Radio Frequency Cavity PCB Manufacturer.A Radio Frequency Cavity PCB Manufacturer specializes in crafting printed circuit boards (PCBs) tailored for radio frequency applications. These intricately designed boards are meticulously engineered to ensure optimal performance and reliability in RF systems. Utilizing advanced manufacturing techniques, they create PCBs featuring specialized cavities and layouts to minimize interference and maximize signal integrity. Their expertise lies in producing high-quality boards that meet stringent RF requirements, catering to industries such as telecommunications, aerospace, and wireless technology. With a focus on precision and innovation, they are the go-to choice for cutting-edge RF PCB solutions.
In today’s rapidly developing electronic technology field, RF cavity PCB manufacturers play an indispensable role. As a core component that supports and connects electronic components, RF cavity PCB plays a vital role in wireless communications, radar systems, satellite technology and other fields. This article will delve into the criticality of RF cavity PCB and its wide application in various electronic devices.
What is Radio Frequency Cavity PCB?
Radio Frequency Cavity PCB (Radio Frequency Cavity PCB) is a printed circuit board (PCB) specially designed to process radio frequency signals. It is a highly specialized PCB type designed to optimize the transmission and processing of radio frequency signals and is commonly used in communications, radar, satellite and wireless networks.
The uniqueness of RF cavity PCB lies in its design structure. Compared with ordinary double-layer or multi-layer PCB, RF cavity PCB has a cavity or cavity structure in which RF signals can propagate freely without interference. This design effectively reduces signal crosstalk and loss, improving system performance and stability.
In RF cavity PCB, special dielectric materials and metal layers are usually used to achieve precise control of RF signals. High-frequency fiberglass and low-loss dielectric materials are widely used to reduce signal transmission losses, while copper foil layers are precisely designed to provide the required impedance matching and signal distribution.
The size and shape of the RF cavity PCB can also be customized according to specific application needs. From micro packages to large boards, RF cavity PCB can be customized in various sizes and shapes to meet the RF signal processing needs in different scenarios.
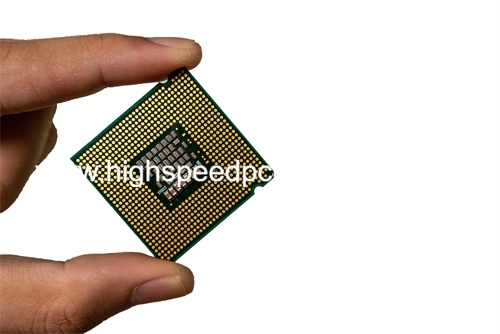
Radio Frequency Cavity PCB Manufacturer
In short, RF cavity PCB is a type of PCB specially designed to process high-frequency RF signals. Its optimized design structure and precise manufacturing process make it an ideal choice for various high-frequency electronic equipment.
Radio Frequency Cavity PCB design Reference Guide.
RF cavity PCB design is a delicate and complex task that requires consideration of many factors to ensure optimal performance and reliability. The following is a brief RF cavity PCB design reference guide to help you better understand and practice the RF cavity PCB design process:
Understanding RF characteristics
Before designing RF cavity PCB, you must first fully understand the RF characteristics. This includes a deep understanding of high-frequency signal transmission, impedance matching, signal coupling, and signal loss. Only by in-depth understanding of RF characteristics can we design an RF cavity PCB with excellent performance.
PCB layer stacking design
The layer stack design of RF cavity PCB is crucial. Proper layer stacking can reduce losses and interference in signal transmission and improve overall performance. Usually, RF cavity PCB will adopt a multi-layer structure, including ground layer, signal layer and power layer, etc., to achieve the best signal transmission and isolation effect.
Cabling and routing rules
In RF cavity PCB design, routing and routing rules are crucial. Good wiring and trace design can minimize signal loss and interference, and improve signal stability and reliability. During the design process, pay attention to avoid sharp corners and excessively long traces, and arrange signal leads and ground wires reasonably.
Impedance matching and signal coupling
In RF cavity PCB design, impedance matching and signal coupling are very important considerations. Reasonable impedance matching can ensure smooth transmission and matching of signals, while effective signal coupling can minimize interference and cross-coupling between signals.
RF cavity structure design
The structural design of RF cavity PCB needs to be customized according to specific application requirements. This includes aspects such as the shape, size and material selection of the RF cavity. Reasonable radio frequency cavity structure design can ensure good radio frequency characteristics and stability.
