Radar/Antenna Substrate Manufacturer.A premier manufacturer specializing in radar/antenna substrates, we lead the industry with cutting-edge technology and unparalleled expertise. Our substrates, meticulously engineered using advanced materials and precision processes, ensure optimal performance and reliability in radar and antenna systems. With a commitment to innovation and quality, we cater to diverse applications, from aerospace and defense to telecommunications and beyond. Our relentless pursuit of excellence drives us to continually push the boundaries of substrate technology, delivering solutions that empower our clients to thrive in an increasingly connected world.
Radar and antenna technology play an integral role in modern communications and wireless. Whether used in military applications, aerospace or civilian communications, they require high-performance, reliable substrate materials to support their functionality. The choice of substrate material directly affects the performance and lifespan of radar and antenna systems, so it is crucial for engineers to select appropriate materials. In this article, we will delve into the importance of radar and antenna substrates and the key information associated with them.
What is Radar/Antenna substrate?
Radar and antenna substrates are indispensable and critical components in modern communications and wireless technologies. They carry the functions of radar systems and antennas, providing these systems with the necessary support, conductivity and isolation to ensure they can work effectively.
In radar and antenna systems, substrate selection is critical. Radar/antenna substrates are not only carriers that provide support, their physical and electrical properties directly affect the performance and stability of the system. These substrates are usually made of specific materials, such as PTFE (polytetrafluoroethylene), FR-4 (fiberglass reinforced epoxy), etc., which have excellent conductivity and insulation properties to adapt to different frequency and power requirements.
In radar and antenna systems, the substrate serves to connect and isolate circuits. They carry various electronic components such as antenna arrays, amplifiers, filters, etc. while ensuring the electrical connections between these components. In addition, the substrate provides isolation to prevent signal interference and electromagnetic interference from occurring, thereby ensuring system stability and performance.
Radar/antenna substrate design requires consideration of many factors, including frequency range, power requirements, thermal management, and manufacturing costs. Designers must meet performance requirements while minimizing size and weight to accommodate the needs of different application scenarios.
In summary, radar and antenna substrates are indispensable and critical components in modern communications and wireless technologies. They provide a stable and reliable working environment for radar systems and antennas by providing support, conductivity and isolation, promoting the continuous development and advancement of communication technology.
Radar/Antenna substrate design Reference Guide.
The design of radar and antenna substrates is a complex and critical process, which directly affects the performance and reliability of radar systems and antennas. Designers need to consider a variety of factors to ensure the final product meets the requirements of a specific application. Here are some key factors to consider when designing radar and antenna substrates, along with corresponding best practices and guidelines:
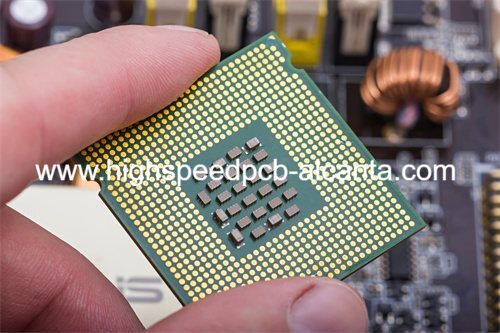
Radar/Antenna Substrate Manufacturer
Frequency Range
Radar and antenna systems often operate within a specific frequency range, so the design must ensure that the substrate materials and layout can support the required frequency range. Choosing the appropriate dielectric constant and loss factor is key to ensuring frequency stability.
Signal loss
Signal loss is one of the issues that needs to be paid attention to during the design process. Reasonable layout and selection of low-loss materials can reduce signal loss and improve system sensitivity and performance.
Thermal management
High-power radar systems and antennas can generate large amounts of heat, so effective thermal management measures must be considered in the design to ensure stable system operation and prevent overheating damage. Leave enough room for heat dissipation in your layout design, and consider using heat sinks or heat pipes to disperse heat.
Manufacturing feasibility
It is important to consider the feasibility of the manufacturing process during the design phase. Select commonly used substrate materials and processes to ensure the design is physically manufacturable and cost-controllable. At the same time, reasonable design layout and process specifications can reduce problems and defects during the manufacturing process.
Layout and connections
Properly designed layout and connection schemes are key to ensuring stable system performance. Reasonably separate analog and digital signal paths, reduce crosstalk and interference, and optimize signal transmission paths to improve the system’s anti-interference capability and sensitivity.
Encapsulation and protection
Select appropriate packaging and protective materials to protect the substrate and critical components from environmental factors and mechanical damage. Taking into account the usage environment and working conditions of the system, select appropriate dust-proof, waterproof and anti-corrosion measures.
Test and verify
Once the design is complete, thorough testing and verification are important steps to ensure system performance and reliability. Use advanced testing equipment and methods to verify that the system meets design specifications and make necessary corrections and optimizations.
