Rigid-Flex Packaging Substrate Manufacturer.A Rigid-Flex Packaging Substrate Manufacturer specializes in crafting innovative substrates for electronic devices, blending rigid and flexible materials seamlessly. With precision engineering and cutting-edge technology, they create durable yet adaptable substrates crucial for modern electronics. Their expertise lies in seamlessly integrating rigid and flexible components, ensuring reliability and performance in compact designs. From intricate circuitry to resilient casings, their substrates enable the seamless assembly of electronic components, facilitating efficiency and durability in diverse applications. With a commitment to quality and innovation, they are pioneers in the field, shaping the future of electronic packaging.
Rigid-Flex Packaging Substrate is a unique electronic component that blends rigid and flexible materials to provide new possibilities for electronic design. In this highly competitive and ever-evolving electronics industry, Rigid-Flex Packaging Substrate is highly regarded for its unique design and functionality.
Traditional electronic components are usually made of rigid materials, which can provide high mechanical strength and stability. However, in some specific application scenarios, their rigidity limits design flexibility and may take up a large amount of space. space. In contrast, Rigid-Flex Packaging Substrate combines rigid and flexible materials, combining the advantages of both, so it can play an important role in a variety of complex electronic devices.
What is unique about this component is its flexibility and plasticity. By cleverly layering rigid and flexible materials together, Rigid-Flex Packaging Substrate can adapt to design needs in a variety of shapes and sizes. This design flexibility allows engineers to better optimize the space utilization of electronic products and more freely explore new possibilities in designs. For example, in small electronic products such as mobile phones, tablets, and portable medical devices, the flexibility of Rigid-Flex Packaging Substrate allows the circuit board to be tightly integrated with the body, thereby saving valuable space and improving the overall performance and use of the device experience.
In addition, Rigid-Flex Packaging Substrate offers outstanding durability and reliability. Due to the multi-layer structure, the connection points between electronic components can be effectively reduced, thereby reducing the risk of failure. This reliability is particularly important for critical application scenarios that require long-term stable operation, such as medical equipment, aerospace, and automotive electronic systems.
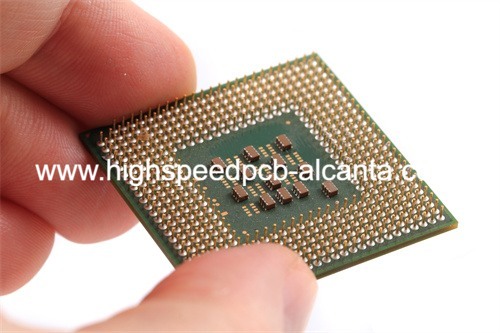
Rigid-Flex Packaging Substrate Manufacturer
Overall, Rigid-Flex Packaging Substrate is not just an electronic component, but also a symbol of technological innovation. Its emergence opens up new possibilities for electronic designers and engineers, promoting the innovation and development of electronic products. As technology continues to advance and market demand continues to grow, Rigid-Flex Packaging Substrate will continue to play an important role in the electronics industry and bring more surprises and changes to future electronic devices.
What types of Rigid-Flex Packaging Substrate are there?
As an important component in electronic equipment, Rigid-Flex Packaging Substrate exists in many types to meet different design needs and application scenarios. Understanding these types can help ensure the best choice among various electronic devices.
Single-layer Rigid-Flex Packaging Substrate is the simplest type, consisting of a single rigid board and a flexible circuit board. It is suitable for space-constrained applications such as mobile devices and medical devices.
The two-layer Rigid-Flex Packaging Substrate consists of a flexible circuit board sandwiched between two rigid boards. This type is typically used in applications that require higher density layouts and more complex connections, such as automotive electronics and aerospace.
Multilayer Rigid-Flex Packaging Substrate consists of multiple rigid and flexible layers that are stacked and connected. They are suitable for high-performance equipment and complex electronic systems such as communications equipment and industrial control systems.
This type combines the characteristics of rigid boards and flexible boards, providing more flexible design options through the combination of flexible wiring and rigid supports. It is widely used in applications that require both flexibility and stability, such as consumer electronics and avionics.
Double-sided Rigid-Flex Packaging Substrate allows connections on both sides, providing higher routing density and more design flexibility. This type is suitable for applications that require higher wiring density, such as high-end mobile communication equipment and computer servers.
