Semiconductor IC substrate Manufacturer, High TG, high speed or high frequency materials, low expansion and shrinkage coefficient materials, ultra-small marks, ultra-small spacing design. we produce this types IC/BGA substrates with high quality and fast lead time.
Semiconductor IC substrates play a crucial role in modern electronic devices, serving as essential elements that provide vital support for hosting various electronic components while establishing the basic framework for connecting and sustaining these components. Understanding the definition of a semiconductor IC substrate requires first grasping the concept of an “integrated circuit” (IC). An integrated circuit is a tiny electronic device that combines hundreds to billions of electronic components onto a single chip, including transistors, capacitors, resistors, and more. The semiconductor IC substrate serves as the foundational backbone for these microelectronic devices, supplying them with the necessary structure and connections.
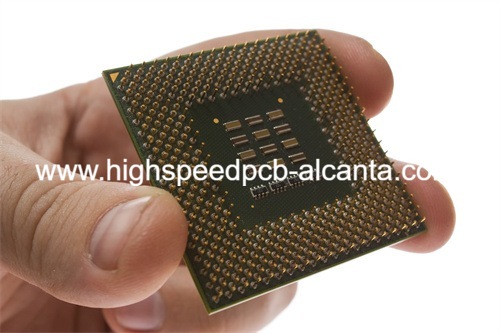
Semiconductor IC Substrate Manufacturer
Typically composed of conductive materials like silicon (Si), semiconductor IC substrates exhibit excellent electronic conduction properties. These substrates often feature intricate multi-layer structures, incorporating insulating layers, conductive layers, and connecting layers. These combined layers form a robust platform capable of hosting and interconnecting various types of electronic components. Furthermore, semiconductor IC substrates can be tailored to specific design specifications, adapting to diverse application scenarios and performance criteria.
In summary, semiconductor IC substrates play a critical role in modern electronics by offering essential support and interconnections for integrated circuits. They serve as the groundwork for the performance and functionality of electronic devices. Hence, a comprehensive understanding of the definition and functions of semiconductor IC substrates is imperative for grasping the fundamental principles of contemporary electronic technology.
What types of semiconductor IC substrate manufacturers are there?
Semiconductor IC substrate manufacturing involves various types, each with unique characteristics and applications. A prevalent type is rigid substrates, typically made from materials like fiberglass-reinforced epoxy (FR-4).
Flexible substrates, conversely, employ flexible materials such as polyimide (PI) or polyester film. Engineered to be pliable and versatile, these substrates are well-suited for tasks necessitating bending or folding, such as flexible displays and wearable devices.
This enables smaller spacing and higher line density, making them common in high-performance electronic devices like smartphones and tablets, allowing for more compact designs and meeting elevated performance requirements.
Rigid-flex boards combine rigid and flexible substrates, incorporating both types to address complex design needs. Often used in electronic devices requiring folding or bending, such as foldable mobile phones and medical equipment.
Metal substrates employ materials like aluminum and copper, leveraging their excellent heat dissipation and electromagnetic shielding properties. Widely used in applications demanding high power and frequency, such as LED lighting and automotive electronics, metal substrates are chosen for their specific advantages.
The diverse semiconductor IC substrates have distinct strengths and limitations in design, manufacturing, and application. The selection of the appropriate type hinges on specific application needs and design requirements.
What is the process of manufacturing semiconductor IC substrates?
The manufacturing process of semiconductor IC substrates involves several intricate and precise stages to guarantee the quality and performance of the final product. Here’s a breakdown of these steps:
Design Phase: Before production begins, there’s a design phase where engineers determine the structure, layout, and dimensions of the substrate according to customer specifications. Designers use specialized software for circuit and layout diagrams, performing simulations to ensure accuracy and feasibility.
Material Preparation: Following design, materials required for fabrication are prepared. This involves selecting suitable substrate materials, dielectrics, metal layers, etc., ensuring they meet quality standards as they significantly impact final product quality and reliability.
Manufacturing Process: The fundamental steps in manufacturing include:
Printed Circuit Board (PCB) Manufacturing: This involves generating circuit patterns and creating through-holes on the board through chemical processes or mechanical cutting, facilitating the connection of electronic components.
Metallization: This phase involves the application of metallic layers, commonly copper or silver, to guarantee conductivity and connectivity across the PCB.
Testing and Verification: After manufacturing, rigorous testing ensures the substrate meets design specifications and quality standards. This includes functional, reliability, and performance testing to verify product stability and reliability.
Final Inspection and Packaging: Qualified substrates undergo final inspection for appearance, dimensions, and defects. They are then appropriately packaged to safeguard against damage during transportation and use.
Each step demands advanced equipment and technical expertise to guarantee the final product’s quality and performance align with customer expectations and requirements.
In what fields are semiconductor IC substrates used?
