RF Cavity PCBs Manufacturer.As a leading RF Cavity PCBs manufacturer, we specialize in producing high-frequency circuit boards designed for optimal performance in demanding RF applications. Our advanced manufacturing techniques ensure precision, reliability, and superior quality, making our RF Cavity PCBs ideal for telecommunications, aerospace, and defense industries. With a commitment to innovation and excellence, we provide customized solutions to meet the unique requirements of our clients, ensuring robust and efficient RF performance.
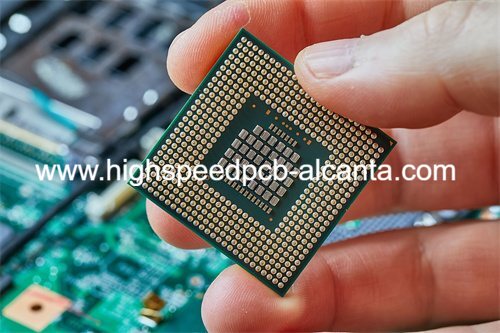
RF Cavity PCBs Manufacturer
RF Cavity PCBs (Radio Frequency Cavity Printed Circuit Boards) are specialized circuit boards designed for high-frequency applications. These boards are integral to the performance of RF and microwave systems, providing superior signal integrity, reduced loss, and enhanced thermal management. Their unique design incorporates cavities or recessed areas that house components, thereby optimizing the overall functionality and performance of the system.
What are RF Cavity PCBs?
RF Cavity PCBs are designed to support radio frequency and microwave circuits. Unlike conventional PCBs, RF Cavity PCBs include cavities or pockets that allow for the precise placement of components such as filters, amplifiers, and antennas. These cavities help to reduce parasitic effects, improve signal isolation, and manage thermal loads more effectively.
Cavity Formation: The cavities are typically milled or etched into the PCB substrate, providing a custom fit for components. This allows for a more compact and efficient layout.
Material Selection: High-frequency laminate materials, such as Rogers or Taconic, are often used for RF Cavity PCBs due to their low dielectric loss and stable performance at high frequencies.
Signal Integrity: By minimizing the distance between components and optimizing the routing of RF signals, these PCBs ensure superior signal integrity and performance.
Design Reference Guide for RF Cavity PCBs
Choosing the right material is critical for the performance of RF Cavity PCBs. Materials such as Rogers RT/duroid, Taconic, and Isola are popular choices due to their low dielectric constants and minimal signal loss. The material must also exhibit good thermal stability and mechanical robustness to withstand the manufacturing process and operational stresses.
The design of the cavities is a crucial aspect of RF Cavity PCBs. The size, shape, and depth of the cavities must be carefully calculated to accommodate the components and maintain optimal performance. This often involves advanced CAD tools and simulation software to model the electromagnetic fields and thermal behavior.
Effective thermal management is essential for RF applications. Techniques such as the incorporation of thermal vias, heat sinks, and metal-backed substrates can be used to dissipate heat generated by high-power components. Proper thermal design ensures reliability and longevity of the PCB.
Maintaining controlled impedance is vital for RF circuits to ensure signal integrity and minimize reflections. This requires precise design of trace widths, spacing, and layer stack-up. Simulation tools are often used to predict and optimize the impedance characteristics of the PCB.
Careful placement and routing of components are necessary to minimize parasitic effects and crosstalk. High-frequency components should be placed close to each other, and signal traces should be kept as short as possible. Shielding techniques can also be employed to isolate sensitive signals.
What Materials are Used in RF Cavity PCBs?
RF Cavity PCBs require materials that can handle high frequencies with minimal loss and distortion. Common materials include:
Rogers RT/duroid: Known for its low dielectric loss and stable performance across a wide frequency range. It is widely used in RF and microwave applications.
Taconic: Offers high-frequency laminates with low loss and excellent thermal stability, suitable for demanding RF applications.
Isola: Provides high-performance materials with low dielectric constant and dissipation factor, ideal for high-frequency circuits.
PTFE (Polytetrafluoroethylene): Often used in combination with woven glass or ceramic fillers, PTFE materials offer excellent electrical properties and high thermal resistance.
Ceramic-filled Hydrocarbon Materials: These materials combine the benefits of ceramics and hydrocarbons, providing low loss and high thermal conductivity.
What Sizes are RF Cavity PCBs?
The size of RF Cavity PCBs can vary widely depending on the application and design requirements. However, common factors influencing the size include:
Component Size and Layout: The size of the components and their layout on the PCB determine the overall dimensions. RF Cavity PCBs often need to accommodate large or multiple components in a compact space.