By understanding these different types of Rigid-Flex Packaging Substrate, engineers can make the best choice based on specific design needs and application scenarios, ensuring optimal performance, reliability and cost-effectiveness of electronic devices.
What are the advantages of Rigid-Flex Packaging Substrate?
Rigid-Flex Packaging Substrate is highly favored in today’s electronics industry and its unique advantages make it the first choice for modern electronic applications. Let’s take a deeper look at these advantages.
Improved Reliability: In electronic devices, reliability is a crucial factor. Rigid-Flex Packaging Substrate reduces the risk of failure by reducing connection points between components. They are more resistant to vibration, temperature changes and mechanical stress than traditional rigid or flexible circuit boards, increasing overall system reliability.
Reduced weight: Lightweighting of electronic devices is one of the current design trends, and Rigid-Flex Packaging Substrate can help achieve this goal. Because they are compact and require fewer connections and support structures, they are generally lighter than traditional boards, helping to reduce the overall weight of the device and improve portability and comfort.
Enhanced Space Utilization: In today’s compact electronic devices, efficient use of space is critical. Rigid-Flex Packaging Substrate has flexible design features that allow the board to be folded or bent to maximize available space. This advantage makes it possible to integrate more functions into small devices, providing more possibilities for innovation.
Increased design flexibility: Innovation requires flexibility, and Rigid-Flex Packaging Substrate provides that flexibility. They allow engineers to design more complex and compact circuit layouts, resulting in higher performance electronic devices. In addition, flexible design can also simplify the assembly process, shorten product time to market, and improve production efficiency.
Taken together, the benefits of Rigid-Flex Packaging Substrate are clear: improved reliability, reduced weight, enhanced space utilization and increased design flexibility. These advantages make it the first choice for modern electronic applications, driving the electronics industry to the forefront of innovation and development.
Why choose Rigid-Flex Packaging Substrate?
Rigid-Flex Packaging Substrate has become an innovative technology in the field of electronic design. Its unique characteristics and advantages make it stand out in many applications. Compared with traditional boards, there are many reasons for choosing Rigid-Flex Packaging Substrate, and these reasons directly affect engineers’ decisions during the design process.
First, Rigid-Flex Packaging Substrate offers unparalleled versatility. While traditional rigid boards are often limited by size and shape, Rigid-Flex Packaging Substrate can flexibly bend and fold, making it more suitable for devices with limited space or complex shapes. This flexibility not only provides greater design freedom, but also reduces connection points between components, thereby reducing potential failure points and improving overall reliability.
Second, Rigid-Flex Packaging Substrate helps engineers overcome design challenges. In some applications, electronic devices need to operate under different environmental conditions, such as high temperature, humidity, or mechanical vibration. While traditional boards may not be able to meet these requirements, Rigid-Flex Packaging Substrate can adapt to various environments through flexible design and material selection, thereby increasing the durability and stability of the device.
Additionally, Rigid-Flex Packaging Substrate helps create innovative, compact electronic devices. By integrating rigid and flexible parts, engineers can fit more functions and components into the same space, allowing devices to be miniaturized and lightweight. This compact design not only improves the appearance of the product, but also reduces manufacturing costs and material consumption.
In the end, Rigid-Flex Packaging Substrate won over engineers with its reliable performance and stable quality. In modern electronic equipment, reliability is crucial and any failure can have serious consequences. Rigid-Flex Packaging Substrate’s design and manufacturing processes undergo rigorous quality controls to ensure consistent performance and long-term reliability, providing engineers with the confidence to use it in critical applications.
To sum up, the reasons for choosing Rigid-Flex Packaging Substrate over other boards are its many advantages such as versatility, design flexibility, innovation and reliability, which make it one of the top choices for modern electronic design.
How are Rigid-Flex Packaging Substrate motherboards and substrates manufactured?
Manufacturing Rigid-Flex Packaging Substrate’s motherboards and substrates involves a complex and critical series of steps that ensure the quality and performance of the final product. This manufacturing process is explored in detail below to provide a more complete understanding of the production cycle.
