Organic Packaging Chip Substrates Manufacturer, the Minimum trace/spacing are 9um/9um, from 4 layer to 20 layers ship substrates production. we use the BT, Showa Denko/Ajinomoto high-speed core materials or other kinds core materials to produce the Packaging Chip Substrates.
Organic Packaging Chip Substrates are one of the crucial components in the field of electronic engineering. It plays a key role in connecting and supporting chips, electronic components, and other devices. In short, it is the foundation of electronic devices, providing the necessary support and connections for various functions. But what exactly is its function?
First of all, the organic packaging chip substrate serves as a basic support structure, carrying the layout and connection of various components in electronic equipment. This includes various chips and related components such as microprocessors, memories, sensors, etc. Through the wiring design on the substrate, it connects these components to build the entire circuit system.
Organic packaging chip substrates play a vital role in protecting electronic components by offering structural support and shielding against environmental elements like moisture, dust, and mechanical impact. This protective function not only extends the lifespan of the components but also enhances the overall stability of electronic device operations.
Moreover, organic packaging chip substrates serve as conduits for electronic signal transmission and processing. Through precise circuit design and layout, they facilitate efficient signal propagation, ensuring stability and integrity particularly in high-frequency and high-speed applications. This capability significantly enhances the performance and functionality of various electronic devices.
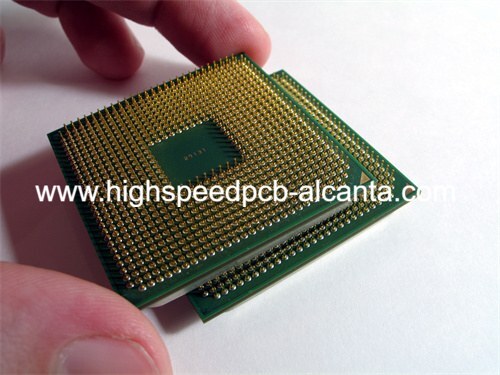
Organic Packaging Chip Substrates Manufacturer
Overall, organic packaging chip substrates are integral to electronic devices, offering multifaceted functions including connection, support, protection, and signal transmission. They establish a robust foundation for the reliable operation of electronic equipment, playing an irreplaceable role in modern electronic engineering.
What types of organic packaging chip substrates are there?
Organic packaging chip substrates play an important role in the electronics field, and different types of substrates are suitable for different application scenarios. Here are three common organic packaging chip substrate types and their characteristics:
HDI (High-Density Interconnect) boards are packaged chip substrates featuring densely packed wiring and smaller pitch. They incorporate multiple layers of stacking, facilitating more connections within a smaller footprint. HDI boards are commonly employed in electronic devices with stringent space constraints and intricate functionalities, including smartphones, tablets, and portable electronics. Their high-density wiring enables complex circuit designs, thereby enhancing circuit performance and signal integrity.
Rigid-Flex boards amalgamate the attributes of rigid and flexible boards, rendering them bendable and foldable. These substrates possess the unique capability of being bent along various planes, making them suitable for electronic devices with unconventional form factors, such as flexible displays and curved electronic products. The flexible nature of Rigid-Flex boards allows for intricate layouts in confined spaces, while reducing connection points and bolstering reliability and stability.
Basic FR4 boards are one of the most common types of organic packaging chip substrates and are typically composed of fiberglass-reinforced epoxy resin. This kind of substrate is widely used in general electronic equipment, such as household appliances, industrial control systems, etc. The basic FR4 board has good mechanical strength and heat resistance, and is suitable for general circuit design and ordinary wiring requirements. It is relatively low-cost to manufacture and is one of the preferred substrate materials for many electronic products.
Different types of organic packaging chip substrates have their own characteristics in terms of design, application and cost. HDI boards are suitable for equipment with high space and performance requirements, Rigid-Flex boards are suitable for products that require bending and foldable designs, and basic FR4 boards are common substrate materials for general electronic equipment. Selecting the appropriate substrate type depends on specific application needs and design considerations.
Why choose organic packaging chip substrate?
In today’s electronics manufacturing industry, organic packaging chip substrates are highly favored as key components. The reason why they are the first choice has many unique advantages.
