultra-high-density wiring substrates can meet the strict requirements for performance and reliability of military equipment, providing key support for military applications.
In general, the application of ultra-high-density wiring substrates covers various key areas, providing key support for the performance improvement and functional innovation of modern electronic equipment. With the continuous advancement of technology and the continuous expansion of applications, ultra-high-density wiring substrates will continue to play an important role in promoting the continuous development and innovation of electronic technology.
What are the advantages of Ultra High Density Wiring Substrates?
Ultra High Density Wiring Substrates have obvious advantages in the design and manufacturing of modern electronic devices. These advantages are not only reflected in performance improvement, but also promote the continuous advancement of technology. The following are the main advantages of ultra-high density wiring substrates:
Higher integration
Traditional wiring methods are limited by space and circuit density, while ultra-high-density wiring substrates achieve higher circuit density and component integration through micro-circuit processing and multi-layer stacking technology. This makes it possible to accommodate more functions and components in a limited space, thereby bringing greater flexibility and innovation to the design of electronic devices.
Lower circuit losses
Ultra-high-density wiring substrates use advanced materials and manufacturing processes to reduce circuit transmission losses and signal attenuation. By optimizing the line layout and reducing the signal path length, the energy loss during signal transmission can be reduced and the efficiency and performance of the circuit can be improved.
Better anti-interference performance
In circuits with high-density wiring, interference and crosstalk between signals are common problems. The ultra-high-density wiring substrate effectively reduces the effects of signal interference and crosstalk through precise design and shielding measures, and improves the anti-interference ability and stability of the circuit. This is particularly important for high-frequency, high-rate data transmission applications to ensure signal accuracy and reliability.
The advantages of ultra-high-density wiring substrates are not only reflected in performance, but also promote the continuous advancement of electronic device technology. They provide new possibilities for the design and manufacturing of electronic devices and promote innovation and development of electronic technology. With the continuous advancement of manufacturing processes and material technologies, ultra-high-density wiring substrates will continue to play an important role in promoting the development of electronic devices towards higher performance, higher integration, and wider application fields.
FAQ
What is the difference between ultra-high-density wiring substrate and traditional PCB?
Traditional printed circuit boards (PCBs) typically have lower circuit density and larger sizes, while ultra-high-density wiring substrates use advanced manufacturing technology to achieve higher circuit density and smaller sizes. This allows ultra-high-density wiring substrates to accommodate more electronic components and support more complex circuit designs.
Is the manufacturing process of ultra-high-density wiring substrate complicated?
Yes, the manufacturing process of ultra-high-density wiring substrates requires highly precise equipment and process control. Multi-layer stacking, micro-circuit processing and precise chemical etching are critical steps in the manufacturing process, requiring experienced technicians and advanced production equipment.
What application fields are ultra-high-density wiring substrates suitable for?
Ultra-high density wiring substrates are widely used in communications, computers, medical and military fields. They support high-speed data transmission, complex circuit design and high-density integration, and are suitable for application scenarios with high requirements on circuit performance and space constraints.
What are the main advantages of ultra-high density wiring substrates?
Ultra-high-density wiring substrates have many advantages over traditional wiring methods, including higher integration, lower circuit losses and better anti-interference performance. In addition, they can achieve compact layout and higher performance density of devices, providing greater flexibility and innovation space for the design of electronic products.