Package Substrate Manufacturer.The Package Substrate Manufacturer is a pivotal player in the semiconductor industry, specializing in crafting substrates crucial for electronic packaging. With precision engineering and cutting-edge technology, they fabricate substrates tailored to specific chip requirements, ensuring optimal performance and reliability. Their expertise lies in designing substrates that facilitate efficient heat dissipation, signal transmission, and electrical connectivity within semiconductor packages. Renowned for their quality assurance and innovative solutions, they are indispensable partners to chip manufacturers worldwide, enabling the seamless integration of chips into various electronic devices, from smartphones to advanced computing systems.
Package Substrate is an innovative electronic packaging substrate in the field of electronic engineering. It is unique in that it cleverly combines rigid and flexible materials to provide excellent flexibility and performance advantages for electronic product design.
First, the innovation of Package Substrate lies in its multi-layer design, which cleverly combines rigid and flexible materials. Rigid materials give the substrate strong support and structural stability, while flexible materials give it superior bending and adaptability. The uniqueness of this structure allows Package Substrate to better adapt to design needs of limited space and irregular shapes.
Secondly, Package Substrate’s flexibility and performance advantages make it stand out in multiple application fields. Especially in fields such as smartphones, medical equipment, and aerospace systems, its flexible design can easily adapt to different electronic component arrangement and connection needs. In these applications, Package Substrate’s high flexibility, excellent space utilization, and lightweight characteristics have become the ideal choice pursued by design engineers.
In smartphone manufacturing, the use of Package Substrate allows circuit boards to better fit into the compact space of the device while reducing the overall weight. In terms of medical equipment, the flexibility and reliability of Package Substrate allow the equipment to better adapt to different human body shapes and movement conditions. In aerospace systems, its lightweight characteristics provide aircraft with higher performance and fuel efficiency.
Overall, the emergence of Package Substrate has brought new possibilities to electronic product design. It is not only an electronic packaging substrate, but also a tool to promote innovation, providing design engineers with greater flexibility when facing complex design requirements. In the future, with the continuous development of technology, I believe that Package Substrate will show its strong application potential in more fields.
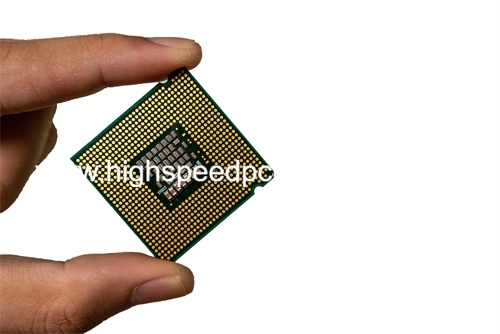
Package Substrate
What are the types of Package Substrates?
In contemporary electronic design, the adaptability of package substrates renders them highly suitable for a myriad of application requirements. This versatility is prominently manifested in distinct categories of package substrates, namely rigid-rigid (Rigid-Rigid), rigid-flexible (Rigid-Flex), and flexible-flexible (Flex-Flex). Each category boasts distinctive characteristics, catering to diverse electronic product design needs.
First, Rigid-Rigid Package Substrate is composed of multiple layers of hard, inflexible substrates. This type of Package Substrate is structurally stronger and is suitable for scenarios that require higher board stability and mechanical strength. Because of its rigid nature, it is commonly found in traditional electronic equipment such as computer motherboards and server systems. Its structure provides strong support and is suitable for accommodating large components and connectors.
Secondly, Rigid-Flex Package Substrate is a design that combines rigid and flexible substrates. This combination allows the board to better adapt to complex shapes in three-dimensional space where it needs to bend. This makes Rigid-Flex Package Substrate widely used in areas requiring high integration and limited space, such as smartphones, camera modules, etc. Its flexibility and foldability bring significant advantages in miniaturization and lightweight.
Finally, the Flex-Flex Package Substrate is entirely composed of flexible substrates and can be bent freely, making it suitable for curved devices and special-shaped electronic products. This type of Package Substrate has excellent performance in bending and bending, so it is widely used in some electronic products that require curved or curled shapes, such as wearable devices, flexible displays, etc.
In essence, the selection of various types of package substrates should be guided by specific application scenarios and design specifications. Rigid-rigid substrates are well-suited for traditional electronic devices that demand robust structural stability. On the other hand, rigid-flexible substrates are apt for situations with confined space and elevated integration needs. Flexible-flexible substrates find their niche in special electronic products that necessitate flexible and contoured shapes. Through judiciously choosing applicable package substrate types, design engineers can adeptly cater to diverse product design requirements, leading to the creation of more innovative and competitive electronic products.