First of all, organic packaging chip substrates have a high degree of flexibility and plasticity in design. Compared with traditional rigid substrates, organic packaging chip substrates can achieve more complex wiring designs and more compact component layouts, thereby achieving higher density circuit connections. This flexibility means designers can better adapt to the needs of different devices and achieve more diverse electronic product designs.
Organic packaging chip substrates offer excellent signal integrity, achieved through advanced manufacturing processes and material technologies. They minimize signal loss and interference, ensuring stable transmission of circuit signals. This is especially critical for high-performance electronic equipment, ensuring both performance and stability, thereby enhancing product competitiveness.
Moreover, organic packaging chip substrates present a cost-effective solution. Compared to materials like ceramic or metal substrates, their manufacturing costs are lower. This appeals to electronic manufacturers, as it reduces production expenses and enhances product market competitiveness while maintaining quality standards.
Moreover, organic packaging chip substrates exhibit exceptional reliability and durability. With inherent resistance to heat and corrosion, they can operate dependably in a wide range of challenging environments. This positions them as the favored choice for critical applications in aerospace, medical, and military sectors.
To sum up, the multitude of benefits offered by organic packaging chip substrates, including flexibility, signal integrity, cost-effectiveness, and reliability, has established them as the preferred option in the electronics manufacturing industry. Their extensive use across diverse fields and ongoing innovative advancements will continue to drive the electronics industry forward, making positive contributions to scientific and technological advancements in society.
How are organic packaging chip substrates made?
Organic Packaging Chip Substrates, as integral components of contemporary electronic devices, undergo a meticulously structured manufacturing process to ensure adherence to quality and performance standards. The manufacturing process is outlined in detail below:
Design Phase:The initial step involves the design team creating precise drawings based on customer specifications, taking into account details such as board size, hierarchical layout, and circuit connections.
Material Selection:After the design phase, manufacturers opt for suitable materials for constructing organic packaging chip substrates. Common choices include fiberglass-reinforced epoxy resin (FR4) owing to its commendable insulation properties and mechanical strength.
Layering:Once the design and material selection are settled, layers of assorted materials are arranged according to the design specifications. The layering process ensures accurate alignment and thickness of each layer, thereby enhancing the overall quality and performance of the end product.
Shaping: Following layering, the arranged materials undergo shaping through the application of heat and pressure within a mold to achieve the desired form. This stage guarantees a robust connection between the layers.
Manufacturing:After shaping, the substrate undergoes a series of manufacturing processes such as cutting, punching, milling, etc., to achieve the final product according to the design specifications.
Quality Control and Validation:Thorough examination and validation are conducted at each stage of the production process. This includes assessing raw materials, inspecting the results after shaping, and performing functional tests on the final product to guarantee compliance with quality criteria and customer requirements.
Surface Treatment:The organic packaging chip substrate undergoes surface treatment to enhance corrosion resistance and welding performance. Common methods include tin spraying, lead spraying, etc.
By meticulously following these key steps, manufacturers produce organic packaging chip substrates, establishing a reliable foundation for the production of diverse electronic devices. Each stage in the manufacturing process is critical, and stringent control and management are essential to ensure product stability and reliability, as any negligence in any stage can impact the final product’s quality and performance.
In what fields are organic packaging chip substrates used?
Organic Packaging Chip Substrates, as an important component in electronic manufacturing, are widely used in various fields. The following are its typical fields and application scenarios in practical applications:
In the domain of communication equipment, organic packaging chip substrates find extensive use in base stations, routers, modems, and similar devices. Given the complex nature of signals and data transmission involved in these systems, organic packaging chip substrates offer excellent signal integrity and high-density wiring, thereby ensuring the stability and reliability of communication equipment.
Organic packaging chip substrates are essential components in medical devices, particularly in equipment like medical monitors and imaging devices. These devices rely on high-performance electronic components to acquire and process data effectively. Organic packaging chip substrates are designed to meet the stringent demands of medical equipment, offering high-density wiring to accommodate complex circuitry while ensuring signal integrity. Moreover, they contribute to the stability and safety of the equipment, fulfilling critical roles in maintaining the reliability and functionality of medical devices used in healthcare settings.
