RF/microwave PCB Manufacturer.A premier RF/microwave PCB manufacturer, dedicated to crafting precision circuitry for cutting-edge telecommunications, aerospace, and medical devices. With state-of-the-art facilities and a seasoned team of engineers, we specialize in the fabrication of high-frequency printed circuit boards tailored to meet the demanding requirements of modern wireless communication systems. Our commitment to innovation and quality ensures that every PCB we produce is optimized for performance, reliability, and signal integrity, empowering our clients to push the boundaries of technology and bring their visions to life.
With the rapid development of wireless communication technology, RF (radio frequency) and microwave circuit boards (PCB) play a vital role in modern electronic equipment. As key components for connecting and transmitting high-frequency signals, they provide basic support for the performance and reliability of wireless communication systems. This article will delve into the importance of RF/microwave PCBs and their widespread use in today’s electronics field to help readers gain a deeper understanding of the core value of this key technology.
What is RF/microwave PCB?
An RF/microwave PCB (radio frequency/microwave printed circuit board) is a printed circuit board specifically designed to handle high-frequency signals. In the fields of modern communications and electronics, with the rapid development of wireless technology, RF/microwave PCB has become an indispensable and key component of wireless devices and systems. These circuit boards have excellent high-frequency characteristics and can efficiently transmit signals in the radio frequency (RF) and microwave frequency bands, providing a stable and reliable signal transmission platform for various wireless communication applications.
Compared with traditional printed circuit boards, RF/microwave PCB pays more attention to the optimization of high-frequency characteristics during the design and manufacturing process. First, they use special high-performance materials such as PTFE (polytetrafluoroethylene) and FR-4 (fiberglass reinforced epoxy), which have lower losses, excellent dielectric properties and highly stable properties , able to maintain stable transmission of signals in high-frequency environments. Secondly, the design of RF/microwave PCB takes into account factors such as signal integrity, impedance matching, coupling, and electromagnetic compatibility to ensure the performance and reliability of the circuit board under high-frequency operating conditions.
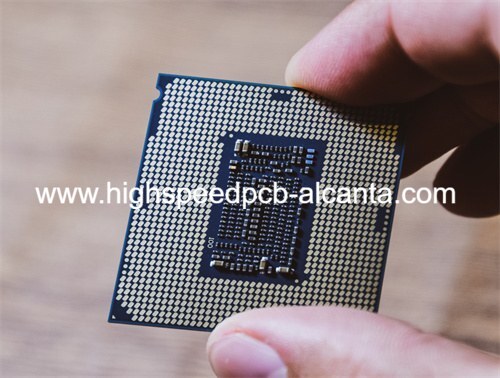
RF/Microwave PCB Manufacturer
RF/microwave PCB is widely used in communications, radar, satellite communications, wireless networks, military and aerospace and other fields. In communication systems, RF/microwave PCB is used to manufacture key components such as antennas, amplifiers, filters, and RF front-end modules to provide reliable signal transmission and processing capabilities for wireless communications. In radar and satellite communication systems, RF/microwave PCB plays a key role, supporting high-precision and high-reliability signal processing and data transmission. In the military and aerospace fields, RF/microwave PCB is an indispensable component and is used to manufacture various high-performance, high-reliability wireless communication systems and radar equipment.
In general, RF/microwave PCB provides reliable technical support for various wireless communication applications through its excellent high-frequency characteristics and stable signal transmission capabilities. With the continuous advancement of wireless technology and the expansion of application fields, RF/microwave PCB will continue to play an important role in promoting the development and innovation of wireless communication technology.
RF/microwave PCB design Reference Guide.
When designing an RF/microwave PCB, designers need to consider many key factors to ensure that the board can provide reliable performance in high-frequency environments. The following are some design reference guides to help designers optimize RF/microwave PCB designs:
Signal integrity
The design of the RF/microwave PCB must ensure that the signal is not distorted or attenuated during transmission. This involves good layout and routing practices to minimize signal path lengths and impedance mismatches.
