Rogers Cavity PCB Manufacturing.Rogers Cavity PCB Manufacturing specializes in crafting intricate printed circuit boards (PCBs) with precision and reliability. With advanced technology and a skilled team, they engineer PCBs featuring cavity structures, ideal for compact electronic devices requiring superior performance. Rogers’ proprietary manufacturing process ensures optimal signal integrity and thermal management, vital for high-frequency applications. Their commitment to quality extends to every stage, from design consultation to final production, ensuring clients receive PCBs that meet the most demanding specifications. Trust Rogers Cavity PCB Manufacturing for cutting-edge solutions in the realm of electronics and telecommunications.
In the world of modern electronics, Rogers Cavity PCBs stand out for their important role in advanced circuits. These specialized printed circuit boards (PCBs) play a vital role in high frequency applications, providing superior performance and reliability. In this comprehensive guide, we’ll dive into the intricacies of Rogers Cavity PCB manufacturing, exploring the details of the design process, manufacturing techniques, material selection, and more.
What is Rogers Cavity PCB?
Rogers Cavity PCB, also known as Rogers High Frequency PCB, is a special circuit board designed for high frequency applications. Their unique structure includes a dielectric material encapsulated inside the board layer, creating a cavity that helps control impedance and reduce electromagnetic interference.
In today’s electronics industry, with the rapid development of communication technology and the widespread application of wireless communication systems, radar systems and radio frequency (RF) equipment, the demand for high-frequency PCBs is growing day by day. Rogers Cavity PCB is a professional solution designed for this demand.
The unique feature of Rogers Cavity PCB is its special cavity structure. In a traditional PCB, the hierarchical structure of the circuit board is composed of multiple layers of copper foil and insulation layers. In Rogers Cavity PCB, in addition to these conventional hierarchical structures, a cavity encapsulated with dielectric material is also added. The existence of this cavity makes the structure of the circuit board more complex, but it also provides a more ideal environment for the transmission of high-frequency signals.
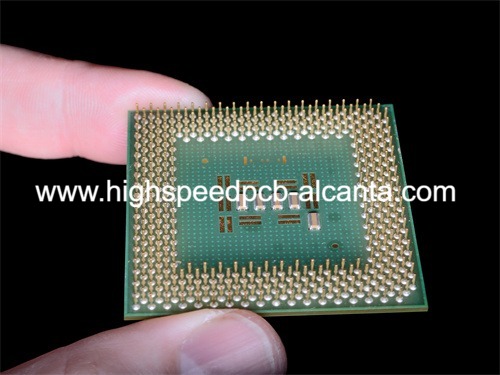
Rogers Cavity PCB Manufacturing
This cavity creates a fixed dielectric constant between the layers of the circuit board, helping to control the speed and impedance of signals. At the same time, it can also reduce signal radiation and absorption, reduce the degree of electromagnetic interference, and improve the stability and reliability of the circuit. This design makes Rogers Cavity PCB the first choice in high-frequency applications, especially in areas that require fast signal transmission speed and high stability.
In general, Rogers Cavity PCB is a professional circuit board that performs well in high-frequency applications. Its unique cavity structure provides an ideal environment for signal transmission, making it useful in communications, radar, radio frequency equipment and other fields. Broad application prospects.
How to design Rogers Cavity PCB?
Designing Rogers Cavity PCB is a complex and precise task, requiring engineers to have in-depth understanding of high-frequency principles and rich experience. During this process, they utilize advanced PCB design software, such as Altium Designer or Cadence Allegro, to implement all aspects of the design.
First, engineers must carefully analyze the circuit’s requirements, including frequency range, signal speed, power requirements, and requirements for electromagnetic compatibility. Based on these parameters, they determine the optimal layer stack structure to ensure signal integrity and electromagnetic compatibility.
Next, engineers begin laying out circuit traces, vias, and component locations. They need to precisely position each component and design an optimal layout to minimize signal transmission path length and electromagnetic interference. During the layout process, they also consider factors such as thermal management, signal isolation, and EMI suppression to ensure optimal overall performance.
Optimizing signal integrity is one of the key points in the design process. Engineers use simulation tools to simulate the working conditions of the circuit and adjust parameters to ensure stable signal transmission. This may involve adjusting parameters such as trace width, spacing, and layer spacing to meet specific impedance requirements and minimize signal attenuation and crosstalk.
