RT/duroid® 5880 Laminates PCB Manufacturer.RT/duroid® 5880 Laminates PCB Manufacturer is renowned for its cutting-edge fabrication of high-quality printed circuit boards (PCBs). Specializing in RT/duroid® 5880 laminates, the company exemplifies excellence in electronic component manufacturing. With a dedication to precision and reliability, they craft PCBs tailored to meet diverse industrial needs. Their advanced technology ensures optimal performance and durability, making them a trusted choice for clients worldwide. From concept to execution, they prioritize innovation and efficiency, delivering products that drive progress in various sectors. Trust RT/duroid® 5880 Laminates PCB Manufacturer for top-tier PCB solutions that empower technological advancement.
RT/duroid® 5880 laminates play a key role in modern electronics. Its excellent performance and wide range of applications make it popular. This article will delve into the unique properties and manufacturing process of RT/duroid® 5880 laminate, giving you a comprehensive understanding of the importance of this material in PCB design and manufacturing.
What is a RT/duroid® 5880 Laminates PCB ?
RT/duroid® 5880 laminate plays an integral role in modern electronics. This high-performance material is favored for its unique properties and wide range of applications. In PCB (Printed Circuit Board, printed circuit board) design and manufacturing, RT/duroid® 5880 laminate has demonstrated excellent performance and reliability, providing a solid foundation for the manufacturing of high-frequency electronic equipment.
The unique properties of RT/duroid® 5880 laminate are mainly reflected in its high dielectric constant and low dissipation factor. This makes it excellent in high-frequency applications such as communication systems, radar technology and satellite communications. The high dielectric constant ensures the stability and reliability of signal transmission, while the low loss factor minimizes signal loss and ensures signal clarity and accuracy.
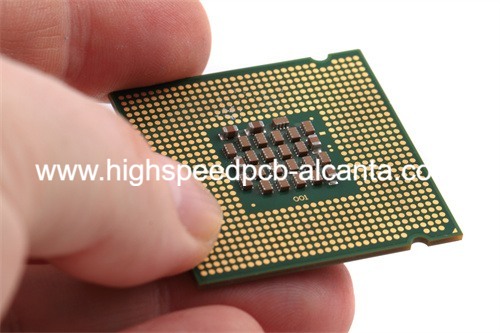
RT/duroid® 5880 Laminates PCB Manufacturer
In addition, RT/duroid® 5880 laminate also has excellent dimensional stability and high temperature resistance, allowing it to maintain stable working conditions in extreme environments. This property is particularly important in applications that require long-term stability and reliability, such as electronic equipment in the aerospace and defense sectors.
In PCB design and manufacturing, the application of RT/duroid® 5880 laminate provides engineers with greater design freedom and flexibility. Its excellent electrical properties make it possible to design circuits with wider bandwidth and faster speed, thus meeting the needs of modern high-speed communication and data transmission. At the same time, the manufacturing process of RT/duroid® 5880 laminate is precisely controlled to ensure the quality and consistency of each board.
In summary, RT/duroid® 5880 laminate has become an important part of modern electronic equipment manufacturing due to its excellent performance and reliability. Its wide application in PCB design and manufacturing has injected new vitality and power into the development of the electronics industry. As technology continues to advance and innovate, RT/duroid® 5880 laminate will continue to play an important role in driving the electronics industry forward.
How to Design a RT/duroid® 5880 Laminates PCB ?
When designing PCBs with RT/duroid® 5880 laminates, engineers must consider multiple factors to ensure the final design achieves optimal performance levels. Here are some important design considerations:
The substrate thickness of RT/duroid® 5880 laminate is one of the key parameters in the design. The choice of substrate thickness directly affects the mechanical strength, electrical characteristics and cost of the PCB. For high-frequency applications, the substrate thickness is usually thinner to reduce signal transmission delays and losses. However, for specific application scenarios, engineers may need to weigh thickness and other factors to achieve optimal performance and reliability.
Conductor geometry is critical to signal transmission and impedance control. During the design process, engineers need to ensure that parameters such as wire width, spacing, and layer spacing meet design specifications to achieve expected impedance matching and signal transmission characteristics. Using advanced CAD tools, engineers can precisely adjust conductor geometry to meet design requirements and optimize performance.
