Top 10 Packaging Substrate Firm, Substrate production company has more than 10,000 employees, a professional engineer team of more than 100 people, advanced production equipment and process.
Package substrate is a critical element within the electronics industry, serving as a pivotal component in connecting and supporting electronic elements. It offers robust structural support and facilitates efficient connections for circuits. Typically crafted from insulating materials, package substrates feature a composite multi-layered construction capable of accommodating and bolstering various electronic components.
In contemporary electronic devices, package substrates are tasked with amalgamating diverse electronic components and establishing electrical connections. These substrates, akin to circuit boards, are notably smaller and thinner than their traditional counterparts, rendering them ideal for high-density circuit designs and applications with space constraints.
Package substrates in semiconductor manufacturing commonly utilize polymer materials known for their outstanding insulation properties, such as glass fiber reinforced polyimide (FR-4) and polyimide (PI). These materials offer excellent electrical insulation characteristics and can endure high temperatures and pressures, thereby ensuring the stability and reliability of electronic devices.
This multi-layered architecture enhances the flexibility and reliability of electronic component connections while simultaneously enhancing circuit integration and performance.
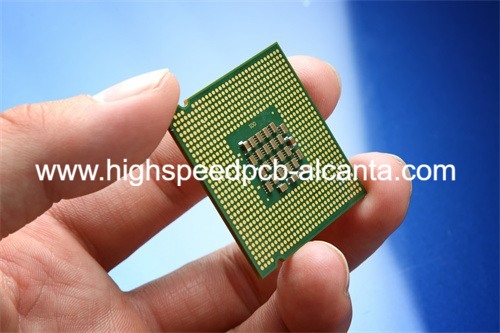
Top 10 Packaging Substrate Manufacturer
In essence, package substrates represent an indispensable component within the electronics industry, bearing the crucial responsibility of connecting and supporting electronic elements and furnishing a sturdy foundation for the stable operation of modern electronic equipment. Their multi-layered structure, superior materials, and precision manufacturing techniques collectively underpin their pivotal role in the production of high-performance, miniaturized electronic products.
What types of Package Substrate are there?
In the modern electronics industry, Package Substrate serves as a key component, carrying electronic components and providing connections and support. Top packaging substrate manufacturers provide the market with multiple types of Package Substrate to meet the needs of different application scenarios. Here are a few common types:
HDI boards are sophisticated, dense, multi-layered package substrates employed in compact electronic gadgets like smartphones, tablets, and laptops. They achieve increased circuit density and reduced dimensions by incorporating micro-traces, blind vias, and buried vias technologies.
Rigid-flex boards are package substrates that blend rigid and flexible materials, enabling them to flex and fold in three-dimensional space. This suppleness renders them suitable for applications with restricted space, such as automotive electronics and aerospace systems, meeting stringent layout and reliability criteria.
Aluminum substrates are package substrates crafted from aluminum-based materials, renowned for their superb heat dissipation characteristics and thermal conductivity. They are extensively utilized in electronic devices necessitating effective heat dissipation, such as LED lighting and automotive electronics, thereby enhancing product stability and reliability.
Each type of package substrate offers distinct advantages tailored to specific application needs. Top manufacturers continually innovate and advance these substrates, delivering high-quality, high-performance solutions to drive electronic product development and innovation.
What are the advantages of Package Substrate?
In the modern electronics industry, Package Substrate has significant advantages over traditional circuit boards. These advantages make it the first choice for the design of many electronic products. The following are several major advantages of Package Substrate over traditional circuit boards:
HDI (High-Density Interconnect) boards represent sophisticated, multi-layered substrates deployed in compact electronic gadgets like smartphones, tablets, and laptops. These boards achieve heightened circuit density and reduced dimensions by incorporating cutting-edge technologies like micro-lines, blind vias, and buried vias.
Rigid-flex boards serve as package substrates that seamlessly integrate rigid and flexible materials, allowing them to flex and fold in three-dimensional space. This adaptability makes them ideal for applications with spatial limitations, such as automotive electronics and aerospace systems, while adhering to stringent layout and reliability standards.
Aluminum substrates are package substrates crafted from materials based on aluminum, renowned for their exceptional heat dissipation properties and thermal conductivity. Widely employed in electronic devices necessitating efficient heat dissipation, such as LED lighting and automotive electronics, these substrates enhance product stability and reliability.
Because Package Substrate can achieve higher integration, more compact designs, and more efficient production processes, it often has a lower cost than traditional circuit boards. This means higher production efficiency and lower manufacturing costs for enterprises, which can improve product competitiveness and reduce market prices.
