What is RF Modules Substrate?
As a leading RF modules substrate manufacturer, we specialize in crafting high-performance substrates tailored to the exacting demands of modern wireless technologies. Our state-of-the-art facilities ensure precision engineering, allowing us to deliver substrates optimized for frequency stability, signal integrity, and thermal management. Backed by years of expertise and relentless innovation, we empower our clients to push the boundaries of connectivity and performance in their RF applications. With a commitment to quality and reliability, we stand as a trusted partner for companies driving the next wave of wireless advancements.
RF module substrate (PCB) plays a vital role in the field of modern wireless communications. Simply put, an RF module substrate is a printed circuit board specifically designed for use in radio frequency electronic equipment. As the carrier of radio frequency circuits, these circuit boards carry various radio frequency components and connections, providing the necessary support structures and signal transmission paths for wireless communication equipment.
The design and manufacturing of RF module substrates requires highly specialized knowledge and technology. First, designers must have a deep understanding of the characteristics of RF circuits, including frequency, wavelength, power, impedance matching, etc. In addition, the design guidelines also include requirements for circuit layout, inter-layer planning, signal integrity, EMI/EMC management, etc. Adherence to these design principles is critical to ensuring the performance and reliability of the final product.
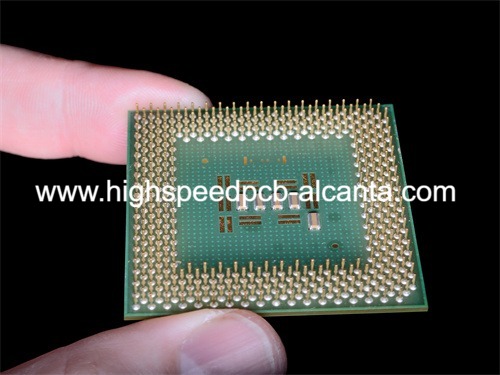
RF Modules Substrate Manufacturer
RF module substrates often adopt multi-layer structures to meet the complexity and performance requirements of RF circuits. Multilayer construction provides better signal integrity and impedance matching while also reducing board size. For high-frequency applications, some special materials such as PTFE (polytetrafluoroethylene) and Rogers are often selected because they have lower dielectric loss and better high-frequency performance.
RF module substrates come in various sizes and shapes, depending on the specific application requirements. Some applications require miniaturized and integrated designs, such as smartphones and wireless sensor networks, while others require larger substrate sizes, such as base station equipment and radar systems.
Overall, RF module substrates play an indispensable role in the field of modern wireless communications. They provide stable and reliable signal transmission and support structures for various wireless communication devices, and promote the continuous progress and innovation of communication technology.
RF Modules Substrate design Reference Guide.
Designing RF module substrates is a complex task that requires precision technology and expertise. Within the design guidelines, there are several key aspects that require special attention to ensure the performance and reliability of the final product.
First, understanding RF signals is crucial. Radio frequency signals have many special characteristics, such as high frequency, short wavelength, and susceptibility to interference. Designers need to understand the propagation characteristics of RF signals, waveguide effects, and how they are transmitted in PCBs in order to effectively design and optimize RF circuits.
Secondly, layout and routing specifications are key aspects of the design. A good layout can minimize signal transmission loss and interference while ensuring signal integrity. Wiring specifications include the design of line width, spacing, layering, routing methods, etc., which need to be accurately adjusted according to the frequency and characteristics of the RF signal.
Signal integrity is another important consideration in the design. In high-frequency radio frequency circuits, signal integrity directly affects the performance and stability of the system. Designers need to pay attention to signal transmission delay, waveform distortion, crosstalk and other issues, and take corresponding measures to ensure signal integrity.
In addition, the management of electromagnetic interference (EMI) and electromagnetic compatibility (EMC) is also an important part of the design guidelines. RF circuits are susceptible to external interference and radiation, so designers need to take measures in the design to reduce interference and ensure the electromagnetic compatibility of the system to meet relevant regulations and standards.
