Rigid-flex BGA substrate Manufacturer, the package substrates will be made with PI(flex) materials. and high-speed or high frequency materials. Make the BGA substrate more flexible.
Rigid-flex BGA Substrate (rigid-flexible BGA substrate) is an advanced packaging substrate that combines the characteristics of rigid and flexible materials to provide unique design solutions for electronic devices. Compared with traditional packaging substrates, Rigid-flex BGA Substrate has higher adaptability and performance, and can meet the needs of modern electronic equipment for lightness, compactness and reliability.
Rigid-flexible combination: Rigid-flex BGA Substrate is composed of a rigid layer and a flexible layer. The combination of these two materials gives the substrate the ability to bend and fold, adapting to various complex device designs. The rigid portion provides stable support and connection, while the flexible portion allows the base plate to flex and stretch in tight spaces.
BGA (Ball Grid Array) package: BGA is a common package type in which the chip is connected to small balls or solder balls on the substrate to provide higher connection density and reliability. Rigid-flex BGA Substrate adopts BGA packaging, making it more popular and widely used in modern electronic equipment.
Application scope: Rigid-flex BGA Substrate is widely used in medical equipment, aerospace systems, consumer electronics and other fields. Its flexibility and reliability make it the first choice in many applications.
Performance characteristics: Rigid-flex BGA Substrate has outstanding performance in space utilization, signal transmission and reliability. It can realize complex layouts in limited space and provide reliable electrical connections to ensure stable operation of equipment.
In summary, Rigid-flex BGA Substrate is a packaging substrate with rigid-flexible combination, BGA packaging, wide application and superior performance, providing an important solution for the design and manufacturing of modern electronic equipment.
What types of manufacturers are there for Rigid-flex BGA Substrate?
When choosing a Rigid-flex BGA Substrate (rigid-flex BGA substrate) manufacturer, you will find that there are many types of manufacturers on the market. Each of these manufacturers has different expertise and services to meet the different needs and requirements of their customers. The following are common Rigid-flex BGA Substrate manufacturer types:
Specialty electronics manufacturers are typically integrated businesses that provide comprehensive services from design to production. They have extensive experience and expertise in packaging substrate manufacturing and are able to provide customers with complete solutions. These manufacturers typically have advanced production equipment and technology that enable them to meet customer demands for high-quality products. They are able to undertake large orders and ensure product quality and on-time delivery during the production process.
The material supplier focuses on providing high-quality substrate materials and is one of the key suppliers in Rigid-flex BGA Substrate manufacturing. They have extensive experience in the R&D and production of substrate materials and provide various types of substrate materials to meet the different needs of customers. Working with a professional manufacturer ensures that the substrate material used meets the product’s design specifications and performance requirements.
The custom solution provider focuses on providing customized Rigid-flex BGA Substrate solutions as per the specific needs and requirements of the customers. They work closely with clients to gain a deep understanding of their project needs and provide personalized design and manufacturing services. These manufacturers typically have flexible production capabilities that can be adjusted and customized to meet customer requirements to meet the needs of different projects.
No matter which type of manufacturer you choose, it should be carefully evaluated based on your project needs and budget. Working with professional manufacturers ensures high-quality Rigid-flex BGA Substrate products and full support and services during project implementation.
