The Thinnest PCB Manufacturer.Discover the epitome of precision and innovation with “The Thinnest PCB Manufacturer.” Setting the benchmark for excellence, we specialize in crafting ultra-thin printed circuit boards (PCBs) with unrivaled precision and quality. Experience the pinnacle of technological advancement with our cutting-edge solutions tailored to meet the most demanding requirements of modern electronics.
With the continuous evolution of electronic equipment, PCB (Printed Circuit Board) has become an indispensable part of the modern electronic field. In this article, we will focus on manufacturing techniques for the thinnest PCBs and their applications in the electronics industry.
What is The Thinnest PCB?
The thinnest PCB is an extremely thin printed circuit board that is widely used in electronic devices that require extremely thin and light design. The thickness of these PCBs is usually between tens and hundreds of microns, which is much thinner than traditional PCBs. In order to achieve such an ultra-thin design, the thinnest PCB uses special materials and manufacturing processes.
First of all, the thinnest PCB usually uses flexible substrate materials, such as polyimide (PI) film or other special film materials. Compared with traditional fiberglass-reinforced epoxy resin (FR-4) substrates, these flexible materials have higher flexibility and bendability, and can meet the thin and light design requirements of electronic devices. In addition, flexible substrates can adapt to complex shapes and curved surfaces, providing designers with greater design flexibility.
Secondly, manufacturing the thinnest PCB requires precision processing technology. This includes advanced processes such as laser cutting and chemical etching to achieve fine lines and tiny apertures. Due to the extremely thin thickness of PCBs, the processing process requires higher precision and control to ensure the accuracy and reliability of circuit layout. These precision processing technologies provide technical support for the manufacturing of the thinnest PCB.
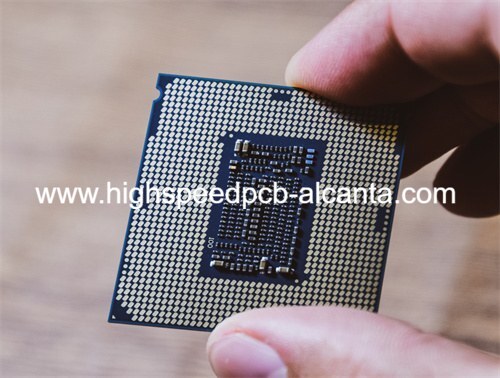
The Thinnest PCB Manufacturer
Finally, the thinnest PCBs are usually assembled using surface mount technology (SMT). SMT enables high-density assembly, soldering micro-components directly to the PCB surface, allowing for more compact circuit layouts. This high-density assembly method not only improves the integration of circuits, but also reduces the overall size, meeting the demand for thin and light designs.
To sum up, the thinnest PCB achieves ultra-thin and high-performance circuit layout by using special materials and manufacturing processes, providing important support for the thin and light design of electronic devices. With the continuous advancement of technology, the thinnest PCB will show its broad application prospects in more fields.
The Thinnest PCB design Reference Guide.
The design of the thinnest PCB requires comprehensive consideration of material selection, circuit layout, processing technology and other factors to ensure the ultimate thin and light design while maintaining circuit performance and reliability. Here is a reference guide for the thinnest PCB design:
Choosing the right substrate material is critical. For the thinnest PCBs, flexible substrate materials such as polyimide (PI) or special film materials are preferred. These materials offer excellent flexibility and high temperature resistance, making them suitable for ultra-thin designs.
When designing the thinnest PCBs, careful routing is required to minimize space usage and ensure signal integrity. Adopting a compact circuit layout and optimized wiring scheme can effectively reduce the thickness of the circuit board and improve performance.
Selecting components that are small in size and light in weight is critical to the design of the thinnest PCBs. The use of micro components and SMT technology can achieve high-density assembly and further reduce the thickness of the circuit board.
When manufacturing the thinnest PCBs, advanced processing techniques and precise control techniques are required. High-precision processing techniques such as laser cutting and chemical etching can achieve fine lines and apertures, ensuring circuit board thinness and performance.
Once the design is complete, rigorous testing and validation must be performed to ensure performance and reliability even on the thinnest PCBs. Test items include electrical performance testing, reliability testing and environmental adaptability testing.
Through reasonable material selection, careful circuit layout and advanced processing technology, the thinnest PCB with extremely thin and light design can be achieved. Designers should consider various factors to carefully design and optimize the thinnest PCB to meet the needs of different application scenarios.
