Semiconductor Glass Substrate Manufacturer.As a semiconductor glass substrate manufacturer, we specialize in crafting precision-engineered substrates tailored to the exacting demands of modern electronics. Our expertise lies in the production of high-quality glass substrates that serve as the foundation for semiconductor devices, ensuring optimal performance, reliability, and efficiency in various applications.
Semiconducting glass substrates play a vital role in today’s electronics industry, especially in the manufacturing of printed circuit boards (PCBs). This article will delve into the key role of semiconductor glass substrates in PCB manufacturing, covering material properties, manufacturing processes, and advantages in various application fields. With the continuous advancement of technology, semiconductor glass substrates will continue to provide stable and reliable support for the development of the electronics industry.
What is Semiconductor Glass Substrate?
Semiconducting glass substrates are a key material used in the manufacture of electronic components and play an important role in modern microelectronics manufacturing. Compared with traditional substrate materials, such as FR-4 (fiberglass reinforced epoxy), semiconductor glass substrates have unique characteristics and advantages.
First, the surface of semiconductor glass substrates is highly smooth and uniform, which is one of its important advantages in microelectronics manufacturing. This flat surface helps maintain the accuracy and consistency of circuit patterns, ensuring the reliability and stability of electronic components. In addition, the highly smooth surface of the semiconductor glass substrate is also conducive to the implementation of micro-fabrication processes such as photolithography and etching, thereby achieving precise production of circuit patterns.
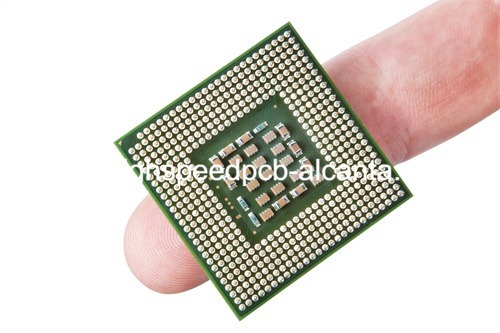
Semiconductor Glass Substrate Manufacturer
Secondly, semiconductor glass substrates are usually made of materials such as silicon or quartz, which have excellent mechanical properties and chemical stability. This allows the semiconductor glass substrate to withstand complex manufacturing processes and harsh working environments, such as high temperature, high pressure, etc. At the same time, the semiconductor glass substrate also has good corrosion resistance and oxidation resistance, which can effectively protect electronic components from damage to the external environment and extend their service life.
Overall, the unique properties of semiconductor glass substrates make them one of the most indispensable materials in the field of microelectronics manufacturing. With the continuous development of science and technology and the expansion of application fields, it is believed that semiconductor glass substrates will play an increasingly important role in the future and promote continued innovation and progress in the electronics industry.
Semiconductor Glass Substrate design Reference Guide.
Semiconductor glass substrates play a key role in modern electronic manufacturing, and their design is one of the important factors in ensuring PCB performance and reliability. The following are the main contents of the Semiconductor Glass Substrate Design Reference Guide:
Material selection: Choosing the right semiconducting glass material for a specific application is critical. Consider factors such as the material’s thermal conductivity, dielectric constant, mechanical strength, and chemical stability to ensure design stability and performance.
Substrate size: Determine the size of the semiconductor glass substrate based on application requirements and space constraints. Considering the manufacturing cost, heat dissipation effect and PCB layout, it is very important to choose the appropriate size.
Substrate layer thickness: The thickness of the substrate directly affects its mechanical strength and thermal conductivity. According to the design requirements and manufacturing process limitations, the appropriate substrate layer thickness is selected to ensure the stability and reliability of the design.
Substrate surface treatment: Surface treatment of semiconductor glass substrates is critical to the production of circuit patterns. Using appropriate surface treatment techniques, such as chemical mechanical polishing (CMP) or electrochemical polishing (ECMP), can ensure the smoothness and flatness of the substrate surface, thereby improving the accuracy and reliability of circuit patterns.
Circuit layout: When designing the circuit layout, factors such as signal transmission paths, power distribution, and heat dissipation layout should be considered. Reasonable circuit layout can minimize signal interference and power loss, and improve PCB performance and reliability.
Circuit pattern design: When designing circuit patterns, the characteristics of the semiconductor glass substrate and the limitations of the manufacturing process should be taken into consideration. Using processes such as photolithography and etching, circuit patterns are accurately made on the surface of the substrate to ensure the stability and performance of the circuit.
Heat and chemical resistance: Semiconductor glass substrates should have good heat and chemical resistance to accommodate various manufacturing and process conditions. During the design process, semiconductor glass materials with excellent heat and chemical resistance should be selected to ensure the stability and reliability of the design.
