Semiconductor substrate Manufacturer. High Frequency and High-speed substrates(PCBs) provider , ultra-small trace width substrates manufacture, specializing in 2-50 layer high-quality substrates, including Semiconductor substrate.
Semiconductor substrates play a vital role in today’s electronic devices. It is a substrate that supports and connects various electronic components, such as chips, sensors, etc., providing a solid foundation for the entire device. In short, semiconductor substrates are an integral part of modern electronic devices.
In various electronic devices, semiconductor substrates serve various functions. First, it provides a stable platform on which various electronic components can be mounted and connected together. Secondly, the semiconductor substrate plays a conductive and insulating role in the circuit, helping to control the flow of electronic signals and isolating interference between different circuits. In addition, the semiconductor substrate can also play a role in heat dissipation in electronic equipment, effectively dissipating the heat generated in the equipment and maintaining the normal operating temperature of the equipment.
By definition, a semiconductor substrate is a substrate used for electronic components, and its materials are usually silicon, glass, etc. Its design and manufacturing processes are subject to precise process control to ensure its quality and stability. In the modern electronics industry, the quality of semiconductor substrates directly affects the performance and reliability of the entire electronic device.
In conclusion, semiconductor substrates play an integral role in modern electronic devices. It not only provides solid basic support, but also plays an important role in circuit connection, signal transmission and heat dissipation. For any electronic product, selecting the appropriate semiconductor substrate is one of the keys to ensuring product performance and quality.
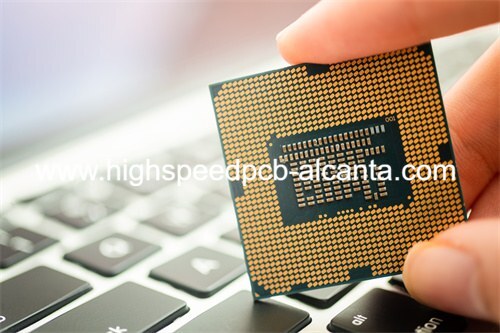
Semiconductor Substrate Manufacturer
What types of semiconductor substrates are there?
There are many types of semiconductor substrates in modern electronic equipment, including BGA (Ball Grid Array), LGA (Land Grid Array), CSP (Chip Scale Package), etc. Each type of semiconductor substrate has unique features in structure and applications and is suitable for different scenarios and needs.
BGA (Ball Grid Array): BGA is a ball grid array package, which is characterized by small spherical solder joints on the bottom for connection to the PCB board. This packaging form makes BGA perform well in high-density circuit layouts and can achieve more connection points in a relatively small space, thus improving the integration and performance of the circuit board. BGA is commonly used in high-performance computers, servers, network equipment and other fields.
LGA (Land Grid Array): Unlike BGA, the solder joints of the LGA package are not on the bottom, but on the sides or top of the package. They are connected to the PCB board through a series of pads or contact points. Compared with BGA, LGA is easier to control during the manufacturing and installation process, and it is also easier to achieve heat dissipation. LGA is commonly used in some applications that require high heat dissipation performance, such as CPUs, GPUs, etc.
CSP (Chip Scale Package): CSP is a form of packaging whose size is usually similar to the size of the chip itself, so it is called chip scale packaging. CSP packaging usually has no additional packaging volume and can achieve high integration and miniaturization. CSP is widely used in mobile devices, consumer electronics and other fields to provide products with higher integration and smaller size.
When selecting a suitable semiconductor substrate type, factors such as product performance requirements, size constraints, cost budget, etc. need to be considered. For example, for applications that require high performance and high-density layout, BGA may be a better choice; while for applications with higher size and heat dissipation requirements, you can consider using LGA packaging; and for applications that pursue miniaturization and high integration, products, CSP packaging may be more suitable.
To sum up, different types of semiconductor substrates have unique advantages in structure and application and can meet the needs of various scenarios. When designing and selecting a semiconductor substrate, product requirements and limitations need to be considered in order to select the most suitable package type.
What are the advantages of semiconductor substrates compared to other boards?
As an important component of electronic equipment, semiconductor substrates have significant advantages in many aspects compared with traditional boards. These advantages are why more and more electronic products choose to use semiconductor substrates.
Semiconductor substrates can accommodate more components and connections, providing a higher level of integration. This means that more complex circuit designs can be implemented in a limited space, making the device smaller and lighter.
Compared with traditional boards, semiconductor substrates are smaller in size, so they have more advantages in designing and manufacturing miniaturized devices. This is crucial for mobile devices such as phones and tablets, allowing them to reduce device size while maintaining performance.