In high-frequency circuits, impedance matching is one of the key factors to ensure signal transmission quality. RT/duroid® 5880 laminates have consistent dielectric constants and dissipation factors, making them excellent at impedance matching. Engineers can use simulation tools to perform impedance matching analysis and optimize impedance matching by adjusting parameters such as line width, line spacing, and layer spacing to ensure stable signal transmission and minimal signal loss.
In addition to impedance matching, engineers also need to conduct a thorough analysis of signal integrity. This includes considering factors such as signal transmission delays, crosstalk, power transfer, and signal reflections. By utilizing advanced simulation tools for signal integrity analysis, engineers can identify potential problems and take appropriate measures to optimize the design to ensure stable transmission and reliability of signals.
In summary, designing a PCB with RT/duroid® 5880 laminate requires considering multiple factors such as substrate thickness, conductor geometry, impedance matching, and signal integrity. By leveraging advanced design software and simulation tools, engineers can optimize signal performance, minimize losses, and ensure the highest levels of functionality and efficiency in designs.
What is the RT/duroid® 5880 Laminates PCB Fabrication Process?
The manufacturing process of RT/duroid® 5880 laminate is a complex and precise process involving highly specialized techniques and careful operations. From material selection to final assembly, every step is critical to ensure the final product meets the highest quality standards and performance requirements.
First, manufacturing PCBs with RT/duroid® 5880 laminates requires precise material selection. RT/duroid® 5880 laminate is composed of high-performance polytetrafluoroethylene (PTFE) dielectric material and glass fiber reinforced polymer substrate. These materials must undergo strict quality control and screening to ensure their stability and reliability.
The manufacturing process then involves multiple steps including lamination, etching, drilling and gold plating. During the lamination process, raw materials are bonded into a multi-layer structure through the action of pressure and temperature to form a complete laminate. The etching and drilling steps are used to create complex circuit patterns and holes on the board, requiring highly sophisticated equipment and process control.
During the manufacturing process, every step must be carefully executed with strict quality and precision control. Utilizing advanced facilities and manufacturing technologies, such as automated production lines, precision control systems and strict quality inspections, manufacturers of RT/duroid® 5880 laminates are able to ensure product consistency and stability.
Finally, the assembly step combines the fabricated laminate with other electronic components to form a complete PCB. This process requires highly skilled operations and precision workmanship to ensure that the quality and performance of the assembly meet expected requirements.
Overall, the manufacturing process of RT/duroid® 5880 laminate is a comprehensive process that requires exquisite technology and strict quality control. Through careful material selection, precision manufacturing processes and advanced equipment, manufacturers of RT/duroid® 5880 laminates are able to provide quality products that exceed industry expectations and provide customers with reliable solutions.
How to Manufacturer a RT/duroid® 5880 Laminates PCB ?
The manufacturing process of RT/duroid® 5880 laminate is a precise and complex process that requires experienced technicians and advanced equipment to ensure the quality and performance of the final product. Below we will introduce the manufacturing process of RT/duroid® 5880 laminate in detail:
Material Preparation: The first step in manufacturing RT/duroid® 5880 laminate is preparing the required materials. This includes high-performance polytetrafluoroethylene (PTFE) dielectric sheets and fiberglass-reinforced polymer substrates. These materials must undergo strict quality controls to ensure they meet specifications.
Lamination: In the lamination process, sheets of PTFE dielectric and fiberglass-reinforced polymer substrates are stacked together in an alternating pattern. This stacked structure provides the desired properties of RT/duroid® 5880 laminates, such as high dielectric constant and low dissipation factor. The lamination process must be carried out under controlled temperature and pressure conditions to ensure good bonding of the materials.
Cutting: Once lamination is complete, the sheets will be cut to the desired size. This is usually done using a CNC cutting machine to ensure that the size and shape of the panels are accurate.
Etching: Next, the metal foil layer on the board is etched according to the design requirements. This step uses a chemical etchant to remove unwanted portions of the metal foil to create the desired circuit pattern.
Drilling: After etching is complete, the board will be drilled to facilitate the connection of circuits between different layers through the holes. These holes must be precisely positioned and drilled to ensure reliable and stable circuit connections.