Transmission line characteristics
Transmission lines are one of the most critical parts of RF/microwave PCBs. Designers must select appropriate transmission line types (e.g., microstrip, coaxial, etc.) and consider factors such as their characteristic impedance, transmission speed, and attenuation.
Impedance matching
Due to the characteristics of high-frequency signals, impedance matching becomes critical. Designers need to ensure that all transmission lines, connectors, and devices are impedance matched to minimize signal reflections and losses.
Coupling
In RF/microwave PCB design, coupling effects may exist between different signal paths, leading to signal interference and crosstalk. Designers must take measures, such as proper spacing and shielding, to minimize coupling effects.
Electromagnetic compatibility
Due to the characteristics of high-frequency signals, RF/microwave PCB design must consider electromagnetic interference (EMI) and electromagnetic compatibility (EMC) issues. Proper ground wire design, shielding and filters can help reduce unwanted interference and ensure the electromagnetic compatibility of your equipment.
In order to achieve the above goals, designers should follow strict specifications and best practices, including using professional PCB design software, conducting simulation and simulation analysis, conducting prototype testing and verification, etc. In addition, industry standards and guidelines related to RF/microwave PCBs should also be considered important reference materials during the design process.
To sum up, the design of RF/microwave PCB requires designers to have in-depth understanding and rich experience in signal integrity, transmission line characteristics, impedance matching, coupling and electromagnetic compatibility. By following strict specifications and best practices, designers can ensure that RF/microwave PCBs have excellent performance and reliability in high-frequency environments.
What material is used in RF/microwave PCB?
RF/microwave PCBs often use high-performance materials to meet stringent requirements for high-frequency signal transmission and stability. Among them, PTFE (polytetrafluoroethylene), FR-4 (glass fiber reinforced epoxy resin) and RO4003C are the most common choices. These materials have a range of excellent properties that make them ideal for RF/microwave PCB manufacturing.
First, PTFE (polytetrafluoroethylene) is a material with excellent dielectric properties and low losses. It maintains a low dielectric constant and dielectric loss at high frequencies, thereby ensuring the stability and accuracy of signal transmission. In addition, PTFE has good thermal and chemical stability and is suitable for applications under various harsh environmental conditions.
Secondly, FR-4 is a common glass fiber reinforced epoxy resin composite material. It has good mechanical strength and heat resistance and is suitable for applications in high temperature environments. In RF/microwave PCBs, FR-4 is often used as a substrate to provide mechanical support and structural support.
In addition, RO4003C is an organic composite material specially designed for high-frequency applications. It has low dielectric loss, high dielectric constant and consistent dielectric properties, making it excellent in high-frequency signal transmission. RO4003C material also has excellent dimensional stability and processing performance, making it suitable for complex RF/microwave PCB designs.
To sum up, RF/microwave PCB usually uses high-performance materials such as PTFE, FR-4 and RO4003C. These materials have low loss, high thermal stability and excellent dielectric properties, making them suitable for a variety of high-frequency applications. By selecting appropriate materials and combining them with precision manufacturing processes, high-performance and reliable RF/microwave PCB designs can be achieved, supporting the development of modern wireless communication technology.
What size are RF/microwave PCB?
The size and shape of RF/microwave PCBs are determined based on specific application requirements. Due to the particularity of RF (radio frequency) and microwave signals, the design of RF/microwave PCB must take into account the frequency, wavelength and propagation characteristics of electromagnetic fields. Therefore, their size and shape depend largely on the required functionality and performance.
First, for some small applications, such as microstrip antennas or micro antenna arrays, RF/microwave PCBs can be very small. These small PCBs are often used in areas such as mobile devices, wireless sensor networks, or medical devices. They may require precision layout and manufacturing to ensure accurate transmission and reception of high-frequency signals.
On the other hand, for some large-scale applications, such as RF front-end modules or microwave communication systems, RF/microwave PCBs may be very large and complex. These large PCBs often contain multiple layers of circuitry, complex RF components, and extensive signal processing circuitry. They are usually used in communication base stations, satellite communications, radar systems, spacecraft and other fields, requiring a high degree of integration and reliability.