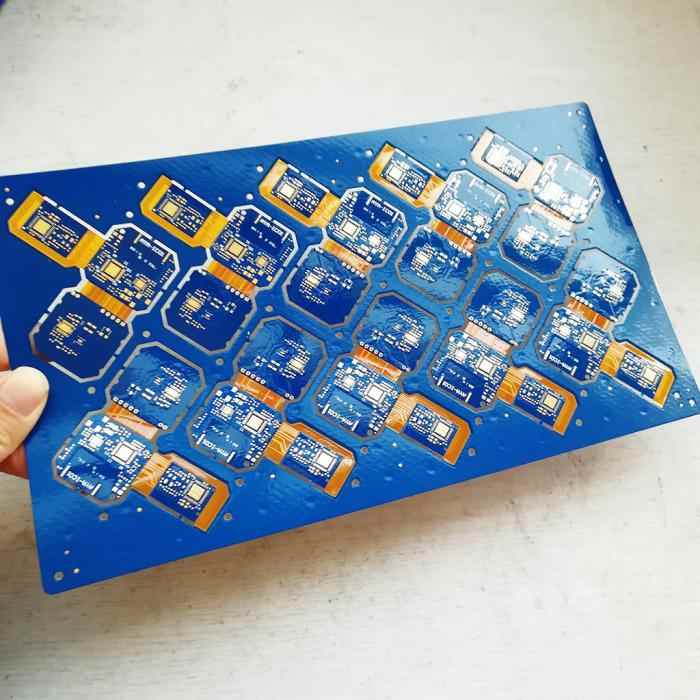
Rigid-Flex BGA Substrate Manufacturer
What are the advantages of Rigid-flex BGA Substrate?
Rigid-flex BGA Substrate (rigid-flexible BGA substrate), as a key component in modern electronic equipment, shows multiple advantages compared to traditional substrates. These advantages are mainly reflected in space efficiency, reliability and adaptability.
Rigid-flex BGA Substrate, with its flexible design, can better utilize space and is especially suitable for space-constrained scenarios in modern electronic equipment. It combines the characteristics of rigid and flexible parts, allowing designers to better layout components and achieve more compact product designs. This advantage is particularly prominent in miniaturized and lightweight electronic products, such as smartphones and wearable devices.
Rigid-flex BGA Substrate has fewer connection points than traditional substrates, which means higher reliability in circuit connections. Fewer connection points reduce possible points of failure, thereby increasing overall system stability and reliability. Especially in applications that require frequent bending or flexing, such as mobile devices or automotive electronic systems, the reliability of Rigid-flex BGA Substrate is even more outstanding.
The design flexibility of Rigid-flex BGA Substrate enables it to adapt to various complex application scenarios and design needs. By combining rigid and flexible parts, Rigid-flex BGA Substrate enables reliable connection and stability in devices of different shapes and structures. This adaptability makes Rigid-flex BGA Substrate the first choice for many applications that require special shapes or curved surfaces, such as medical equipment, aerospace systems, and industrial control systems.
To sum up, the advantages of Rigid-flex BGA Substrate in terms of space efficiency, reliability and adaptability make it an important part of the design of modern electronic equipment. Its flexible design and reliable performance provide strong support for the innovation and development of electronic products, and are expected to play an increasingly important role in the future technology field.
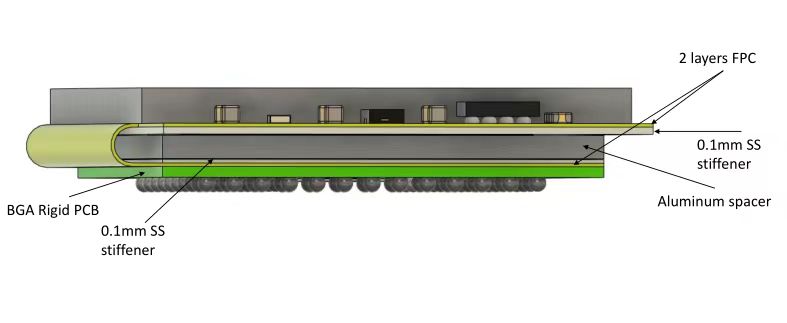
Rigid-flex BGA substrate
What is the process of manufacturing Rigid-flex BGA Substrate?
When manufacturing Rigid-flex BGA Substrate, a complex series of process steps are involved, of which the design phase, material selection and lamination process are critical parts.
