Radar HF Substrate Manufacturer.The Radar HF Substrate Manufacturer specializes in crafting advanced materials tailored for high-frequency radar applications. With precision engineering and cutting-edge technology, they produce substrates optimized to enhance radar performance across a range of frequencies. Their expertise lies in creating substrates that exhibit exceptional electrical properties, ensuring minimal signal loss and maximum sensitivity. These substrates are integral components in radar systems used for various purposes, including military surveillance, weather monitoring, and aviation navigation. Committed to innovation and quality, the manufacturer plays a pivotal role in advancing radar technology for diverse industries.
In modern electronic equipment, Radar HF substrate is a crucial component, which carries various electronic components and provides connections so that the electronic equipment can work properly. As a Radar HF substrate Manufacturer, you understand the importance of Radar HF substrate in electronic systems. In this article, we will delve into the definition, design, manufacturing process of Radar HF substrate, as well as the costs, materials, and manufacturers related to Radar HF substrate.
What is Radar HF substrate?
Radar HF substrates, namely radar high-frequency substrates, are substrate materials specifically used for high-frequency applications in radar systems. They are designed to provide excellent electrical performance and high-frequency transmission capabilities in the HF band, typically between hundreds of megahertz to several gigahertz. As a Radar HF substrate Manufacturer, it is crucial to understand the importance of radar HF substrate.
In radar systems, the transmission of high-frequency signals is crucial. Radar systems need to be able to accurately transmit and receive high-frequency signals to achieve target detection and tracking. As one of the core components of the radar system, PCB‘s performance in high-frequency transmission directly affects the performance and stability of the radar system.
Radar HF substrates are usually made of special materials, such as PTFE (polytetrafluoroethylene) substrates. PTFE has low loss and stable dielectric properties, and can provide excellent signal transmission characteristics in the HF band. In addition, the radar HF substrate may also adopt special structural designs, such as microstrip lines and cavity structures, to further optimize the transmission effect of high-frequency signals.
As Radar HF substrate Manufacturer, we understand the strict requirements of radar systems for HF substrates. We are committed to providing high-performance, reliable HF substrate materials to meet the radar system’s high-frequency transmission and signal integrity requirements. Our HF substrate not only has excellent electrical properties, but also has good high temperature resistance and corrosion resistance, making it suitable for application scenarios in various harsh environments.
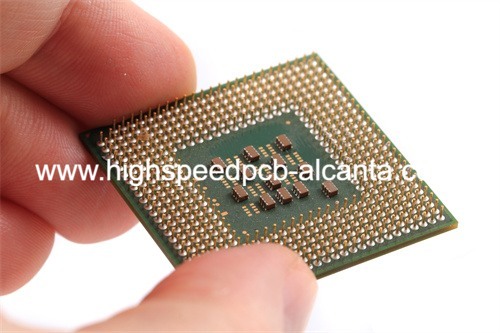
Radar HF Substrate Manufacturer
In short, radar HF substrates play a vital role in the radar system. They provide the radar system with stable and reliable high-frequency transmission capabilities and are a key component to ensure the performance and stability of the radar system. As a Radar HF substrate Manufacturer, we will continue to work hard to provide high-quality HF substrate materials to meet customer needs and expectations for radar systems.
How to Design a Radar HF substrate?
In radar systems, the HF radar substrate carries various radio frequency (RF) components and antennas and is responsible for transmitting signals to other components of the system. These substrates not only need to provide stable electrical performance, but also need to have excellent high-frequency transmission capabilities to ensure accurate transmission and reception of signals. As a Radar HF substrate Manufacturer, your products provide critical basic support for the HF radar system, ensuring the performance and reliability of the radar system.
When designing a radar HF substrate, there are several key factors to consider:
Select the appropriate substrate material: The radar HF substrate needs to choose a material with excellent high-frequency characteristics, such as PTFE (polytetrafluoroethylene) substrate. These materials have low dielectric loss, stable dielectric constant and low transmission loss, and can meet the high-frequency transmission performance requirements of HF radar systems.
Optimize layout and layer stacking: When designing HF radar substrates, the layout and layer stacking need to be optimized to minimize signal crosstalk and impedance mismatch. Reasonable layout and layer stacking can ensure accurate transmission of signals and improve the system’s anti-interference ability.
Consider the ground plane and power plane: The ground plane and power plane play an important role in the radar HF substrate. They not only provide good ground and power distribution, but also reduce electromagnetic interference and noise. During the design process, the location and layout of the ground plane and power plane need to be properly planned to ensure the stability and reliability of the system.
