Mini Led PCB Manufacturing, Ultra-small gap LED PCBs manufacture. We have made the LED pcb Pads to pads gap with 40um. 50um, 60um, some pads to pads gap are 80um. we can use the package substrates Msap and Sap production technology to produce the MINI led PCBs. we can do the LED pcb gaps with lower 20um gaps.
What is Mini LED PCB manufacturing?
In today’s rapidly developing electronics industry, Mini LED PCB (Printed Circuit Board) has become a technology that has attracted much attention. In short, Mini LED PCB is a circuit board specially designed for Mini LED display technology. This circuit board carries a large number of Mini LED chips, providing a key foundation for the manufacture of Mini LED displays.
The rise of Mini LED technology stems from the continuous pursuit of display effects. Compared with traditional LEDs, Mini LEDs are smaller, so they can achieve higher pixel density and better display effects. Mini LED PCB is a key link in transforming this technology into actual products.
Mini LED PCB usually adopts a multi-layer design to accommodate a large number of Mini LED chips and provide circuit connection and control. These boards can come in different shapes and flexibility to suit the needs of various display devices. From HDTVs to automotive displays, Mini LED PCBs play an important role in a variety of applications.
The manufacturing process of Mini LED PCB requires several key steps. It starts with substrate preparation, selecting suitable materials, and surface preparation to ensure good welding. Then there’s the precise placement of the Mini LED chips, usually done by automated pick-and-place machines. The last step is soldering and testing to ensure the functionality and reliability of the Mini LED PCB.
The emergence of Mini LED PCB brings many advantages to display technology. Due to the small size of Mini LED chips and uniform light emission, Mini LED displays can achieve higher brightness, contrast and energy efficiency. At the same time, the design of Mini LED PCB also provides greater flexibility and customizability, making it suitable for various display applications.
Overall, Mini LED PCB is a key technology that promotes innovation and progress in the display field. With the continuous development of Mini LED technology, it is believed that Mini LED PCB will play an increasingly important role in future display manufacturing.