Simulation and verification
Before proceeding with RF cavity PCB design, simulation and verification are recommended. By simulating signal transmission and performance through simulation software, potential problems can be discovered early and optimized. At the same time, the reliability and performance of the design can also be verified through actual testing and verification.
RF cavity PCB design is a comprehensive engineering task that requires designers to have solid RF technical knowledge and rich practical experience. We hope this design reference guide can provide you with help and guidance in the RF cavity PCB design process.
What material is used in Radio Frequency Cavity PCB?
Material selection for RF cavity PCB is critical to its performance. When designing and manufacturing RF cavity PCB, using appropriate materials can ensure that it has excellent electrical performance and stability to meet the requirements of high-frequency signal transmission.
First of all, high-frequency glass fiber is one of the commonly used substrate materials in RF cavity PCB. This material has good dielectric properties and mechanical strength, can effectively support circuit components and resist the loss of high-frequency signals. High-frequency fiberglass substrates generally have low dielectric losses and good thermal stability, making them one of the ideal choices for RF circuits.
Secondly, copper foil is a commonly used conductive layer material in RF cavity PCB. Copper foil has excellent electrical conductivity and good weldability, and can effectively transmit high-frequency signals and reduce signal transmission losses. In RF cavity PCB, copper foil is usually used to form the wires, ground layer and signal layer of the circuit to ensure the stability and reliability of the circuit.
In addition, special dielectric materials are also an integral part of RF cavity PCB. These dielectric materials have low dielectric constant and low dielectric loss, which can effectively reduce the transmission loss and signal attenuation of high-frequency signals. Dielectric materials in RF cavity PCB are usually used to form the insulating and dielectric layers of the circuit to ensure the stability and performance of the circuit.
To sum up, the material selection of RF cavity PCB is crucial. By using high-frequency glass fiber, copper foil and special dielectric materials, the RF cavity PCB can be ensured to have excellent electrical performance and stability, thereby meeting the requirements for high-frequency signal transmission, and is widely used in communications, radar, satellites and Wireless networks and other fields.
What size are Radio Frequency Cavity PCB?
The dimensions of RF cavity PCBs are customized according to specific application requirements, which makes them widely used in various scenarios. From micro packages to large boards, RF cavity PCBs can be customized in various sizes and shapes to meet the needs of different electronic devices.
For micro RF cavity PCBs, they are usually designed into very small packages to meet the needs of small electronic devices such as mobile phones, smart watches, and headphones. These micro PCBs may only be a few millimeters in size, but are capable of hosting complex circuits and RF components.
For large boards, RF cavity PCBs can be designed to larger sizes to accommodate applications that require more connection points and more complex wiring, such as communication base stations, radar systems, and satellite communication equipment. These large PCBs may require dozens or even hundreds of square centimeters in size while maintaining stable transmission of high-frequency signals and good RF performance.
In addition, the shape of the RF cavity PCB can also be customized according to specific design requirements. Some applications may require a plate-shaped PCB, while others may require a round, oval, or other non-traditional shape PCB. This flexibility allows RF cavity PCB to meet the needs of various application scenarios.
In general, the size and shape of RF cavity PCB can be customized according to the requirements of specific applications. From micro to large, from traditional shapes to non-traditional shapes, customized designs can be achieved to meet the high frequency requirements of modern electronic equipment. signal processing requirements.
The Manufacturer Process of Radio Frequency Cavity PCB.
RF cavity PCB, as a type of PCB specially designed to process RF signals, needs to go through a series of precise steps during its manufacturing process to ensure the quality and performance of the final product.
Design
The first step in manufacturing an RF cavity PCB is the design. The design team uses professional PCB design software to create circuit board layout and electrical connections based on customer requirements and technical specifications. During the design process, layout optimization, layer stacking, impedance matching, and RF signal transmission characteristics need to be considered.
Prototyping
Once the design is complete, the manufacturing team will then prototype the PCB. Designs can be verified and optimized by converting them into actual physical prototypes. Rapid prototyping technology, such as CNC machining or 3D printing, is usually used to produce PCB samples.
Chemical corrosion
After the prototype verification is passed, formal PCB manufacturing begins. The first is the chemical etching step, which is to put the copper foil-covered substrate into an etching solution, and remove the unnecessary copper foil through a chemical reaction, leaving the desired circuit pattern. This step is related to the accuracy and reliability of the circuit board, so the corrosion time and temperature need to be strictly controlled.
Drilling
After chemical etching is completed, drilling is next. With a high-precision CNC drilling machine, holes are drilled on the PCB for mounting components and connecting circuits between different layers. The accuracy of drilling directly affects the final quality of the circuit board, so it is necessary to use high-quality drilling tools and strictly control the drilling position and size.