To sum up, Package Substrate has many advantages over traditional circuit boards, including higher integration, better signal integrity, smaller size and lower cost. These advantages make Package Substrate very popular in modern electronic product design and widely used in various application scenarios.
What is the process of manufacturing Package Substrate?
The following are the main steps in making a Package Substrate:
Design: This stage includes determining the layout, hierarchy, and design of signal and power paths of the Package Substrate. The design team will formulate corresponding plans based on customer needs and application scenarios to ensure that the product meets functional and performance requirements.
Material Selection: Select appropriate substrate materials, conductor materials and other auxiliary materials based on design requirements and product performance. Top manufacturers advise customers on the best material selection based on their extensive experience and expertise.
Molding: In this phase, the chosen material undergoes manipulation into the intended form and dimensions. This could entail cutting, shaping, pressing, and other techniques to ensure the substrate conforms to design specifications and possesses the necessary mechanical resilience and longevity.
Printing: In the manufacturing process of Package Substrate, printing techniques are extensively employed to incorporate conductor designs, branding elements, and additional functional layers. This may entail various printing methodologies such as silk-screen printing, digital printing, etc. to achieve precise and efficient production.
Printing: During the manufacturing process of Package Substrate, printing technology is widely used to add conductor patterns, logos and other functional layers. This may involve different printing technologies such as screen printing, inkjet printing, etc. to achieve high-precision and efficient manufacturing.
Assembly: The process of installing electronic components and other components onto Package Substrate. This may include both manual and automated assembly to ensure components are connected correctly and meet design requirements.
Testing: Following the completion of manufacturing, Package Substrates undergo comprehensive testing and validation procedures to verify adherence to quality and performance benchmarks. This encompasses electrical, reliability, and environmental testing, among other methodologies, to ascertain product reliability and stability.
Leading manufacturers employ cutting-edge technology and stringent quality control protocols throughout the Package Substrate manufacturing process to uphold superior product quality and consistency. They continually refine production techniques, enhance manufacturing efficiency, and deliver high-performance, highly reliable Package Substrate solutions to customers.
In what fields is Package Substrate applied?
Package substrate, as a critical electronic substrate, finds extensive usage across numerous sectors such as communications, computing, medical, automotive, and beyond. Diverse requirements and application scenarios within these domains necessitate top-tier package substrates to facilitate the connection and support of various electronic components, ensuring optimal device functionality and performance enhancement.
In the field of communications, Package Substrate plays a vital role. From mobile phones to base station equipment to communication infrastructure, high-performance Package Substrate is required to support circuit design and data transmission. In high-frequency communications and wireless network equipment, the requirements for signal integrity and high-density layout are particularly prominent, and the application of Package Substrate can effectively meet these requirements.
In the realm of computing, Package Substrate stands as an integral component. Whether in personal computers, servers, or the vast infrastructure of cloud computing and data centers, stability and reliability in electronic components and connections are paramount. Leveraging high-density layouts and multi-layer structures, Package Substrate facilitates the optimization of circuit designs, thereby enhancing performance and efficiency across computing systems.
In the medical field, Package Substrate is also increasingly used. From medical equipment control systems to medical image processing to remote monitoring and diagnostic equipment, stable and reliable electronic components and connections are needed to support the normal operation of medical equipment. Package Substrate’s high performance and reliability can meet the medical industry’s requirements for device stability and data accuracy.
In the automotive sector, there is a significant surge in the adoption of Package Substrate. This expansion spans various applications, ranging from in-car entertainment systems to vehicle control units, and from autonomous driving to intelligent transportation systems. The increasing need for high-performance electronic components and robust connections is being driven by the desire to enhance vehicle intelligence and automation. Package Substrate’s attributes, including high temperature tolerance and resistance to vibrations, closely align with the automotive industry’s stringent requirements for in-vehicle electronic equipment.
Broadly speaking, Package Substrate, as a vital component of the modern electronics industry, assumes a pivotal role across diverse fields such as communications, computers, healthcare, and automobiles. It contributes significantly to the advancement and progress of modern technology. With the continual evolution of technology and the expanding range of applications, the outlook for Package Substrate appears increasingly promising, with potential for even broader applications in the future.
How to get Package Substrate?
Securing access to premium Package Substrate entails forging partnerships with leading packaging substrate manufacturers in the industry. As a supplier committed to fulfilling our clients’ needs, we prioritize delivering bespoke solutions that align with their specific requirements, while upholding the highest standards of product excellence and service caliber.