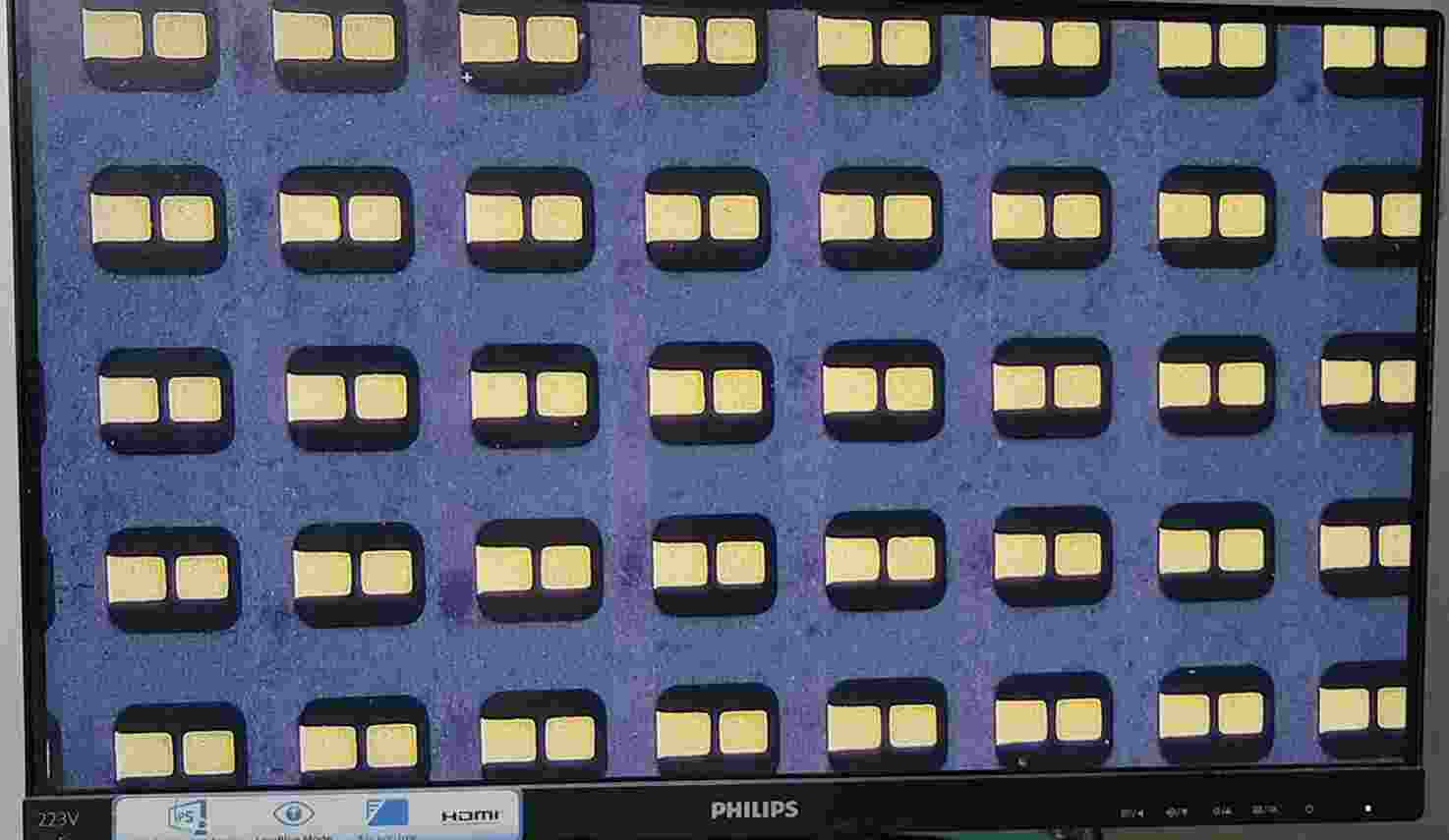
Mini led pcb(Black core and black soldermask)
How to Design a Mini led pcb manufacturing?
Designing micro LED PCB manufacturing usually requires the following key steps:
Circuit design: Design the circuit layout and connections according to the specifications and requirements of the LED lamp beads. Determine the number, arrangement and circuit connection of LEDs to meet design requirements.
PCB layout design: Design the layout of the PCB board based on the circuit design. Reasonably arrange the position and spacing of LED lamp beads, as well as the position of other components, to ensure a compact layout and good circuit connections.
PCB circuit connection design: Design the circuit connection method on the PCB board, including wire connection and welding methods. Consider the continuity and stability of the circuit to ensure reliable and durable connections.
PCB manufacturing process selection: Select the process and materials suitable for micro LED PCB manufacturing. Consider the thickness, material, solder mask, printing, metallization and other process requirements of the PCB board to select the appropriate manufacturing process.
PCB manufacturing file generation: According to the design requirements, generate the files required for PCB manufacturing, including Gerber files, drilling files, etc. Ensure manufacturing documents are consistent with design to ensure production accuracy.
PCB board manufacturing: Send the designed PCB file to the PCB manufacturer for PCB board production. Quality needs to be strictly controlled during the production process to ensure that the PCB board meets the design requirements.
Component installation: Install the LED lamp beads and other components on the PCB board according to the design requirements. Make sure the installation position is accurate and the welding is firm to ensure the connection of the LED lamp beads and the normal operation of the circuit.
Are the circuit connections normal? Make adjustments and corrections when necessary to ensure stable product quality and performance.
Through the above design steps and process flow, a micro LED PCB that meets the requirements can be successfully designed and manufactured for use in various small LED lamps and electronic equipment.