Optimize impedance matching: In HF radar systems, impedance matching is critical to the quality and efficiency of signal transmission. Therefore, when designing an HF radar substrate, impedance matching needs to be optimized through appropriate line width and spacing design to ensure accurate transmission and reception of signals.
Consider thermal management and EMC: In radar systems, thermal management and electromagnetic compatibility (EMC) are critical factors. Therefore, when designing the HF radar substrate, heat dissipation and heat dissipation, as well as electromagnetic interference control, need to be taken into consideration to ensure the stability and reliability of the system.
Through the consideration and optimization of the above key factors, the designed radar HF substrate will be able to meet the strict requirements of high-frequency transmission and signal integrity of the HF radar system, providing reliable basic support for the performance and reliability of the radar system.
What is the Radar HF substrate Fabrication Process?
The manufacturing process of radar HF substrates is complex and precise, involving multiple steps and processes. As a Radar HF substrate Manufacturer, understanding these steps is critical to ensuring product quality.
The first step in manufacturing radar HF substrate is to prepare the materials. Commonly used substrate materials include PTFE (polytetrafluoroethylene), RO4003C, etc. These materials have excellent dielectric properties and high-frequency characteristics and are suitable for HF radar systems.
Once the material is ready, the next step is to cut the sheet to the desired size. Accurate board size is very important to ensure the size and geometry of the PCB, especially in HF systems, which has a direct impact on signal integrity and impedance control.
Before graphic processing, the CAD file of the PCB needs to be designed and prepared. These CAD files contain PCB layout, connections, wiring and other information. Through graphics imaging processing, CAD files can be converted into actual patterns and layouts on PCB.
Photolithography is one of the key steps in manufacturing radar HF substrates. In this step, the desired lines and patterns are formed by covering the substrate with photoresist and exposing it using UV light. Photoresist selection and processing are critical to PCB accuracy and quality.
Acid etching is a process in which copper materials not covered by photoresist are etched away using a chemical solution to form lines and patterns. During the acid etching process, the concentration, temperature and etching time of the solution need to be strictly controlled to ensure the quality and accuracy of the PCB.
In the final stage of PCB manufacturing, drilling and socket processing are required. These holes are used to install electronic components and connectors, so the location, size and quality of the holes need to be consistent with the design requirements.
Finally, the PCB undergoes surface treatment to enhance its corrosion resistance and soldering performance. Common surface treatment methods include spray plating, gold plating, etc. These treatment methods can improve the reliability and durability of PCB.
By strictly controlling each manufacturing step and ensuring the stability and consistency of process parameters, Radar HF substrate Manufacturer can produce high-quality radar HF substrates that meet the performance and reliability requirements of HF radar systems.
How to Manufacturer a Radar HF substrate?
In modern radar systems, HF (high frequency) substrates play a vital role, providing stable electrical performance and high-frequency transmission capabilities for the system. As a radar HF substrate manufacturer, it is crucial to understand how to manufacture high-quality substrates. The steps and key considerations for manufacturing radar HF substrates are described below.
The performance of HF substrates directly depends on the materials selected. Common HF substrate materials include PTFE (polytetrafluoroethylene), RO4003C, etc., which have lower dielectric loss and higher dielectric constant and are suitable for high-frequency applications. When selecting a material, factors such as its dielectric properties, thermal stability, and manufacturing cost need to be considered.
The design of HF substrate needs to fully consider factors such as matching, impedance control and signal integrity of high-frequency transmission lines. By optimizing PCB layout and wiring methods, signal loss and crosstalk effects can be minimized, and system performance and stability can be improved.
Manufacturing HF substrates requires the use of advanced manufacturing processes and equipment. Common manufacturing processes include chemical etching, gold plating, lamination, etc., among which chemical etching is one of the most critical steps in manufacturing HF substrates. Chemical etching can precisely control the width and spacing of PCB traces to ensure impedance matching and signal integrity of the HF substrate.
Quality control is a crucial part of the manufacturing process of HF substrates. Material and process parameters need to be strictly controlled in each manufacturing step to ensure the stability and reliability of the substrate. At the same time, strict inspection and testing are also required to ensure that the substrate meets the customer’s technical requirements and standards.