First, the process of manufacturing Rigid-Flex Packaging Substrate begins in the design phase. At this stage, engineers need to accurately plan the layout and connection of the motherboard and baseboard. Considering the combination of rigid and flexible materials, the design must take into account mechanical properties, electrical performance, and production feasibility.
Next comes material preparation and preprocessing. Before manufacturing motherboards and substrates, various materials must undergo rigorous inspection and processing. This includes the selection and handling of rigid materials such as FR-4 and flexible materials such as polyimide (PI) membranes to ensure they meet product specifications and quality standards.
Then comes graphic visualization. By using computer-aided design (CAD) software, design graphics are transformed into graphic images required for actual manufacturing. This step is crucial because it directly affects the precision and accuracy of subsequent manufacturing.
This is followed by graphic conversion, i.e. converting the design into a file format required for manufacturing, such as a Gerber file. These files contain PCB layer information, including wires, hole locations, pads, etc., providing an accurate reference for subsequent processing and manufacturing.
Then comes production and processing. This stage includes using CNC machine tools and other advanced equipment to convert the design graphics into actual motherboards and substrates based on graphic image files. This includes processes such as etching, drilling, cutting, etc. to ensure the accuracy and quality of motherboards and substrates.
Next comes assembly and connections. In this step, the manufactured motherboard and substrate are assembled and connected with other electronic components. This may involve manual or automated assembly processes, depending on the complexity and requirements of the product.
Finally comes testing and quality control. The completed Rigid-Flex Packaging Substrate will undergo rigorous testing and quality control to ensure it meets design specifications and customer requirements. This includes electrical testing, reliability testing and visual inspection.
Through this series of manufacturing steps, Rigid-Flex Packaging Substrate’s motherboards and substrates are manufactured accurately and reliably, providing a solid foundation and critical support for a variety of electronic applications.
What are the applications of Rigid-Flex Packaging Substrate?
Rigid-Flex Packaging Substrate is an integral part of today’s electronics industry, and its applications in various fields are rapidly expanding. From aerospace to medical devices, the flexibility and reliability of Rigid-Flex Packaging Substrate make it a core component of innovative electronic solutions.
In the aerospace field, Rigid-Flex Packaging Substrate plays a key role. The design of spacecraft, satellites and aircraft requires electronic components that are high temperature resistant, lightweight and reliable. Rigid-Flex Packaging Substrate can meet these requirements while reducing equipment weight and improving system performance.
In the field of medical equipment, Rigid-Flex Packaging Substrate is also increasingly used. Medical devices require extremely high levels of compactness, performance and reliability, and the design features of Rigid-Flex Packaging Substrate enable it to meet these demands. For example, medical monitoring equipment, implantable medical devices, and portable medical devices are all using Rigid-Flex Packaging Substrate to achieve better design and performance.
In addition, Rigid-Flex Packaging Substrate is also widely used in consumer electronics, automotive electronics, industrial control and communications fields. With the continuous advancement of technology and the growing market demand, Rigid-Flex Packaging Substrate will continue to play an important role in various fields and promote the development of the electronics industry.
Overall, the wide range of applications of Rigid-Flex Packaging Substrate not only reflects its importance in the electronics field, but also demonstrates its versatility and adaptability in different industries. With the continuous evolution of technology and the promotion of innovation, Rigid-Flex Packaging Substrate will continue to bring more opportunities and possibilities to all walks of life, becoming a key component of future electronic equipment design.
Where to find Rigid-Flex Packaging Substrate?
Finding a reliable Rigid-Flex Packaging Substrate manufacturer is crucial to ensuring high-quality components. As an industry-leading manufacturer, our company plays an integral role in ensuring the quality and performance of these critical components.
In the modern electronics industry, choosing the right supplier is critical to the success of your project. The quality and performance of Rigid-Flex Packaging Substrate directly affects the reliability and stability of the final product. Therefore, to ensure you get the best support for your design, it becomes crucial to choose a reputable manufacturer.
Why choose our company as your supplier?
EXCELLENT QUALITY CONTROL: Our company is known for its excellent quality control system, ensuring that every Rigid-Flex Packaging Substrate is manufactured to the highest standards. From the selection of raw materials to every step of the production process, we are committed to delivering impeccable quality.
Advanced production technology: We use advanced production technology, including the latest manufacturing equipment and processes. This not only improves production efficiency but also ensures product consistency and reliability.