What material is used in The Thinnest PCB?
The manufacture of the thinnest PCBs requires special materials to achieve extreme thinness and high performance. The following materials are commonly used for the thinnest PCBs:
Flexible polyimide (PI): Flexible polyimide is a high-temperature, high-strength polymer material with excellent heat resistance and chemical stability. It can maintain good mechanical strength in an extremely thin state and is suitable for applications that require flexible PCBs, such as wearable devices and medical devices.
Polyimide film (PI Film): Polyimide film is a special film material with extremely high temperature resistance and chemical stability. It can be made into extremely thin substrates and used to manufacture ultra-thin PCBs, suitable for electronic products that require high performance and lightweight design.
Polyimide fiberglass composite (PI/Glass Composite): This material combines the flexibility of polyimide and the strength of fiberglass, with good mechanical properties and heat resistance. It can be used to manufacture thin PCBs while ensuring high performance and reliability.
Thin Glass Substrate: Some special glass materials have extremely thin characteristics and are suitable for manufacturing ultra-thin PCBs. These thin glass substrates typically have excellent flatness and surface quality, enabling high-density circuit and component layouts.
Polyimide-polytetrafluoroethylene composite (PI-PTFE Composite): This composite material combines the advantages of polyimide and PTFE and has excellent heat resistance, chemical stability and low dielectric constant. It can be used to manufacture thin PCBs, achieve high-frequency signal transmission and suppress signal crosstalk.
To sum up, the materials used in the manufacture of the thinnest PCBs are usually special polymer materials with high temperature, high strength and chemical stability, such as flexible polyimide and polytetrafluoroethylene, as well as some special thin glass substrates . These materials can meet the thinness, performance and reliability requirements of ultra-thin PCBs, providing important support for the lightweight design of electronic products.
What size are The Thinnest PCB?
The dimensions of the thinnest PCBs vary and are often determined by specific application requirements and manufacturing technology limitations. Although there is no uniform standard size, the thinnest PCBs usually have the following characteristics:
Ultra-thin design: The thickness of the thinnest PCBs is usually between tens to hundreds of microns, which is much thinner than traditional printed circuit boards. This ultra-thin design allows them to be easily integrated into electronic devices that require an extremely thin and light design, such as smartphones, tablets, and wearable devices.
Small size: Due to their ultra-thin nature, the thinnest PCBs also tend to have small sizes. This allows them to achieve high-density circuit layouts in limited space, thereby meeting the needs for compact design and high performance.
Flexible substrate: Some of the thinnest PCBs use flexible substrate materials such as polyimide (PI), giving them the ability to bend and fold. This flexible design can not only adapt to special shapes and application scenarios, but also improve the reliability and durability of electronic devices.
Customized Dimensions: The thinnest PCBs are often custom manufactured based on specific application needs, so their dimensions can be adjusted and customized according to the customer’s requirements and design specifications.
Although the dimensions of the thinnest PCBs may vary depending on the application, their ultra-thin design and small size make them an integral part of modern electronic devices. With the continuous development of technology and advancement of manufacturing processes, we can foresee that the thinnest PCB will play a more important role in a wider range of applications, injecting new vitality into the innovation and development of the electronics industry.
The Manufacturer Process of The Thinnest PCB.
The manufacturing process of the thinnest PCBs involves a series of advanced processes and sophisticated technologies to ensure extreme thinness and high performance. Here are the main steps to create the thinnest PCB:
Select special substrate materials: Manufacturing the thinnest PCB first requires selecting special substrate materials, such as flexible polyimide (PI) or special film materials. These materials have excellent flexibility and high-temperature stability to meet the design requirements of ultra-thin PCBs.
Precision machining: Using advanced processing technology, such as laser cutting and chemical etching, the substrate is precision processed. These technologies enable extremely fine lines and tiny apertures, ensuring accuracy and reliability in circuit layout.
Surface treatment: Surface treatment, such as chemical cleaning and surface coating, is performed on the surface of the substrate to improve the accuracy and stability of the circuit layout. These surface treatments eliminate contaminants and oxides and enhance adhesion to the welding material.
Micro assembly: Using micro components and SMT (Surface Mount Technology) technology, high-density assembly of the thinnest PCB is possible. These assembly techniques enable compact layouts on extremely thin PCBs and ensure stable connections between electronic components.
Quality inspection: Conduct strict quality inspection and performance testing to ensure that the quality and performance of the thinnest PCB meet the requirements. These tests include electrical testing, reliability testing, and environmental suitability testing to verify the stability and reliability of the PCB under various conditions.