In addition, engineers also need to consider electromagnetic coupling issues. By adopting appropriate inter-layer connection methods, ground layer design and electromagnetic shielding measures, they can effectively reduce electromagnetic interference and ensure the stability and reliability of the circuit.
After the design is completed, engineers will conduct strict verification and testing to ensure that the design meets the requirements. This may include steps such as SI/PI simulation, prototype verification, and electrical testing to verify the performance and reliability of the circuit.
To sum up, designing Rogers Cavity PCB requires engineers to have in-depth professional knowledge and extensive experience to ensure high performance and reliability of the design. Through careful design and strict verification, engineers can provide customers with high-quality PCB solutions to meet their high-frequency circuit needs.
What is the manufacturing process of Rogers Cavity PCB?
How does the manufacturing process of Rogers Cavity PCB ensure its optimal performance and reliability? We’ll delve deeper into this issue below.
First, before manufacturing Rogers Cavity PCB, a critical step is to prepare the substrate material. This process requires the selection of high-quality substrate materials, such as Rogers Corporation’s specialty laminates, such as RO4000 series and RO3000 series. These materials have stable dielectric properties and excellent high-frequency characteristics, laying a solid foundation for the performance of the final product.
Next comes the lamination process. In this step, the individual layers of the multilayer substrate are bonded together to form the complete panel structure. This process requires the use of high-temperature and high-pressure equipment to ensure strong bonding between the layers and the stability of the overall structure.
This is followed by etching of the circuit pattern. In this step, the designed circuit pattern is transferred to the surface of the board through chemical etching or mechanical etching. This requires precise control and highly accurate operations to ensure the accuracy and clarity of circuit patterns, thereby guaranteeing the performance of the final product.
Strict tolerance control and impedance control are critical throughout the entire manufacturing process. In order to ensure the stability and reliability of Rogers Cavity PCB, dimensional tolerances in each process must be precisely controlled and constant impedance maintained during lamination and etching. To do this, specialized equipment and technology are required to meet the demanding process standards.
Overall, manufacturing Rogers Cavity PCB is a complex and delicate process involving multiple critical steps and specialized techniques. Through strict quality control and highly accurate operations, we can ensure that the final product has excellent performance and reliability and meets the requirements of various high-frequency applications.
How are Rogers Cavity PCBs manufactured?
Manufacturing Rogers Cavity PCB requires a series of precise and complex process steps to ensure that the final product has excellent performance and reliability. From initial material preparation to quality verification of the final product, every link is critical and requires advanced technology and experienced craftsmanship.
First of all, before manufacturing Rogers Cavity PCB, the raw materials must be carefully selected and prepared. High-quality substrate materials, such as Rogers Corporation’s specialty laminates, are one of the key factors in ensuring PCB performance. The choice of materials directly affects the electrical characteristics, signal transmission efficiency and overall reliability of the PCB.
Once the materials are ready, the manufacturing process moves into the actual production phase. This stage involves many complex process steps and requires a high degree of technical and process support. Experienced technical personnel supervise every link on the production line to ensure that every detail of the product meets strict requirements.
Drilling is one of the key steps in manufacturing Rogers Cavity PCB. Precise hole location and aperture diameter are critical to ensure circuit board performance. During the drilling process, advanced CNC drilling machines and high-speed drill bits are used to ensure that the location and size of the holes meet the design requirements.
Next is the copper plating step, which is used to form a conductive layer on the surface of the PCB. By depositing copper material on the PCB surface, it ensures the electrical conductivity of the circuit board and provides a good foundation for subsequent circuit wiring.
Solder capping and surface preparation are the last two critical steps in manufacturing Rogers Cavity PCBs. The application of solder cap layer can protect the circuit board from the influence of the external environment and improve its durability and stability. Surface treatment can improve soldering performance and ensure reliable connection between PCB and other components.
Strict quality control measures are integral throughout the entire manufacturing process. By using advanced inspection equipment and technologies, such as optical inspection and X-ray inspection, it is possible to ensure that the dimensional accuracy, signal integrity and overall functionality of PCBs meet standard requirements. Any potential defects are promptly discovered and resolved during the production process to ensure the quality and reliability of the final product.
To sum up, manufacturing Rogers Cavity PCB requires advanced technology and skilled craftsmanship to ensure that the product has excellent performance and reliability. Through strict quality control and professional production processes, we can provide customers with high-quality PCB solutions to meet their needs in high-frequency circuit applications.
How much does a Rogers Cavity PCB cost?
