RO4350B PCB Manufacturing.RO4350B PCB manufacturing involves the production of printed circuit boards using the RO4350B laminate, known for its low dielectric loss and high thermal conductivity. This material is ideal for high-frequency applications such as RF and microwave circuits. The process includes precision etching, layering, and quality testing to ensure optimal performance and reliability in advanced electronic systems.
In the field of modern electronics, Printed Circuit Boards (PCBs) play a vital role. They are the core components that connect and support electronic components. Among many PCB types, RO4350B PCB is popular in high-frequency applications due to its excellent high-frequency performance and thermal stability. This article will take you deep into the RO4350B PCB manufacturing process, every key step from design to finished product, giving you a full understanding of the excitement of this special model PCB.
What is RO4350B PCB?
RO4350B PCB (Rogers RO4350B printed circuit board) is a high-performance printed circuit board made of special materials with excellent dielectric constant and low loss characteristics. This material is widely used in high-frequency electronic equipment and communication systems, especially in fields such as microwave communications, radar systems, and satellite receivers.
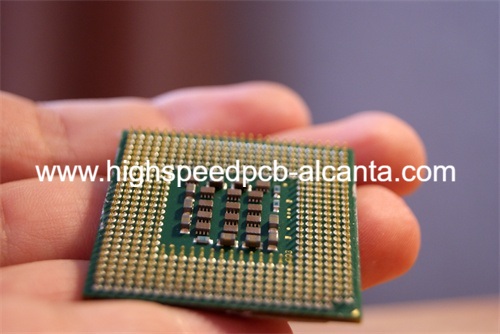
RO4350B PCB Manufacturing
RO4350B PCB is known for its excellent performance and stability, and the stability of its dielectric constant makes it ideal for high-frequency applications. The dielectric constant is a measure of the permittivity of a material under the action of an electric field. For high-frequency circuits, a stable dielectric constant can ensure the transmission speed and accuracy of signals, thereby improving the performance and reliability of the system.
In addition, RO4350B PCB also has low loss characteristics, which means that energy loss can be minimized during signal transmission, maintaining signal clarity and stability. This is important for applications that require high accuracy and reliability, such as wireless communication systems, antenna design, and satellite communications.
Due to its superior performance, RO4350B PCB has been widely used in various high-frequency applications. In microwave communications, it can be used to manufacture key components such as antennas, radio frequency filters and power amplifiers, providing reliable signal transmission and processing capabilities. In radar systems, RO4350B PCB can be used to manufacture high-performance antenna arrays and RF front-end modules to achieve accurate target detection and tracking. In satellite receivers, RO4350B PCB can be used to manufacture high-sensitivity radio frequency receivers and signal processing units to achieve stable reception and decoding of satellite signals.
In short, RO4350B PCB, as a printed circuit board made of special materials, has excellent dielectric constant and low loss characteristics, is suitable for various high-frequency applications, and provides a reliable foundation and design for modern communication and electronic systems. solution.
How to design RO4350B PCB?
The design of RO4350B PCB is a critical and complex process, which involves many important steps such as circuit diagram capture, component placement, routing and layout. First, designers need to use professional design software to capture circuit diagrams, which means converting information such as electronic components, connection lines, and functional modules into digital form for subsequent layout and wiring.
Component layout is an important part of the design process. It determines the placement of various components on the PCB and the relationship between them. In the design of RO4350B PCB, designers need to consider the high-frequency characteristics and thermal stability of the circuit and reasonably arrange the location of components to minimize signal transmission loss and interference.
Routing is the process of drawing the connection lines between circuit components on the surface of the PCB, which directly affects the performance and stability of the circuit. In the design of RO4350B PCB, designers need to accurately plan the routing path to avoid cross interference and signal crosstalk, while ensuring the stability and reliability of the circuit.
Layout combines component placement and routing to form the final physical layout of the PCB. In the design of RO4350B PCB, the layout needs to comprehensively consider factors such as circuit function, space utilization, heat dissipation effect, and manufacturing process, and optimize the performance and manufacturability of the PCB through reasonable layout.
Through the above steps, engineers can convert the circuit schematic diagram into a physical layout and complete the design of the RO4350B PCB. This design process requires rigorous engineering skills and expertise to ensure that the final PCB meets the design requirements and has good performance and reliability.
What is the manufacturing process of RO4350B PCB?