Manufacturers often provide detailed design guidelines that include recommendations and best practices for different RF applications. These guidelines can help designers understand and solve various technical challenges in design, ensuring that the designed products have excellent performance and reliability.
To sum up, designing RF module substrates requires designers to have rich experience and professional knowledge in RF circuit design. By following the recommendations and best practices in the design guide, designers can effectively solve various technical challenges in the design and ensure that the performance and reliability of the final product reach the expected level.
What material is used in RF Modules Substrate?
The material selection of the RF module substrate is one of the key factors affecting its performance and stability. Among the many options available, common materials include FR-4, PTFE (polytetrafluoroethylene), Rogers, and Arlon, among others. These materials have different properties, including dielectric constants, dissipation factors, and thermal properties, so selection requires trade-offs based on the requirements of the specific application.
First, FR-4 is one of the most common PCB materials and has good mechanical strength and heat resistance, making it suitable for most general-purpose RF applications. Its relatively low cost makes it widely adopted in cost-sensitive projects.
And PTFE materials, such as special Teflon, have extremely low loss factors and high dielectric constants, making them excellent in high-frequency RF applications. It can effectively reduce signal loss and improve system performance, so it is widely used in applications requiring high performance and low loss.
High-frequency materials such as Rogers and Arlon are specifically designed for RF and microwave applications and have excellent dielectric properties and stability. Their dielectric constants typically range from 2 to 10, allowing them to meet the stringent signal integrity and performance requirements of high-frequency circuits.
When selecting materials, in addition to considering the dielectric properties, factors such as thermal stability, mechanical strength, and processing performance of the material also need to be considered. For example, applications that operate in high-temperature environments may require the selection of materials with good thermal stability to ensure system reliability and stability.
Taking the above factors into consideration, RF module substrate manufacturers usually select the most appropriate materials to design and manufacture RF module substrates based on customers’ specific needs and application scenarios to ensure that the final product has excellent performance and stability.
What size are RF Modules Substrate?
The size of the RF module substrate is one of the crucial considerations during the design and manufacturing process. The choice of size depends not only on technical specifications but also on application requirements. From micro devices to large base stations, RF module substrates of different sizes have emerged to meet various needs.
For tiny devices, such as smartphones, wearables, and IoT sensors, space is often very limited. Therefore, the RF module substrate needs to be small enough to fit into these compact device sizes. They may only be a few millimeters in size, but still need to maintain sufficient performance and stability to support the functional requirements of the device.
In contrast, large base station equipment such as communication base stations, radar systems and satellite communication equipment have very different size requirements for RF module substrates. These devices typically need to handle larger data volumes and higher frequency ranges, requiring larger substrates to accommodate more RF circuit components and connections. These substrates may be tens of centimeters or larger to meet the device’s performance needs.
Size selection is influenced not only by device functionality and performance, but also by cost and physical space constraints. During the design phase, engineers need to weigh various factors to find the optimal sizing solution. If the substrate is too small, it may cause signal interference and performance issues; if the substrate is too large, it may increase cost and manufacturing complexity. Therefore, size selection is a complex process that requires the consideration of multiple factors.
In addition to performance and cost, power consumption is also one of the important considerations in size selection. Larger baseboards often accommodate more heat sinks and cooling structures, helping to reduce power consumption and improve stability. Therefore, when designing the RF module substrate, power consumption management and heat dissipation design need to be comprehensively considered to ensure long-term stable operation of the equipment.
To sum up, the size selection of RF module substrate is a complex and critical decision-making process that requires comprehensive consideration of multiple factors such as performance, power consumption, cost, and physical space. Through reasonable size design, the RF module substrate can be ensured to achieve optimal performance and stability in various application scenarios, promoting the continuous progress and innovation of wireless communication technology.
The Manufacturer Process of RF Modules Substrate.