Professional engineering team: We have an experienced and professional engineering team that can understand and meet customers’ specific design needs. Whether it is a complex layout or high performance requirements, we can provide individual solutions.
Timely delivery: We focus on punctuality of delivery. Understanding that project time is of the essence to your business, we will ensure that your required Rigid-Flex Packaging Substrate is delivered according to the negotiated timeline.
Customer Support and Communication: We are committed to building strong relationships with our customers and providing excellent customer support and timely communication. We understand your needs and work hard to ensure your project is met and exceeds expectations.
When choosing a supplier for Rigid-Flex Packaging Substrate, choosing our company is a solid foundation for your project. We support you with superior quality, advanced technology and a dedicated team to ensure your electronic devices achieve excellence in performance and reliability.
How much does Rigid-Flex Packaging Substrate cost?
In the electronics industry, understanding the quoting process for Rigid-Flex Packaging Substrate is critical for businesses and engineers. This session will provide insights into the factors affecting Rigid-Flex Packaging Substrate’s offer and navigating the changing pricing landscape.
In today’s highly competitive electronics market, correct evaluation of Rigid-Flex Packaging Substrate offers is crucial for business decisions. There are multiple factors involved in this process, some of which can directly impact production costs and the performance of the final product.
First of all, material cost is one of the main factors affecting Rigid-Flex Packaging Substrate quotation. Different types of materials, such as combinations of rigid and flexible materials, as well as high-performance substrates, can have a significant impact on costs. Engineers need to weigh material performance against cost to ensure the best design and manufacturing balance.
Secondly, the complexity in the manufacturing process will also directly affect the quotation of Rigid-Flex Packaging Substrate. Highly precise manufacturing processes and complex stack-up structures can result in higher labor and equipment costs. Therefore, understanding the manufacturing process, technical requirements and equipment investment is critical to accurately evaluate a quote.
Changes in the pricing landscape are one of the common challenges in the industry. Fluctuations in raw material prices, changes in market demand, and uncertainty in global supply chains may cause fluctuations in Rigid-Flex Packaging Substrate quotations. Amid this uncertainty, businesses and engineers need to adopt flexible strategies to adapt to market dynamics.
How to respond to changes in the pricing situation has become a key factor in corporate success. Strategies such as regularly reviewing supply chains, building strong relationships with suppliers, and finding alternative materials or manufacturing processes can help companies better respond to price fluctuations in changing market conditions.
In practice, effective cost management and flexible supply chain strategies are key to ensuring that companies remain competitive in a pricing environment. Engineers’ design choices can also directly impact the final cost of the Rigid-Flex Packaging Substrate, so they need to work closely to find a solution that meets performance requirements while staying within budget.
To sum up, understanding the factors behind Rigid-Flex Packaging Substrate’s offer and being flexible in responding to the changing market is one of the keys to success for businesses and engineers in the electronics field. By managing costs prudently and responding flexibly to market changes, companies can remain competitive in a highly competitive environment and provide high-performance and cost-effective electronic solutions.
Frequently Asked Questions
What are Rigid-Flex Packaging Substrates?
Rigid-Flex Packaging Substrates are specialized circuit boards that integrate both rigid and flexible materials, offering enhanced flexibility and durability in electronic designs.
What types of applications are Rigid-Flex Packaging Substrates suitable for?
Rigid-Flex Packaging Substrates find applications in a wide range of industries, including aerospace, medical devices, automotive electronics, consumer electronics, and more. They are particularly useful in devices that require compact form factors and reliability in harsh environments.
What are the advantages of using Rigid-Flex Packaging Substrates?
The advantages include improved reliability due to fewer interconnects, reduced weight and volume, increased design flexibility, and enhanced resistance to vibration and thermal stress.
How are Rigid-Flex Packaging Substrates manufactured?
The manufacturing process involves laminating flexible circuit layers with rigid layers, followed by etching, drilling, and plating to create the desired circuit patterns and connections.
What design considerations should be taken into account when using Rigid-Flex Packaging Substrates?
Designers need to consider factors such as bend radius, material properties, stackup design, and thermal management to ensure the reliability and performance of Rigid-Flex Packaging Substrate assemblies.