Substrate & Packaging Manufacturer, We mainly produce various types of packaging substrates, ultra-small marks and gaps, at the same time, we also assemble packaging business.
Package substrate, a fundamental element in contemporary electronic devices, serves as a foundational material for encapsulating and interconnecting electronic components. Typically crafted from insulating materials, it features circuit patterns and electrical connections, facilitating the integration of chips, resistors, capacitors, and other components. The substrate fulfills several crucial functions within electronic devices. Firstly, it establishes electrical connections, enabling seamless communication among various components. Additionally, it offers structural support and safeguards against environmental damage, ensuring the longevity of the components. Furthermore, the substrate efficiently transmits electronic signals, thereby sustaining the device’s operational integrity and performance. As electronic technologies evolve, the significance of packaging substrates continues to grow, becoming not only a central component but also a determinant of device functionality and efficiency. Consequently, comprehending the fundamentals and roles of packaging substrates is imperative for designing and producing high-quality, dependable electronic products.
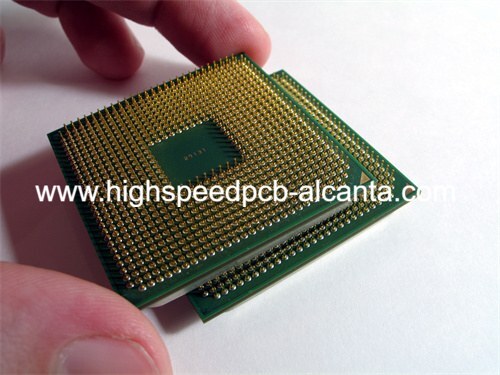
Substrate & Packaging Firm
What types of packaging substrates are there?
Packaging substrates play a crucial role in electronic devices, with distinct characteristics and applications across various types. Single-layer boards are basic substrates featuring simple structures and cost-effective manufacturing. They consist of an insulating base material with a conductive pattern, suitable for straightforward electronic devices like toys and household appliances. However, their limitations in circuit layout and connections make them less suitable for complex designs.
Double-layer boards enhance single-layer ones by adding an extra layer of conductive patterns, enabling more intricate circuit connections. Comprising two insulating substrates with a conductive layer in between, these boards offer higher circuit density and flexible layouts. They find applications in moderately complex electronic equipment such as computer peripherals and consumer electronics.
Multilayer boards represent the most intricate packaging substrates, incorporating multiple insulating layers and conductive patterns interconnected through perforations. Despite their complex manufacturing process, they provide superior circuit density and design flexibility, catering to high-end electronic devices like communication equipment, industrial control systems, and medical devices, meeting demanding performance criteria.
In summary, the choice of packaging substrate depends on factors like product design, performance needs, and cost considerations. Single-layer boards suit simple designs, double-layer boards are apt for moderate complexity, while multilayer boards excel in intricate designs and high-performance applications.
What are the advantages of packaging substrates?
Package substrates offer numerous advantages over traditional circuit boards, making them indispensable in the design and manufacturing of contemporary electronic devices. They provide stable electrical connections and reliable signal transmission through the use of high-quality conductive materials and advanced manufacturing techniques, crucial for high-frequency and high-speed data transmission applications. Additionally, they offer high integration and design flexibility, allowing for customized layouts that save space and enhance system performance. Package substrates also excel in thermal management, employing materials like metal layers or heat sinks to optimize heat dissipation and maintain stable component temperatures, vital for power-intensive or high-performance equipment. Moreover, their mass production and automated manufacturing processes reduce production costs and enhance efficiency compared to manual soldering and routing methods, ensuring consistency and minimizing defects. Through stringent quality control measures at every production stage, including material selection and welding processes, package substrate manufacturers uphold high standards, resulting in improved product quality and reliability, reduced maintenance needs, and enhanced user experiences. Overall, package substrates are pivotal in modern electronics, offering stable connections, design flexibility, thermal optimization, cost reduction, efficiency improvement, and heightened product quality and reliability.
How are packaging substrates made?
Packaging substrate manufacturing is a meticulous and intricate process aimed at ensuring the utmost quality and dependability of the final product. Below are the primary stages involved in manufacturing package substrates, along with key attributes of both motherboard and substrate manufacturing processes.
In the initial phases of packaging substrate manufacturing, engineers utilize professional design software to craft circuit diagrams and layouts. These designs account for the arrangement of electronic components, their interconnections, and overall dimensions.
The performance of the package substrate depends heavily on the careful selection of appropriate substrate materials. Factors such as insulating material thickness, properties of the conductive layer, and thermal characteristics are meticulously considered during this stage.
A critical phase in the manufacturing process involves creating the printed circuit board (PCB), which includes printing a circuit pattern onto a substrate and applying a conductive material to establish electrical pathways.
Unwanted metal segments are removed from the conductive layer to create the desired circuit pattern using techniques like chemical or laser etching.
Package substrates typically consist of multiple material layers, requiring a lamination process to bind them together and ensure substrate strength and stability.
The motherboard acts as the core of electronic equipment, containing essential components like the central processing unit (CPU), memory, and expansion slots. Its manufacturing process encompasses several key stages:
Substrate Fabrication: The initial step involves manufacturing the substrate through the PCB manufacturing process, ensuring precise circuit patterns and stable electrical performance.
