Substrate For Chips Manufacturer.”Substrate for Chips Manufacturer” refers to a specialized manufacturer that focuses on producing high-quality substrates used in chip packaging. They excel in designing and fabricating substrates tailored to meet the stringent requirements of modern semiconductor devices, ensuring optimal electrical performance and reliability. These manufacturers play a pivotal role in enabling advanced technologies by providing innovative substrate solutions that enhance the efficiency and functionality of electronic components.
What is Substrate For Chips?
Chip substrate is an indispensable and important component of modern electronic equipment. It is a flat plate-like structure usually made of insulating materials such as FR4 (fiberglass reinforced epoxy) or polyimide, which have excellent electrical insulation properties and mechanical strength. These insulating materials are covered with copper foil, which is chemically etched to form circuit paths and soldering areas for connecting and supporting electronic components.
The design of the chip substrate can be flexibly adjusted according to specific application requirements, and can be rigid or flexible. Rigid chip substrates are suitable for applications that require higher mechanical strength and stability, such as computer motherboards, industrial control systems, etc.; while flexible chip substrates are suitable for devices that require bending or limited space, such as folding mobile phones, wearable devices, etc.
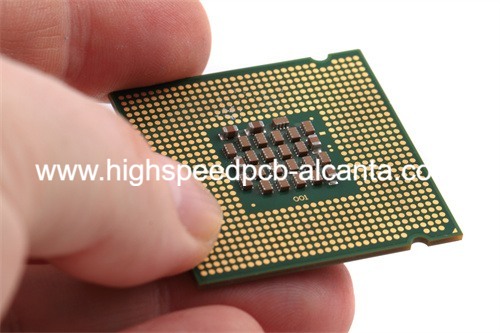
Substrate For Chips Manufacturer
On the chip substrate, complex circuit designs can be accurately produced through advanced manufacturing processes such as photolithography, etching and drilling steps. These circuits not only connect various electronic components, but also support the functional implementation and performance optimization of the device. Through surface mount technology (SMT) and through-hole assembly, components can be mounted on the surface or inside the chip substrate, further improving the integration and reliability of the device.
In short, as a key support platform for electronic devices, chip substrates not only provide stable electrical connections, but also meet the high requirements for performance, size and durability in different industries and application fields through their diversity of materials and designs. In the development of continuously innovative electronic technology, the importance of chip substrates will continue to play a key role, promoting the advancement of device functions and the development of intelligence.
Substrate For Chips design Reference Guide.
In modern electronic devices, the design of Substrate For Chips (chip substrate) is a key factor in ensuring device performance and reliability. Chip substrates are more than just platforms that support and connect electronic components. Their design directly affects the overall performance and cost-effectiveness of electronic devices. To help engineers and designers optimize their design processes and results, here are some key chip substrate design guidelines and recommendations.
Material selection for the chip substrate is critical to the success of the design. Common materials include FR4 (fiberglass reinforced epoxy) and polyimide, etc. When selecting materials, consider their electrical properties, mechanical strength, thermal properties, and cost-effectiveness. For example, for high-frequency applications, polyimide provides excellent electrical properties and stability, while FR4 is suitable for most applications in general electronic equipment.
During the design process of chip substrates, following strict design rules and constraints is key to ensuring circuit board performance and reliability. These rules cover aspects such as board stack-up structure, routing rules, component placement, pad design, and circuit isolation. Reasonable design rules can minimize signal interference, electrical noise and thermal problems, and improve the stability and reliability of the equipment.
In high-performance and high-density electronic devices, effective thermal management is critical. Reasonable heat dissipation design can ensure that the chip substrate maintains a stable temperature during long-term operation and avoids performance degradation or equipment damage caused by overheating. Designers should consider using thermal copper foil, heat sinks, and thermal conductive materials to optimize heat dissipation, combined with proper air flow and equipment layout.
Effective chip substrate design should take into account future device scalability and maintainability. This includes allowing enough space and interfaces to support future feature expansion while simplifying repairs and upgrades. Proper layout and standardized connector selection can reduce maintenance costs and equipment downtime.
Modern chip substrate design relies on advanced design tools and technologies. Using CAD software for design and simulation can help designers discover and solve potential problems in the early stages of design, improving design efficiency and accuracy. In addition, incorporating rapid prototyping technologies (such as 3D printing) can speed up the design iteration process and shorten product time to market.
By following the above chip substrate design guidelines and recommendations, engineers and designers can better optimize their design process to ensure optimal performance, reliability and cost-effectiveness of the design. This not only helps improve product competitiveness, but also promotes technological progress and innovation in the entire electronics industry.
What material is used in Substrate For Chips?
Material selection for chip substrates is critical to the performance and reliability of electronic devices. Common chip substrate materials include FR4 (fiberglass reinforced epoxy resin) and polyimide, each of which has its own characteristics and is suitable for different application needs.