Beyond consumer electronics, communication equipment, and medical devices, organic packaging chip substrates are widely employed in fields like automotive electronics and industrial control. Whether it’s intelligent driving systems or industrial automation equipment, these applications heavily rely on high-performance electronic components and stable, reliable circuit boards—where organic packaging chip substrates stand out as vital components providing essential support for these industries.
Its wide application in various fields such as consumer electronics, communication equipment, and medical equipment provides the design and manufacturing of various electronic equipment. Reliable technical support.
How to obtain organic packaging chip substrate?
Want to obtain organic packaging chip substrates, you may ask: What are the ways to obtain them? How to contact organic packaging chip substrate manufacturers? In addition, through which electronic parts suppliers can I obtain related products?
There are multiple pathways for obtaining organic packaging chip substrates. One avenue involves direct engagement with specialized manufacturers of these substrates, offering the advantage of tailored solutions. Engaging directly with such manufacturers allows access to detailed information on product specifications, customization options, pricing, as well as additional technical support and after-sales services. This direct approach ensures a comprehensive understanding of the product and facilitates seamless project execution.
Alternatively, for a broader range of options, electronic parts suppliers can serve as a viable choice. Many of these suppliers maintain partnerships with various manufacturers, providing a diverse product selection and flexible procurement options. Engaging with electronic parts suppliers allows for learning about product availability, pricing structures, and delivery timelines through their online platforms, websites, or dedicated sales representatives, facilitating convenient ordering based on specific project requirements.
In conclusion, obtaining organic packaging chip substrates is a simple process. Whether you contact manufacturers directly or work with electronic parts suppliers, finding the right products is readily achievable. As your supplier, we are committed to supporting your project and ensuring its success.
How is the quotation of organic packaging chip substrate formed?
The quotation of organic packaging chip substrate is formed by comprehensive consideration of many factors, among which factors such as design complexity, material cost and manufacturing process play a crucial role.
Design complexity stands as a pivotal determinant in the pricing of organic packaging chip substrates. It encompasses factors such as circuit layout intricacy, hierarchical structure, and board specifications. More intricate designs necessitate advanced processes and technologies, thereby escalating manufacturing expenses. For instance, designs requiring high-density wiring and multi-layer structures mandate the adoption of sophisticated processes and equipment, directly influencing the final quotation.
Material cost represents another significant aspect determining the pricing of organic packaging chip substrates. Variations in substrate materials across different types of organic packaging chip substrates lead to cost discrepancies. High-density interconnect (HDI) boards, for instance, often incorporate high-performance substrate materials, which incur relatively higher costs. Moreover, special surface treatment techniques and copper coating thickness further contribute to material expenses.
Additionally, the manufacturing process plays a crucial role in shaping the quotation of organic packaging chip substrates. This process involves multiple stages including lamination, etching, and copper plating, each consuming resources like manpower, equipment, and energy, thereby directly impacting manufacturing costs. Particularly, flexible substrates or boards necessitating intricate surface treatments undergo a more complex manufacturing process, resulting in elevated costs.
What are Frequently Asked Questions (FAQs)?
What are organic packaging chip substrates and their primary functions?
Organic packaging chip substrates serve as fundamental components in electronic devices, providing support and connectivity for chips, electronic components, and other devices. They form the backbone of modern electronic systems.
How can one obtain organic packaging chip substrates?
Organic packaging chip substrates can be acquired through direct contact with manufacturers or through electronic component suppliers. By liaising with these sources, one can obtain the desired products tailored to specific project requirements.
What factors influence the pricing of organic packaging chip substrates?
Pricing for organic packaging chip substrates is influenced by factors such as design complexity, material costs, manufacturing processes, and order quantities. Understanding these factors helps in obtaining competitive pricing for projects.
What exactly is an Organic Packaging Chip Substrate?
An Organic Packaging Chip Substrate serves as a fundamental component in electronic devices, but what specific role does it play? This section aims to provide a comprehensive understanding of its core functionality.
What advantages do Organic Packaging Chip Substrates offer?
Delve into the advantages that make Organic Packaging Chip Substrates stand out. From high-density wiring to excellent signal integrity and cost-effectiveness, what specific benefits do they bring to the table?