RF SIP Substrate Manufacturer.Flip Chip (ABF) Substrate Manufacturer specializes in producing advanced packaging substrates that facilitate high-density interconnections for semiconductor devices. They focus on innovative design, precise manufacturing processes, and ensuring reliability in electronic assemblies.
With the rapid development of wireless communication technology, RF SIP (Radio Frequency System Integrated Package) substrate, as a key technology, plays an important role in improving device performance and functionality. This article will take an in-depth look at the definition, design guidelines, manufacturing processes, application areas and significant advantages of RF SIP substrates.
What is RF SIP Substrate?
An RF SIP substrate is a specialized printed circuit board designed and manufactured to integrate various key components of an RF system, such as RF amplifiers, filters, and antennas. In modern wireless communication equipment, RF SIP substrate plays a vital role, achieving high-frequency, low-loss and high-stability signal transmission through optimized layout and material selection.
First, the RF SIP substrate ensures stability and transmission efficiency in the high frequency range through precise circuit design and the use of specific materials. Its design takes into account the special needs of RF signals, such as avoiding signal attenuation and cross-interference, thereby improving overall system performance.
Secondly, the RF SIP substrate uses high-quality dielectric materials, such as PTFE (polytetrafluoroethylene) or ceramics, to reduce losses during signal transmission. These materials have low dielectric constant and low loss tangent values, which help reduce energy loss and improve the efficiency of signal transmission.
In addition, the layout and layer stacking design of the RF SIP substrate are carefully optimized to minimize electromagnetic interference (EMI) and improve electromagnetic compatibility (EMC), thereby ensuring stable operation of the RF system under various environmental conditions.
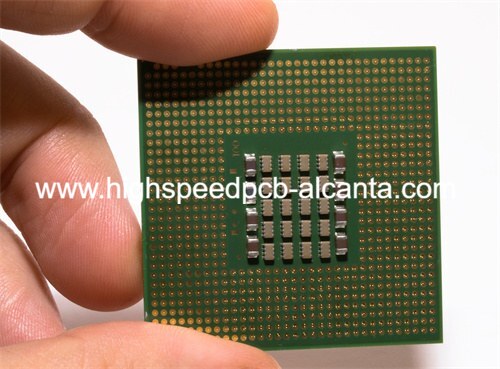
RF SIP Substrate Manufacturer
To sum up, the RF SIP substrate is not only an extension of the traditional printed circuit board, but also a dedicated solution designed for high-frequency RF applications. Its application in modern communication equipment is becoming more and more widespread, including 5G base stations, satellite communication systems, radar and wireless sensor networks and other fields. Through its optimized design and advanced manufacturing process, RF SIP substrate provides a solid foundation for the advancement of wireless communication technology, driving the continuous improvement of device functions and performance.
RF SIP Substrate design Reference Guide.
The design of RF SIP (Radio Frequency System Integrated Package) substrate is a key step to ensure high performance and stable operation of wireless communication equipment. Design engineers need to consider many factors to ensure that the substrate performs well in high-frequency environments and achieves optimal signal transmission.
When designing an RF SIP substrate, optimization of frequency response is crucial. In high-frequency environments, circuit layout and signal path design must be precise to ensure signal stability and minimal transmission loss. By optimizing the length, shape, and layer stacking of transmission lines, signal attenuation and distortion during transmission can be reduced, thereby improving overall system performance and reliability.
Material selection for an RF SIP substrate is critical to its performance and stability. Commonly used high-frequency materials include polytetrafluoroethylene (PTFE) and ceramic substrates, which have excellent dielectric properties and low loss characteristics. PTFE substrates are commonly used in high frequency and microwave applications and are popular for their low dielectric loss and good thermal stability. Ceramic substrates perform well in high temperatures and harsh environments, making them suitable for demanding RF applications.
Effective electromagnetic interference (EMI) and electromagnetic compatibility (EMC) design is one of the key factors to ensure the proper operation of RF SIP substrates. By using appropriate shielding techniques, ground wire design, and filter layout, the impact of external interference on system performance can be effectively reduced. Good EMC design can not only improve the anti-interference ability of the system, but also reduce unnecessary electromagnetic radiation and faults in the system.
To sum up, designing an RF SIP substrate requires comprehensive consideration of many factors such as frequency response optimization, material selection, and EMI/EMC management. Through precise circuit design and appropriate material application, the RF SIP substrate can be ensured to perform well in various complex radio frequency environments, providing a solid foundation for performance improvement and technological progress of wireless communication equipment. Design engineers should follow best practices in practical applications and continuously optimize and improve design solutions to meet changing market needs and technical challenges.
What material is used in RF SIP Substrate?
