Semiconductor BGA substrate Manufacturer, the best small BGA Ball pitch 100um. the minimum Trace width are 9um, the minimum spacing are 9um. the minimum via holes size are 50um. This is the minimum production data. please try to design the data as big as better. the price will be not same.
Semiconductor BGA (Ball Grid Array) substrate is one of the crucial components in modern electronic systems. Not only are they the basis for mounting and connecting semiconductor devices, they also play an important role in providing electrical connections and thermal management. Among electronic devices pursuing miniaturization, semiconductor BGA substrates are favored for their compact footprint.
First, let us understand the role of semiconductor BGA substrate in electronic systems. These substrates allow semiconductor chips to be mounted on their surface and connected to a printed circuit board (PCB) by soldering. This connection is essential because it provides the electrical connection between the chip and the circuit board, allowing signal and power transfer.
In addition to electrical connections, the semiconductor BGA substrate also plays a key role in thermal management. In many electronic devices, the heat generated by semiconductor devices can affect their performance and reliability. Through a well-designed BGA substrate, heat can be effectively conducted and dispersed to ensure that the device operates within the appropriate temperature range.
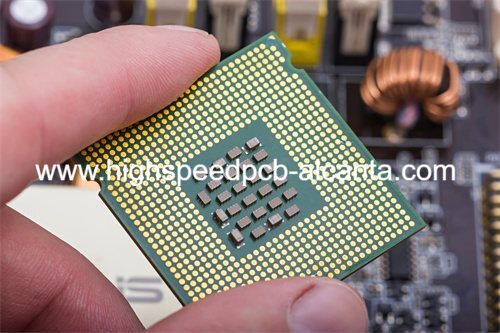
Semiconductor BGA Substrate Manufacturer
In addition, the compact design of semiconductor BGA substrates makes them ideal for miniaturized electronic devices. As technology advances and market demand increases, the demand for smaller, lighter, and more portable devices continues to increase. The miniaturized design of the BGA substrate enables the overall device size to be effectively reduced, thus meeting this demand.
To sum up, semiconductor BGA substrate plays a vital role in electronic systems. Not only do they provide electrical connections and thermal management, they also provide critical support for the realization of miniaturized electronic devices. As technology continues to advance, semiconductor BGA substrates will continue to play an important role in the electronics industry.
What are the types of semiconductor BGA substrates?
In the field of electronic packaging, there are various types of semiconductor BGA substrates, each with its own unique advantages and applicable scenarios. Let’s explore these types together:
Made from organic materials such as FR-4 or BT resin, this type of substrate provides a cost-effective and flexible solution. Due to relatively low material costs, organic substrates are often used in cost-sensitive applications. Their flexibility also gives them an advantage in certain designs.
The ceramic substrate is made of ceramic material with high thermal conductivity and reliability. This makes ceramic substrates ideal for demanding applications that require high thermal management and reliability. For example, ceramic substrates can provide better performance and stability in high temperatures or extreme environments.
Metal core substrates incorporate a metal core to improve thermal dissipation and mechanical stability. This type of substrate is commonly used in applications with high thermal management requirements, such as high-power LED lighting, automotive electronics and power modules. The design of the metal core substrate can effectively conduct heat to the external environment, thus maintaining the stability of the device.
Flexible substrates offer greater design flexibility, allowing them to fit around curves or space-constrained environments. This type of substrate is typically made from materials such as flexible polyester or polyimide, which have high bending and tensile properties. Flexible substrates are commonly used in fields such as mobile devices, flexible displays, and medical equipment, and can achieve smaller and lighter designs.
By understanding these different types of semiconductor BGA substrates, design engineers can better select the substrate type that suits their project needs, optimizing design performance and cost-effectiveness.
What are the advantages of semiconductor BGA substrate?
Semiconductor BGA substrates show many advantages in modern electronic packaging, making them an indispensable key component in electronic design. The following are the main advantages of semiconductor BGA substrates:
Efficient thermal dissipation: For high-power semiconductor devices, effective thermal management is critical. Through the optimization of its structure and materials, the semiconductor BGA substrate can effectively dissipate heat, effectively disperse and discharge the heat generated by the device, and help maintain the stability and performance of the device.
