RF Package Substrates Manufacturer.”RF Package Substrates Manufacturer” refers to a company specializing in the production of substrates tailored for RF (radio frequency) applications. They design and manufacture advanced materials and structures that optimize signal integrity, thermal management, and reliability in RF electronic devices.
RF (Radio Frequency) package substrates are specialized components designed to support and house RF circuits and devices. These substrates are crucial for the proper functioning of RF systems, which are widely used in wireless communication, radar, satellite, and other high-frequency applications. RF package substrates provide the necessary mechanical support, electrical connectivity, and thermal management to ensure the optimal performance and reliability of RF components.
What is an RF Package Substrate?
An RF package substrate is a type of printed circuit board (PCB) specifically engineered for RF applications. These substrates serve as the foundation for mounting RF chips, components, and circuits, providing electrical interconnections and mechanical stability. RF package substrates are designed to handle high-frequency signals, typically in the range of MHz to GHz, and are constructed to minimize signal loss, interference, and distortion.
RF Package Substrate Design Reference Guide
Designing an RF package substrate involves several critical considerations to achieve optimal performance and reliability. The following sections outline the key aspects of the design process:
Material selection is crucial for RF package substrates, as the materials used must possess excellent electrical, thermal, and mechanical properties. Common materials include:
High-Performance Organic Resins: Organic resins such as PTFE (polytetrafluoroethylene) and high-frequency laminates like Rogers materials are widely used for their excellent dielectric properties, low loss, and good thermal stability.
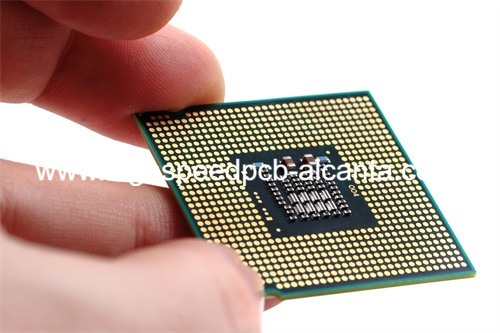
RF Package Substrates Manufacturer
Ceramics: Ceramic materials such as alumina (Al2O3) and aluminum nitride (AlN) offer superior thermal conductivity and electrical insulation properties, making them ideal for high-power RF applications.
Metals: Conductive metals such as copper and silver are used for the conductive layers due to their excellent electrical conductivity. Surface treatments like gold plating are often applied to improve solderability and corrosion resistance.
The layer structure of an RF package substrate is designed to minimize signal loss and interference. Typical layer structures include:
Effective thermal management is essential to prevent overheating and ensure the longevity of RF components. RF package substrates often incorporate:
Thermal Vias: These are small holes filled with conductive material that create a path for heat to travel from the surface-mounted RF components to the other side of the substrate, where it can be dissipated more effectively.
Heat Spreaders: Heat spreaders made from materials with high thermal conductivity, such as copper or aluminum, are integrated into the substrate to spread heat evenly across the surface.
Heat Sinks: In some designs, external heat sinks are attached to the substrate to further enhance thermal performance.
The electrical performance of an RF package substrate is determined by factors such as signal integrity, impedance control, and crosstalk minimization. Key design considerations include:
Impedance Control: Precise control of the impedance of signal traces is essential for maintaining the performance of high-frequency signals. This involves careful design of the trace width, spacing, and dielectric properties of the substrate materials.
Signal Integrity: Maintaining signal integrity involves minimizing signal loss and distortion through careful design of the signal traces, proper grounding, and the use of advanced materials and fabrication techniques.
Crosstalk Minimization: Crosstalk, or interference between adjacent signal traces, must be minimized to ensure reliable operation of RF circuits. This is achieved through careful layout design, the use of shielding techniques, and proper grounding.
What Material is Used in RF Package Substrates?
The materials used in RF package substrates are selected based on their electrical, thermal, and mechanical properties. The following materials are commonly used:
High-Performance Organic Resins: Materials like PTFE (Teflon) and high-frequency laminates (e.g., Rogers materials) are used for their low dielectric constant, low loss tangent, and excellent thermal stability.
Ceramics: Ceramic materials such as alumina (Al2O3) and aluminum nitride (AlN) offer superior thermal conductivity, low dielectric loss, and excellent electrical insulation properties.
Metals: Copper is commonly used for the conductive layers due to its excellent electrical conductivity. Surface treatments like gold plating are applied to improve solderability and corrosion resistance. Silver and other metals may also be used for specific applications.
Composite Materials: Advanced composite materials that combine different properties of ceramics and polymers are also used to achieve a balance of electrical performance, thermal management, and mechanical strength.
What Size are RF Package Substrates?
The size of RF package substrates varies depending on the specific application and design requirements. The following factors influence the size of these substrates:
Thickness: The thickness of RF package substrates typically ranges from 0.1 mm to several millimeters, depending on the complexity and functionality required. Thicker substrates are used for high-power applications to provide better thermal management and mechanical strength.