Good customer service is an integral part of the process of manufacturing HF substrates. Establishing good communication and cooperative relationships with customers, responding to customer needs and feedback in a timely manner, and providing professional technical support and solutions will help build brand reputation and competitive advantage.
Manufacturing radar HF substrates is a complex and precise task that requires adequate materials, design, process and quality control. As a radar HF substrate manufacturer, we are committed to providing customers with high-performance, high-quality substrate products to meet their performance and reliability requirements.
How Much Does a Radar HF substrate Cost?
The cost of radar HF substrates depends on several factors, including selected materials, plate type, size and quantity, etc. Generally speaking, the cost of radar HF substrate is relatively high, mainly because it requires the use of high-performance materials and requires more stringent process control during the manufacturing process.
First of all, radar HF substrates usually use special materials required for high-frequency applications, such as PTFE (polytetrafluoroethylene) substrates. PTFE substrate has excellent high-frequency transmission performance and stable dielectric properties, but the cost is relatively high. In addition, radar HF substrates may require special metallization to ensure good conductivity and impedance control, further increasing costs.
Secondly, radar HF substrates usually require multi-layer structures to meet complex circuit layout and high-frequency transmission requirements. The multi-layer structure means that the manufacturing process is more complex and requires more processes and consumables, so the cost will increase accordingly.
In addition, the size and quantity of radar HF substrates will also affect its cost. Generally speaking, large-size and low-volume substrates cost more because they require more materials and more manufacturing steps.
Taking the above factors into consideration, under normal circumstances, the cost of radar HF substrate will be much higher than that of ordinary PCB. The specific cost can be customized according to the customer’s needs and requirements, so it is recommended to conduct detailed communication and negotiation with the radar HF substrate manufacturer to obtain an accurate quotation and customized solution.
What materials are Radar HF substrate made of?
Radar high frequency (HF) substrates play a vital role in radar systems as they need to maintain stable signal transmission and electrical performance in high frequency environments. In order to meet these requirements, radar HF substrates usually use some special materials. The following are some common radar HF substrate materials:
PTFE (polytetrafluoroethylene) substrate: PTFE is a polymer material with excellent dielectric properties. Its characteristics include low dielectric constant, low loss and high temperature stability. This makes the PTFE substrate ideal for radar HF applications as it provides stable high frequency performance and excellent signal transmission capabilities.
RO4003C: RO4003C is a special PTFE glass fiber composite material with high dielectric constant and dielectric loss, suitable for microstrip line and antenna design in high-frequency radar systems. RO4003C substrate has excellent mechanical properties and thermal stability, which can meet the high-frequency signal transmission and stability requirements of complex radar systems.
RO4350B: RO4350B is a high-performance PTFE ceramic composite material with a low dielectric constant and loss factor that performs well in high-frequency environments. RO4350B substrate is widely used in radar antenna, microstrip line and radio frequency module design, which can achieve fast transmission and stability of high-frequency signals.
RF-35: RF-35 is a high-performance polyurethane substrate material with excellent dielectric properties and thermal stability, suitable for radio frequency antenna and microstrip line design in HF radar systems. The RF-35 substrate has good mechanical strength and environmental resistance, and can meet the high-frequency signal transmission and reliability requirements of complex radar systems.
To sum up, radar HF substrates are usually made of PTFE and its composite materials to meet stability and performance requirements in high-frequency environments. These materials have excellent dielectric properties, thermal stability and mechanical strength and are critical components in radar systems.
Who manufactures Radar HF substrate?
The fabrication of radar HF substrates is critical to the performance of HF radar systems. As a leading Radar HF substrate Manufacturer, we are committed to providing high-performance radar HF substrates to meet customers’ needs for signal transmission, impedance control and stability in HF radar systems.
Our manufacturing process uses advanced technology and strict quality control standards to ensure that each radar HF substrate has excellent electrical performance and reliability. Our supplier is our company. We have advanced production equipment and technical team, which can flexibly respond to customer needs and provide customized solutions.
As a Radar HF substrate Manufacturer, our products are widely used in various HF radar systems, including military radar, aviation radar, weather radar and other fields. We work closely with customers to understand their needs and conduct customized designs based on actual application scenarios to ensure the best performance and stability of the product.
Our radar HF substrate uses high-quality substrate materials, such as PTFE, RO4003C, etc., which has excellent high-frequency transmission performance and stable electrical characteristics. Our manufacturing processes are strictly controlled in accordance with international standards to ensure stable and reliable product quality.