Metallization: After drilling is completed, the sheet will be metallized to form circuit connections. This usually involves plating a layer of metal, such as copper or nickel, on the surface of the board to enhance the electrical conductivity of the circuit.
Final Inspection: The final step in the manufacturing process is final inspection of the RT/duroid® 5880 laminate. This includes checking that the size, shape and circuit connections of the board meet design requirements and verifying its performance and reliability through necessary testing.
By strictly controlling the quality and precision of each manufacturing step, RT/duroid® 5880 laminate manufacturers are able to produce products that meet the highest standards and meet the needs of a variety of high-frequency applications.
How Much Does a RT/duroid® 5880 Laminates PCB Cost?
Cost is a crucial consideration during the PCB design and manufacturing process. While RT/duroid® 5880 laminate offers excellent performance and reliability, it may cost slightly more than traditional materials. However, a comprehensive consideration of long-term return on investment suggests that RT/duroid® 5880 laminate may be a wiser choice.
First, the excellent performance of RT/duroid® 5880 laminate can improve product reliability and durability. Due to its high dielectric constant, low dissipation factor and excellent dimensional stability, RT/duroid® 5880 laminate is suitable for a variety of high-frequency applications such as communications, radar systems and satellite communications. This means that the product can not only maintain stable performance over long-term use, but also reduce maintenance and repair costs, thus saving additional expenses.
Second, the long-term benefits of RT/duroid® 5880 laminate far exceed the initial investment. Although its cost is higher, its excellent performance can increase the market competitiveness of products and bring more business opportunities and benefits to enterprises. By improving product quality and performance, companies can better meet customer needs and establish a good brand reputation, thereby attracting more customers and partners and further expanding business scale.
Finally, by partnering with a reputable RT/duroid® 5880 laminate manufacturer, engineers can optimize cost-effectiveness without sacrificing quality. These manufacturers have the experience and expertise to provide customized solutions to meet the unique needs of their customers. By choosing the right manufacturer, engineers can minimize costs while ensuring product quality and performance are not compromised.
In summary, while the cost of RT/duroid® 5880 laminate may be slightly higher, its superior performance and long-term benefits far outweigh the initial investment. Through reasonable cost management and cooperation with reputable manufacturers, engineers can maximize cost-effectiveness and achieve a win-win situation in product quality and performance.
What materials are RT/duroid® 5880 Laminates PCB made of?
RT/duroid® 5880 laminate is an exceptional performance material consisting of a high-performance polytetrafluoroethylene (PTFE) dielectric material and a fiberglass-reinforced polymer substrate. This special combination gives RT/duroid® 5880 laminate excellent electrical properties and mechanical strength, making it ideal for high-frequency electronic applications.
The process of manufacturing RT/duroid® 5880 laminates involves several critical steps, each requiring a high degree of precision and expertise. First, the polytetrafluoroethylene (PTFE) dielectric material and the glass fiber reinforced polymer substrate are laminated according to the design requirements to ensure the uniformity and stability of the material. Then, through etching technology, the unnecessary parts are peeled off, leaving the desired circuit pattern. Next is the drilling process, which uses high-precision equipment to drill holes at designated locations for subsequent metallization. Finally, through a gold plating process, a metal layer is covered on the surface of the circuit pattern to provide conductivity and protection.
The key to the RT/duroid® 5880 laminate manufacturing process is its precision and accuracy. Each step requires strict control and monitoring to ensure that the final product meets design specifications and has excellent performance. Because RT/duroid® 5880 laminates are often used in high-frequency applications such as communications and radar systems, the accuracy and stability of their circuit patterns are critical, requiring excellence in every detail of the manufacturing process.
Overall, RT/duroid® 5880 laminates are renowned for their unique combination of materials and precision manufacturing processes. Its excellent electrical properties and mechanical strength make it the material of choice for high-frequency electronic applications, providing a solid foundation for the development of modern technology.
Who manufactures RT/duroid® 5880 Laminates PCB ?
The manufacture of RT/duroid® 5880 laminate is a precision process that requires deep expertise and advanced manufacturing technology. Our company (here you can enter your company name) is a highly respected and leading manufacturer in this field.