Although Rogers Cavity PCBs offer unparalleled performance, they often cost more than traditional PCBs. This is mainly due to the increased cost caused by the special materials and manufacturing processes used in Rogers Cavity technology. Let’s take a closer look at the cost components of Rogers Cavity PCB and the factors that affect the cost.
First of all, material selection is one of the key factors that determine the cost of Rogers Cavity PCB. Rogers Corporation’s high-performance laminates, such as the RO4000 Series and RO3000 Series, are known for their superior electrical performance and stability, but they come at a relatively high price. The cost of these high-performance materials can be higher compared to traditional FR4 substrates.
Secondly, board complexity also has a significant impact on cost. As circuit design complexity increases, such as multi-layer stacking, high-density wiring, and special shape requirements, process and time costs in the manufacturing process increase accordingly. These factors will drive up the manufacturing cost of Rogers Cavity PCB.
In addition, manufacturing quantity is also one of the important factors affecting costs. Typically, volume production of Rogers Cavity PCBs results in lower unit costs because production line setup costs can be spread over more boards. But for low-volume production or sample manufacturing, the cost per board may be higher.
Despite the higher cost of Rogers Cavity PCBs, investments in this technology often bring significant returns. First, excellent signal integrity and stability can improve circuit performance and reduce signal distortion and interference, thereby improving product quality and reliability. Secondly, due to Rogers Cavity PCB’s high-quality materials and precision manufacturing processes, its product life is generally longer, reducing maintenance and replacement costs.
To sum up, although the cost of Rogers Cavity PCB may be higher, the advantages in high performance, reliability and long-term return on investment are often worth it. By considering factors such as material selection, board complexity and manufacturing quantity, and selecting the right manufacturing partner, companies can maximize the cost-benefit ratio of Rogers Cavity PCB and achieve commercial success.
What materials are used in Rogers Cavity PCB?
Rogers Cavity PCB is an important component in high-frequency applications, and its excellent performance is inseparable from carefully selected materials. When designing and manufacturing Rogers Cavity PCBs, choose the right
The material is crucial because it directly affects the performance and stability of the circuit board. These materials need to have excellent electrical properties to ensure stable signal transmission at high frequencies and have sufficient stability to cope with different working environments and temperature changes.
Rogers Cavity PCB uses a range of specialized materials, the most prominent of which are high-performance laminates produced by Rogers. The most famous series include RO4000 series and RO3000 series. These laminates are highly regarded for their superior performance, especially in high-frequency applications.
The RO4000 series is a polytetrafluoroethylene (PTFE) substrate with extremely low dielectric loss and stable dielectric constant, making it ideal for high-frequency applications. Its excellent signal retention and low distortion characteristics make it an ideal choice for wireless communications, radar systems, and radio frequency transmission.
RO3000 series substrates, on the other hand, feature glass fiber reinforced PTFE substrates with excellent dielectric properties and mechanical strength, making them suitable for high-speed digital and high-frequency analog applications. These substrates excel in high-speed data transmission and digital signal processing.
Overall, the material selection for Rogers Cavity PCB is based on strict requirements for high-frequency performance and stability. RO4000 series and RO3000 series laminates are the materials of choice for Rogers Cavity PCB manufacturing due to their low dielectric loss, stable performance and wide range of applications. These excellent materials ensure that Rogers Cavity PCB can provide reliable performance in high-frequency environments and meet various demanding application requirements.
Who makes Rogers Cavity PCBs?
In the field of Rogers Cavity PCB manufacturing, it is crucial to find a manufacturer with a good reputation and strong professional skills. Some well-known manufacturers specialize in the manufacturing of Rogers Cavity PCB. They rely on years of experience and technology accumulation to provide advanced solutions for a variety of demanding applications. These manufacturers are recognized for their commitment to innovation, quality and customer satisfaction, making them the preferred partner for businesses looking for high-performance PCB solutions.
As one of the manufacturers of Rogers Cavity PCB, our company is committed to providing the highest quality products and services. We have advanced production equipment and a professional technical team to meet our customers’ various needs for high-performance PCBs. We focus on technological innovation and quality control, and constantly introduce the latest manufacturing technologies and processes to ensure the stability and reliability of our products.
As a manufacturer, we always focus on customer needs, actively listen to customer feedback and suggestions, constantly optimize products and services, and provide customers with customized solutions. We know that customer satisfaction is the key to our success, so we are committed to establishing long-term and stable cooperative relationships and growing together with our customers.