Length and Width: The length and width of RF package substrates are determined by the size and layout of the RF components they support. The dimensions must accommodate the RF package and provide sufficient space for signal routing and power distribution. The exact size can range from a few millimeters to several centimeters, depending on the complexity and requirements of the application.
The Manufacturing Process of RF Package Substrates
The manufacturing process of RF package substrates involves multiple stages, each requiring precise control and advanced technology. The following steps outline the typical manufacturing process:
The process begins with the preparation of the base materials, including organic resins, ceramics, and metals. These materials are processed into thin sheets or films of the desired thickness.
The thin sheets of materials are stacked and laminated to form a multilayer substrate. Each layer serves a specific purpose, such as signal routing, power distribution, or grounding. The layers are aligned and bonded together using heat and pressure to create a solid and cohesive structure.
Microvias are drilled into the substrate to create interconnections between the layers. Laser drilling is commonly used for this purpose due to its precision and ability to create small, high-density vias. The vias are then plated with conductive materials, typically copper, to establish electrical connections between the layers.
The conductive layers are patterned to create the desired circuit layout. This is achieved using photolithography, where a photoresist is applied to the substrate and exposed to light through a mask. The exposed areas are developed and etched away, leaving behind the desired circuit patterns.
The surface of the substrate is treated to enhance solderability and protect against corrosion. Common surface finishes include electroless nickel immersion gold (ENIG) and organic solderability preservatives (OSP). These finishes ensure reliable solder joints and long-term durability.
The final step involves rigorous quality control and testing to ensure the substrates meet the required specifications. Electrical testing, thermal cycling, and mechanical stress tests are performed to verify the performance and reliability of the substrates. Defective units are identified and discarded to ensure only high-quality substrates are used in electronic devices.
The Application Area of RF Package Substrates
RF package substrates have a wide range of applications across various industries. Their unique properties make them suitable for advanced and compact RF systems. The following are some key application areas:
In wireless communication systems, RF package substrates are used to support and interconnect various RF components, such as amplifiers, filters, and antennas. These substrates are critical for maintaining signal integrity and minimizing loss in high-frequency communication devices like smartphones, tablets, and wireless routers.
Radar systems, used in automotive, aerospace, and defense applications, rely on RF package substrates for their high-frequency components. The substrates’ ability to handle high power and maintain signal integrity is essential for accurate radar performance.
In satellite communication systems, RF package substrates are used to support and interconnect RF components that operate at very high frequencies. These substrates must provide excellent thermal management and reliability to ensure the continuous operation of satellite systems.
RF technology is increasingly used in medical devices for diagnostics and treatment. RF package substrates are essential for the reliable operation of medical devices such as MRI machines, RF ablation devices, and wireless health monitors.
The Internet of Things (IoT) encompasses a wide range of connected devices that communicate wirelessly. RF package substrates are used in IoT devices to support RF transceivers and antennas, enabling efficient and reliable wireless communication.
What are the Advantages of RF Package Substrates?
RF package substrates offer several significant advantages, making them a preferred choice in various high-frequency applications. The following are the key advantages:
Enhanced Signal Integrity: RF package substrates are designed to minimize signal loss and distortion, ensuring accurate transmission and reception of high-frequency signals.
Efficient Thermal Management: The substrates provide efficient thermal management through the use of high-conductivity materials and advanced thermal vias, preventing overheating and extending the lifespan of RF components.
Density Interconnections: The design of RF package substrates allows for high-density interconnections, enabling complex and compact RF circuit designs.
Reliability and Durability: RF package substrates are designed to withstand mechanical stresses, thermal cycling, and harsh environmental conditions, ensuring the reliability and durability of RF systems.
Cost Efficiency: Advancements in manufacturing technologies and materials have made the production of RF package substrates more cost-effective, allowing manufacturers to produce high-performance substrates at a lower cost.
FAQ
What is the typical frequency range for RF package substrates?
RF package substrates are designed to handle high-frequency signals, typically in the range of MHz to GHz. The specific frequency range depends on the application and design requirements.
What materials are commonly used in RF package substrates?
Common materials used in RF package substrates include high-performance organic resins (e.g., PTFE, Rogers materials), ceramics (e.g., alumina, aluminum nitride), and metals (e.g., copper, silver). These materials offer excellent electrical conductivity, thermal stability, and mechanical strength.
What are the main applications of RF package substrates?
RF package substrates are used in various applications, including wireless communication, radar systems, satellite communications, medical devices, and IoT devices. Their unique properties make them suitable for advanced and compact RF systems.
How are RF package substrates manufactured?
The manufacturing process of RF package substrates involves material preparation, layer stacking, drilling and via formation, patterning and etching, surface finishing, and rigorous quality control and testing. Each step requires precise control and advanced technology to ensure the quality and performance of the substrates.