Frequency Range: Higher frequency applications may require more precise and complex designs, potentially influencing the size and complexity of the PCB.
Thermal Management: The need for effective thermal management may affect the size, as additional space may be required for heat sinks, thermal vias, or metal backing.
Standard and Custom Sizes: While there are standard sizes for some applications, RF Cavity PCBs are often custom-designed to meet specific requirements, leading to a wide range of possible sizes.
The Manufacturing Process of RF Cavity PCBs
The manufacturing process for RF Cavity PCBs involves several steps to ensure precision and performance:
CAD Design: The process begins with detailed CAD design, incorporating all the necessary cavities, traces, and components.
Simulation: Electromagnetic and thermal simulations are conducted to optimize the design and ensure it meets the desired performance criteria.
Lamination: The selected high-frequency laminate material is prepared, which may involve bonding multiple layers together.
Cavity Formation: Cavities are created using precise milling or etching techniques.
Photo-etching: The circuit pattern is transferred onto the PCB using photo-etching techniques, which involve applying a photoresist, exposing it to UV light through a mask, and etching away the unprotected areas.
Plating: Conductive traces are plated with copper, and vias are filled or plated to establish interconnections between layers.
Surface Mount Technology (SMT): Components are placed and soldered onto the PCB using automated SMT processes.
Flip-Chip Bonding: For certain applications, flip-chip bonding may be used to attach components with minimal interconnection length.
Electrical Testing: The PCB undergoes rigorous electrical testing to ensure all connections are intact and the board functions as intended.
Thermal Testing: Thermal tests verify the board’s ability to dissipate heat and maintain performance under operational conditions.
Final Inspection: A thorough inspection ensures the board meets all design specifications and quality standards.
The Application Area of RF Cavity PCBs
RF Cavity PCBs are used in various high-frequency and high-performance applications:
Telecommunications: Used in base stations, transceivers, and other communication devices that require high-frequency signal processing.
Aerospace and Defense: Employed in radar systems, avionics, and other critical defense electronics where reliability and performance are paramount.
Medical Devices: Integrated into medical imaging equipment, diagnostic tools, and other devices that require precise RF signal handling.
Automotive: Utilized in advanced driver-assistance systems (ADAS), vehicle-to-everything (V2X) communication, and other automotive electronics.
Consumer Electronics: Found in high-frequency consumer electronics like smartphones, Wi-Fi routers, and satellite communication devices.
What are the Advantages of RF Cavity PCBs?
RF Cavity PCBs offer several advantages for high-frequency applications:
Superior Signal Integrity: The optimized design and material selection ensure minimal signal loss and distortion, providing high-quality signal transmission.
Enhanced Thermal Management: The incorporation of cavities and advanced thermal management techniques helps to dissipate heat effectively, maintaining performance and reliability.
Reduced Parasitic Effects: The precise placement of components within cavities minimizes parasitic inductance and capacitance, improving overall circuit performance.
High Integration Density: RF Cavity PCBs allow for the integration of complex RF circuits in a compact form, saving space and reducing the overall size of the device.
Customizability: The ability to create custom cavity designs and layouts allows for tailored solutions that meet specific application requirements.
Durability and Reliability: The use of high-performance materials and advanced manufacturing techniques ensures that RF Cavity PCBs are durable and reliable, even in demanding environments.
FAQ
What are the main benefits of using RF Cavity PCBs in high-frequency applications?
RF Cavity PCBs provide superior signal integrity, enhanced thermal management, reduced parasitic effects, high integration density, customizability, and reliability, making them ideal for high-frequency applications.
How are cavities in RF Cavity PCBs formed?
Cavities in RF Cavity PCBs are typically formed through precise milling or etching techniques, which allow for the creation of custom-fit spaces for components within the PCB substrate.
What materials are commonly used in RF Cavity PCBs?
Common materials include high-frequency laminates such as Rogers RT/duroid, Taconic, Isola, PTFE, and ceramic-filled hydrocarbon materials, all chosen for their excellent electrical properties and thermal stability.
In which industries are RF Cavity PCBs most commonly used?
RF Cavity PCBs are commonly used in telecommunications, aerospace and defense, medical devices, automotive electronics, and high-frequency consumer electronics.
How do RF Cavity PCBs improve thermal management?
RF Cavity PCBs improve thermal management by incorporating thermal vias, heat sinks, and metal-backed substrates, which help to dissipate heat generated by high-power components effectively.