First, during the design phase, engineers need to plan the structure and layout of Rigid-flex BGA Substrate in detail. This includes determining the location, size and connection of rigid and flexible parts. Designers need to consider the environment in which the final product will be used, its performance requirements, and how it will fit with other components. Precise design is the basis for ensuring the quality of the final product.
Secondly, material selection is another critical step in manufacturing Rigid-flex BGA Substrate. When selecting materials, engineers need to consider factors such as the material’s mechanical properties, electrical properties, and heat resistance. The rigid part usually uses a glass fiber reinforced epoxy resin substrate, while the flexible part uses flexible substrates such as polyimide (PI). Choosing the right material can ensure that Rigid-flex BGA Substrate has good mechanical strength and electrical properties.
Finally, the lamination process is a key step in combining the rigid and flexible parts into a complete Rigid-flex BGA Substrate. During the lamination process, engineers stack pre-designed rigid and flexible layers in a certain order and use high temperature and pressure to bond them together. This process requires precise control and a high degree of expertise to ensure that the bond between the different material layers is strong and does not create bubbles or other defects.
In general, manufacturing Rigid-flex BGA Substrate is a complex and precise process, involving multiple aspects such as design, material selection and lamination process. Only when each step is precisely controlled and executed can Rigid-flex BGA Substrate be produced with reliable quality that meets customer needs and expectations.
In which application fields is Rigid-flex BGA Substrate widely used?
As an innovative packaging substrate technology, Rigid-flex BGA Substrate is widely used in many fields due to its unique structure and performance characteristics. Here are some of the main application areas:
The medical equipment industry has extremely high requirements for the stability and reliability of electronic components, and the structural design of Rigid-flex BGA Substrate can meet these requirements. Rigid-flex BGA Substrate is widely used in medical imaging equipment, implantable medical devices and wearable medical devices. Its flexibility and high-density wiring design allow medical equipment to be more compact and lightweight, while ensuring stable performance and long service life.
In the aerospace field, there are extremely high requirements on the weight, space utilization and reliability of electronic components. Rigid-flex BGA Substrate’s thin, lightweight design and ability to accommodate complex layouts make it an ideal choice for aerospace systems. In critical applications such as avionics, satellite communication systems and navigation systems, Rigid-flex BGA Substrate can play an important role in ensuring system performance and reliability.
The consumer electronics market has increasingly stringent requirements for product size, appearance design and performance, and the flexibility and highly integrated design of Rigid-flex BGA Substrate just meet these needs. Rigid-flex BGA Substrate is widely used in fields such as smartphones, tablets, wearable devices and portable electronic products. It can achieve a more compact design, higher performance and longer battery life, bringing a better user experience to consumers.
To sum up, Rigid-flex BGA Substrate has been widely used in many fields such as medical equipment, aerospace systems and consumer electronics. Its unique structural design and performance advantages make it an important part of various electronic devices, driving the continuous innovation and development of these industries.
How to find a professional Rigid-flex BGA Substrate manufacturer?
When selecting a Rigid-flex BGA Substrate manufacturer, critical steps are critical to ensure that the supplier you ultimately select meets your needs. Here are some suggestions to help you make an informed decision when looking for the right Rigid-flex BGA Substrate manufacturer.
First, check out the customer reviews of potential manufacturers. These reviews can be obtained from a variety of sources, including online reviews, social media, and industry forums. Understanding the experiences of other customers can help evaluate a supplier’s reliability and service quality.
Examining the technical capabilities of suppliers is a crucial step in the selection process. Ensure that they have advanced production equipment and a professional team with the technology and experience required to manufacture high-quality Rigid-flex BGA Substrate. Ask about their success stories on similar projects to confirm their technical prowess.
It is very important to ask the supplier to provide samples for testing before making a final decision. Through actual sample testing, you can evaluate the quality, performance and compliance of their products to ensure they meet your technical and design requirements. It is also an effective way to verify the technical capabilities claimed by the manufacturer.