Semiconductor substrates generally have better thermal management capabilities and can more effectively disperse and remove the heat generated by the device. This ensures that the equipment is less likely to overheat during long-term high-load operation, improving the stability and reliability of the equipment.
Because semiconductor substrates can accommodate more components and have better thermal management capabilities, higher performance electronic devices can be achieved. This is especially important for devices that need to process large amounts of data or perform complex tasks.
Although the manufacturing cost of semiconductor substrates may be higher, overall system costs can be reduced due to their small size, high integration, and high performance. For example, the number of external components and connecting lines can be reduced, saving material and production costs.
Since semiconductor substrates have many advantages, they are widely used in various electronic products. From smartphones and tablets to industrial control systems and medical equipment, semiconductor substrates play a key role.
In general, semiconductor substrates have obvious advantages over traditional boards in terms of size, performance, and thermal management, making them the first choice for more and more electronic products. With the continuous development of technology, the advantages of semiconductor substrates will be further highlighted and promote the innovation and development of electronic products.
What is the manufacturing process of semiconductor substrates?
The manufacturing process of semiconductor substrates is a precise and complex process involving multiple critical steps to ensure the quality of the final product. The following will introduce the manufacturing process of semiconductor substrates and how manufacturers ensure product quality.
The first step in the manufacturing process is design and planning based on the customer’s needs and application scenarios. At this stage, the manufacturer works closely with the customer to determine parameters such as substrate specifications, materials, and properties.
Once the design is finalized, the manufacturer will prepare the required materials. These materials typically include substrates, metallization layers, insulating layers, etc. Manufacturers strictly select and inspect each batch of materials to ensure they meet quality standards.
Next, manufacturers use techniques such as chemical vapor deposition (CVD) or physical vapor deposition (PVD) to form a thin film on the surface of the substrate. These films are often used to provide conductivity or isolation layers.
Patterning is one of the key steps in the manufacturing process, with manufacturers using photolithography techniques to transfer the desired pattern to the substrate surface. This typically involves steps such as coating, exposing, and developing photoresist.
After the pattern is formed, the manufacturer will deposit a metallization layer on the surface of the substrate to form wires, connection points, etc. This is usually achieved through techniques such as evaporation or electroplating.
Finally, manufacturers perform final processing, including cutting, cleaning, inspection and other steps to ensure that the final product meets specifications. Throughout the manufacturing process, manufacturers will take strict quality control measures, such as using advanced equipment and implementing strict inspection procedures, to ensure product quality.
Manufacturers conduct strict quality checks at every manufacturing stage to ensure that products meet customer requirements and industry standards. These inspections include visual inspection, dimensional measurements, electrical testing, etc. In addition, manufacturers will establish a quality management system and continuously improve the manufacturing process to ensure the stability and reliability of product quality.
Through the above steps, manufacturers can ensure that the manufacturing process of semiconductor substrates is efficient and precise, and product quality is reliably guaranteed. These efforts not only ensure customer satisfaction, but also lay a solid foundation for manufacturers to maintain a competitive advantage in a highly competitive market.
In what fields are semiconductor substrates used?
As an indispensable component of modern electronic equipment, semiconductor substrates are widely used in many fields. From smartphones to automotive electronics, semiconductor substrates play a critical role, providing a solid foundation for the performance and functionality of these devices.
In the field of smartphones, semiconductor substrates are widely used in chip packaging and connection. By connecting various chips and sensors together, the semiconductor substrate enables efficient communication between the various functional modules of the mobile phone, thereby enabling the feature-rich and high-performance smartphones.
In addition to smartphones, semiconductor substrates also play an important role in computer devices such as tablets, laptops, and desktop computers. They are used to connect core components such as processors, memory, and graphics cards, realizing interconnection between various computer components and ensuring the stability and performance of the computer system.
In the field of automotive electronics, semiconductor substrates are increasingly used. They are used to connect various sensors, control units and communication equipment in the car, enabling data exchange and collaborative work between various systems in the vehicle. Through the application of semiconductor substrates, modern automobiles have realized functions such as intelligent driving, intelligent safety and intelligent entertainment, improving vehicle safety, comfort and convenience.
In addition, semiconductor substrates also play an important role in industrial control, medical equipment, communication equipment and other fields. They provide stable connections and efficient data transmission for devices in these fields, promoting technological progress and application innovation in various industries.
To sum up, semiconductor substrates are widely used in many fields such as smartphones, computers, automotive electronics, industrial control, and medical equipment. They provide a solid foundation for the functions and performance of these devices and promote the development and progress of modern electronic technology.
How to obtain semiconductor substrate?
