Semiconductor Glass Package Substrates Manufacturer.Semiconductor Glass Package Substrates Manufacturer.A leading provider in the realm of Semiconductor Glass Package Substrates Manufacturer, our company stands at the forefront of innovation and precision engineering. With a commitment to excellence, we craft substrates that form the backbone of cutting-edge semiconductor devices, enabling the seamless integration of electronic components. Our state-of-the-art facilities employ advanced techniques to ensure superior quality and reliability in every substrate produced. Through relentless research and development, we continually push the boundaries of possibility, driving forward the evolution of semiconductor technology. Trust us as your partner in realizing the next generation of electronic solutions.
In modern electronic equipment, semiconductor glass package substrates (Semiconductor Glass Package Substrates) play a vital role. As a key component that connects electronic components and provides electrical connections, it is critical to understand the design, manufacturing and application of semiconductor glass packaging substrates. In this article, we will delve into all aspects of semiconductor glass packaging substrates, from concept to practice, giving you a comprehensive understanding of this key technology. You will learn about the definition of semiconductor glass packaging substrates, design principles, manufacturing processes, application areas, cost factors, manufacturer selection, and key attributes of excellent customer service.
What is the definition of semiconductor glass packaging substrate?
Semiconductor glass packaging substrate is a critical electronic component used to connect and support semiconductor chips. In short, it provides a stable platform that allows the chip to work reliably and communicate with other electronic components. Modern electronic devices such as smartphones, computers, automobiles and medical equipment widely use semiconductor glass packaging substrate technology.
Before understanding the semiconductor glass packaging substrate, let us first understand the semiconductor chip. Semiconductor chips are tiny circuit boards made of materials such as silicon and inlaid with many tiny electronic components, such as transistors and capacitors. These chips are usually very thin and therefore require a stable substrate to support and connect them, which is where semiconductor glass packaging substrates come in.
Semiconductor glass packaging substrates are usually composed of several layers of different materials, including glass substrates, metal wires, and insulating layers. The glass substrate provides a stable support platform, metal wires are used to connect the electronic components on the chip, and the insulating layer is used to isolate signals between different circuits to prevent interference and short circuits.
Designing semiconductor glass packaging substrates requires sophisticated engineering and design techniques. Engineers must consider factors such as circuit routing, signal integrity, and thermal management to ensure design stability and performance. Advanced CAD tools and simulation technology make the design process more efficient and accurate, and also provide strong support for optimized design.
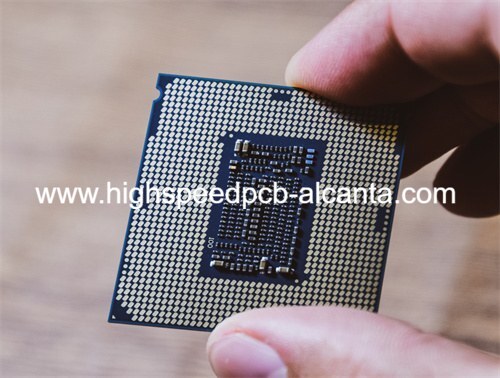
Semiconductor Glass Package Substrates Manufacturer
Once the design is complete, manufacturing a semiconductor glass packaging substrate involves multiple complex process steps. This includes substrate preparation, glass covering, metallization and final testing. Every step is critical, and a mistake at any point could lead to an unstable or unreliable product.
Overall, semiconductor glass packaging substrates play a vital role in the modern electronics industry. It not only provides the function of supporting and connecting chips, but also provides critical support for the performance and stability of electronic devices. Therefore, it is crucial for both electronic engineers and manufacturers to have an in-depth understanding and mastery of the design and manufacturing technology of semiconductor glass packaging substrates.
How is the semiconductor glass packaging substrate designed?
Designing semiconductor glass packaging substrates is a complex project that requires precise planning and meticulous operations. This task involves several critical steps, each of which has a significant impact on the performance and reliability of the final product. Below we will delve into the design process of semiconductor glass packaging substrates.
