As a leading RF high-frequency flip chip substrate manufacturer, we specialize in crafting cutting-edge solutions for the most demanding technological applications. With a commitment to innovation and precision engineering, our substrates empower next-generation electronics with unparalleled performance and reliability. Leveraging state-of-the-art fabrication techniques and advanced materials, we cater to the evolving needs of industries such as telecommunications, aerospace, and beyond. Our dedication to quality ensures that each substrate meets the highest standards, enabling seamless integration into diverse systems and unlocking new possibilities in the realm of RF technology.
As a core component of modern electronic equipment, PCB (Printed Circuit Board) plays a vital role in various industries. In the field of RF (radio frequency) high-frequency flip chip substrate manufacturing, PCB plays a key role. RF high-frequency flip chip substrate is a special PCB specially used for the manufacturing of radio-frequency high-frequency electronic devices. It not only needs to meet the stability and performance requirements in high-frequency environments, but also needs to have high integration and size advantages. In this article, we will delve into the key concepts of RF high-frequency flip chip substrate manufacturers and explain to you the importance of PCB and its application in the electronic field.
What is RF High Frequency Flip Chip Substrate?
When talking about RF high frequency flip chip substrate, we first need to understand its nature and function. RF high-frequency flip chip substrate, referred to as RF PCB, is a special PCB specially used for the manufacturing of radio frequency high-frequency electronic devices. Compared with traditional PCB, RF PCB needs to work in a higher frequency environment and has higher requirements for the stability and performance of signal transmission.
RF PCBs are usually made of high-frequency materials. These materials have excellent dielectric properties and conductive properties, which can effectively reduce signal loss and interference and improve the reliability of signal transmission. Compared with ordinary PCBs, RF PCBs are more precise and strict in material selection and manufacturing processes to ensure their stability and performance in high-frequency environments.
In the manufacturing process of RF high-frequency flip chip substrates, advanced manufacturing processes and equipment, such as precision printing technology, laser processing technology, etc., are usually used to ensure the accuracy and consistency of the board. In addition, for specific application requirements, special processing may be required, such as controlling impedance, optimizing wiring, etc., to meet customer performance and size requirements.
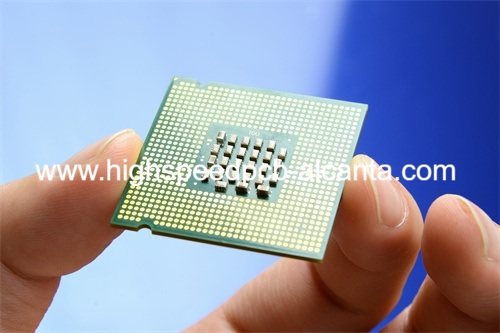
RF High Frequency Flip Chip Substrate Manufacturer
In general, RF high-frequency flip chip substrates play an important role in the manufacturing of RF high-frequency electronic devices. It not only needs to have excellent high-frequency performance and stability, but also needs to meet customers’ strict requirements for size, integration and reliability. Therefore, understanding the characteristics and manufacturing processes of RF PCB is crucial for practitioners in the electronics industry and researchers in related fields.
RF High Frequency Flip Chip Substrate design Reference Guide.
The manufacturing of RF high-frequency flip chip substrates is a highly sophisticated process that requires strict adherence to a series of reference guidelines and best practices. Having a good reference guide is critical to ensuring product quality and performance. The following are the key contents of the reference guide for RF high-frequency flip chip substrate manufacturing:
Familiar with the characteristics of various high frequency materials
In the manufacturing process of RF high-frequency flip chip substrates, it is crucial to select appropriate high-frequency materials. Different high-frequency materials have different dielectric properties, thermal stability and mechanical properties. Manufacturers need a deep understanding of the properties of various high-frequency materials in order to select the materials best suited for specific applications.
Master advanced design software and tools
In the RF high-frequency flip chip substrate design stage, the use of advanced design software and tools is essential. These tools help manufacturers perform precise routing and designs to ensure signal integrity and performance stability in high-frequency environments. Proficiency in these tools increases design efficiency and reduces errors.