By considering the above factors and following best practices and guidelines, designers can develop radar and antenna substrates with excellent performance, stability and reliability to meet the needs of various applications.
What material is used in Radar/Antenna substrate?
Material selection for radar and antenna substrates is critical to system performance and reliability. Common radar/antenna substrate materials include polytetrafluoroethylene (PTFE), glass fiber reinforced epoxy resin (FR-4), and PTFE glass fiber, etc.
Polytetrafluoroethylene (PTFE) is an excellent radar/antenna substrate material with excellent high temperature resistance, chemical resistance and dielectric properties. Due to its low dielectric constant and dielectric loss, PTFE is widely used in high frequency and microwave applications and can provide excellent signal transmission performance. However, the cost of PTFE is relatively high, and performance and cost need to be balanced in the design.
Fiberglass reinforced epoxy (FR-4) is a common substrate material that has good mechanical strength and heat resistance and is suitable for general radar and antenna applications. FR-4 material is relatively cheap and easy to process, making it suitable for mass production, but its dielectric properties are relatively poor, which can cause signal loss and interference.
Another common material is PTFE fiberglass composite, which combines the advantages of PTFE and fiberglass. This material has excellent dielectric properties and mechanical strength, making it suitable for high-frequency and microwave applications. However, PTFE fiberglass materials are more expensive and are typically used in applications with higher performance requirements.
When selecting radar/antenna substrate materials, factors such as frequency range, mechanical requirements, cost, and manufacturing feasibility need to be considered. Appropriate material selection can ensure that the system has good performance and reliability, and can achieve the best results in different application scenarios.
What size are Radar/Antenna substrate?
Radar and antenna substrate dimensions are critical considerations in the design and manufacturing process as they directly impact device performance, power consumption and cost. The size of these substrates often varies based on the needs of the specific application, from tiny antennas to large radar systems, each size has its own unique advantages and application scenarios.
First, miniature antenna substrates are commonly used in small electronic devices and wireless sensor networks. These substrates are typically very small, perhaps only a few millimeters to a few centimeters in size. They are suitable for applications requiring a high degree of integration and space constraints, such as smart watches, smart wearables, and medical monitors. The design of micro-antenna substrates needs to consider the balance of size and performance to ensure good signal transmission and reception in a limited space.
Second, medium to large antenna substrates are commonly used in communications equipment, radar systems, and aerospace applications. The size of these substrates can vary from tens of centimeters to several meters, depending on the power, frequency range and coverage of the device. For example, in radar systems, large substrates can accommodate complex antenna arrays and signal processing circuits to enable long-range target detection and tracking. In communication equipment, medium-sized antenna substrates are commonly used in base stations and communication towers to support wide-area signal coverage and data transmission.
In addition, the size of the antenna substrate is limited by the manufacturing and assembly processes. For example, in large radar systems, the size of the substrate may be limited by factory equipment and transportation conditions, so these factors need to be taken into account during the design stage to ensure smooth manufacturing and assembly.
In summary, radar and antenna substrate size is a complex and critical design parameter that requires comprehensive consideration of device performance, space constraints, and manufacturing requirements. Through careful design and optimization, the best signal transmission effect and system performance can be achieved to meet the needs of various applications.
The Manufacturer Process of Radar/Antenna substrate.
The manufacturing of radar and antenna substrates is a complex and sophisticated process involving multiple critical steps, each of which has a significant impact on the performance and reliability of the final product. Here’s a detailed description of the process:
Design Phase
In the manufacturing process of radar and antenna substrates, the design phase is a crucial step. Engineers design circuit layout and routing based on specific application needs and technical requirements. The key goal at this stage is to ensure that the circuit layout is reasonable, signal paths are shortest, and performance and reliability requirements are met.
Prototyping
Once the design is complete, prototypes are created to verify the correctness and feasibility of the design. Prototyping typically involves using CAD software to generate circuit board layouts and making samples through rapid prototyping techniques such as 3D printing. The key to this stage is to promptly discover and correct errors or deficiencies in the design.
Chemical Etching
Once the prototype is verified, actual production proceeds. In the chemical etching process, the circuit board is covered in a chemical solution, and the unnecessary metal parts are removed by controlling the etching time and temperature to form a circuit pattern. The key to this step is to ensure that the etching process is uniform and precise to ensure the accuracy and stability of the circuit.
Drilling
Drilling is the process of drilling holes on a circuit board so that components can be installed and connected. These holes are usually located at strategic locations on the circuit board, such as connecting pins and component mounting holes. The quality and precision of drilling are crucial for subsequent assembly and connection.
Metalization
In the metallization process, a conductive layer is formed on the metal parts of the circuit board to ensure the connectivity of the circuit by immersing the circuit board in a chemical solution or using metal evaporation technology. The key to this step is to ensure even metal coverage and avoid connection problems caused by breaks or uneven conductive layers.