First, before the design process begins, the design team needs to understand the requirements and goals of the project in detail. This includes determining the circuit’s functionality, performance requirements, operating environmental conditions, and other special needs. By communicating with the client and other stakeholders, the design team can ensure that their understanding of the project is accurate and can provide the client with a satisfactory solution.
Once the project requirements are clear, the design team can begin circuit layout planning. During this stage, they determine the location and connection of various components on the circuit board to maximize the performance and reliability of the circuit. Factors such as signal integrity, electromagnetic compatibility (EMC), and thermal management need to be considered during the layout planning process to ensure that the circuit can operate stably under a variety of operating conditions.
Next is the schematic design stage, where the design team will convert the circuit layout plan into specific schematics. At this stage, they use electronic design automation (EDA) software tools to create circuit diagrams and perform the necessary simulation and verification. Through simulation analysis, the design team can evaluate the performance of the circuit and make necessary adjustments and optimizations to the design.
Once the schematic design is complete and verified, the design team can begin work on the wiring design. During this stage, they determine the paths for individual wires and connections on the circuit board and perform routing planning. Wiring design needs to consider factors such as signal integrity, impedance matching, and interference suppression to ensure that the circuit can operate stably and meet design requirements.
Finally, the design team generates the final PCB design files and submits them to the manufacturing team for production. During the manufacturing process, they closely monitor production progress and conduct necessary quality control and inspection. Once the PCB is manufactured, the design team performs final testing and verification of the finished product to ensure it meets customer requirements and standards.
In general, designing semiconductor glass packaging substrates is a complex and precise project that requires the design team to have extensive experience and expertise. By deeply understanding the project requirements, carefully planning the design process, and performing the necessary simulations and verifications, design teams can ensure that the solutions they deliver will meet customer requirements and be successful in the market.
What is the manufacturing process of semiconductor glass packaging substrates?
The manufacturing process of semiconductor glass packaging substrates involves multiple complex process steps, from the preparation of raw materials to final inspection and packaging, each step is critical. Let’s take a closer look at the process.
First, the first step in manufacturing a semiconductor glass packaging substrate is to prepare the substrate material. Typically, the substrate is made of glass material, which has good thermal conductivity and mechanical strength. These glass substrates must undergo rigorous screening and inspection to ensure quality meets requirements.
Next comes substrate handling and cleaning. At this stage, the substrate surface undergoes a special chemical treatment and cleaning process to remove surface contaminants and impurities and provide good adhesion.
Once the substrate is ready, the patterning stage begins. This involves transferring the designed circuit pattern to the substrate surface. The commonly used technology is photolithography or imaging, which uses photosensitive materials and masks to project a pattern onto a substrate, and uses a chemical etching process to remove unwanted parts.
Then comes the metallization process, which is to create a conductive layer on the surface of the substrate. Commonly used metals include copper, nickel and gold, which can form thin films on the surface of substrates through electroplating or other chemical deposition techniques. These metal layers will be used to connect and conduct electricity.
This is followed by hole machining and metallization. At this stage, the required holes are formed on the substrate through chemical etching or mechanical drilling to facilitate interlayer connection and welding. A metal layer is then also formed inside the hole to ensure electrical connection.
Finally comes the final inspection and packaging. At this stage, the manufactured semiconductor glass packaging substrate is comprehensively inspected and tested through methods such as optical microscopy, X-ray inspection, and electrical testing to ensure that the quality meets standards. It is then packaged for protection and ease of shipping.
Overall, the manufacturing process of semiconductor glass packaging substrates requires a high degree of precision and expertise, and each step cannot be ignored. Through strict quality control and continuous technological innovation, manufacturers are able to produce high-quality, reliable semiconductor glass packaging substrates to meet the needs of different applications.
In what fields can semiconductor glass packaging substrates be used?
Semiconductor glass packaging substrates have a wide range of applications in today’s electronics industry, and their functions and properties make them one of the indispensable components in many fields. Here are some application examples in the main areas:
In communication equipment, semiconductor glass packaging substrates play a key role and are used to manufacture various types of communication equipment, including routers, switches, optical fiber communication equipment, etc. Due to their high degree of integration and reliability, these devices are able to provide stable and efficient data transmission in complex communication networks.