Learn about the latest manufacturing technologies and standards
With the continuous advancement of technology, RF high-frequency flip chip substrate manufacturing technology is also constantly evolving. Manufacturers need to always pay attention to the latest trends and standard requirements in the industry to ensure that they always stay ahead of the curve. Understanding the latest manufacturing technologies and standards can help manufacturers optimize production processes and improve product quality.
The manufacturing of RF high-frequency flip chip substrates is a complex and precise process that requires manufacturers to have deep technical strength and rich experience. By having a good reference guide at hand, manufacturers can better understand the key elements of RF high frequency flip chip substrate manufacturing and ensure the highest level of product quality and performance. It is hoped that the reference guide provided in this article can provide some help and guidance to RF high-frequency flip chip substrate manufacturers and promote the continued development and progress of the industry.
What material is used in RF High Frequency Flip Chip Substrate?
In the manufacturing of RF high-frequency flip chip substrates, material selection is crucial and directly affects the performance and reliability of the product. The following are some commonly used materials and their properties in high frequency environments:
PTFE (polytetrafluoroethylene)
PTFE is an inorganic compound with excellent dielectric properties and high-frequency characteristics. Its low dielectric constant and low loss tangent make it ideal for high frequency circuit boards. The PTFE substrate can provide excellent signal transmission performance in high-frequency environments, as well as excellent heat resistance and chemical stability.
FR-4
FR-4 is a glass fiber reinforced epoxy resin substrate commonly used in general PCB manufacturing. Although the performance of FR-4 materials in high-frequency environments is not as good as that of PTFE materials, its lower cost and good mechanical strength and processability make it still widely used in some low- and medium-frequency applications.
Metallized ceramics
Metallized ceramics are a special type of material consisting of a metal layer on a ceramic substrate. This material has a low dielectric constant and losses while possessing good thermal conductivity and mechanical strength, making it suitable for high-power and high-frequency applications. Metallized ceramic substrates are widely used in wireless communication systems in the microwave and millimeter wave bands.
Other special materials
In addition to the common materials mentioned above, there are also some special materials used for specific high-frequency applications, such as silicon nitride (Si3N4) substrate, aluminum oxide (Al2O3) substrate, etc. These materials have specific dielectric and conductive properties that meet the needs of specific applications.
When selecting materials, manufacturers need to consider factors such as product performance requirements, cost budget, and manufacturing processes. Through reasonable selection of materials and combined with precise manufacturing processes, RF high-frequency flip chip substrates with stable performance and high reliability can be produced to meet customer needs and expectations.
What size are RF High Frequency Flip Chip Substrate?
When it comes to the size of RF high-frequency flip chip substrates, the flexibility and versatility is remarkable. The size of this substrate is usually determined based on specific application requirements, as different application scenarios require different sizes of substrates to meet their functional and performance requirements.
First, let us consider micro-sized chip-scale RF high-frequency flip chip substrates. These micro-sized substrates are often used in small devices or applications that require a high degree of integration. For example, smart wearables, portable medical devices, or other electronic products with limited size may require very small substrates to accommodate their circuits and components. In this case, the size of the RF high-frequency flip chip substrate must be carefully designed to ensure high performance and stable signal transmission in a limited space.
On the other hand, large-sized communication equipment-level RF high-frequency flip chip substrates are also very common. These substrates may be used in wireless base stations, satellite communications equipment, or other large communications systems. In this case, the size of the substrate is usually larger to accommodate the complex circuit layout, large number of components and interfaces. The large size base plate also provides better heat dissipation performance and can accommodate more functional modules, thereby improving the performance and reliability of the entire system.
Whether it is a micro-sized chip level or a large-sized communication equipment level, the size design of the RF high-frequency flip chip substrate must take into account multiple factors, including circuit layout, component layout, heat dissipation requirements, mechanical strength, etc. Therefore, substrate manufacturers must have advanced design tools and technologies to meet the needs of different application scenarios.