By cooperating with our company, customers can safely leave the manufacturing of Rogers Cavity PCB to us and enjoy high-quality, high-performance products and professional technical support. We will wholeheartedly provide customers with the best quality services and create a better future with them.
What are the key attributes of great customer service?
In Rogers Cavity PCB manufacturing, excellent customer service is the key to success. For manufacturers, providing excellent customer service means not only meeting customer needs, but also establishing long-term relationships and laying the foundation for mutual growth and success. Here are the key attributes for great customer service in this area:
Clear Communication: During the Rogers Cavity PCB manufacturing process, clear communication is fundamental to ensuring a smooth project. Manufacturers should promptly communicate information about order status, production progress, and any important changes to customers to ensure that customers are always informed of the progress of the project.
Response to customer needs: Timely response to customer needs is the core of excellent customer service. Manufacturers should always remain flexible, adapt based on customer requests and feedback, and proactively find solutions to meet customer needs.
Technical Expertise: In the field of Rogers Cavity PCB manufacturing, technical expertise is crucial. Manufacturers should have extensive industry experience and expertise, be able to provide the technical support and advice customers need, and play an active role in solving complex problems.
On-time and reliable delivery: Ensuring on-time delivery is an important factor in building customer trust. Manufacturers should develop reasonable production plans and ensure that every link in the production process is effectively managed to ensure that orders can be delivered on time.
Positive problem-solving attitude: Manufacturers should demonstrate a positive problem-solving attitude when facing challenges and difficulties. They should be willing to listen to customer feedback and opinions and proactively find solutions to ensure customer satisfaction and trust.
By prioritizing these attributes, manufacturers can build strong relationships with their customers to jointly drive growth and success in Rogers Cavity PCB manufacturing. In this highly competitive market, providing great customer service not only helps manufacturers stand out, it can also win them more business and word of mouth. Therefore, ensuring excellent customer service is always crucial for any manufacturer committed to success in the Rogers Cavity PCB field.
Frequently Asked Questions
What are the advantages of Rogers Cavity PCBs over traditional PCBs?
Rogers Cavity PCBs offer several advantages over traditional PCBs. Firstly, they provide enhanced performance at high frequencies due to their specialized design, which includes a cavity structure that minimizes signal loss and electromagnetic interference. Additionally, Rogers Cavity PCBs exhibit superior thermal stability, making them suitable for applications where temperature fluctuations are common. Moreover, their excellent dimensional stability ensures consistent performance over time, contributing to the overall reliability of electronic systems.
How does the cavity design contribute to improved performance in Rogers Cavity PCBs?
The cavity design in Rogers Cavity PCBs plays a crucial role in optimizing performance, particularly at high frequencies. By encapsulating a dielectric material within the board layers, the cavity effectively controls impedance and reduces signal loss. This design minimizes electromagnetic interference and ensures consistent signal integrity, resulting in improved overall performance and reliability in high-frequency applications.
What factors should be considered when selecting materials for Rogers Cavity PCBs?
When selecting materials for Rogers Cavity PCBs, several factors should be taken into consideration. Firstly, the dielectric constant and loss tangent of the substrate material are critical, as they directly impact signal propagation and loss characteristics. Additionally, factors such as thermal conductivity, coefficient of thermal expansion, and dimensional stability are essential for ensuring reliable performance, especially in demanding operating environments. Moreover, compatibility with manufacturing processes and cost considerations are also important factors to evaluate when selecting materials for Rogers Cavity PCBs.
Can Rogers Cavity technology be applied to multilayer PCB designs?
Yes, Rogers Cavity technology can be applied to multilayer PCB designs to achieve enhanced performance and functionality. By incorporating cavity structures within the PCB stack-up, designers can effectively control impedance and minimize signal loss across multiple layers. This allows for the integration of high-frequency components and circuits into complex multilayer PCB designs, enabling the realization of advanced electronic systems with superior performance and reliability.
How can manufacturers ensure the reliability of Rogers Cavity PCBs in harsh operating environments?
Manufacturers can ensure the reliability of Rogers Cavity PCBs in harsh operating environments through careful design, material selection, and manufacturing processes. By using high-quality materials with proven performance characteristics, such as Rogers Corporation’s specialized laminates, and employing advanced manufacturing techniques, manufacturers can produce PCBs that meet stringent reliability standards. Additionally, thorough testing and quality control measures are essential to identify and mitigate any potential issues before deployment, ensuring the long-term reliability of Rogers Cavity PCBs in demanding applications.