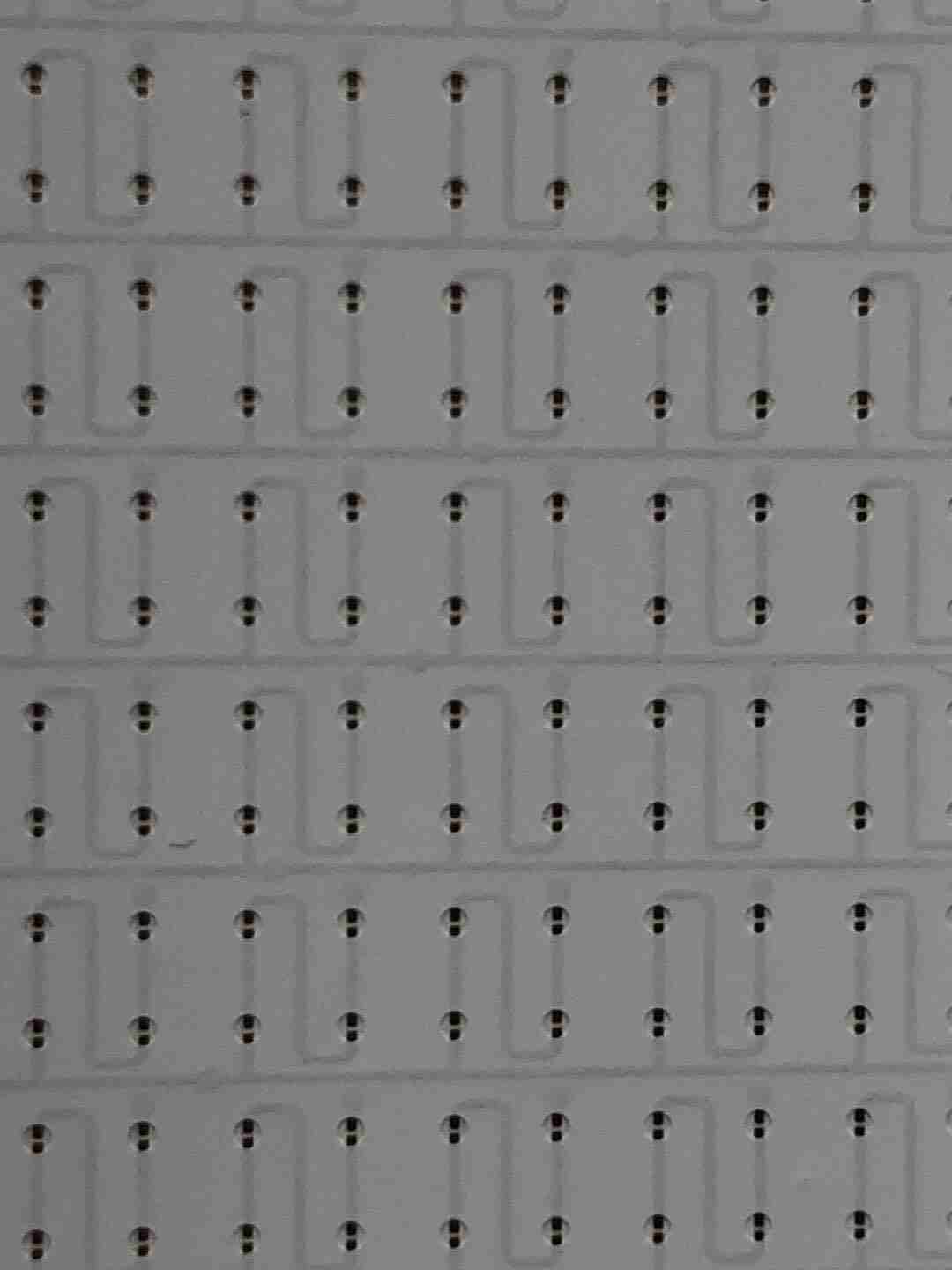
Mini led pcb(white core and white solder mask)
What is the manufacturing process of Mini LED PCB?
The manufacturing process of Mini LED PCB is critical because it directly affects the performance and reliability of Mini LED display technology. In Mini LED display technology, Mini LED PCB is a circuit board specially designed to accommodate a large number of Mini LED chips. They are considered the foundation of Mini LED displays as they provide the necessary support for the precise placement and connection of Mini LED components.
First, the manufacturing process of Mini LED PCB begins with the design phase. Engineers must plan the layout and routing precisely to ensure the correct placement and connection of Mini LED chips. This includes determining the number of Mini LEDs, their arrangement, and their relationship to other circuit components.
Next is the preparation of the substrate. Typically, Mini LED PCB uses high-quality substrate materials such as FR-4 fiberglass composite or flexible substrate materials such as polyimide. The substrate must be carefully processed and processed to ensure surface flatness and stability of electrical performance.
Then comes the precise placement of the Mini LED chips. This step is usually accomplished with the help of automated equipment, such as precision pick-and-place machines. These machines can accurately place Mini LED chips in designed positions, ensuring that the position of each chip is accurate.
Next comes the welding process. Mini LED chips must be soldered to the PCB surface to ensure a solid connection and good electrical performance. Commonly used welding technologies include surface mount technology (SMT) and hot air soldering technology (Reflow Soldering), which can ensure the stability and reliability of welding.