In general, the size design of the RF high-frequency flip chip substrate is highly flexible and can meet the needs of various application scenarios. Whether micro or large, precision design and manufacturing techniques are required to ensure substrate performance and reliability.
The Manufacturer Process of RF High Frequency Flip Chip Substrate.
The manufacturing process of RF high-frequency flip chip substrates is a complex process involving multiple key steps, requiring precise manufacturing processes and strict quality control to ensure stable performance of the final product. In this section, we will delve into the manufacturing process of RF high-frequency flip chip substrates to better understand this critical area.
Design
The first step in manufacturing an RF high-frequency flip chip substrate is design. The design process involves determining key parameters such as circuit layout, routing, hierarchy, etc. During the design stage, the signal transmission characteristics in high-frequency environments need to be taken into consideration to ensure the stability and performance of the circuit.
Material selection
Material selection is one of the key aspects of RF high-frequency flip chip substrate manufacturing. According to specific application needs and design requirements, manufacturers need to choose appropriate high-frequency materials, such as PTFE (polytetrafluoroethylene), FR-4, etc. These materials have excellent high-frequency characteristics and stability and can meet the high-frequency environment the following requirements.
Plate preparation
During the sheet preparation stage, the selected material is processed into a substrate with specific dimensions and thickness. This involves cutting, polishing, copper plating and other process steps to ensure the surface smoothness and flatness of the substrate, laying a good foundation for subsequent process steps.
Printing
Printing is one of the important links in the manufacturing process of RF high-frequency flip chip substrates. During the printing process, the designed circuit pattern needs to be transferred to the surface of the substrate through printing technology. Commonly used methods include screen printing, inkjet printing, etc. to ensure the accuracy and stability of circuit wiring.
Assemble
Assembly is the final step in RF high frequency flip chip substrate manufacturing. During the assembly process, the electronic devices need to be accurately installed on the substrate according to the design requirements, and processed by welding, packaging and other processes to ultimately form a complete high-frequency flip chip substrate product.
The manufacturing process of RF high-frequency flip chip substrates involves multiple key steps, each of which requires precise manufacturing processes and strict quality control to ensure the stable performance and reliability of the final product. By in-depth understanding of the manufacturing process of RF high-frequency flip chip substrates, we can better understand its importance and application prospects in the field of high-frequency electronics.
We hope that the contents of this section can provide readers with some useful information and inspiration, and promote the further development and application of RF high-frequency flip chip substrate manufacturing technology.
The Application area of RF High Frequency Flip Chip Substrate.
RF high-frequency flip chip substrate plays a vital role in the field of modern technology. It is widely used in wireless communications, radar, satellite communications, medical equipment and other fields, providing a solid foundation for these applications.
Wireless communication
In the field of wireless communications, RF high-frequency flip chip substrates are widely used in communication equipment such as mobile phones, wireless network equipment, and Bluetooth devices. These devices require stable high-frequency performance to ensure the reliability and speed of data transmission, and RF high-frequency flip chip substrates are ideal for meeting this demand.
Radar
Radar systems are important equipment in modern military and civilian fields and are used to detect, track and identify targets. RF high-frequency flip chip substrate plays a key role in radar systems. Its stable performance and high-frequency characteristics can ensure the accuracy and reliability of radar systems.
Satellite Communications
Satellite communications are an important part of modern communications technology and are used to achieve global communications coverage and data transmission. RF high-frequency flip chip substrates are widely used in satellite communication equipment. Its excellent high-frequency performance can ensure the stable operation of satellite communication systems in complex environments.
Medical equipment
In the medical field, RF high-frequency flip chip substrates are used in various medical equipment, including medical imaging equipment, wireless medical monitoring equipment, etc. These devices require stable high-frequency performance and reliability to ensure accurate transmission of medical data and reliability of diagnostic results, and RF high-frequency flip chip substrates are ideal for meeting this need.
In summary, the application of RF high-frequency flip chip substrates in wireless communications, radar, satellite communications, medical equipment and other fields has been widely recognized. Its stable performance and reliability provide strong support for technological innovation and development in these fields, and also bring more convenience and possibilities to our life and work.