The primary materials used in RF SIP substrates in their manufacture are critical to their performance and functionality. The following are several common RF SIP substrate materials:
PTFE substrate is widely used in high frequency RF SIP applications due to its excellent dielectric properties and low loss. It has excellent chemical and thermal stability and is able to maintain the stability of electrical performance over a wide temperature range. PTFE substrates are often used in radio frequency system integration packages that require high frequency response and low signal loss.
FR4 substrate is one of the most common printed circuit board materials and is mainly used for general performance RF applications. It has good mechanical strength and heat resistance, is relatively economical, and is suitable for RF SIP design at medium and low frequencies. FR4 substrates are widely used in communication equipment, consumer electronics and industrial control systems.
Ceramic substrates are an ideal choice for RF applications requiring extremely high frequency performance and stability. Ceramic substrates are usually made of materials such as aluminum oxide (Alumina) or aluminum nitride (AlN), which have excellent thermal conductivity and mechanical strength. They provide excellent high-frequency signal transmission characteristics and high temperature resistance and are commonly used in high-performance applications such as radar, satellite communications, and wireless sensor networks.
With the development of technology, some new special materials have emerged, such as polyimide, etc., used in the manufacturing of flexible RF SIP substrates. These materials maintain their electrical properties in curved or tight spaces and have excellent chemical and high temperature resistance, making them suitable for specific high-density integrated packaging needs.
Choosing the appropriate RF SIP substrate material is related to the performance and stability of the overall system. Engineers need to comprehensively consider factors such as frequency characteristics, loss indicators, mechanical strength, and cost-effectiveness when designing and selecting to ensure that the final product can meet complex RF applications. Require.
What size are RF SIP Substrate?
RF SIP (Radio Frequency System Integrated Package) substrates are diversified in size to accommodate different wireless communication equipment and application requirements. Its size is usually affected by several key factors:
Application scenario requirements: The size of the RF SIP substrate will vary according to the specific application scenario. For example, for large equipment such as 5G base stations or satellite communication systems, larger-sized substrates are often required to accommodate complex RF circuits and components.
Physical space constraints of the device: In some applications, the physical space of the RF device may be limited, so the RF SIP substrate needs to be designed in a smaller size to be efficiently integrated and installed inside the device.
Optimization of high-frequency characteristics: In order to ensure stability and performance at high frequencies, the size design of the RF SIP substrate needs to consider the optimization of the circuit layout to reduce loss and interference during signal transmission.
Manufacturing and cost considerations: Size also affects substrate manufacturing costs and production efficiency. Typically, larger substrate sizes may increase manufacturing complexity and cost, while smaller substrate sizes may be more cost-effective.
Generally speaking, there is no fixed standard for the size of RF SIP substrate, but it is flexibly determined based on specific design requirements and application needs. With the development of radio frequency technology and the diversification of application scenarios, the flexibility and diversity in size design of RF SIP substrates will continue to promote its wide application and progress in the field of wireless communications.
The Manufacturer Process of RF SIP Substrate.
The manufacturing of RF SIP (Radio Frequency System Integrated Package) substrates is a complex and precise process involving multiple critical steps, each of which has a significant impact on the performance and reliability of the final product.
First, the manufacturing process begins with the selection of special substrate materials suitable for high-frequency applications. Common materials include PTFE (polytetrafluoroethylene) and ceramics. These materials have excellent dielectric properties and low loss characteristics and can effectively support the transmission of high-frequency signals.
After the substrate material selection is completed, engineers use CAD (computer-aided design) tools to design and optimize the RF circuit diagram. At this stage, the focus is on ensuring that the circuit layout is sound, signal paths are short and losses are minimized, and specific RF performance requirements are met.
After the design is completed, the material layers are stacked according to the circuit design requirements. This involves stacking layers of copper foil and dielectric material together in a strict specification and sequence. The copper foil layer is used to form the conductive path of the circuit, while the dielectric material layer is used to insulate and support the circuit.
Once the material layers are stacked, the forming and processing stages follow. This includes using precision machining techniques such as chemical etching and precision drilling to form precise circuit board structures. Chemical etching technology precisely removes unwanted portions of copper foil to create circuit patterns.
After completing the molding of the circuit board, the next step is the assembly of the radio frequency device. This step involves precisely mounting RF components such as RF amplifiers, filters, and antennas onto the circuit board. After the assembly is completed, strict testing and debugging are performed to ensure that the performance and reliability of the entire RF SIP substrate meet the design requirements.
Through the above steps, the manufacturing process of RF SIP substrate not only requires highly professional engineering knowledge and technology, but also requires strict quality control and testing standards. Only through precise manufacturing processes and strict quality assurance can RF SIP substrates exert their superior performance and stability in various high-frequency applications, providing solid support for the development of modern wireless communication technology.
The Application area of RF SIP Substrate.