Assemble
The final step is assembly, mounting the electronic components onto the PCB and making solder connections. This process requires a high degree of skill and precision to ensure that components are installed correctly and good electrical connections are made. After assembly is completed, necessary testing and quality checks are performed to ensure that the PCB meets specifications and customer requirements.
Through the above precision manufacturing process, RF cavity PCB manufacturers can produce high-quality, stable-performance electronic products to meet the needs of different industries and provide strong support for the development of modern wireless communication technology.
The Application area of Radio Frequency Cavity PCB.
RF cavity PCB has a wide range of applications in fields such as communications, radar, satellites and wireless networks. Its excellent radio frequency characteristics and stability make it the first choice for various high-frequency electronic equipment.
In the field of communication, RF cavity PCB is widely used in wireless base stations, antenna systems and communication equipment. These devices need to process high-frequency signals and ensure signal transmission stability and reliability, and the design of RF cavity PCB can effectively meet these needs.
Radar systems are also one of the main application areas of RF cavity PCB. Radar systems need to process high-frequency signals and perform accurate detection and tracking, and RF cavity PCB can provide highly controllable signal transmission and reception performance, thereby achieving efficient operation of the radar system.
Satellite communications are another important application area for RF cavity PCBs. Satellite communication systems need to handle a large number of high-frequency signals and maintain stable signal transmission under different weather conditions. The excellent performance of RF cavity PCB can ensure that satellite communication systems can work reliably in various environments.
In addition, in wireless network equipment, RF cavity PCB also plays an important role. Wireless routers, base stations and other wireless devices need to process high-frequency signals and provide stable network connections, and the design of RF cavity PCB can effectively improve the performance and stability of the equipment and meet users’ needs for high-speed and stable networks.
In general, the wide application of RF cavity PCB in the fields of communications, radar, satellites and wireless networks fully demonstrates its importance and superior performance in high-frequency electronic equipment. With the continuous development and innovation of technology, RF cavity PCB will continue to play a key role in promoting the progress and development of high-frequency electronic technology.
What are the advantages of Radio Frequency Cavity PCB?
Radio Frequency Cavity PCB (Radio Frequency Cavity PCB) plays a vital role in the manufacturing of modern electronic equipment and has many advantages over traditional wiring methods. The following are the main advantages of RF cavity PCB:
Small size
RF cavity PCB allows for a more compact design and efficient use of space. Its high integration level and compact structure make it possible to realize the layout of complex circuits in a limited space, and is especially suitable for electronic equipment that requires miniaturization.
Stable performance
RF cavity PCB uses specialized design and materials to provide stable RF characteristics. Its precise impedance matching, low loss and high-quality signal transmission ensure the stability and reliability of the circuit in high-frequency environments.
Easy to mass produce
The manufacturing process of RF cavity PCB is relatively simple and can be highly automated. Through modern production equipment and process control, efficient large-scale production can be achieved, production costs can be reduced and product quality consistency can be ensured.
Flexible design
The design of RF cavity PCB has high flexibility. Design engineers can customize designs based on specific application requirements, including layer stacking, routing, impedance matching and antenna design. This flexibility allows RF cavity PCB to meet the needs of different application scenarios and respond quickly to market changes.
In short, RF cavity PCB has become an indispensable key component in the manufacturing of modern electronic equipment due to its advantages such as small size, stable performance, easy mass production, and flexible design. It not only promotes the development of electronic technology, but also provides reliable solutions for various high-frequency applications.
FAQ
What is the difference between RF cavity PCB and ordinary PCB?
RF cavity PCB is a special type of PCB designed to handle RF signals. Compared with ordinary PCBs, RF cavity PCBs are different in material selection, wiring design and packaging to ensure better RF performance and signal stability.
What are the materials of RF cavity PCB?
Commonly used materials for RF cavity PCB include high-frequency glass fiber, polytetrafluoroethylene (PTFE), copper foil, etc. These materials have excellent electrical and radio frequency properties and can meet the requirements of high-frequency signal transmission.
Is the manufacturing cost of RF cavity PCB high?
The manufacturing cost of RF cavity PCB is usually slightly higher than that of ordinary PCB, mainly because the materials and processes used are more stringent, and special equipment and technology are required to ensure RF performance and signal stability.
What is the application scope of RF cavity PCB?
RF cavity PCB is widely used in communications, radar, satellites, wireless networks and other fields. Especially in equipment that needs to process high-frequency signals and microwave signals, its performance advantages are fully utilized.