The manufacturing process of RF module substrates is a complex process involving multiple links, requiring a high degree of technology and precise operations. The following is a detailed introduction to each aspect of the RF module substrate manufacturing process:
Design verification
Before starting to manufacture the RF module substrate, design verification first needs to be done. This phase includes review and verification of design documents to ensure that the design complies with specifications and requirements. Design verification can also verify circuit performance through simulation and simulation to ensure the performance and reliability of the final product.
Purchase of raw materials
The manufacturing of RF module substrates requires the use of a variety of materials, including substrate materials, metallization materials, chemical treatments, etc. Manufacturers need to carefully select the right material suppliers and ensure that the purchased materials meet quality standards and specifications.
Printing
PCB manufacturing usually starts with printing. During the printing process, the design file is transferred to the substrate, and a special printing technology is used to print the circuit pattern onto the surface of the substrate. The accuracy and quality of printing are critical to the performance of the final product.
Chemical treatment
After printing is completed, the substrate needs to go through a series of chemical treatments, including etching, cleaning and coating. These chemical treatments are designed to remove unwanted metallization layers and ensure a flat and clean substrate surface.
Drilling
Drilling holes on the substrate are used to form circuit connection holes and mounting holes. The accuracy and location of drilling has a significant impact on the performance and reliability of the circuit, so it requires the use of high-precision drilling equipment.
Metalization
Metallization is a critical step in depositing conductive materials onto the surface of a substrate to form circuit connections. This process is typically accomplished using chemical deposition, electroplating, or other metallization techniques.
Assemble
After metallization is completed, the RF module substrate needs to be assembled. This involves soldering the components to the substrate and making the necessary connections and fastenings. The assembly process requires a high degree of precision and skill to ensure that each element is installed and connected correctly.
The last step is to test the manufactured RF module substrate. Testing includes functional testing, performance testing and reliability testing to ensure that the product meets specifications and can operate stably and reliably.
In general, the manufacturing process of RF module substrate is a highly precise and complex process involving multiple links and technologies. Precision and quality control are critical to the performance and reliability of the final product, so manufacturers must strictly enforce manufacturing standards and processes.
The Application area of RF Modules Substrate.
As an indispensable component of modern electronic equipment, RF module substrates play a key role in various fields, provide important support for technological innovation, and promote the development and progress of science and technology.
Communication field
In the field of communications, RF module substrates are widely used in mobile phones, base stations, satellite communications, radar systems and other equipment. They can provide stable and reliable wireless communication connections, support data transmission, voice calls and Internet access, and promote the development of information exchange and social interconnection.
Medical field
In the medical field, RF module substrates are used in medical equipment such as pacemakers, medical imaging equipment and wireless monitoring systems. They can realize the transmission and monitoring of medical data, provide technical support for medical diagnosis and treatment, and improve the level and efficiency of medical services.
Military field
In the military field, RF module substrates are used in military equipment such as radar, navigation systems, and communication equipment. They have the characteristics of anti-interference, high-density integration, and high reliability. They can meet the needs of military operations and command and control, and improve the combat effectiveness and effectiveness of military technology.
Aerospace field
In the aerospace field, RF module substrates are widely used in aerospace devices such as aircraft, satellites, and navigation systems. They can realize functions such as aviation communications, navigation and positioning, and data transmission, ensuring the safe and stable operation of aerospace equipment.
Automotive field
In the automotive field, RF module substrates are used in automotive electronic equipment such as vehicle communication systems, radar sensing systems, and vehicle entertainment systems. They can realize communication between vehicles, autonomous driving technology, in-vehicle infotainment and other functions, and promote the development and popularization of smart car technology.
Industrial control field
In the field of industrial control, RF module substrates are used in industrial automation, remote monitoring, wireless sensor networks and other fields. They enable data exchange and control between devices, improving industrial production efficiency and product quality.