Semiconductor IC substrates are a vital component of modern electronic products and are widely used in many key areas. The following are some major fields and the applications of semiconductor IC substrates in them:
Semiconductor IC substrates are integral components utilized across diverse sectors such as communication, medicine, automotive, industrial control, and military/aerospace. In communication, they facilitate the functioning of equipment like mobile phones, base stations, and satellite communication devices, ensuring data processing and transmission. Similarly, in medicine, they enable the precision required for devices such as heart rate monitors and medical imaging equipment, contributing to accurate diagnostics and treatments. Automotive systems, including engine control units and driving assistance systems, benefit from semiconductor IC substrates, ensuring reliable electronic control and sensor operation. Industrial control equipment such as PLCs and robot control systems rely on these substrates for efficient electronic control and data processing. Furthermore, in military and aerospace applications, semiconductor IC substrates provide the reliability and anti-interference capabilities essential for missile systems, radar systems, and spacecraft control systems to operate effectively in extreme environments. Overall, semiconductor IC substrates play a crucial role in advancing modern technology by providing stable circuit support and connectivity across a spectrum of electronic products and systems.
How to find a suitable semiconductor IC substrate manufacturer?
Utilize search engines and electronic component supplier directories to gather information on multiple semiconductor IC substrate manufacturers. These platforms offer detailed insights into company profiles, product ranges, and contact information, facilitating initial screening.
Seek recommendations and insights from industry insiders, experts, and peer companies operating within the same sector. Drawing upon their experiences with semiconductor IC substrate manufacturers can provide valuable insights for making informed decisions.
For critical suppliers, consider arranging on-site visits to their manufacturing plants. This allows for a firsthand understanding of production equipment, processes, and quality control systems. Visual assessments of production capabilities and quality levels can be invaluable.
Once relevant information has been gathered, it is imperative to conduct a meticulous evaluation and comparison. Key factors to consider include product quality, technical capabilities, delivery cycles, and after-sales service. This in-depth analysis ensures alignment with our company’s precise needs and standards, facilitating the selection of the most suitable manufacturer.
To summarize, the process of identifying an appropriate semiconductor IC substrate manufacturer involves a multifaceted approach. By amalgamating online research, active participation in industry events, soliciting word-of-mouth recommendations, carrying out on-site inspections, and undertaking thorough evaluations, our company can pinpoint the suppliers best suited to fulfill our specific needs and requirements.
What factors affect the quotation of semiconductor IC substrate manufacturers?
The pricing provided by semiconductor IC substrate manufacturers is influenced by various factors, which collectively determine the final cost and price. Familiarizing oneself with these factors is essential for selecting the most suitable manufacturer and establishing a budget. Here are the key considerations along with recommendations for obtaining comprehensive quote details:
Design Complexity: The complexity of the design significantly impacts manufacturing costs. More intricate designs necessitate greater engineering resources and advanced manufacturing expertise, consequently driving up costs. Features such as high density, multiple layers, and unique layout requirements contribute to increased expenses.
Material Selection: The choice of materials plays a crucial role in determining the quotation. Different materials possess distinct cost and performance characteristics. While high-performance materials tend to be more expensive, they offer superior electrical performance and reliability. Balancing cost considerations with desired performance is essential when selecting materials.
Production Scale and Quantity: Economies of scale come into play, wherein larger production volumes generally lead to lower costs per unit. Consequently, the customer’s order volume and delivery timeline influence the final quote. Bulk orders typically attract more competitive pricing due to efficiencies in mass production.
Technical Requirements and Manufacturing Processes: Specific technical requirements and manufacturing processes can drive up costs due to the need for specialized equipment and procedures. Manufacturers tailor their quotations based on the customer’s technical specifications and production processes involved.
To obtain detailed quotation information, it is advisable to reach out to multiple semiconductor IC substrate manufacturers. Providing comprehensive design specifications and requirements allows them to furnish project-specific quotations. Utilizing resources such as online search engines, industry exhibitions, and supply chain platforms facilitates the identification of additional manufacturers for comparison purposes. By evaluating multiple quotes from various sources, one can identify the manufacturer that best aligns with their requirements and budget constraints.
In summary, the pricing offered by semiconductor IC substrate manufacturers is influenced by factors such as design complexity, material selection, production scale, technical requirements, and manufacturing processes. Understanding these factors and actively seeking detailed quote information enables informed decision-making in selecting the appropriate manufacturer and establishing a realistic budget.
What common problems need to be solved in semiconductor IC substrate manufacturing?
What are the typical challenges in semiconductor IC substrate manufacturing?
Semiconductor IC substrate manufacturing often faces challenges related to material compatibility, design complexity, and process optimization. Ensuring precise alignment of multiple layers and achieving uniformity in material properties throughout the substrate are common issues.
What steps are taken to maintain alignment accuracy during fabrication?
To maintain alignment accuracy, manufacturers utilize sophisticated equipment such as photolithography systems and automated alignment tools. Additionally, meticulous process optimization and calibration are conducted to minimize deviations.
What role does design complexity play in the manufacturing process?
Complex designs pose challenges in terms of layout, routing, and interconnectivity. Balancing functionality with manufacturability is essential to avoid production delays and defects.
What are the challenges in meeting tight tolerances?
Meeting tight tolerances demands precise control over dimensions, thicknesses, and alignment during manufacturing. Deviations from specifications can lead to performance issues and component failures.
How do manufacturers address alignment issues during substrate manufacturing?
Manufacturers employ advanced alignment techniques, such as optical alignment systems and automated alignment algorithms, to achieve precise alignment of layers during substrate manufacturing.