RF SIP substrates are widely used and critical in wireless communication equipment. With its superior high-frequency performance and stability, it has become an ideal choice for high-speed data transmission and complex signal processing in many fields.
First of all, RF SIP substrate plays an important role in 5G base stations. The high frequency and large bandwidth of 5G technology require solving complex radio frequency signal transmission and processing problems. Through optimized design and selected materials, the RF SIP substrate can provide efficient signal transmission and low loss, supporting the stable operation of 5G base stations in high-density user scenarios.
Secondly, RF SIP substrates are also widely used in satellite communication systems. Satellite communications require reliable communications connections under extreme environmental conditions, such as high radiation and temperature changes in space. The RF SIP substrate not only resists electromagnetic interference (EMI), but also provides stable signal transmission over a wide frequency range, ensuring efficient operation and data transmission of satellite communication systems.
In addition, radar systems also rely on RF SIP substrates to support their complex signal processing requirements. Radar systems need to detect targets quickly and accurately and process the returning RF signals. Through optimized layout and high-performance materials, the RF SIP substrate can provide precise signal transmission and processing capabilities, helping the radar system achieve high-precision target tracking and environmental monitoring.
Finally, RF SIP substrates also play an important role in wireless sensor networks (WSN). WSN requires nodes to be able to transmit data in real time and collaborate effectively to support various application scenarios, such as environmental monitoring, smart cities, and the Internet of Things. Through its highly integrated design and stable signal transmission characteristics, the RF SIP substrate can improve the communication efficiency and reliability of WSN nodes, thereby achieving more intelligent and effective data collection and processing.
In summary, RF SIP substrates not only play a key role in traditional wireless communication equipment, but also promote the development of emerging technologies such as 5G, satellite communications, radar and WSN. Its advantages in providing high-frequency performance, stability and reliability make it an indispensable and important technical component in today’s wireless communications field. As technology advances and applications expand, RF SIP substrates will continue to play a vital role in future communications and sensing applications. .
What are the advantages of RF SIP Substrate?
RF SIP substrate is one of the key technologies for radio frequency system integrated packaging. It shows many advantages in wireless communication equipment. Compared with traditional circuit design, its significant advantages are as follows:
First of all, the RF SIP substrate ensures stable performance and efficient signal transmission at high frequencies through optimized design and selected materials. This optimization not only improves the overall efficiency of the system, but also meets the high-frequency bandwidth requirements of modern wireless communication equipment, such as 5G base stations and satellite communication systems.
Secondly, the RF SIP substrate uses low dielectric loss materials, which effectively reduces energy loss during signal transmission. This not only helps maintain signal clarity and accuracy, but also reduces device power consumption and extends battery life, especially for mobile devices and battery-powered applications.
In addition, the RF SIP substrate significantly reduces space occupation and connection complexity in the system through the design of integrating multiple RF components. This highly integrated design not only makes the equipment more compact and lightweight, but also simplifies the manufacturing and assembly process, improves production efficiency and reduces manufacturing costs.
Finally, the RF SIP substrate undergoes strict manufacturing and testing processes to ensure its long-term stable operation and reliability. This reliability guarantee can not only meet the requirements of industrial-grade applications for equipment stability and durability, but also reduce maintenance costs and equipment failure rates, providing users with a more reliable experience.
To sum up, the advantages of RF SIP substrate in high-frequency performance, low loss, high integration and strong reliability make it an indispensable key technology for modern wireless communication equipment. With the continuous advancement of technology and the growth of market demand, RF SIP substrate will continue to promote the development of wireless communication technology and bring users more efficient and reliable communication solutions.
FAQ
What is the difference between RF SIP substrate and traditional PCB?
Compared with traditional PCB, RF SIP substrate has significant differences in material selection, design complexity and radio frequency performance optimization. They are specifically designed for high-frequency applications, using low-loss materials and precise layout to ensure stable signal transmission at high frequencies.
What are the main application areas of RF SIP substrates?
RF SIP substrates are widely used in 5G base stations, satellite communication systems, radar, aerospace equipment, wireless sensor networks and other fields. Its high-frequency performance and stability make it ideal for high-speed data transmission and complex signal processing.
How to design and manufacture RF SIP substrate?
Designing an RF SIP substrate requires consideration of factors such as frequency response optimization, material selection, and EMI/EMC management. The manufacturing process includes substrate preparation, circuit diagram design, material layer stacking, molding processing, assembly testing and other steps, which requires precise process control and test verification.
What are the advantages of RF SIP substrate?
RF SIP substrate has the advantages of high-frequency performance optimization, low loss, high integration and strong reliability. They reduce system space occupation and connection complexity by integrating multiple radio frequency components, and are suitable for application scenarios that require high frequency stability and transmission efficiency.