The manufacturing process of RO4350B PCB is a sophisticated and complex process involving multiple critical steps to ensure superior performance and reliability of the final product. These steps are detailed below:
First, the process of manufacturing a RO4350B PCB begins with substrate selection. RO4350B substrates are typically made from glass fiber reinforced polytetrafluoroethylene (PTFE) material with excellent dielectric properties and thermal stability for high frequency applications. The quality and performance of the substrate directly affects the quality of the final PCB.
Next comes the layering stage. At this stage, different material layers are combined together to form a multi-layered PCB structure. These layers can include copper foil, dielectric materials, and other ancillary materials, customized according to design requirements.
Copper foil processing is a crucial step in the PCB manufacturing process. At this stage, the copper foil is processed into the required wires and connection points, and the conductive paths for the circuit are formed through methods such as chemical etching or mechanical processing.
Drilling is a critical step for forming connection holes on a PCB. These holes can be used to mount components, connect wires between different layers, and provide interconnections in multilayer PCB structures.
Electroplating is an important surface treatment process used to form a metallic coating, usually copper, on the surface of a PCB. This metal covering helps improve electrical conductivity and protects the PCB surface from oxidation and corrosion.
The last critical step is etching, which is used to remove excess copper from the PCB surface, leaving the desired wires and connection points intact. Through chemical or mechanical etching, a precisely controlled process ensures that the conductors and connection points on the PCB meet the design requirements.
Through these key steps, the RO4350B PCB manufacturing process forms a complete closed loop from raw material to final product transformation, ensuring that the final PCB has excellent performance and reliability.
How much does a RO4350B PCB cost?
The cost of the RO4350B PCB is a complex and critical consideration. It depends on several factors, the most important of which include size, complexity, material, and quantity.
First of all, size is one of the important factors that affects the cost of RO4350B PCB. Larger PCB sizes require more materials and production resources and therefore cost more. In contrast, small size PCBs usually cost less.
Second, complexity also has a significant impact on costs. Complex PCB designs may require more layers, denser routing, and more advanced process techniques, which increase manufacturing costs. Simple designs usually cost less.
Material selection is also an important factor in cost. RO4350B material itself has high performance and stability, but it is also relatively expensive. In addition to the substrate material, other materials such as copper foil, solder film, etc. will also affect the cost.
Finally, quantity is one of the key factors that determines cost. Generally speaking, high-volume production reduces the cost per unit, while low-volume production increases costs. Therefore, it is crucial to take expected order quantities into account when developing budgets and optimizing production costs.
Overall, understanding these cost drivers is critical to effectively managing RO4350B PCB manufacturing costs. Through reasonable design, material selection and production planning, companies can achieve budget control and optimize production efficiency, thereby improving competitiveness and achieving long-term success.
What material is the RO4350B PCB made of?
RO4350B PCB is a printed circuit board made of special materials. Its excellent performance and stability come from its carefully selected material combination. It is mainly composed of the following materials:
RO4350B substrate material: RO4350B is a high-performance organic glass fiber reinforced composite material with excellent dielectric properties and stable mechanical properties. Its special dielectric constant and low loss angle make it ideal for high-frequency circuit design. RO4350B substrate material not only has excellent dimensional stability, but also maintains stable electrical performance over a wide temperature range, providing a solid foundation for reliable circuit operation.
Copper foil: Copper foil is used to create conductive paths that connect various electronic components and circuits. High-quality copper foil has good electrical conductivity and good weldability, which can ensure the stability and reliability of the circuit. The thickness and quality of the copper foil are critical to the performance and reliability of the circuit, so selecting high-quality copper foil is critical during the manufacturing process of the RO4350B PCB.
Solder film: Solder film is a covering layer used for insulation and protection, usually coated on the surface of a PCB to prevent circuit components from contacting the external environment while protecting the copper foil from corrosion and oxidation. The solder film in RO4350B PCB needs to have good high temperature resistance, excellent adhesion and high mechanical strength to ensure the stability and reliability of the circuit.
The application of these advanced material technologies ensures that RO4350B PCB has excellent performance and stability in high-frequency circuit applications. Through careful selection of materials and strict control of the manufacturing process, RO4350B PCB is able to meet stringent engineering requirements and perform well in a variety of high-frequency applications.
Who makes the RO4350B PCB?
The manufacturing of RO4350B PCB is a complex and precise process involving specialized technology and advanced equipment. For many companies, choosing the right manufacturer is crucial to ensure product quality and production efficiency. For our company, the manufacturing of RO4350B PCB is the responsibility of our suppliers, who are our long-term reliable partners.