Finally comes testing and quality control. The soldered Mini LED PCB must undergo rigorous testing to verify whether its functionality and performance meet specification requirements. This includes electrical testing, optical testing, and temperature and humidity testing, among others. Only after passing all tests can the Mini LED PCB be considered a qualified product and can be put into use.
Overall, the Mini LED PCB manufacturing process requires precision design, high-quality materials, and strict quality control to ensure that the performance and reliability of the final product reach expected levels.
How to manufacturing a Mini led pcb manufacturing?
The manufacturing of micro LED PCB usually includes the following key steps:
Material preparation: Prepare the required PCB substrate, LED chips, conductive materials (such as copper foil), insulating materials and other components. Ensure material quality meets requirements and perform necessary cleaning and processing.
PCB design: Use circuit design software to design PCB layout and connections according to the specifications and layout requirements of the LED chip. Determine the location, quantity and arrangement of LED lamp beads, and design the circuit connection diagram.
Manufacturing file generation: Generate files required for PCB manufacturing according to design requirements, including Gerber files, drilling files, etc. These files will be used for production in the PCB manufacturing factory.
PCB board manufacturing: Send the designed PCB file to the PCB manufacturing factory for PCB board production. The production process includes cutting, cleaning, chemical treatment, photolithography, electroplating, drilling and other processes.
Hard and soft layout: According to the design requirements, the LED chips and other components are arranged and fixed according to the PCB layout diagram. The LED chip needs to be accurately welded on the PCB board to ensure a solid connection.
Soldering and connection: LED chips and other components are soldered to the PCB board through surface mount technology (SMT) or plug-in technology. Make sure the welding quality is good and the connection is solid and reliable.
Testing and debugging: Test and debug the manufactured micro LED PCB to check whether the brightness, color, circuit connection, etc. of the LED lamp beads are normal. Make adjustments and corrections when necessary to ensure stable product quality and performance.
Packaging and delivery: After completing testing and debugging, the micro LED PCB is packaged, marked with product information, and arranged for delivery to customers or downstream manufacturers.
Through the above manufacturing steps, micro LED PCBs that meet the requirements can be produced and used in various small LED lighting products and electronic equipment.
How Much Does a Mini led pcb manufacturing Cost?
The cost of micro LED PCB manufacturing depends on many factors, so it is difficult to give a specific cost figure. Here are some of the major factors that affect micro LED PCB manufacturing costs:
Material cost: including the cost of PCB substrate, LED chips, conductive materials, insulating materials and other components. The quality and specifications of the LED chip, the material and thickness of the PCB substrate, etc. will directly affect the manufacturing cost.
Production process cost: PCB manufacturing process includes cutting, cleaning, chemical treatment, photolithography, electroplating, drilling and other links. Each link has corresponding labor and equipment costs.
Labor cost: The production process requires operating equipment, welding, assembly and other processes, which all require labor costs. Labor costs depend on worker wage levels and working hours.
Equipment investment costs: The purchase and maintenance costs of production equipment such as PCB production lines and SMT equipment are also an important part of manufacturing costs.
Capacity utilization: The size of the production scale and capacity utilization will affect the production cost per unit of product. Low capacity utilization can lead to higher unit costs.
Quality control costs: Ensuring product quality and stability requires quality control and testing, which increases manufacturing costs.
To sum up, the cost of micro LED PCB manufacturing is affected by many factors. The specific cost depends on material cost, production process cost, labor cost, equipment investment cost, capacity utilization and quality control cost, etc.
What materials are Mini led pcb manufacturing Cost made of?
Micro LED PCB manufacturing usually uses the following main materials:
PCB substrate: The PCB substrate is the main body of the micro LED PCB and is usually made of glass fiber reinforced epoxy resin material. The material selection and thickness of the PCB substrate will affect the performance and stability of the product.
LED chip: The LED chip is the key component of the micro LED PCB and is used to emit light. The selection of LED chips affects the brightness, color, energy consumption and other performance indicators of the product.
Conductive material: Copper foil is usually used as a conductive material, covering the PCB substrate and used to connect LED chips and other components to form a circuit.
Insulating materials: In order to prevent circuit short circuits and protect components, the PCB substrate needs to be covered with insulating materials, such as solder resist ink, copper coating, etc.