Whether it is a small or large RF/microwave PCB, its design and manufacturing require precise processes and technologies. During the design phase, engineers must consider factors such as signal integrity, impedance matching, coupling, and routing rules to ensure circuit stability and performance. During the manufacturing process, every step, including chemical processing, molding, printing, copper laying, cutting and assembly, must be strictly controlled to ensure the quality and reliability of PCBs.
In general, the size and shape of the RF/microwave PCB depends on its required functions and performance. It can be a small microstrip antenna or antenna array, or a large RF front-end module or microwave communication system. Regardless of size, these PCBs play a vital role in modern wireless communication systems, supporting high-performance, high-reliability communication networks.
The Manufacturer Process of RF/microwave PCB.
The manufacturing process of RF/microwave PCB is a complex and precise project, which involves multiple key steps, from design to final assembly, each step has a vital impact on the performance and quality of the final product.
The first is the design and layout phase. At this stage, engineers design the layout and connection methods of the circuit board based on the customer’s needs and application scenarios. They must consider factors such as signal integrity, transmission line characteristics, impedance matching, etc., and use professional design software for simulation and optimization.
Next is material selection. Based on the design requirements and application scenarios, engineers select appropriate high-performance materials, such as PTFE, FR-4, RO4003C, etc. These materials have low loss, high thermal stability and excellent dielectric properties, and can meet the needs of high-frequency signal transmission.
Then comes chemical processing and shaping. During this stage, engineers chemically treat the selected materials to remove unnecessary oxides and surface contaminants. They are then formed into the desired shape and size in preparation for subsequent processing and printing.
Printing is one of the key steps in the manufacturing process. At this stage, engineers use special printing technology to imprint the circuit pattern and component layout on the surface of the circuit board. This requires high-precision equipment and technology to ensure printing accuracy and quality.
Next is laying the copper. Copper is one of the most commonly used conductive materials in RF/microwave PCBs, where it is used to connect various components and signal paths on the board. Engineers use chemical methods or electroplating techniques to form a layer of copper on the surface of the circuit board to create conductive connections.
Cutting is an important step in cutting large circuit boards to the desired size. Engineers use cutting machines or laser cutters to precisely cut circuit boards into the required size and shape to suit different application scenarios and equipment requirements.
Finally comes assembly. At this stage, engineers accurately solder various electronic components, such as chips, resistors, capacitors, etc., onto the circuit board. They use automated equipment and sophisticated technology to ensure assembly accuracy and stability.
In general, the manufacturing process of RF/microwave PCB is a precise and complex process that requires engineers to have extensive experience and skills to ensure that the performance and quality of the circuit board reach the best level. Only through precise manufacturing processes can high-quality circuit boards that meet the needs of high-frequency applications be produced.
The Application area of RF/microwave PCB.
RF/microwave PCB, as the core component of high-frequency signal transmission, plays a vital role in many fields. The following are the application expansions of RF/microwave PCB in communications, radar, satellite communications, wireless networks, military and aerospace and other fields:
Communication field
In the field of communications, RF/microwave PCB is widely used in wireless base stations, antenna systems, microwave receivers and transmitters and other equipment. They ensure the high efficiency and stability of signal transmission and support various communication methods such as mobile phone communications, satellite communications and Internet connections.
Radar system
Radar systems rely on the rapid transmission and accurate detection of high-frequency signals, and RF/microwave PCBs play a key role. From military defense to weather monitoring, radar systems require reliable circuit boards to support their complex signal processing and data transmission functions.
Satellite Communications
In satellite communications, RF/microwave PCBs are used in satellite antennas, radio frequency front-end modules and satellite communications terminal equipment. They ensure the stable transmission of satellite signals and support various satellite communication services such as satellite phones, satellite broadcasts and remote monitoring.
Wireless network
In the field of wireless networks, such as Wi-Fi, cellular networks and the Internet of Things (IoT), RF/microwave PCBs are widely used in wireless routers, base stations and terminal equipment. They ensure high-speed transmission of wireless signals and stable connections, supporting the wireless network communication needs in modern life.