Improve electrical performance: By optimizing design and material selection, semiconductor BGA substrates can reduce signal loss and impedance mismatch, thereby improving electrical performance. Good signal integrity and electrical characteristics ensure reliability and stability in high-speed communication and data transmission.
Compact form factor: Semiconductor BGA substrates have a compact form factor, enabling denser packaging and smaller electronic devices. This compact design helps improve product integration and performance while saving space, making the product more lightweight and portable.
Improved reliability and durability: Semiconductor BGA substrates are precisely designed and rigorously tested to provide excellent reliability and durability. Its materials and construction resist the effects of harsh environments, ensuring stable performance and functionality over long periods of operation. This reliability is critical for critical applications such as aerospace, medical equipment and industrial control systems.
To sum up, the semiconductor BGA substrate has become an ideal choice in modern electronic design due to its efficient thermal management, optimized electrical performance, compact size and reliable performance, providing stable and reliable solutions for various applications.
What is the manufacturing process of semiconductor BGA substrate?
The manufacturing process of semiconductor BGA substrates involves multiple key steps, each step is crucial and directly affects the quality and performance of the final product.
The first is the substrate preparation stage. At this stage, manufacturers need to carefully select and prepare suitable substrate materials. These materials are typically high-quality substrates such as organic, ceramic or metal core substrates. Selecting the appropriate substrate material depends on the requirements of the specific application, such as factors such as thermal management, electrical performance, and cost.
Next comes the layer building process. During the layer building stage, conductive and insulating layers are deposited and formulated on the substrate. The design and layout of these layers are determined based on the requirements of the circuit design. Conductive layers are used to connect semiconductor devices and other components, while insulating layers are used to isolate different circuit layers to prevent short circuits and interference.
Then comes the interconnect formation step. At this stage, the manufacturer creates solder balls or bumps on the substrate to connect the semiconductor device to the substrate. These solder balls or bumps act as electrical and mechanical bridges, ensuring a solid connection between the device and the substrate.
The last step is the surface treatment stage. Surface treatment is to improve the corrosion resistance and solderability of the substrate. This includes applying various chemical treatments or metallic coatings to protect the substrate surface from environmental influences and ensure the reliability and stability of the welding process.
To sum up, the manufacturing process of semiconductor BGA substrate is a delicate and complex process that requires careful design and strict control. By optimizing each critical step, manufacturers can ensure the production of semiconductor BGA substrate products with high quality, reliability and performance.
What are the application fields of semiconductor BGA substrates?
As the core component of electronic packaging, semiconductor BGA substrate plays an important role in all walks of life. Their application range covers many fields, including but not limited to:
In the field of consumer electronics, semiconductor BGA substrates are widely used in products such as smartphones, tablets, and wearable devices. These devices require compact, high-performance electronic solutions, and BGA substrates provide an ideal solution, allowing devices to achieve higher performance and smaller size.
The automotive industry’s demand for electronic technology continues to grow, and semiconductor BGA substrates play a vital role in this field. They are used in key components such as engine control units, infotainment systems and advanced driver assistance systems (ADAS), providing reliable electrical connections and high-performance data processing capabilities.
In the aerospace and defense sectors, the need for highly reliable and high-performance electronic equipment is particularly important. Semiconductor BGA substrates play a key role in applications such as avionics, radar systems and satellite communications, ensuring stable operation of the system and efficient data transmission.
The manufacturing of medical devices requires stringent reliability and accuracy, and semiconductor BGA substrates meet these requirements. They are widely used in key components such as implantable medical devices, diagnostic equipment and patient monitoring systems, helping the medical industry achieve higher levels of treatment and monitoring capabilities.
Telecom equipment needs to process large amounts of data and signals, and semiconductor BGA substrates can provide efficient electrical connections and data processing capabilities. They are used in key equipment such as network routers, base stations and optical fiber transceivers to ensure the stability and reliability of communication networks.