Teaming up with top-notch packaging substrate manufacturers necessitates collaboration with seasoned professionals who possess cutting-edge technology and sterling reputations. These manufacturers operate sophisticated production facilities, backed by adept technical teams, and provide a diverse range of offerings, including personalized options tailored to individual customer demands.
Acknowledging the distinctiveness of each customer’s demands, premier manufacturers are committed to delivering personalized solutions that address specific industry requirements, product design complexities, and scalability needs in production. Utilizing their expertise, they provide optimal recommendations and solutions tailored to the unique circumstances of each client.
Through partnerships with leading manufacturers, customers can anticipate superior Package Substrate offerings and outstanding post-sales support. These manufacturers adhere to rigorous quality management processes, conducting comprehensive quality control checks and extensive testing to meet global standards and satisfy customer specifications. Furthermore, they offer prompt and efficient technical support and after-sales assistance to resolve any issues encountered during product usage.
Partnering with leading manufacturers not only ensures access to premium goods and services but also delivers cost advantages. Leveraging economies of scale and streamlining the supply chain, manufacturers provide competitive pricing, allowing clients to minimize procurement costs and enhance market competitiveness.
Opting to collaborate with premier packaging substrate manufacturers constitutes a pivotal stride towards securing high-caliber Package Substrate. As a supplier, our unwavering commitment entails furnishing clients with superior bespoke solutions, surpassing expectations in product quality and service delivery. Embrace collaboration with us to harness cost-effective products propelling your business towards success.
What factors affect the quotation of Package Substrate?
When selecting an appropriate Package Substrate, the pricing it commands holds significant sway for businesses and manufacturers. The cost of the Package Substrate not only mirrors the expenses incurred in production but also has a direct impact on a company’s bottom line and its ability to stay competitive in the market. Hence, it’s essential to grasp the elements that sway Package Substrate pricing.
One of the major costs of Package Substrate is the cost of materials. The costs of different materials vary greatly, and prices fluctuate greatly when market supply and demand change. For example, some high-performance specialty materials may be expensive, while ordinary materials are relatively cheap. Therefore, choosing the right material type is crucial to controlling costs.
The design complexity of Package Substrate directly affects the difficulty and cost of manufacturing. Complex designs often require more steps and precision machining techniques, thus increasing manufacturing costs. For example, if the design involves complex elements such as multi-layer wiring, fine line width and line spacing, blind and buried vias, then its manufacturing cost will be relatively high.
Production scale is a significant determinant in Package Substrate pricing. Typically, larger-scale production offers cost advantages as fixed costs are distributed across a greater number of products, thereby lowering the manufacturing cost per unit. Conversely, small-scale production tends to incur a higher proportion of fixed costs due to lower output, leading to relatively higher manufacturing costs per unit of product.
Top manufacturers can provide competitive quotes and flexible delivery options based on customer needs. **They usually comprehensively consider the customer’s mass production needs, technical requirements, delivery time and other factors, and provide a personalized quotation plan. They may provide different quotation options, such as bulk purchase discounts, customized service charges, expedited delivery charges, etc., to meet the different needs of customers.
Therefore, when selecting a Package Substrate supplier, in addition to paying attention to the quotation, you should also consider the manufacturer’s overall strength, technical level, delivery capabilities, and after-sales service to ensure that you choose the supplier that best suits your needs.
Frequently Asked Questions (FAQs) about Package Substrate
What is Package Substrate and how does it differ from traditional circuit boards?
Package Substrate is a critical electronic board that connects and supports electronic components, providing a structural foundation for circuits. Unlike traditional circuit boards, it typically features multiple layers and is made of insulating materials.
What advantages does Package Substrate offer over traditional circuit boards?
Package Substrate boasts several advantages, such as higher integration, improved signal integrity, smaller form factor, and cost-effectiveness. These features make it a preferred choice in modern electronic product design.
How does choosing Package Substrate benefit product performance and cost?
Collaborating with leading Package Substrate manufacturers ensures high-quality solutions that enhance product performance while reducing costs. This technology is particularly suitable for applications requiring high-density layouts and complex designs.
How does one choose the right Package Substrate for specific applications?
Choosing the right Package Substrate involves considering factors like product requirements, cost considerations, and performance criteria. Working closely with manufacturers and discussing specific needs can aid in making informed decisions.
Why should one opt for Package Substrate?
Opting for Package Substrate from top manufacturers ensures high-quality solutions tailored to meet specific requirements. Package Substrate enhances product performance, reduces costs, and is well-suited for applications demanding high-density layouts and complex designs.