Military applications
The military field has extremely high requirements for high-performance and high-reliability communication systems, and RF/microwave PCB is a key component to meet these requirements. From military radar to communication reconnaissance, RF/microwave PCB plays a vital role in military equipment, ensuring the security and stability of military communications and intelligence transmission.
Aerospace applications
In the aerospace field, RF/microwave PCB is used in spacecraft communication systems, navigation systems and control systems. They need to be able to work under extreme environmental conditions, including vacuum, radiation and high temperatures, to ensure the normal operation of the spacecraft’s communication and control functions.
In general, RF/microwave PCB plays an indispensable role in various fields such as communications, radar, satellite communications, wireless networks, military and aerospace. Their high performance, high reliability and stability provide a solid foundation and support for the development and progress of modern wireless communication systems.
What are the advantages of RF/microwave PCB?
RF/microwave PCBs have significant advantages over traditional circuit boards in many aspects, making them ideal for many high-frequency applications. Here’s a more detailed look at its benefits:
Low signal loss
RF/microwave PCB uses high-performance materials and precision manufacturing processes to effectively reduce signal loss during transmission. The transmission of high-frequency signals requires consideration of signal integrity and loss. RF/microwave PCB reduces signal attenuation and ensures signal stability and accuracy by optimizing design and material selection.
Higher operating frequency
RF/microwave PCB has a higher operating frequency range and can support a wider range of frequency applications. Their material properties and design optimization enable them to operate in the frequency range of GHz or even THz, making them suitable for high-frequency applications such as wireless communications, radar, and satellite communications.
Better anti-interference ability
RF/microwave PCB is designed with electromagnetic compatibility (EMC) in mind, using shielding technology and optimized layout, which can effectively reduce the impact of external interference on the circuit. This enables them to maintain stable performance in complex electromagnetic environments and improves system reliability and anti-interference capabilities.
Smaller size
RF/microwave PCBs typically have smaller sizes and higher levels of integration, allowing for more compact designs and lighter devices. This is particularly important for application scenarios that require equipment to be miniaturized and lightweight, such as portable wireless devices, aerospace systems, etc.
Improve system performance and stability
Combining the above advantages, RF/microwave PCB can significantly improve the performance and stability of the system. Low signal loss, high operating frequency, excellent anti-interference ability and compact size design enable RF/microwave PCB to achieve higher data transmission rates, longer transmission distances and more stable signal quality, thereby meeting the needs of complex high-frequency system requirements.
In general, RF/microwave PCB has an irreplaceable position in the high-frequency field. Its excellent performance and characteristics make it the first choice for many high-frequency applications, promoting the development and innovation of wireless communications, radar, satellite communications and other fields. .
FAQ
What is special about RF/microwave PCB design?
RF/microwave PCB design needs to consider the particularities of high-frequency signal transmission, including signal integrity, transmission line characteristics, impedance matching and coupling. In addition, attention needs to be paid to the management of electromagnetic compatibility and radio frequency interference to ensure that the circuit board works stably and reliably in a high-frequency environment.
What are the considerations in RF/microwave PCB material selection?
When selecting materials, factors such as dielectric constant, loss factor, thermal stability and mechanical strength need to be considered. Commonly used materials include PTFE (polytetrafluoroethylene) and FR-4 (fiberglass-reinforced epoxy), which have low loss, high dielectric constant and excellent mechanical properties.
How to ensure the high frequency characteristics of RF/microwave PCB?
High-frequency characteristics depend on factors such as circuit board layout, interlayer copper laying, impedance matching, and line length. Through reasonable design and strict control of the manufacturing process, the circuit board can be ensured to have stable high-frequency characteristics to meet the requirements of specific applications.
What are the key steps in the RF/microwave PCB manufacturing process?
The manufacturing process includes multiple steps such as design, material selection, chemical processing, molding, printing, copper laying, cutting and assembly. Every step is critical, and any mistake in any step may affect the performance and quality of the circuit board.