To obtain high-quality semiconductor substrates, you can purchase them through a variety of channels. Both manufacturers and suppliers offer a variety of services to meet the needs of different customers. Here are some common sources and services:
Contacting the manufacturer of the semiconductor substrate directly is one of the most direct ways to obtain it. Manufacturers often offer customized solutions that can be produced according to the customer’s specific needs. By contacting the manufacturer directly, you can gain more customization options and ensure the product meets your requirements.
As a supplier of semiconductor substrates, we provide various types and specifications of semiconductor substrate products. Through our company, you can get a diverse product selection and competitive prices. Our service team will provide you with professional consultation and support to help you choose the product that best suits your needs.
In addition to contacting manufacturers and suppliers directly, you can also purchase semiconductor substrates through online platforms. Many e-tailers and B2B platforms offer sales of semiconductor substrates, where you can find and compare products from different brands and models to find the best option for you.
Participating in relevant professional exhibitions and industry events is also a way to obtain semiconductor substrates. At these exhibitions, you can communicate directly with various manufacturers and suppliers to learn about the latest product information and technology trends, so as to better select and purchase suitable products.
No matter which method you choose to obtain semiconductor substrates, the choice should be based on your specific needs and budget. Make sure the product you choose meets quality standards and can meet your project needs. If you have any questions or need further assistance, please feel free to contact us and we will be happy to serve you.
What is the quote for semiconductor substrates?
When seeking a quote for a semiconductor substrate, there are several key steps and factors to consider. Here are some important takeaways on how to get a quote for a semiconductor substrate and what factors influence the price:
First, you can obtain a quote by contacting the semiconductor substrate manufacturer directly or through its official website. Manufacturers often provide online quoting tools or contact forms that enable you to provide them with the required specifications and quantities and get a quick quote.
Second, quotes can be obtained through approved semiconductor substrate suppliers. These suppliers often work with multiple manufacturers and are able to offer customers a variety of options to meet their needs.
Material cost: The cost of semiconductor substrates is mainly affected by material cost. The cost of different materials varies greatly, and market availability may also affect prices.
Customization requirements: If the customer has special customization requirements, such as special size, material or process, it will increase the manufacturer’s cost, thus affecting the final quotation.
Quantity: The order quantity is an important factor affecting the quotation. Generally speaking, large quantity orders can get more competitive prices, while small quantity or sample orders may have higher prices.
Technology requirements: If customers require higher-level technologies, such as high-density interconnect (HDI) technology or advanced packaging processes, manufacturers may increase prices.
Market demand: The supply and demand relationship in the market will also have an impact on prices. When market demand increases, manufacturers may adjust prices to match market demand.
To sum up, obtaining a quotation for a semiconductor substrate requires consideration of multiple factors, including material cost, customization requirements, order quantity, technical requirements, and market supply and demand. In order to get the most suitable quotation, it is recommended to contact multiple manufacturers or suppliers and compare and evaluate based on actual needs.
What are the common problems with semiconductor substrates?
What are the typical issues encountered during semiconductor substrate manufacturing?
During semiconductor substrate manufacturing, common issues may include material defects, process variations, and contamination. These issues can impact the quality and reliability of the substrates, leading to potential performance issues in electronic devices.
How does substrate design affect device performance?
Substrate design plays a crucial role in determining the electrical and thermal characteristics of semiconductor devices. Poor substrate design can result in signal interference, thermal inefficiency, and other performance limitations. It’s essential to optimize substrate design to enhance device performance.
What measures are taken to ensure substrate reliability?
Semiconductor substrate manufacturers implement various quality control measures to ensure substrate reliability. These measures may include rigorous testing, material inspections, and adherence to industry standards such as IPC (Association Connecting Electronics Industries) specifications.
What factors influence substrate selection for specific applications?
Several factors influence substrate selection, including electrical properties, thermal conductivity, mechanical strength, and cost. The chosen substrate must meet the specific requirements of the application, balancing performance, reliability, and cost-effectiveness.
How does substrate material choice impact device functionality?
The choice of substrate material significantly affects device functionality. Different materials offer varying electrical, thermal, and mechanical properties, influencing device performance and reliability. Manufacturers select substrate materials based on the application’s requirements and performance objectives.
What role do advanced technologies play in substrate manufacturing?
Advanced manufacturing technologies, such as laser drilling, precision etching, and automated assembly, play a crucial role in semiconductor substrate manufacturing. These technologies enable the production of intricate substrate designs with high precision and consistency, enhancing device performance and reliability.
What are the environmental considerations in substrate manufacturing?
Semiconductor substrate manufacturing involves various processes that may have environmental implications, such as chemical usage, waste generation, and energy consumption. Manufacturers prioritize sustainability by implementing environmentally friendly practices, waste reduction strategies, and energy-efficient processes.