Assemble
The final stage is to mount the components onto the circuit board and solder and connect them. This includes soldering component pins, connecting circuit board layer connections, etc. The quality of assembly directly affects the performance and reliability of the final product.
In general, the manufacturing process of radar and antenna substrates is a complex and precise process that requires highly professional technology and strict quality control. Each step is critical, and any oversight or error can result in reduced performance or failure of the final product. Therefore, every detail in the manufacturing process needs to be taken seriously and managed.
The Application area of Radar/Antenna substrate.
Radar and antenna substrates are indispensable key components in the field of modern technology. They are used in a wide range of fields, including military, aerospace, communications, automobiles, and consumer electronics. These substrates play a vital role in various fields, providing critical circuit support and signal transmission functions for various applications.
In the military field, radar and antenna substrates are widely used in military communication systems, navigation systems, long-range reconnaissance and surveillance systems, etc. They can provide reliable signal transmission and data processing functions in complex battlefield environments, providing important support for the successful execution of military operations.
In the aerospace field, radar and antenna substrates are used in aircraft communication, navigation and monitoring systems. They are lightweight, high-performance and high-temperature resistant to meet the stringent performance and reliability requirements of the aerospace industry.
In the field of communications, radar and antenna substrates are core components of wireless communication systems, including mobile communications, satellite communications, wireless networks and radar systems. They can achieve high-speed data transmission, stable signal connections and long-distance communications, promoting the continuous development and progress of communication technology.
In the automotive field, radar and antenna substrates are widely used in vehicle radar systems, vehicle communication systems and vehicle entertainment systems. They can realize intelligent interconnection between vehicles and information exchange between vehicles and infrastructure, improving the safety, comfort and intelligence level of cars.
In the field of consumer electronics, radar and antenna substrates are used in various consumer electronics products such as smartphones, tablets, and smart home devices. They can realize wireless connection, data transmission and signal reception between devices, providing users with a more convenient and smarter experience.
In general, radar and antenna substrates have a wide range of applications. They play an important role in various fields and promote the continuous development and progress of modern technology.
What are the advantages of Radar/Antenna substrate?
Radar and antenna substrates offer multiple advantages over other circuit connection methods, making them essential and critical components in many electronic devices. Here is a more detailed explanation of several advantages of radar/antenna substrates:
High frequency performance
Radar and antenna systems often operate in high frequency ranges, so the high frequency performance of the substrate is critical. The design and material selection of the radar/antenna substrate can ensure stable signal transmission and good signal integrity at high frequencies, thereby achieving precise signal processing and data transmission.
Low signal loss
Since radar and antenna systems require high signal sensitivity, signal loss needs to be minimized. The radar/antenna substrate uses high-quality materials and precise manufacturing processes to reduce signal loss during transmission and ensure signal accuracy and stability.
Good thermal stability
Radar and antenna systems often require continuous operation for long periods of time and can generate significant amounts of heat at high powers. Good thermal stability is one of the key factors to ensure reliable operation of the system. The radar/antenna substrate uses materials with good thermal conductivity, and uses design optimization and heat dissipation measures to effectively manage and dissipate heat, thereby maintaining the stability and reliability of the system under various operating conditions.
Design flexibility
The design of radar and antenna systems often requires consideration of a variety of factors, including frequency range, antenna type, system layout, etc. The radar/antenna substrate has design flexibility and can be customized according to specific application requirements to meet the functional and performance requirements of different systems. Through flexible design and manufacturing processes, radar/antenna substrates can implement complex circuit layouts and multi-layer structures, providing more efficient and reliable solutions.
In general, radar/antenna substrates provide a reliable foundation for the design and manufacturing of radar and antenna systems and promote modern communications with their advantages such as high-frequency performance, low signal loss, good thermal stability, and design flexibility. and the development of wireless technology.
FAQ
What is the cost of the radar/antenna substrate?
The cost of a radar/antenna substrate depends on several factors, including materials selected, design complexity, manufacturing process, and market demand. Generally speaking, high-performance materials and complex-designed substrates cost more, while mass production can reduce unit costs.
What are the environmental impacts of radar/antenna substrates?
Radar/antenna substrates are typically manufactured from environmentally friendly materials, but some chemical waste may be generated during manufacturing and processing. However, as technology advances, many manufacturers are taking steps to reduce their environmental impact, such as adopting green manufacturing processes and recyclable materials.
Can radar/antenna substrates be recycled?
Yes, many materials in the radar/antenna substrate, such as metal and plastic, can be recycled. However, the recycling process requires special processing techniques because the substrates often contain metals, chemicals, and insulating materials that need to be separated and processed for effective recycling.
How to troubleshoot radar/antenna substrate failures?
Radar/antenna substrate failures can be caused by a variety of factors, including design errors, material damage, welding issues, etc. Resolving a fault often requires a careful testing and diagnostic process, which may involve the use of specialized equipment and techniques, to determine the root cause of the problem and implement appropriate fixes.