What are the advantages of Package Substrates?
In contemporary PCB design, Package Substrate emerges as a highly favored choice among design engineers due to its array of superior performance and flexibility when compared to traditional circuit boards. The distinctive advantages of Package Substrate make it an ideal solution for modern PCB design.
Foremost, Package Substrate distinguishes itself with its exceptional flexibility and space efficiency. In contrast to conventional circuit boards, Package Substrate offers heightened adaptability to diverse and intricate design requirements.
This adaptability not only enhances overall design efficiency but also contributes significantly to the successful integration of advanced technologies into compact and space-constrained products. In essence, Package Substrate stands as a cornerstone in the pursuit of miniaturization and enhanced performance in modern electronic designs.
Secondly, Package Substrate also performs well in terms of weight. Compared with rigid circuit boards, Package Substrate uses lighter materials, making the overall product lighter. This means better performance and user experience for portable electronic devices and the aerospace field.
In terms of reliability, Package Substrate also has significant advantages. Its design reduces the number of connection points on a traditional circuit board, thereby reducing potential points of failure. This design makes electronic devices more durable and able to cope with changing environments and usage conditions.
Package Substrate has also made breakthroughs in electrical performance.This makes Package Substrate widely used in the fields of high-performance computing and communications, providing greater innovation space for modern PCB design.
Finally, Package Substrate’s flexibility in the manufacturing process is also one of its strengths. Its multi-layer structure and complex manufacturing process require a high degree of process control, but once mastered, it can meet diverse design needs. This flexibility allows designers to more freely conceive and implement innovative circuit layouts, providing the possibility for differentiated product design.
Overall, Package Substrate is an ideal choice for modern PCB design due to its excellent performance, flexibility and reliability. Its advantages in miniaturization, lightweight, high frequency and high speed provide strong support for the continuous innovation of electronic products. In the future, with the continuous advancement of technology, Package Substrate is expected to demonstrate its unique value in a wider range of application fields.
Why choose Package Substrate?
In today’s increasing development of electronic design, faced with limited space and urgent demand for high integration, Package Substrate, as an advanced choice for circuit boards, stands proudly above many circuit boards with its unique design advantages. Here’s what makes Package Substrate stand out compared to other boards, and how competitive it is in terms of miniaturization and lightweight.
First, Package Substrate’s unique design is reflected in its three-dimensional shape and foldability. Traditional circuit boards are usually rigid and difficult to adapt to complex space requirements, while Package Substrate uses flexible materials that can be flexibly bent and folded. This provides more freedom for layout in a limited space, so that the design of electronic products is no longer constrained by space limitations. Its unique three-dimensional shape allows it to fit into complex structures and provide higher integration for electronic devices.
Secondly, Package Substrate shows significant competitiveness in miniaturization and lightweight. Due to the use of flexible materials, Package Substrate is thinner, lighter and more flexible than rigid circuit boards. This feature enables Package Substrate to provide more innovative possibilities for product design in the design of electronic products, especially in the field of mobile devices with high lightweight requirements. At the same time, foldability allows designers to cleverly integrate circuit boards into mechanical structures, no longer limited to traditional flat designs, further promoting product miniaturization.
In highly integrated application scenarios, the design advantages of Package Substrate are particularly obvious. It can combine rigid and flexible layers to effectively achieve a high degree of circuit integration and improve the performance of electronic products. In addition, the bending performance of Package Substrate also provides the possibility of designing some special shapes, making the product more structurally diverse.
Overall, the reason for choosing Package Substrate over other circuit boards is mainly due to its unique three-dimensional shape and foldability, which allows for more freedom in laying out circuits in limited space and has greater miniaturization and lightweight capabilities. Strong competitiveness. As electronic products continue to pursue design flexibility and performance, Package Substrate will play an increasingly important role in future circuit design.
What is the manufacturing process for Package Substrate?
The production of Package Substrate is a meticulously intricate and sophisticated process, characterized by a series of critical steps. Commencing with the overlay of numerous layers of both rigid and flexible substrates, it culminates in the creation of the ultimate product. Precision and meticulous process control are paramount at every stage to guarantee the superior performance and reliability of the final output. This remarkable manufacturing process demands an acute attention to detail and a commitment to excellence. Let’s delve deeper into the intricacies of this exceptional production process.
Overlay of multiple layers of rigid and flexible substrates
The first step in making Package Substrate is to stack multiple layers of rigid and flexible substrates together. The choice of these substrates depends on design needs and typically includes rigid FR-4 fiberglass sheets and flexible polyimide films. Through precise lamination and positioning, it lays the foundation for subsequent circuit pattern preparation.