Other components: In addition to LED chips, other components are also required on the micro LED PCB, such as resistors, capacitors, diodes, etc., for auxiliary circuit connection and control.
The above are the materials commonly used in micro LED PCB manufacturing. Together, they constitute the basic structure of micro LED PCB and ensure the performance and reliability of the product. By selecting appropriate materials and through reasonable design and manufacturing processes, high-quality micro LED PCB products can be produced.
Who manufactures Mini led pcb manufacturing?
When looking for reliable Mini LED PCB manufacturing services, our company offers customized solutions designed to meet the specific needs and requirements of our clients. As one of the industry’s leading suppliers, we are committed to providing customers with high-quality, high-performance Mini LED PCB solutions and ensuring advanced manufacturing processes and quality control.
We understand that each client’s needs are unique. Therefore, we provide customized Mini LED PCB manufacturing services to meet our customers’ specific application needs. Whether for HDTVs, automotive displays or other industry applications, we are able to provide customized solutions based on our customers’ requirements, ensuring optimal performance and applicability.
We use state-of-the-art manufacturing processes and equipment to ensure the accuracy and consistency of our Mini LED PCBs. From substrate preparation to precise placement of LED chips to soldering and testing, we strictly execute each manufacturing step to ensure product quality and reliability. Our processes are carefully designed to ensure a high-quality product that meets our customers’ expectations.
In order to ensure the quality of Mini LED PCB, we implement strict quality control measures. From the selection and inspection of raw materials to the monitoring and testing during production, we always pay attention to every detail. We are equipped with advanced testing equipment and technology, as well as an experienced quality control team, to ensure that each Mini LED PCB meets the highest quality standards.
As your trusted partner, our company is committed to providing you with high-quality Mini LED PCB manufacturing services to meet your needs and achieve your project goals. No matter what your needs are, we are dedicated to providing you with professional support and solutions.
What are 5 qualities of a good customer service?
Excellent customer service is crucial to the development of a business, not only improving customer satisfaction, but also building a good brand reputation and customer loyalty. Here are five qualities of great customer service:
Prompt response: Excellent customer service requires prompt response to customer needs and questions. Whether it’s a phone call, email or online chat, you should respond to customers in the shortest possible time to make them feel valued.
Expertise: Good customer service requires expertise and skills. Employees should have an in-depth understanding of the product or service, be able to accurately answer customer questions, and provide customers with professional advice and support.
Friendliness: Excellent customer service represents kindness and respect for customers. Employees should treat every customer with a cordial and polite attitude, listen patiently to customers’ needs and opinions, and work hard to solve problems so that customers feel cared for and warm.
Personalized care: Excellent customer service requires customized services based on the individual needs of customers. Understand customers’ preferences, historical purchase records and special requirements, and be able to give personalized suggestions and recommendations to enhance customer experience and satisfaction.
Continuous improvement: Good customer service is continually improved and improved. By collecting customer feedback and suggestions, we continuously optimize service processes and solutions to improve customer satisfaction and loyalty.
To sum up, good customer service should have the characteristics of prompt response, professional knowledge, friendly attitude, personalized care and continuous improvement. By continuously improving customer service levels, companies can establish a good brand image, win customer trust, and promote sustainable business development.
Frequently Asked Questions (FAQs)
Can Mini LED PCBs be customized for specific display applications?
Yes, Mini LED PCBs can be customized to meet the unique requirements of different display applications. Whether it’s for high-definition televisions, gaming displays, automotive screens, or other specialized uses, manufacturers offer customization options to tailor Mini LED PCBs to specific size, shape, and performance needs.
How do Mini LED displays compare to OLED displays in terms of performance and cost?
Mini LED displays offer advantages in terms of brightness, contrast, and energy efficiency compared to OLED displays. While OLED displays provide deeper blacks and wider viewing angles, Mini LED displays can achieve higher peak brightness levels and potentially lower production costs, especially for larger screens.
Are Mini LED displays suitable for outdoor applications requiring high brightness and durability?
Yes, Mini LED displays are well-suited for outdoor applications that demand high brightness and durability. Their superior brightness levels and robust construction make them suitable for outdoor digital signage, stadium screens, and other outdoor advertising or information displays, providing excellent visibility even in bright sunlight and harsh environmental conditions.