To sum up, RF module substrates play an important role in various fields such as communications, medical, military, aerospace, automotive and industrial control, providing a solid foundation and support for technological innovation and social progress.
What are the advantages of RF Modules Substrate?
The advantage of the RF module substrate lies not only in its improvement over traditional line wiring, but also in its indispensability in wireless communication systems. The following will explore in detail the advantages of RF module substrates over traditional wiring and how these advantages make them an important part of modern wireless communication systems.
Higher integration
RF module substrates allow the integration of multiple RF components and circuits in a relatively small space. In contrast, traditional line routing requires a large amount of wiring and connections, making the overall layout more complex. The high level of integration of the RF module substrate makes the device more compact and suitable for space-critical applications such as smartphones and wireless sensor networks.
Better signal integrity
The design and manufacturing of RF module substrates undergo precise process control, which can effectively reduce signal loss and distortion during transmission. Compared with traditional line wiring, RF module substrates can provide more stable and reliable signal transmission, thereby ensuring data accuracy and communication stability.
Lower signal loss
Since the RF module substrate uses high-quality materials and precise manufacturing processes, its signal transmission loss is usually low. In contrast, traditional line wiring may cause significant signal loss due to factors such as resistance, inductance, and crosstalk. The low signal loss of the RF module substrate makes it perform better in long-distance or high-frequency transmission.
Smaller size
RF module substrates are typically more compact and smaller than traditional wiring. This allows them to be easily integrated into a variety of devices and systems, whether mobile or embedded systems. At the same time, the small size also means lower weight and higher flexibility, helping to design lighter and more portable products.
In general, RF module substrates have the advantages of higher integration, better signal integrity, lower signal loss and smaller size than traditional circuit wiring. These advantages make RF module substrates an indispensable part of modern wireless communication systems, providing stable and reliable RF solutions for various applications, and promoting the continuous innovation and development of wireless technology.
FAQ
What is the future development trend of RF module substrates?
With the continuous development of wireless communication technology and the popularization of smart devices, the demand for RF module substrates will continue to grow. In the future, the development trend of RF module substrates mainly includes the demand for higher frequency, higher integration and lower power consumption to meet the requirements of the new generation of wireless communication systems. At the same time, with the commercialization of 5G technology and the continuous expansion of IoT applications, RF module substrates will play an increasingly important role in various fields and promote the continued innovation and development of the industry.
How long is the manufacturing cycle of RF module substrate?
The manufacturing cycle time for RF module substrates varies depending on project complexity and manufacturer. Typically, the time from design confirmation to final delivery ranges from a few days to a few weeks. Simple projects may be completed in a shorter time, while complex projects may take longer to ensure quality and performance.
What is the cost of RF module substrate?
The cost of an RF module substrate depends on several factors, including the materials selected, board size, design complexity, and production quantity. Generally speaking, higher performance materials and more complex designs result in higher costs. In addition, increased production quantities typically reduce the cost per board. Therefore, for an accurate cost estimate, it is recommended to contact the manufacturer directly to obtain a quote.
What special skills are required for the design of RF module substrates?
Designing RF module substrates requires an in-depth understanding of RF circuits and PCB design. RF circuit design involves knowledge of high-frequency signal transmission, antenna design, impedance matching, etc. In addition, familiarity with professional design software (such as Altium Designer, Cadence Allegro, etc.) and EM simulation tools (such as Ansys HFSS, CST Studio Suite, etc.) is also necessary. In addition, stack design, electromagnetic compatibility (EMC) and signal integrity (SI) considerations for multi-layer boards are also essential skills.
How is thermal management of the RF module substrate handled?
The RF module substrate generates heat during operation, and good thermal management is one of the key factors to ensure device performance and reliability. Common methods include designing a radiator, adding fans, or using metallized plates to increase heat dissipation capacity. In addition, the layout of components must be considered during design to ensure that heat can be effectively dispersed and discharged.