What are the advantages of RF High Frequency Flip Chip Substrate?
RF high-frequency flip chip substrate is a special PCB type optimized for high-frequency applications. Compared with traditional PCBs, it has obvious advantages in many aspects. The advantages of RF high-frequency flipping chip substrates will be introduced in detail below.
Better high frequency performance
The RF high-frequency flip chip substrate is optimized for high-frequency environments during the design and manufacturing process. Its material selection, interlayer structure and wiring methods are precisely designed to ensure excellent signal transmission characteristics and stability under high-frequency conditions. In contrast, traditional PCBs may suffer from signal attenuation, crosstalk and other problems in high-frequency environments, while RF high-frequency flip chip substrates can better meet the performance requirements of high-frequency electronic equipment.
Lower signal loss
Because the RF high-frequency flip chip substrate uses high-quality high-frequency materials and uses precise manufacturing processes to ensure the quality of the board and the stability of the inter-layer connection, its signal loss is low. During high-frequency signal transmission, the reduction of signal loss means less energy loss and more stable signal transmission, thereby improving system performance and reliability.
Higher integration
The RF high-frequency flip chip substrate has a higher integration level and can achieve more functions and connections in a smaller space. Through advanced design and manufacturing technology, more devices can be integrated onto the same substrate, thereby reducing the size and weight of the entire system. This is particularly important for modern high-frequency electronics, which often require more functionality and performance in the smallest possible space.
Smaller size
Since the RF high-frequency flip chip substrate has higher integration and better performance, smaller size substrates can be designed. In comparison, traditional PCBs may require more layers and larger sizes to achieve the same functionality and performance, which is not suitable in some application scenarios with higher size requirements. The RF high-frequency flip chip substrate can meet the compact size requirements of modern high-frequency electronic equipment, making it more competitive in various application scenarios.
To sum up, the RF high-frequency flip chip substrate has better high-frequency performance, lower signal loss, higher integration and smaller size than traditional PCB. These advantages enable it to better meet the performance and size requirements of modern high-frequency electronic equipment, bringing new opportunities and challenges to the development of the electronics industry.
FAQ
Is the design and manufacturing of RF high-frequency flip chip substrates subject to specific industry standards and specifications?
Yes, the design and manufacturing of RF high-frequency flip chip substrates are subject to a variety of industry standards and specifications, including but not limited to relevant standards of IPC (Printed Circuit Institute), MIL-STD (Military Standard), and customer-specific requirements, etc. . Following these standards and specifications can ensure that the RF high-frequency flip chip substrate has stable performance and reliability and meets customer needs and industry standard requirements.
What is the difference between RF high-frequency flip chip substrate and traditional PCB?
There are obvious differences between the RF high-frequency flip chip substrate and traditional PCB in material selection, design optimization and manufacturing process. Traditional PCBs usually use conventional materials such as FR-4, while RF high-frequency flip chip substrates use high-frequency materials such as PTFE to ensure better high-frequency performance and signal transmission characteristics. In addition, the design of RF high-frequency flip chip substrates is usually optimized for high-frequency environments, using special layouts and layer stacks to reduce signal loss and crosstalk and improve overall performance.
How long is the manufacturing cycle for RF high-frequency flipping chip substrates?
The manufacturing cycle of RF high-frequency flip chip substrate depends on the specific design requirements and process flow. Generally, it may take several weeks from design confirmation to sample production. For large-scale production orders, the manufacturing cycle may be longer and need to be adjusted and arranged according to the actual situation. Our manufacturing team will do their best to ensure efficient production and meet customer needs in a timely manner.
What are the main application areas of RF high-frequency flipping chip substrates?
RF high-frequency flip chip substrates play an important role in various high-frequency electronic devices and are mainly used in wireless communications, radar systems, satellite communications, medical equipment and other fields. In these fields, there are high requirements for high-frequency performance, signal transmission stability and size. RF high-frequency flip chip substrates can meet these requirements and provide key support for equipment performance improvement.