At Radar HF substrate Manufacturer, we not only focus on product quality, but also on customer experience. We provide a full range of customer services, including technical support, sample testing and after-sales service, to meet our customers’ needs and solve their challenges in HF radar systems.
Through continuous technological innovation and service optimization, we are committed to becoming a radar HF substrate supplier trusted by customers, providing them with high-quality products and professional services, and jointly promoting the development and application of HF radar technology.
What are 5 qualities of a good customer service?
In the field of Radar HF substrate Manufacturer, providing excellent customer service is crucial. Excellent customer service not only enhances customers’ trust in the company, but also promotes the establishment of long-term cooperative relationships. Here are five hallmarks of great customer service:
Excellent customer service starts with prompt response and effective communication. Whether customers raise questions, needs or feedback, companies should respond quickly, maintain active communication, and provide timely solutions and feedback. Through timely response and communication, companies can establish good interactions with customers and enhance customer satisfaction and trust in the company.
Excellent customer service should be personalized, that is, provide customized solutions and services based on the customer’s needs and characteristics. Understanding customer needs and preferences and tailoring products and services to their needs can effectively increase customer satisfaction and loyalty. Through personalized services, companies can better meet customer needs and establish long-term and stable cooperative relationships.
As a Radar HF substrate Manufacturer, providing professional technical support is very important to customers. Customers may encounter various technical problems when using products, so companies should provide professional technical support teams to solve customers’ technical problems in a timely manner and provide customers with professional consultation and suggestions. By providing professional technical support, companies can increase customers’ trust and satisfaction with products, thereby promoting customers’ repurchase and long-term cooperation.
Excellent customer service not only includes product quality assurance, but also should provide complete after-sales service. Enterprises should ensure that the quality of products meets customer expectations and standards, while providing timely after-sales services to solve customers’ problems and troubles during the use of products. By providing quality assurance and comprehensive after-sales service, companies can enhance customers’ trust and satisfaction with products and establish long-term and stable cooperative relationships.
Excellent customer service is a process of continuous improvement and improvement. Enterprises should constantly collect customer feedback and suggestions, and timely adjust and improve products and services to meet customer needs and expectations. At the same time, enterprises should pay attention to the development trends of the industry and the changing needs of customers, and constantly innovate and optimize products and services to maintain competitive advantages and customer satisfaction.
Through the above five characteristics, Radar HF substrate Manufacturer can provide high-quality customer service, meet customer needs and expectations, establish long-term and stable cooperative relationships, and achieve a win-win situation.
FAQS
What are the special requirements for PCB for HF radar systems?
HF radar systems usually require PCBs with high signal integrity and impedance control capabilities. This is because the signal transmission speed in the HF band is fast and the wavelength is short, which requires the design of wires and transmission lines on the PCB to maintain stable impedance matching to prevent signal attenuation and distortion. In addition, HF radar systems also require PCBs with lower signal loss and cross-harmonic interference to ensure system performance and sensitivity.
How to choose PCB materials suitable for HF radar systems?
In order to meet the special requirements of HF radar systems, materials with low dielectric constant and low loss tangent are usually selected, such as PTFE (polytetrafluoroethylene), RO4003C, etc. These materials have excellent high-frequency performance and can maintain stable signal transmission and impedance matching in the HF band, thereby improving system performance and reliability.
What are the common quality control measures during PCB manufacturing?
Quality control measures in the PCB manufacturing process include raw material inspection, process control, finished product testing and other links. Among them, raw material inspection mainly checks the quality and specifications of substrate materials; process control includes plate thickness control, line width and line spacing control, surface treatment, etc. to ensure that the quality of each process meets the requirements; finished product inspection includes appearance inspection, electrical Performance testing, etc. to ensure the quality and reliability of the final product.
How to optimize PCB design to reduce signal loss in HF radar systems?
In order to reduce the signal loss of the HF radar system, the following measures can be taken: use low-loss tangent materials to reduce the energy loss during signal transmission; use appropriate line width and line spacing design to reduce the resistance and inductance of the transmission line; reasonably Lay out and shield sensitive signal lines to reduce electromagnetic interference and crosstalk.
What are the common technical difficulties in the PCB manufacturing process?
Common technical difficulties in the PCB manufacturing process include: high-end board lamination technology, fine line width and line spacing processing, blind buried holes and blind hole drilling technology, surface treatment technology, etc. These difficulties require manufacturers to have extensive experience and advanced processing equipment to ensure the quality and reliability of PCBs.