Semiconductor Substrate Manufacturer.”Semiconductor Substrate Manufacturer” refers to a company specializing in the production of substrates crucial for semiconductor device assembly. These manufacturers ensure precise material selection, advanced manufacturing processes, and stringent quality control to meet the exacting demands of modern electronics.
In today’s world, where electronic devices are becoming increasingly miniaturized and high-performance, semiconductor substrates are leading the wave of innovation in the semiconductor packaging industry. By integrating various advanced materials and techniques, semiconductor substrates achieve thinner, lighter, and higher-performing packaging forms, meeting the demands of modern electronic devices for high density and high performance. This article will provide a detailed overview of semiconductor substrates, covering their definition, design references, materials, sizes, manufacturing process, application areas, advantages, and frequently asked questions, helping readers gain a comprehensive understanding of this advanced technology.
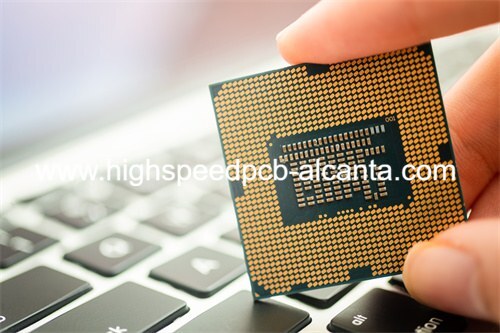
Semiconductor Substrate Manufacturer
What is Semiconductor Substrate?
A semiconductor substrate is a foundational material used in the fabrication of semiconductor devices. It serves as the base on which various electronic components, such as transistors and integrated circuits, are built. Semiconductor substrates are typically made from silicon or other semiconductor materials, providing the necessary physical support and electrical properties for the devices. These substrates play a crucial role in determining the overall performance, efficiency, and reliability of the semiconductor devices. By providing a stable platform with precise electrical characteristics, semiconductor substrates enable the integration of complex electronic functions in a compact form factor.
Semiconductor Substrate Design Reference Guide
Designing semiconductor substrates requires a thorough understanding of both the electrical and mechanical requirements of the final application. The design process involves several critical steps. Firstly, material selection is essential, with dielectric materials being chosen for their electrical insulation and mechanical stability. These materials are selected based on their dielectric constant, loss tangent, and thermal properties. Secondly, the layer stack-up design ensures optimal signal integrity and power distribution, often including multiple signal layers, power planes, and ground planes. Via and trace design is another critical aspect, defining the size, shape, and placement of vias and traces to minimize signal degradation and electromagnetic interference. Effective thermal management is crucial, incorporating thermal vias, heat sinks, and other techniques to dissipate heat efficiently. Finally, simulation and testing are imperative, using simulation tools to model the electrical performance and validate the design through rigorous testing. By following these guidelines, designers can create semiconductor substrates that meet the stringent requirements of modern electronic devices.
What Material is Used in Semiconductor Substrate?
The materials used in semiconductor substrates are crucial for their performance and reliability. High-performance resins and epoxy materials are typically used as dielectric materials, providing excellent electrical insulation and mechanical strength. These materials are selected based on their dielectric constant, loss tangent, and thermal properties to ensure optimal performance. Copper is commonly used for the conductive traces and planes due to its excellent electrical conductivity and compatibility with standard PCB manufacturing processes. A protective solder mask layer is applied over the substrate to prevent solder bridging and to protect the underlying circuits from environmental damage. Additionally, various surface finishes, such as Electroless Nickel Immersion Gold (ENIG), are used to enhance solderability and protect the copper surfaces from oxidation. These materials are carefully chosen to ensure the semiconductor substrates meet the required electrical, thermal, and mechanical specifications.
What Size are Semiconductor Substrates?
Semiconductor substrates come in various sizes, tailored to the specific needs of different applications. The size of the substrate is determined by several factors, including the dimensions of the silicon die being packaged, the number of input/output connections required for the application, and the specific requirements of the end application, such as space constraints and performance criteria. Typically, semiconductor substrates range from a few millimeters to several centimeters in size, providing flexibility to accommodate various chip sizes and application needs.
The Manufacturing Process of Semiconductor Substrate
The manufacturing process of semiconductor substrates involves several key steps. It begins with lamination, where layers of dielectric and conductive materials are laminated together to form the substrate. Photolithography is then used to create the desired circuit patterns on the substrate layers. Vias are drilled or laser-etched into the substrate to provide electrical connections between the layers. Copper plating is applied to the vias and traces to ensure good electrical conductivity. A solder mask is then applied to protect the circuits and define the areas for solder ball placement. A surface finish, such as ENIG, is applied to enhance solderability and protect the copper surfaces. Finally, the substrates undergo rigorous inspection and testing to ensure they meet the required specifications and quality standards. Each step in the manufacturing process is carefully controlled to produce high-quality semiconductor substrates that meet the demanding requirements of modern electronics.
The Application Area of Semiconductor Substrate
Semiconductor substrates are used in a wide range of applications, including consumer electronics, automotive electronics, networking and telecommunications, medical devices, and industrial automation. In consumer electronics, smartphones, tablets, and wearable devices benefit from the compact size and high performance of semiconductor substrates. Advanced driver-assistance systems (ADAS) and infotainment systems in automotive electronics require reliable and high-performance substrates. High-speed routers, switches, and servers in networking and telecommunications utilize semiconductor substrates for their superior electrical performance. Miniaturized medical devices and diagnostic equipment in the medical field require substrates that offer excellent performance in a small form factor. Control systems and sensors in industrial automation benefit from the robustness and reliability of semiconductor substrates. These diverse application areas highlight the versatility and importance of semiconductor substrates in modern electronics.
What are the Advantages of Semiconductor Substrates?
Semiconductor substrates offer several significant advantages. One of the primary benefits is the reduction in thickness and weight, achieved by the elimination of traditional core layers, making these substrates ideal for compact and portable devices. Improved electrical performance is another key advantage, with lower signal loss and power consumption enhancing overall device performance. This is particularly beneficial for high-speed and high-frequency applications. Cost savings in manufacturing are also a notable benefit, as simplified production processes and reduced material usage lead to lower production costs. Enhanced reliability is achieved through better thermal management and reduced mechanical stress, contributing to increased longevity of the package. Finally, the ability to accommodate high-density interconnects allows for more complex and capable electronic designs, making semiconductor substrates a preferred choice for many high-performance and space-constrained applications.
FAQ
What is the main difference between traditional FC-BGA and semiconductor substrates?
The primary difference lies in the advanced materials and techniques used in semiconductor substrates, which result in a thinner, lighter, and more electrically efficient package compared to traditional FC-BGA.
How does the design of semiconductor substrates improve electrical performance?
By using high-performance materials and optimizing the layer stack-up and via design, semiconductor substrates reduce signal loss and power consumption, leading to better electrical performance, especially in high-speed and high-frequency applications.
What are the typical materials used in semiconductor substrates?
High-performance dielectric resins, copper for conductive traces, solder mask for protection, and surface finishes like ENIG for enhanced solderability are commonly used materials in semiconductor substrates.
What sizes are available for semiconductor substrates?
Semiconductor substrates come in various sizes, typically ranging from a few millimeters to several centimeters, depending on the application requirements and chip size.