In computer and server systems, semiconductor glass packaging substrates are used to connect and support processors, memory and other critical components. These substrates feature highly dense wiring and reliable signal transmission, ensuring that systems can maintain stable operation under high loads and pressures.
Electronic systems have become increasingly common in modern vehicles, from engine controls to safety systems. Semiconductor glass packaging substrates are widely used in the manufacture of automotive electronic modules, such as engine control units (ECUs), in-car entertainment systems and driver assistance systems. These substrates provide reliable performance in harsh environmental conditions, ensuring vehicle safety and stability.
In the medical industry, semiconductor glass packaging substrates are used to manufacture a variety of medical devices, including medical imaging equipment, patient monitoring systems, and surgical instruments. These devices require highly precise electronic control and data processing, and semiconductor glass packaging substrates can meet these requirements and provide stable and reliable performance.
In the field of industrial automation, semiconductor glass packaging substrates are widely used to manufacture various types of control systems and sensors. These substrates enable high-speed data transmission and precise control, helping factories improve production efficiency and product quality.
Overall, semiconductor glass packaging substrates play an important role in many key areas, and their stability, reliability and high performance make them an indispensable component of modern electronic devices.
How high is the cost of semiconductor glass packaging substrate?
The cost of semiconductor glass packaging substrates is one of the key factors that need to be carefully considered during the design and manufacturing process. The level of cost not only affects the profitability of manufacturers, but also directly affects product pricing and market competitiveness. So, what factors determine the cost of semiconductor glass packaging substrates?
First, a major component of cost is material cost. The manufacture of semiconductor glass packaging substrates requires the use of a variety of materials, including substrate materials, conductive layers, insulating layers and covering layers. The prices of different materials vary greatly, and different application scenarios may have different requirements for material performance, which will also have an impact on costs.
Secondly, the manufacturing process is another important factor affecting the cost. The manufacturing of semiconductor glass packaging substrates involves multiple complex process steps, such as substrate preparation, glass covering, metallization and final testing. Each process step requires the investment of resources such as manpower, equipment, and energy, and different process technologies may have different cost-effectiveness.
In addition, economies of scale are also one of the important factors affecting costs. Large-scale production often reduces manufacturing costs per unit of product because fixed costs can be spread over more products. Therefore, the size of the production batch has a direct impact on costs.
Finally, technology level and innovation capabilities will also have an impact on costs. As technology advances and innovation drives, new manufacturing processes and materials may reduce costs and increase production efficiency. Manufacturers need to constantly update equipment and processes to maintain a competitive advantage and meet market demand.
To sum up, the cost of semiconductor glass packaging substrates is affected by many factors, including material selection, manufacturing process, production scale and technological innovation. Understanding these factors and properly controlling costs is crucial for manufacturers to help them become more competitive and achieve sustainable development.
Who will manufacture the semiconductor glass packaging substrate?
Who will manufacture the semiconductor glass packaging substrate? This is a crucial issue because the quality of semiconductor glass packaging substrates directly affects the performance and reliability of electronic devices. Before answering this question, let’s understand what impact manufacturers have on the production process of semiconductor glass packaging substrates.
Manufacturers are key players within a company who bear the responsibility of transforming designs into actual products. At our company, we have an experienced manufacturing team focused on the production of semiconductor glass packaging substrates. Not only do they have profound technical skills, but they also have advanced equipment and process technology to ensure that we can provide high-quality products.
Our manufacturing team plays a key role in the manufacturing process of semiconductor glass packaging substrates. They oversee every stage of production, from material procurement to final testing, ensuring products meet strict quality standards. We use advanced production technology, such as automated assembly lines and precision processing equipment, to improve production efficiency and product consistency.
In addition to technical strength, our manufacturing team also focuses on innovation and continuous improvement. They constantly seek new manufacturing technologies and process optimizations to improve product quality, reduce costs and shorten lead times. Through close cooperation with customers and suppliers, we continuously optimize our production processes to meet changes in market demand and customers’ special requirements.