Our suppliers have rich experience and expertise and are committed to providing high-quality RO4350B PCB to meet our design needs and industry standards. They have advanced production equipment and technical teams that can precisely control every manufacturing step, from substrate selection to inspection of final products, ensuring product reliability and superior performance.
As part of our company’s supply chain, suppliers work closely with us to understand our needs and customize production to our specifications. They not only provide timely feedback and technical support during the production process, but also work with us to resolve challenges that may arise to ensure a smooth production process.
Our suppliers not only focus on product quality, but also on environmental protection and sustainable development. They use advanced manufacturing technologies and environmentally friendly materials and are committed to reducing waste and pollution during production to support our shared environmental mission.
By working with our suppliers, we are able to ensure high quality and stable supply of RO4350B PCBs to meet our customers’ needs and maintain a competitive advantage. We will continue to work with them to jointly promote technological innovation and industry development, and provide customers with better products and services.
The supplier’s role is crucial in the RO4350B PCB manufacturing process. Their expertise, technical capabilities and cooperative spirit lay a solid foundation for our product quality and customer satisfaction. We will continue to work closely with them to achieve business goals and sustainable development.
Five traits of great customer service
Excellent customer service is vital to any business. It is a key factor in not only retaining existing customers but also attracting new ones. Here are five traits of great customer service that form the cornerstone of building long-term customer relationships.
Responding to customer inquiries and concerns promptly and effectively is a fundamental requirement for providing quality customer service. Customers want their issues to be resolved in a timely manner rather than being shelved or ignored. By promptly responding to customer emails, phone calls, or online messages, you demonstrate your importance and concern for your customers, thereby increasing customer satisfaction and trust.
Treating your customers’ needs with compassion and understanding is the key to building positive customer relationships. Customers may encounter various problems or difficulties, and they expect not only solutions, but also understanding and care. By listening to customers’ problems, understanding their situations, and proactively finding solutions, you can make customers feel valued and respected, thereby enhancing customer loyalty.
Always keeping your promises and commitments to your customers is key to building customer trust. Customers want to be able to rely on you for service and support in their business transactions. Whether it is the time to deliver products, the speed of providing technical support, or the efficiency of problem solving, you need to ensure that promises can be fulfilled to build a reliable reputation and brand image.
Maintaining clear and transparent communication during the service process is an important means to ensure customer understanding and satisfaction. Providing necessary information to customers in a timely manner, explaining the details of products or services, and maintaining open and honest communication with customers can reduce misunderstandings and dissatisfaction and establish a good cooperative relationship.
Proactively solving problems and striving for customer satisfaction is the ultimate goal of providing quality customer service. Customers may encounter various problems or challenges, and how to resolve these problems quickly and effectively will directly affect customer satisfaction and loyalty. By setting up a dedicated customer support team, providing timely technical support, and flexibly responding to customer needs and feedback, we can effectively solve problems and win customers’ trust and support.
Overall, great customer service is not just a service, it’s an attitude and culture. Through proactive responsiveness, an empathetic attitude, reliable commitment, clear communication, and effective problem-solving skills, companies can build a strong brand image, win the trust and loyalty of customers, and achieve long-term business success.
Frequently Asked Questions
Can RO4350B PCBs be recycled?
Yes, RO4350B PCBs can be recycled to recover valuable metals and reduce environmental impact. However, recycling processes must be conducted responsibly to minimize potential hazards associated with electronic waste. Proper handling and disposal methods should be employed to mitigate environmental and health risks.
What are the key considerations when selecting a manufacturer for RO4350B PCBs?
When selecting a manufacturer for RO4350B PCBs, factors to consider include their experience with high-frequency materials, adherence to quality standards, production capabilities, lead times, and customer support. It’s essential to choose a reputable manufacturer with a track record of delivering reliable products and excellent service.
How does the cost of RO4350B PCBs compare to conventional PCBs?
The cost of RO4350B PCBs is typically higher than that of conventional PCBs due to the specialized materials and manufacturing processes involved. However, the higher cost is justified by the superior performance and reliability of RO4350B PCBs in high-frequency applications.
What are the advantages of using RO4350B PCB over conventional PCB materials?
RO4350B PCB offers superior high-frequency performance and thermal stability compared to conventional materials, making it ideal for applications requiring precise signal integrity and reliability at microwave frequencies.