Preparation of circuit patterns
Following the completion of substrate lamination, the subsequent crucial phase involves delineating the circuit pattern onto the surface. Typically, this intricate task is accomplished through the utilization of photolithography techniques. These techniques involve applying photosensitive resin to the surface, followed by a series of exposure and development steps to precisely craft the desired circuit pattern. The precision and accuracy achieved during this step wield a direct influence on the ultimate performance of the circuit.
Chemical etching
After the circuit pattern is formed, the next step is the chemical etching stage. Excess material is removed by immersing the substrate in a chemical solution that corrodes unprotected areas. This step ensures that the circuit graphics are visible and guarantees the accuracy and clarity of the circuit.
Blind hole drilling
In order to connect circuits at different levels, blind holes need to be drilled. This step uses high-precision drilling equipment to drill holes through the multi-layer substrate for subsequent metallization and connection.
Metallization
Metalization stands out as a crucial stage in the manufacturing process of Package Substrates. This pivotal step involves the deposition of a conductive layer, typically composed of copper, onto the intricate circuit patterns. Beyond merely facilitating the interconnection of circuits, this metal layer significantly elevates the overall stability and reliability of the entire structural framework. By seamlessly integrating with the circuitry, the plated metal enhances the robustness of the substrate, ensuring optimal performance and longevity.
Process control and inspection
Throughout the manufacturing process, process control is crucial. Maintaining precision requires strict control of each step, including temperature, humidity, chemical concentration, etc. In addition, post-manufacturing inspection steps ensure products meet design specifications and provide superior performance and reliability.
Through this complex and sophisticated manufacturing process, Package Substrate becomes a key component in modern PCB design. Its flexibility, high level of integration, and superior performance are all due to exquisite craftsmanship and strict control of every aspect of the manufacturing process. Behind Package Substrate are the silent efforts of PCB engineers to support innovation.
What are the applications of Package Substrate?
Package Substrate, as an advanced electronic packaging substrate, has extensive and profound applications in electronic product design. Its unique flexibility and performance advantages enable it to play a key role in many fields and drive the pace of innovation.
Its lightweight and flexible characteristics align seamlessly with the contemporary requirements of mobile devices, emphasizing thinness, lightness, and portability, thereby offering extensive possibilities for innovative device design.
In the field of medical equipment, Package Substrate demonstrates a wide array of applications. The demanding nature of medical devices necessitates high reliability and flexibility to accommodate diverse clinical scenarios. Package Substrate’s design features empower it to navigate complex circuit layouts and spatial constraints in medical electronic equipment. Its exceptional performance ensures reliable operation in the challenging medical environment, thereby enhancing the overall efficacy of such equipment.
Aerospace systems, known for their stringent weight and space considerations, also benefit significantly from the utilization of Package Substrate. With its lightweight and flexible properties, Package Substrate becomes an optimal choice for designing highly integrated electronic components.
In the IoT sector, where compact designs are imperative for embedding devices into various objects, Package Substrate’s design proves instrumental. Its ability to implement complex electronic functions in small devices provides ample innovation space for IoT applications, contributing to the advancement and proliferation of this dynamic field.
Overall, Package Substrate is not only widely used in traditional electronic products, but also plays a key role in emerging innovative fields. Its flexibility and performance advantages bring new possibilities to the design of electronic products, promoting the continuous evolution of technology and the expansion of application fields.
How to obtain Package Substrate?
In the pursuit of advanced PCB design and electronic product innovation, access to high-quality Package Substrate is critical. Understanding how to obtain this advanced electronic packaging substrate to meet design needs will be a critical task for design engineers.
First, finding reputable suppliers and manufacturers is the preferred way to obtain Package Substrate. These companies usually have extensive experience and advanced production technology to provide high-quality, standard-compliant Package Substrate. By forming partnerships with these specialist companies, design engineers can ensure that their projects are well supported.
Selecting the right partner for Package Substrate is a critical decision given the multitude of companies in the market. As a distinguished PCB manufacturer, our firm boasts extensive experience, coupled with cutting-edge technology and equipment for Package Substrate production. Our unwavering commitment lies in delivering highly tailored solutions to cater to the diverse design requirements of our clientele.
Technological Prowess: At the forefront of Package Substrate manufacturing, our company leverages advanced production techniques to maintain a leadership position in technology. This ensures that our products consistently outshine competitors in terms of both performance and quality.
By choosing us as a Package Substrate supplier, design engineers can focus on their design work with confidence while enjoying high-quality, reliable substrate support.
In the process of obtaining Package Substrate, cooperation with professional suppliers and manufacturers, especially choosing our company with technology leadership and customization advantages, will bring design engineers a smoother and more successful design experience.