In the process of manufacturing semiconductor glass packaging substrates, we always put quality first. We strictly follow international standards and industry best practices, and conduct strict quality control and testing on each production batch. Our goal is to win the trust and satisfaction of our customers through high-quality products and excellent services.
Overall, manufacturers play a vital role in the production process of semiconductor glass packaging substrates. At our company, we have a professional manufacturing team dedicated to providing high-quality products and services. Whether it’s small batch customization or mass production, we have the ability to meet our customers’ needs and support their success.
What are the five key attributes of great customer service?
High-quality customer service is one of the keys to business success, and in the semiconductor glass packaging substrate industry, providing high-quality customer service is even more critical. Here are five key qualities of great customer service:
Professionalism: In the semiconductor glass packaging substrate industry, professionalism is the cornerstone of providing quality customer service. Businesses need to have a team of technical experts and customer service specialists who can understand customer needs and provide professional solutions. They need to have solid product knowledge and industry experience to ensure customers receive accurate and timely technical support and advice.
Prompt Response: Fast, timely response is an important part of great customer service. When customers face technical problems or emergencies, they need to be able to contact the company in a timely manner and obtain timely solutions. Therefore, companies need to establish an efficient communication mechanism to ensure that customer problems can be solved quickly, thereby improving customer satisfaction and loyalty.
Personalized care: Understanding customer needs and providing personalized care is the key to improving customer service quality. Enterprises should establish close working relationships with customers, understand their business needs, preferences and challenges, and provide customized solutions and support. Through personalized care, businesses can enhance customer trust and loyalty, leading to long-term relationships.
Problem Solving Skills: Excellent customer service requires excellent problem solving skills. Businesses should be able to quickly and accurately identify customer problems and take effective measures to resolve them. This requires the team to have good analytical and problem-solving skills to ensure that customer needs are met and expected results are achieved.
Continuous Improvement: Continuous improvement is one of the key drivers of quality customer service. Enterprises should constantly collect customer feedback and suggestions, analyze trends in customer satisfaction and demand changes, and adjust and improve their service strategies and processes accordingly. Through continuous improvement, companies can continuously improve customer service quality, establish closer cooperative relationships with customers, and maintain competitive advantages in a fiercely competitive market.
In short, providing high-quality customer service is one of the keys to the success of semiconductor glass packaging substrate companies. Through five key attributes: professionalism, timely response, personalized care, problem solving and continuous improvement, companies can meet customer needs, improve customer satisfaction, enhance competitiveness, and achieve long-term sustainable development.
FAQs
How widely is the use range of semiconductor glass packaging substrates?
Semiconductor glass packaging substrates are widely used in communications, computers, medical, automotive and other fields. They are used not only in consumer electronics such as smartphones, tablets and laptops, but also in professional fields such as medical equipment, automotive electronic systems and industrial control equipment.
What factors need to be considered in the design of semiconductor glass packaging substrates?
When designing semiconductor glass packaging substrates, factors such as signal integrity, power consumption distribution, thermal management, EMI/EMC (electromagnetic interference and compatibility) need to be considered. Proper design considering these factors can ensure the stability, reliability and performance of the circuit.
How long does the manufacturing process of semiconductor glass packaging substrates take?
The time to manufacture semiconductor glass packaging substrates depends on the manufacturer’s equipment and process flow. Typically, it can take weeks or even months from design to delivery of the final product. However, in some emergency situations, methods such as expedited production may be adopted to shorten the cycle.
How to choose a suitable semiconductor glass packaging substrate manufacturer?
Choosing the right manufacturer is key to ensuring product quality and production efficiency. When selecting a manufacturer, you should consider its reputation in the industry, manufacturing capabilities, technical level, and whether it has certification to meet quality standards. In addition, communication and cooperation with manufacturers are also very important to ensure that the needs and expectations between both parties can be effectively communicated and met.
How to reduce the cost of semiconductor glass packaging substrates?
Methods to reduce costs include optimizing design, selecting appropriate materials, improving production efficiency, and seeking the most cost-effective manufacturing solutions. Through reasonable cost control strategies, production costs can be reduced without affecting product quality and performance.