First, FR4 is a widely used rigid chip substrate material. It is composed of fiberglass cloth and epoxy resin matrix, and has excellent electrical insulation properties and good mechanical strength. This material is widely used in many common electronic devices, such as computer motherboards, electronic game consoles, communication equipment, etc. The main advantage of FR4 material is its stability and reliability. It can withstand high temperatures and environmental stress and is suitable for applications that require long-term stable operation.
Second, polyimide (PI) is an ideal choice for flexible chip substrates. Polyimide has excellent high temperature resistance and chemical stability, as well as excellent mechanical flexibility and the ability to maintain stable electrical properties in environments that require bending and twisting. This makes it widely used in flexible electronic devices such as foldable screens, curved displays and medical equipment. The main characteristics of polyimide materials are their lightness, thinness and moldability, allowing designers to create more compact and innovative products.
Overall, choosing the right chip substrate material has a significant impact on the performance, reliability, and cost of electronic devices. Whether you choose stable FR4 or flexible polyimide, you need to evaluate and select based on specific design requirements and application environment to ensure optimal circuit performance and long-term reliable operation. With the continuous advancement of electronic technology, the choice of chip substrate materials is also constantly evolving, providing more possibilities and opportunities for the development of new electronic products.
What size are Substrate For Chips?
The size of chip substrates (Substrate For Chips) varies greatly due to the wide range of applications. From small smart devices to large industrial equipment, different application requirements determine the size range and form of chip substrates.
In consumer electronics, such as smartphones and tablets, chip substrates are often very small. These devices pursue lightness and portability, so the chip substrate needs to be designed to be compact enough to accommodate various tiny electronic components and connection lines. The size of a typical mobile phone chip substrate may be only a few centimeters to more than ten centimeters, but it integrates multiple functional units such as processors, memories, and wireless modules.
In industrial automation and aerospace, chip substrates tend to be larger and more complex. These applications need to handle higher power and more complex electronic signals, so the chip substrate must be able to carry a large number of electronic components and complex connection structures. For example, the chip substrates of industrial equipment controllers or avionics equipment may reach tens of centimeters or even larger to meet complex circuit design and high reliability requirements.
In addition, the medical device field is also a typical example of the diversification of chip substrate sizes. From portable health monitoring devices to large medical imaging devices, the chip substrate size and shape of these devices are optimized for their specific medical use and technical requirements.
Overall, the size of the chip substrate not only depends on the functional requirements of the device, but is also affected by factors such as manufacturing technology, cost-effectiveness, and reliability. As technology continues to advance and application fields expand, chip substrates will continue to develop more diverse and complex sizes and designs to support various innovations and application needs.
By understanding and adapting to chip substrate designs of different sizes, engineers and designers can better meet market demands and promote the advancement and development of electronic technology.
The Manufacturer Process of Substrate For Chips.
Substrate For Chips is a core component of modern electronic equipment. Its manufacturing process goes through multiple delicate steps to ensure the stable performance and reliability of electronic equipment. The following are the key steps in chip substrate manufacturing:
The first step in manufacturing a chip substrate is to prepare the base material. Commonly used base materials include fiberglass reinforced epoxy (FR4) and polyimide (PI). These materials must be cut to precise dimensions and surface treated to ensure smooth processing in subsequent process steps.
A thin layer of copper foil is deposited on the surface of the substrate to form a conductive layer. This step is critical because the copper foil will form the basis for subsequent circuit patterns and requires good adhesion and uniform thickness.
Coat the surface of the copper foil with photoresist, and then project the designed circuit pattern onto the photoresist through exposure. After exposure, the photoresist will solidify to form a pattern, exposing the portions of the copper foil that need to be etched.
The uncured photoresist and the copper foil underneath are etched away, leaving only the designed circuit pattern. This step is achieved through chemical solutions or physical methods and requires precise control to ensure the accuracy and clarity of the circuit pattern.
According to the design requirements, holes are drilled on the etched substrate for circuit interconnection and component installation. These holes must be precisely located and sized to accommodate subsequent component installation and soldering.
Electronic components are mounted on the substrate, including integrated circuit chips, resistors, capacitors, etc. These components are fixed on the substrate through soldering technology and connected with the wires in the circuit pattern to form a complete circuit structure.
After components are installed and soldered, a comprehensive functional and performance test is performed. These tests ensure that the chip substrate will operate stably in actual applications and meet design requirements and specifications.
Through the above meticulous manufacturing steps, chip substrates are guaranteed to play an important role in modern electronic devices. Its high-precision manufacturing process and stable quality control make chip substrates a reliable foundation for various electronic devices, promoting the continuous progress and innovation of electronic technology.
The Application area of Substrate For Chips.
As a key component of modern electronic equipment, chip substrates (Substrate For Chips) are widely used in many industries, providing reliable electrical connections and support for various equipment and applications. The following are the specific applications and importance of chip substrates in several major application areas:
In consumer electronics such as smartphones, tablets and personal computers, chip substrates play a key role. They support the connection and electrical signal transmission of key components such as processors, memory chips, and communication modules. Due to the requirements for miniaturization and high performance of consumer electronics products, compact design and high-density integration of chip substrates are particularly important.