Through the above steps, the process of manufacturing the thinnest PCB enables precise control of materials and processes to ensure the ultimate thinness and high performance of the final product. These thinnest PCBs can be used in fields such as smartphones, wearable devices, medical devices, and aerospace, providing important support for the lightweight and high performance of electronic products.
The Application area of The Thinnest PCB.
The thinnest PCB has shown its unique application advantages in various fields. The following are some of the main application fields:
Smartphones and tablets are one of the most common applications for thinnest PCBs. As consumers’ demand for thin and light designs continues to increase, mobile phone and tablet manufacturers continue to pursue lighter and thinner designs. The use of the thinnest PCB makes the device lighter while ensuring high performance and reliability.
In the field of wearable devices, such as smart watches, fitness trackers and other products, the thinnest PCB is widely used. Since wearable devices need to be lightweight and comfortable, the thinnest PCB can achieve a lightweight design of the device and ensure its comfort when worn.
In the field of medical devices, the thinnest PCB also has important applications. For example, used in medical sensors and monitoring equipment, the thinnest PCB enables portable design of the equipment, making it more convenient and flexible for patients to use medical equipment.
In the aerospace industry, the demand for lightweight design and high performance is particularly prominent, and the thinnest PCB can meet this demand. The use of the thinnest PCB can effectively reduce the weight of aerospace electronic equipment and improve the performance and reliability of aerospace devices.
In addition to the above major fields, the thinnest PCB is also widely used in various high-end consumer electronics products, such as digital cameras, game consoles, audio equipment, etc. These products have high requirements for thin and light design and high performance. The thinnest PCB can meet these requirements and provide support for the market competitiveness of the products.
To sum up, the thinnest PCB is widely used in the fields of smartphones, wearable devices, medical equipment, aerospace, and high-end consumer electronics products. Its thin and light design and high-performance features provide excellent solutions for electronic equipment in all walks of life. Important support.
What are the advantages of The Thinnest PCB?
The advantage of the thinnest PCB lies in its unique design and manufacturing technology, which brings many benefits to various electronic devices.
First, one of the biggest advantages of the thinnest PCBs is the thin and light design. Due to the use of special substrate materials and precision processing technology, the thinnest PCB can achieve extreme thinness, allowing electronic devices to be lighter and more portable. This is particularly important for lightweight designed products such as mobile phones, tablets, and wearable devices, which improves user portability and comfort.
Secondly, the thinnest PCBs offer high flexibility. The thinnest PCBs made with flexible substrate materials can be bent, folded, and even adapted to special shape requirements. This flexibility allows the thinnest PCB to be used in various curved devices or products with special shapes, expanding its application fields.
Plus, the thinnest PCBs offer high performance and reliability. Although the PCB is extremely thin, it uses advanced manufacturing processes and high-quality materials to ensure its high performance in circuit layout, signal transmission, etc. At the same time, precision machining and strict quality control ensure the reliability and stability of the thinnest PCB, allowing it to work properly in various environments.
Overall, the advantages of the thinnest PCB lie in its thin and light design, flexibility, high performance and reliability, which provides new possibilities for the design and application of electronic devices. With the continuous advancement of technology and the expansion of application scenarios, the thinnest PCB will show broader development prospects in various fields.
FAQ
What is the thinnest PCB?
The thinnest PCB refers to an extremely thin printed circuit board, often used in electronic devices that require an extremely thin and light design. These PCBs often use special materials and manufacturing processes to achieve ultra-thin and high-performance circuit layouts.
What are the application areas of the thinnest PCB?
The thinnest PCB has a wide range of applications, including but not limited to smartphones, tablets, wearable devices, medical devices and aerospace. They are widely used in electronic products that require lightweight design and high performance.
What are the manufacturing technologies for the thinnest PCBs?
Manufacturing the thinnest PCBs requires advanced processes and materials. These include the use of ultra-thin substrate materials, precision processing techniques such as laser cutting and chemical etching, and micro-assembly techniques such as SMT. The combination of these technologies enables extreme thinness and high performance for the thinnest PCBs.
What are the advantages of the thinnest PCB?
The thinnest PCB brings many benefits including thin and light design, flexibility and high performance. They enable lightweight and compact designs of electronic devices while being suitable for special shapes and application scenarios. Advanced manufacturing processes and materials ensure high performance and reliability in the thinnest PCBs.