To sum up, semiconductor BGA substrates are widely used in various fields, provide important support for the performance and functions of modern electronic equipment, and play a key role in promoting technological development and innovation.
Where to find semiconductor BGA substrate manufacturers?
When looking for a semiconductor BGA substrate manufacturer, you have several avenues to choose from. First, you can check out industry directories, which often list information on a variety of electronics manufacturers and suppliers, including semiconductor BGA substrate manufacturers. Secondly, you can search in the online market, many electronic parts suppliers offer their products and services online. Finally, you can also ask professional suppliers directly to find out whether they provide semiconductor BGA substrate manufacturing services.
When selecting a semiconductor BGA substrate manufacturer, there are several key factors to consider. The first is quality and reliability. Make sure that the manufacturer you choose has a good reputation and meets industry standards and quality control requirements to ensure that the semiconductor BGA substrates produced are of consistent quality and reliability. Second is the ability to customize. Ensure that the manufacturer can provide a customized solution based on your project needs to meet your specific needs and requirements. Finally, communication is also very important when working with suppliers. Ensure a good working relationship with the manufacturer and be able to communicate and resolve any issues that may arise in a timely manner.
In this regard, our company can also be one of your choices when looking for semiconductor BGA substrate manufacturers. We are committed to providing high quality, reliability and customization capabilities for semiconductor BGA substrate manufacturing services. We have an experienced team and advanced manufacturing equipment to meet your various project needs. Whether you need standardized products or customized solutions, we can provide you with professional support and services.
What is the quotation for semiconductor BGA substrate?
As the core component of modern electronic packaging, the quotation of semiconductor BGA substrate is affected by many factors, including material, size, complexity and quantity. Therefore, it is important to understand how these factors affect costs and how to obtain an accurate quote.
The material selection of semiconductor BGA substrate directly affects its cost. For example, ceramic substrates may be more expensive than organic substrates, but have higher thermal conductivity and reliability, so their cost increases accordingly.
The size of the substrate is also an important factor in determining cost. Larger substrate sizes typically consume more material and increase manufacturing costs. Therefore, an increase in substrate size may result in an increase in cost.
Substrate complexity includes factors such as hierarchical structure, circuit density, and number of solder balls. More complex substrates may require more production steps and more elaborate manufacturing processes, and therefore cost relatively more.
Costs will also differ between mass production and low-volume production. Generally speaking, mass production can enjoy the advantages of economies of scale and lower unit costs. Small batch production may require more customization work, so the unit cost will be relatively high.
The cost of semiconductor BGA substrates is affected by many factors, including material, size, complexity and quantity. By fully understanding these cost factors and communicating with multiple manufacturers, an accurate quote can be obtained and strong support can be provided for the implementation of the project.
Frequently Asked Questions (FAQs)
Are Semiconductor BGA Substrates suitable for high-power applications?
Absolutely. These substrates excel in high-power scenarios due to their efficient thermal management, ensuring optimal performance and reliability for semiconductor devices in demanding applications.
How do the different types of Semiconductor BGA Substrates cater to specific needs?
The various types, such as organic, ceramic, metal core, and flex substrates, cater to diverse requirements. Organic substrates provide flexibility and cost-effectiveness, while ceramic substrates excel in high thermal conductivity applications.
What factors influence the cost of Semiconductor BGA Substrates?
The cost varies based on factors such as material type, size, complexity, and order quantity. Requesting a quote from manufacturers with detailed specifications will provide a more accurate cost estimate.
Can Semiconductor BGA Substrates be customized for specific project requirements?
Yes, many manufacturers offer customization options to tailor Semiconductor BGA Substrates according to specific project needs, ensuring optimal compatibility and performance.
How do manufacturers ensure the reliability of Semiconductor BGA Substrates?
Reputable manufacturers implement rigorous quality control measures, including testing for thermal performance, electrical connectivity, and overall durability, ensuring the reliability of Semiconductor BGA Substrates.