What is the quote for Package Substrate?
Obtaining a Package Substrate quote is a crucial step in PCB design and involves several key factors, with design complexity and material selection being crucial influences. By communicating directly with the manufacturer, you can ensure you receive accurate and applicable quote information.
Design complexity plays a pivotal role in determining the cost of a Package Substrate. The intricacy of the design directly impacts the amount of workmanship and materials required, consequently influencing the final quotation. Elements such as complex circuit layouts, multi-layer stacks, blind vias, and blind buried vias contribute to the manufacturing challenges, thereby affecting the overall cost.
Material selection is another crucial factor influencing Package Substrate quotes. The choice of substrates, copper thicknesses, and metallization methods significantly affects costs. Opting for high-performance, specialty materials often incurs higher expenses, yet proves indispensable in specific application scenarios.
For obtaining accurate quotation information, direct communication with the manufacturer proves to be the most effective approach. Engaging in detailed discussions about project requirements, design specifications, and material selections allows design engineers to gain a comprehensive understanding of potential challenges and cost factors in the manufacturing process. This direct communication minimizes information asymmetries, ensuring that manufacturers fully comprehend the complexity and specific requirements of the design.
Early communication with manufacturers not only aids in obtaining accurate quotes but also helps design engineers assess the feasibility of manufacturing. This proactive approach enables timely adjustments to the design, aligning it with the manufacturing process and minimizing costs. Furthermore, this collaborative approach fosters strong relationships with manufacturers, laying a solid foundation for future projects.
Taken together, obtaining an accurate Package Substrate quote requires the design engineer to fully understand the design requirements of the project, taking into account the complexity of the design and the specificities of the materials selected. By communicating directly with the manufacturer and establishing a cooperative relationship between the two parties, you can ensure that you can obtain feasible and specific quotation information, providing strong support for the successful implementation of the PCB project.
Frequently Asked Questions (FAQs)
What advantages does Package Substrate offer over other circuit boards?
Package Substrate boasts exceptional advantages, such as high bendability, efficient space utilization, lightweight construction, and enhanced reliability. These features make it a preferred choice over traditional PCBs in modern electronic designs.
How is Package Substrate manufactured, particularly concerning the motherboard and substrate layers?
The manufacturing process involves layering rigid and flexible base materials, preparing circuit patterns, chemical etching, blind hole drilling, and metalization. Precision and process control are crucial to ensuring the final product’s performance and reliability, especially concerning the motherboard and substrate layers.
Can you elaborate on the manufacturing process of Package Substrate, especially concerning Motherboard and Substrate layers?
The manufacturing process of Package Substrate involves layering rigid and flexible base materials, preparing circuit patterns, chemical etching, blind hole drilling, and metalization processes. Precision and meticulous control are crucial to ensuring the final product’s performance and reliability, especially in the Motherboard and Substrate layers.
How can one source Package Substrate, and where can it be found?
Package Substrate can be sourced from suppliers and manufacturers specializing in advanced PCB technologies. Reputable companies in the market offer high-quality Package Substrate solutions tailored to different design needs.
What factors influence the pricing of Package Substrate, and how can one obtain a quote?
The pricing of Package Substrate is influenced by factors like design complexity and material selection. Communicating directly with manufacturers is key to obtaining accurate and competitive quotes for Package Substrate.
What are some common concerns addressed in Package Substrate FAQs?
Common concerns addressed include performance considerations, design best practices, and cost-related inquiries. Understanding these FAQs can assist engineers in making informed decisions when incorporating Package Substrate in their PCB designs.
How does the manufacturing process of Package Substrate differ from traditional PCBs?
The manufacturing process involves layering rigid and flexible base materials, preparing circuit patterns, chemical etching, blind hole drilling, and metalization treatments. The precision and control in these processes ensure the final product meets high-performance and reliability standards.
How are Package Substrate quotes determined, and what factors influence the pricing?
Package Substrate quotes are influenced by factors like design complexity, material choices, and manufacturing intricacies. Direct communication with manufacturers is key to obtaining accurate and competitive quotes for specific project needs.
What design considerations should be taken into account when working with Package Substrate?
Designers should consider factors like bending radius, the transition zone between rigid and flexible sections, and interlayer connection methods. These considerations ensure that the Package Substrate performs optimally without stress concentration or mechanical damage.
What is the future outlook for Package Substrate in PCB design and electronics manufacturing?
The future holds the potential for expanded applications of Package Substrate, especially in emerging fields like artificial intelligence and the Internet of Things. Continuous improvements in performance and cost-effectiveness are expected, driving electronics design to new heights.