In the communications industry, including mobile communications base stations, satellite communications equipment, and wireless network equipment, chip substrates are widely used to support high-frequency and high-speed data transmission requirements. They not only connect and support radio frequency devices, but also ensure the stability and reliability of communication systems, adapting to complex environmental conditions and long-term operation requirements.
In modern automobiles, chip substrates are used to control key components such as engine management systems, in-vehicle infotainment systems, and driver assistance systems. They must be able to withstand high temperatures, vibrations and electromagnetic interference while ensuring system stability and safety. The rapid development and intelligent trend of automotive electronics have further promoted the innovation and application of chip substrates in this field.
In industrial control and automation systems, chip substrates are used to connect and support sensors, actuators, control units and other equipment to achieve factory automation and intelligent production. They are responsible for transmitting and processing critical data, supporting complex manufacturing processes and equipment Internet of Things (IIoT) applications, and improving production efficiency and product quality.
In the field of medical equipment, such as pacemakers, medical imaging equipment and monitoring systems, the application of chip substrates is crucial. They support the integration of various medical sensors and signal processing devices to ensure the accuracy, stability and safety of the equipment. The requirements for high reliability and long-term stable operation of medical equipment make chip substrates indispensable in this field.
To sum up, chip substrates, as a basic component of electronic technology, play a key role in multiple application fields such as consumer electronics, communications, automotive electronics, industrial automation and medical equipment. As technology advances and market demands continue to evolve, the design and application of chip substrates will continue to innovate, promoting performance improvements and functional expansion of electronic products.
What are the advantages of Substrate For Chips?
As a key component of modern electronic equipment, chip substrate (Substrate For Chips) has multiple advantages and plays a vital role in the performance and reliability of the equipment. Here are a few significant advantages of chip substrates:
The chip substrate design enables a highly compact circuit layout and effectively utilizes the internal space of the device. By optimizing wiring and component arrangement, electronic components can be integrated into a miniaturized space, thereby making the device lighter and more portable. This is especially important with today’s mobile devices and portable electronics, such as smartphones, tablets and wearables.
The chip substrate uses high-quality insulating materials, such as FR4 and polyimide, which have excellent electrical insulation properties and stability. This ensures reliable operation of the circuit and immunity to environmental changes. For high-frequency and high-speed transmission applications, such as communication equipment and data center servers, chip substrates can provide excellent performance with low loss and high-frequency response.
Chip substrate manufacturing uses advanced automated processes, including steps such as photolithography, etching, drilling and component mounting, which greatly improves production efficiency and consistency. Automated production not only reduces costs, but also reduces the risk of human error and ensures product quality and reliability. This makes the chip substrate suitable for mass production and rapid market response needs.
Environmentally friendly and sustainable materials and processes are increasingly used in modern chip substrate manufacturing processes. For example, some manufacturers choose to use lead-free solder and recycled materials to reduce negative environmental impacts. This environmental awareness is not only in line with global green standards, but also in line with consumers’ growing concerns about product sustainability.
Chip substrates allow designers to flexibly customize designs based on specific needs. Layout and size can be adjusted based on factors such as circuit complexity, power requirements, and physical space constraints to achieve the best balance of performance and cost-effectiveness. This flexibility makes the chip substrate not only suitable for general-purpose electronic devices, but also supports highly customized industry applications, such as medical equipment and industrial automation systems.
In summary, chip substrates are not only a key component of modern electronic technology, but their advantages include compact design, excellent electrical performance, efficient manufacturing processes, environmentally friendly material selection, and flexible customization capabilities. These advantages allow chip substrates to play an important role in promoting innovation and performance improvement of electronic equipment, bringing broad development space and application potential to various industries.
FAQ
What is Substrate For Chips?
A chip substrate is a flat plate-like structure used to support and connect electronic components, usually made of insulating material and covered with copper foil. It provides a mounting platform for electronic components and connects these components through structures such as wires and pads. It is an indispensable and key component of electronic equipment.
What materials are used for chip substrates?
Common chip substrate materials include FR4 (fiberglass reinforced epoxy), which has good electrical insulation properties and mechanical strength and is suitable for most applications. Flexible chip substrates use materials such as polyimide, which can bend and twist, and are suitable for applications that require high flexibility.
What is the manufacturing process of chip substrates?
The manufacturing process of chip substrates includes multiple key steps such as substrate preparation, copper foil layer deposition, photoresist coating and exposure, etching, drilling, component mounting, soldering, and testing. Advanced manufacturing technology ensures product high quality and stability.
In what fields are chip substrates widely used?
Chip substrates are widely used in consumer electronics products such as smartphones, tablets, industrial automation equipment, communication equipment, medical instruments, aerospace devices and other fields. They play an important role in connecting and supporting electronic components in these fields.