As a company with extensive experience and a reputation for excellence, we are committed to providing the highest quality RT/duroid® 5880 laminate products that meet our customers’ demands for high performance and reliability. Our manufacturing process strictly follows industry standards and incorporates the latest manufacturing technology and precision equipment to ensure that each product meets the strictest quality requirements.
Our professional team consists of experienced engineers and technicians who have deep industry knowledge and professional skills to ensure that every project is carefully designed and precision manufactured. We not only provide RT/duroid® 5880 laminate products in standard specifications, but also provide customized solutions according to customers’ specific requirements to meet the needs of various application scenarios.
Our company adheres to the concept of customer first and always wins the trust and support of customers with high-quality products and excellent services. We are not only committed to the quality of our products, but also focus on communication and cooperation with our customers to ensure that their needs are fully met.
Through unremitting efforts and continuous innovation, our company has become one of the leaders in the field of RT/duroid® 5880 laminate manufacturing, and will continue to be committed to providing customers with better products and services, promoting the development and development of the electronics industry progress.
What are 5 qualities of a good customer service?
In the PCB manufacturing industry, excellent customer service is a key factor in ensuring customer satisfaction and business success. RT/duroid® 5880 laminate manufacturers understand this and are committed to providing an excellent customer experience. Here are the key customer service attributes of RT/duroid® 5880 laminate manufacturers:
Professionalism: RT/duroid® 5880 laminate manufacturers focus on professionalism, and their team members are professionally trained and possess rich industry knowledge and skills. They understand their clients’ needs and provide professional advice and solutions to ensure the best business results.
Responsiveness: In a fast-paced business environment, timely response to customer needs is critical. RT/duroid® 5880 laminate manufacturers handle customer inquiries and requests in an efficient and agile manner, ensuring customers receive timely feedback and support.
Personalized Care: Every customer is unique, and RT/duroid® 5880 laminate manufacturers know this. They are committed to building close relationships with their customers, understanding their needs and expectations, and providing personalized service and support to meet their specific requirements.
Problem-solving ability: Problems and challenges will inevitably be encountered in business operations, and RT/duroid® 5880 laminate manufacturers are problem-solving oriented. They have extensive experience and expertise and are able to quickly identify and resolve issues to ensure clients’ benefits are maximized.
Continuous Improvement: RT/duroid® 5880 laminate manufacturers are committed to continuously improving their customer service systems. They actively listen to customer feedback and suggestions and take action to improve them. Through continuous learning and improvement, they continue to improve customer service levels and provide customers with a better experience.
In summary, RT/duroid® 5880 laminate manufacturers demonstrate excellent customer service attributes in terms of professionalism, responsiveness, personalized care, problem solving and continuous improvement. Their continuous efforts are aimed at ensuring customer satisfaction and loyalty and staying ahead in the highly competitive market.
FAQS
How does RT/duroid® 5880 laminate compare to other PCB materials?
RT/duroid® 5880 laminates perform well in high-frequency applications, with high dielectric constant and low loss factor, which makes them more stable in signal transmission and suitable for applications with higher frequency requirements. RT/duroid® 5880 laminate offers better performance and reliability than traditional materials.
What are the key considerations when designing with RT/duroid® 5880 laminate?
When designing a PCB with RT/duroid® 5880 laminate, key considerations include substrate thickness, conductor geometry, impedance matching and signal integrity. Engineers need to utilize advanced design tools and simulation software to optimize designs to ensure optimal performance and efficiency.
How to optimize cost-efficiency when using RT/duroid® 5880 laminates in designs?
While RT/duroid® 5880 laminates may have a higher cost, engineers can achieve cost-effective optimization by optimizing the design, selecting the right manufacturer, and considering the benefits of long-term performance and reliability. It is important to consider all aspects of the design, materials and manufacturing process to achieve the best cost effectiveness.
Are there specific design guidelines for using RT/duroid® 5880 laminate in high frequency applications?
Yes, specific design guidelines are required for use with RT/duroid® 5880 laminates for high frequency applications. This includes considering factors such as impedance matching, signal integrity, electromagnetic compatibility, and more. Engineers need to follow the design specifications and recommendations provided by the manufacturer to ensure the reliability and performance of the design.