Choosing a supplier with reliability and stability is critical to ensuring the success of your project. Review the supplier’s operating history, financial health, and reputation in the industry. Make sure they have sufficient resources and capabilities to provide stable support throughout the partnership.
Timely and effective communication is the key to successful cooperation. Ensure that suppliers have good communication channels and feedback mechanisms in place so that any potential issues can be addressed promptly while the project is ongoing. A transparent partnership helps build trust, ensuring a successful project.
How to get a quote for Rigid-flex BGA Substrate?
When you decide to choose a Rigid-flex BGA Substrate manufacturer, it is crucial to obtain a detailed quote. Here are some key considerations to ensure you get an accurate, comprehensive quote that includes all related fees and services.
First, communicate your needs clearly with the manufacturer. Before requesting a quote from a manufacturer, make sure you have a clear understanding of your project requirements, including details such as size, materials, number of layers, quantities, and delivery time. This will help the manufacturer accurately understand your needs and provide a corresponding quote.
Secondly, ask the manufacturer to provide a detailed quotation. You should receive a detailed quote that includes all associated fees and services, which may include material costs, workmanship charges, sample charges, shipping charges, and any other additional charges. Make sure the quote is clear and has no hidden fees.
It’s also important to understand the manufacturer’s pricing policy and payment terms. You should clearly understand details such as the validity period of the quote, payment method and payment terms. Some manufacturers may require upfront payment or installment payments, while others may offer more flexible payment options.
Additionally, considering that you may need multiple modifications or customizations, it’s important to discuss the additional fees and services associated with the manufacturer. Make sure you understand the additional costs that may be incurred by modifying your order or customizing services and take this into account in your quote.
Finally, it is also very important to establish good communication and cooperative relationships with manufacturers. When discussing quotes with manufacturers, make sure you are able to communicate fully with them, raise any questions or concerns, and work with them to ensure a successful project.
In summary, obtaining a detailed quote for Rigid-flex BGA Substrate requires clear and transparent communication between you and the manufacturer, ensuring you understand all associated fees and services, and establishing a good working relationship to ensure the project goes smoothly and is successful. .
What are the common problems with Rigid-flex BGA Substrate?
How do temperature variations affect Rigid-flex BGA Substrates?
Rigid-flex BGA substrates experience thermal expansion and contraction due to temperature changes, which can lead to mechanical stress and reliability issues over time. Proper design considerations and material selection are crucial to mitigate these effects.
What measures are taken to ensure signal integrity and reliability in Rigid-flex BGA Substrates?
Maintaining signal integrity and reliability in Rigid-flex BGA substrates requires careful attention to impedance control, routing, and shielding. Signal distortion and cross-talk are common concerns that need to be addressed through meticulous design and testing.
How do designers manage the complexities of Rigid-flex BGA Substrate layouts?
Designing Rigid-flex BGA substrates involves navigating complex layouts to accommodate both rigid and flexible sections. Challenges such as bending radius limitations, via reliability, and mechanical stability need to be addressed while optimizing space and functionality.
What are the main failure modes associated with Rigid-flex BGA Substrates?
Common failure modes include solder joint fatigue, microcracks in flexible sections, and electrical opens due to mechanical stress. Understanding these failure mechanisms is essential for implementing robust design practices and ensuring long-term reliability.
How do environmental factors impact the performance of Rigid-flex BGA Substrates?
Environmental factors such as humidity, moisture ingress, and chemical exposure can degrade the material properties and lead to premature failure of Rigid-flex BGA substrates. Encapsulation, conformal coating, and proper sealing techniques are employed to enhance environmental ruggedness.
What quality control measures are implemented during Rigid-flex BGA Substrate production?
Quality control measures include material inspection, dimensional verification, and electrical testing to ensure compliance with specifications. Advanced inspection techniques such as X-ray imaging and automated optical inspection (AOI) are utilized to detect defects and anomalies.