Component Installation: The motherboard undergoes the process of mounting various electronic components such as the CPU, memory modules, and power interfaces, ensuring they are correctly connected and adhering to design specifications.
Soldering Techniques: Surface mount technology (SMT) components are firmly affixed to the motherboard through soldering methods, ensuring secure attachment and proper functionality.
Quality Assurance: During production, thorough testing and quality inspections are conducted on motherboards to verify that each component meets the required performance and connectivity standards.
In what fields are packaging substrates widely used?
Packaging substrates serve as critical connection and support structures for electronic components across diverse industries. In the realm of consumer electronics, they find extensive applications in devices like smartphones, tablets, and smart home gadgets, facilitating the stable electrical connections and signal transmission of key components such as processors, memories, and sensors.
In the communication equipment sector, packaging substrates are prevalent in routers, switches, and base stations. They play a crucial role in carrying various electronic components, enabling these devices to achieve complex signal processing and data transmission functions while ensuring device stability and reliability.
Industrial control demands highly reliable electronic equipment for monitoring and controlling production processes. Packaging substrates are integral to industrial controllers, sensors, and robots, supporting the connection of various sensors and actuators. They facilitate data acquisition, processing, and control functions.
Packaging substrates are essential components in a variety of industries, including consumer electronics, communication equipment, industrial control, medical devices, and automotive electronics. They facilitate the connection of sensors, actuators, and monitoring equipment, enabling precise data collection and processing for accurate diagnosis, treatment, and system functionality. In medical devices, these substrates are integral to monitoring equipment, diagnostic instruments, and treatment devices, ensuring reliable performance and data accuracy. Similarly, in automotive electronics, they are crucial for electronic control units (ECUs), entertainment systems, and driving assistance systems, enhancing overall functionality and performance. Across these sectors, packaging substrates serve as foundational platforms, supporting the design and manufacturing of diverse electronic devices.
How to find the right packaging substrate manufacturer?
When selecting the right packaging substrate manufacturer, it’s vital to consider several key factors to ensure the chosen supplier can effectively meet the company’s needs and standards. Here are some important considerations:
Quality Standards and Certifications: Confirm whether suppliers comply with industry-specific quality standards and possess certifications like ISO 9001. This guarantees consistent quality in the provided packaging substrates and adherence to global standards.
Manufacturing Technology and Capabilities: Assess the supplier’s manufacturing technology, equipment strength, process flow, and technical expertise. This evaluation ensures that the supplier can handle the required production volumes and troubleshoot technical challenges effectively.
Product Customization Abilities: If customized packaging substrates are needed, the supplier’s ability to tailor products to specific requirements is crucial. Opting for a supplier with robust customization capabilities enables the company to fulfill its unique needs effectively.
Selecting the appropriate packaging substrate manufacturer involves a nuanced evaluation process encompassing several critical factors. One must meticulously assess elements such as delivery time and service quality, as timely deliveries and responsive post-sales support are pivotal for maintaining operational efficiency and addressing issues promptly. Additionally, cost and price competitiveness play a significant role, as selecting a supplier offering reasonable and competitive pricing helps minimize production expenses and bolsters competitiveness in the market. Moreover, it is imperative to evaluate supply stability and supply chain management capabilities to mitigate risks associated with disruptions. A dependable supplier should exhibit robust supply chain management skills to ensure uninterrupted access to raw materials and seamless execution of production processes. By thoroughly scrutinizing aspects like quality, technology, service, cost, and supply chain management, companies can pinpoint a supplier that aligns with their requirements, thereby facilitating improvements in product quality and production efficiency.
How much does the packaging substrate cost?
Material cost: The type and quality of materials required for packaging substrate manufacturing directly affects the cost. High-quality materials typically cost more, and the cost of specialty materials can also increase manufacturing costs.
Production process: The level of process and technology required to manufacture the packaging substrate will also affect the price. Complex processes or special manufacturing requirements may require greater investment in manpower and equipment, thereby increasing costs.
The price of packaging substrates is influenced by various factors, with production quantity being a significant determinant. Higher production volumes often lead to lower unit costs, whereas smaller volumes may incur higher per-unit expenses. Additionally, specialized technical requirements or customized features can necessitate additional research and development expenses, impacting the final product price. Market competition also plays a crucial role, as manufacturers may adjust prices to remain competitive and attract customers in a highly contested market. Overall, customers should carefully assess these factors and compare offerings from multiple manufacturers to ensure they select reasonably priced products that meet their requirements.
FAQs about packaging substrates?
How can one find a suitable Package Substrate manufacturer?
Finding a reliable Package Substrate manufacturer involves methods such as online searches, attending industry exhibitions, considering reputation and recommendations, among others. It’s crucial to select a manufacturer that aligns with specific project needs.
What exactly is a package substrate?
A package substrate is a foundational material used in electronic devices to connect and package various electronic components. It typically consists of an insulating material with circuit patterns and electrical connections.
Why opt for package substrates over other boards?
Package substrates provide higher integration levels, superior electrical performance, and wider application scopes compared to other types of boards, making them ideal for diverse electronic device designs.
Where can one find reliable package substrate manufacturers?
Reliable package substrate manufacturers can be found through online searches, industry exhibitions, referrals, and reputation assessments to ensure quality and service satisfaction.
What are some common questions and answers regarding package substrates?
Common questions may include inquiries about manufacturing lead times, quality control measures, post-sales support, and customization options to ensure alignment with specific project needs.