The Semiconductor Glass Substrate Design Reference Guide covers every aspect from material selection to circuit layout and is designed to help design engineers and manufacturers develop high-performance and reliable PCB designs. By following these guidelines, you can ensure the stability, performance, and reliability of your semiconductor glass substrate designs, driving growth and innovation in the electronics industry.
What material is used in Semiconductor Glass Substrate?
Semiconductor glass substrate is a key electronic material, and its manufacturing material is usually made of high-purity silicon (Si) or quartz (Quartz). These materials have excellent physical and chemical properties, making them ideal for manufacturing semiconductor devices and electronic components.
First of all, one of the commonly used materials for semiconductor glass substrates is silicon (Si). Silicon is a material widely used in the semiconductor industry because of its stable crystal structure, high mechanical strength, and good thermal conductivity. The preparation process of silicon substrates usually includes the growth and cutting of single crystal or polycrystalline silicon, and then through process steps such as chemical mechanical polishing (CMP) to obtain a glass substrate with high flatness and smooth surface.
Another common semiconductor glass substrate material is quartz. Quartz has excellent optical transparency, thermal stability, and chemical inertness, making it ideal for manufacturing high-performance optoelectronic devices and optical components. Quartz substrates are usually prepared through special quartz ore extraction and processing processes to ensure their high purity and stability.
Whether it is silicon substrate or quartz substrate, they are strictly processed and treated to ensure that their surface flatness and chemical purity meet the requirements. These properties make semiconductor glass substrates an indispensable material in the electronics industry and are widely used in semiconductor devices, optoelectronic devices, flat panel display devices and other fields.
What size are Semiconductor Glass Substrate?
The size of semiconductor glass substrates often depends on specific manufacturing needs and application scenarios. Semiconductor glass substrates generally come in a larger size range than traditional silicon substrates and can be customized according to customer requirements. Generally speaking, the size of semiconductor glass substrates can range from a few millimeters to tens of centimeters.
In microelectronics manufacturing, the dimensions of semiconducting glass substrates may vary depending on the application. For example, in integrated circuit manufacturing, smaller sized semiconductor glass substrates are often used to produce microchips and sensors. In the field of display device manufacturing, larger-sized semiconductor glass substrates are more common and are used to produce large-sized flat panel display devices.
In addition, the size of semiconductor glass substrates is also affected by manufacturing process and equipment limitations. With the advancement of manufacturing technology, modern semiconductor glass substrate manufacturing equipment can achieve more precise size control and processing, thus promoting the trend of diversification and increase in the size of semiconductor glass substrates.
Overall, semiconductor glass substrates are available in a wide range of sizes and can be customized and adjusted to specific manufacturing needs and application scenarios. With the continuous development of technology and the expansion of application fields, the size of semiconductor glass substrates will continue to play an important role and play an important role in various fields of the electronics industry.
The Manufacturer Process of Semiconductor Glass Substrate.
The manufacturing process of semiconductor glass substrates is a complex and precise process that requires multiple steps to complete. The following is a brief introduction to its main manufacturing processes:
The first step in the manufacturing process is substrate preparation. At this stage, the raw material (usually high-purity silicon or quartz) is cut into appropriately sized sheets. The sheets undergo high-temperature and chemical treatments to ensure surface smoothness and purity for subsequent processing.
After substrate preparation, grinding and polishing steps follow. During this process, the surface of the substrate is continuously ground and polished to achieve very high flatness and smoothness. This is a critical step in ensuring circuit patterning, as a flat surface facilitates even coating and patterning of the photoresist.
Photolithography is one of the key steps in fabricating circuit patterns on semiconductor glass substrates. In this process, a layer of photoresist is coated on the surface of the substrate, and then the designed circuit pattern is projected onto the photoresist through a photolithography machine. The photoresist is then developed to form a template for the circuit pattern.
After the photolithography is completed, the next step is the etching step. In this process, a chemical etchant is used to etch away the portions of the substrate that are not protected by the photoresist, exposing the conductive layer. This forms a conductive path for the circuit pattern.
After etching is complete, a layer of conductive material, usually metal (such as copper), needs to be deposited on the surface of the substrate. This layer of conductive material fills the gaps in the circuit pattern and forms a good connection with the substrate surface. Deposition of conductive layers is usually achieved using techniques such as chemical vapor deposition (CVD) or physical vapor deposition (PVD).
After the conductive layer is deposited, the substrate undergoes final processing and testing. At this stage, the substrate must be rigorously inspected and tested to ensure the quality and accuracy of the circuit pattern. Any defects or issues need to be repaired or adjusted promptly to ensure the quality and performance of the final product meets requirements.
The above is a brief introduction to the manufacturing process of semiconductor glass substrates. This sophisticated process requires highly specialized equipment and technical support to ensure the quality and performance of the final product meets customer needs and standards.
The Application area of Semiconductor Glass Substrate.
Semiconductor glass substrates play an important role in many fields, and their applications are wide and diverse. The following are the main applications of semiconductor glass substrates in different fields:
Electronic product manufacturing: Semiconductor glass substrate is one of the key materials for manufacturing electronic products. In consumer electronics such as smartphones, tablets, and laptops, semiconductor glass substrates are used as basic materials for PCBs (printed circuit boards) to provide stable support and electrical insulation properties.
Optical device manufacturing: Semiconductor glass substrates are widely used in optical device manufacturing due to their excellent flatness and optical transparency. For example, in optical devices such as lasers, fiber optic communication equipment, and camera modules, semiconductor glass substrates serve as carrier materials to help achieve high-precision assembly of optical components.
Biomedical field: Semiconductor glass substrates are used in the biomedical field to manufacture biosensors and diagnostic equipment such as biochips and laboratory kits. Its flatness and biocompatibility make it ideal for biomaterial immobilization, cell culture and other applications.
Microelectronics Manufacturing: In the microelectronics manufacturing process, semiconductor glass substrates are used as the base material for wafers used to manufacture integrated circuits (ICs) and microelectronic components. Its high thermal conductivity and chemical stability ensure the reliability and stability of microelectronic devices.
Solar cell manufacturing: Semiconductor glass substrate is used as the base material of solar cells to support and protect photoelectric conversion devices. Its high transparency and weather resistance make it an ideal encapsulation material for solar cell modules.
Automotive electronics: In automotive electronics, semiconductor glass substrates are used to manufacture key components such as vehicle electronic control modules and vehicle displays to ensure the reliability and stability of vehicle electronic systems.
To sum up, semiconductor glass substrates play an important role in many fields such as electronic product manufacturing, optical device manufacturing, biomedical fields, microelectronics manufacturing, solar cell manufacturing, and automotive electronics fields, providing technological innovation and innovation in all walks of life. development provides solid support.
What are the advantages of Semiconductor Glass Substrate?
Semiconductor glass substrates have many advantages in electronic manufacturing, the following are their main advantages:
Excellent thermal conductivity: The semiconductor glass substrate has excellent thermal conductivity and can effectively dissipate heat, helping electronic components maintain a stable operating temperature. This feature is particularly important for high-power electronic devices, which can effectively extend their service life and improve system reliability.
Highly flat surface: The surface of the semiconductor glass substrate is highly flat and can meet the requirements for precision processing in microelectronics manufacturing. This flat surface makes the fabrication process of semiconductor devices more precise, helping to improve the performance and reliability of circuits.
Excellent chemical stability: Semiconductor glass substrates have good chemical stability and can resist the effects of chemical corrosion and environmental changes on their performance. This allows the semiconductor glass substrate to maintain stable working conditions in harsh environments and is suitable for various application scenarios.
Low dielectric constant: The low dielectric constant of the semiconductor glass substrate reduces energy loss during signal transmission and improves the transmission rate and performance of the circuit. This is particularly important for high-frequency electronic devices and communication systems to ensure the stability and reliability of signal transmission.
Strong processability: Semiconductor glass substrates have good processability and can produce complex circuit patterns and structures through a variety of processing techniques. This makes semiconductor glass substrates suitable for various electronic manufacturing processes, providing broad space for innovative design and product development.
In general, semiconductor glass substrates have important application prospects in the field of electronic manufacturing due to their excellent thermal conductivity, high-precision processing, chemical stability and other characteristics, providing reliable support for the performance improvement and innovative development of electronic products.
FAQ
What is a semiconductor glass substrate?
Semiconductor glass substrate is a substrate material used in electronic component manufacturing that is highly smooth and uniform. It is usually made of materials such as silicon or quartz and has excellent mechanical properties and chemical stability, making it suitable for use in the field of microelectronics manufacturing.
What is the difference between semiconductor glass substrate and ordinary glass?
Compared with ordinary glass, semiconductor glass substrates have higher purity and uniformity, and their surfaces are smoother and flatter. In addition, it has excellent thermal conductivity properties and low dielectric constant, making it suitable for the manufacture of high-performance electronic devices.
What is the role of semiconductor glass substrate in PCB manufacturing?
In PCB manufacturing, semiconductor glass substrates are mainly used as carriers and supporting materials for circuit patterns. Through process steps such as photolithography and etching, the conductive layer is patterned on the surface of the substrate to form the circuit structure of the PCB.
What are the advantages of semiconductor glass substrates?
Semiconductor glass substrates have the advantages of high stability, high processing precision and good thermal conductivity. Its highly flat surface and fine processing technology can ensure the high-precision production of circuit patterns. At the same time, its excellent thermal conductivity helps dissipate heat from electronic components and improves the efficiency and stability of the entire system.