Multilayer Load PCB Manufacturer.multi-layered printed circuit boards designed to handle substantial electrical loads. Our state-of-the-art manufacturing process ensures precision and reliability, making our PCBs ideal for demanding applications in industries such as telecommunications, automotive, and consumer electronics. By integrating advanced materials and innovative design techniques, we provide robust solutions that meet the rigorous performance and durability standards of modern electronic systems.
Multilayer Load Printed Circuit Boards (PCBs) are a vital component in modern electronics, enabling complex circuitry and enhanced performance in compact forms. These PCBs are designed to handle high electrical loads and multiple functions, making them indispensable in various high-performance applications. This article explores the concept, structure, materials, manufacturing process, applications, and advantages of Multilayer Load PCBs.
What is a Multilayer Load PCB?
A Multilayer Load PCB is a type of printed circuit board that consists of multiple layers of conductive material, typically copper, separated by insulating materials. These layers are laminated together to form a single, compact board that can support complex circuits and high electrical loads. Multilayer Load PCBs are used in applications where space is limited, and high performance is required, such as in telecommunications, aerospace, medical devices, and advanced computing.
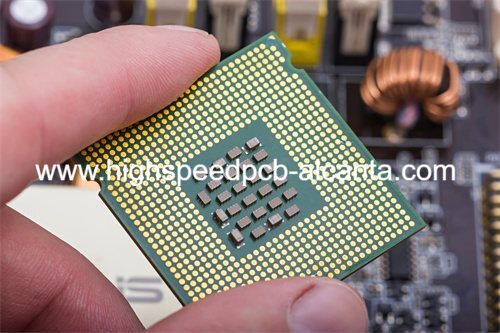
Multilayer Load PCB Manufacturer
Multilayer Load PCBs are characterized by their ability to integrate numerous electronic components and interconnections within a confined space. This integration allows for enhanced functionality, improved signal integrity, and reduced electromagnetic interference (EMI). These PCBs are essential for applications that demand high reliability, performance, and miniaturization.
Structure of Multilayer Load PCBs
The structure of Multilayer Load PCBs is designed to accommodate multiple layers of conductive and insulating materials, enabling complex circuitry and high electrical load handling. Key structural elements include:
The core of a Multilayer Load PCB is typically made of a rigid material such as FR4, polyimide, or a high-performance composite. This core provides mechanical support and stability for the entire board.
Multiple layers of conductive material, usually copper, are laminated onto the core. These layers form the electrical pathways that interconnect the various components and circuits on the board. The number of layers can range from four to over a dozen, depending on the complexity of the design.
Dielectric layers made of insulating materials like epoxy resin, prepreg (pre-impregnated fiberglass), or advanced polymers are placed between the conductive layers. These layers provide electrical insulation and help maintain signal integrity by reducing crosstalk and EMI.
Vias (vertical interconnect access) and microvias are used to create electrical connections between different layers of the PCB. These features are critical for maintaining the electrical continuity and integrity of the multilayer circuit.
A surface finish such as ENIG (Electroless Nickel Immersion Gold), HASL (Hot Air Solder Leveling), or OSP (Organic Solderability Preservative) is applied to the external layers. This finish enhances solderability and protects the conductive traces from oxidation and corrosion.
A protective solder mask is applied to the surface of the PCB to prevent solder bridges and protect the underlying circuits from environmental damage.
Materials Used in Multilayer Load PCBs
The choice of materials for Multilayer Load PCBs is crucial to their performance and reliability. Key materials include:
High-performance core materials such as FR4, polyimide, and composite materials are used for their excellent thermal stability, mechanical strength, and electrical insulation properties.
Copper is the most commonly used conductive material due to its high electrical conductivity and thermal performance. In some cases, other metals like gold or silver may be used for specific applications requiring higher conductivity or corrosion resistance.
Advanced dielectric materials such as epoxy resins, prepreg, and liquid crystal polymers (LCP) are used to insulate the conductive layers. These materials ensure low dielectric loss and high thermal stability.
Various surface finishes like ENIG, HASL, and OSP are used to enhance solderability and protect the conductive traces from oxidation. The choice of surface finish depends on the specific requirements of the application.
Solder masks made of epoxy or liquid photoimageable (LPI) materials are applied to protect the PCB surface and prevent solder bridges during the assembly process.
The Manufacturing Process of Multilayer Load PCBs
The manufacturing process of Multilayer Load PCBs involves several precise and controlled steps to ensure high quality and performance. Key steps include:
The design phase involves creating detailed schematics and layouts using computer-aided design (CAD) software. Prototypes are then fabricated to validate the design and test for performance and reliability.
High-quality raw materials, including core materials, copper foils, and dielectric materials, are prepared and inspected to ensure they meet the required specifications.
The core material and copper foils are laminated together using heat and pressure to form a unified multilayer structure. This step involves precise alignment and control to ensure the layers are properly bonded.
Vias and microvias are drilled into the PCB to create vertical electrical interconnections. These holes are then plated with copper to establish conductive pathways.
The circuit patterns are created using photolithographic processes. This involves applying a photosensitive film (photoresist) to the copper surface, exposing it to ultraviolet (UV) light through a mask, and developing the exposed areas to reveal the desired circuit patterns. The PCB is then etched to remove the unwanted copper, leaving behind the circuit traces.
Dielectric layers are applied to insulate the conductive layers. This step involves coating the PCB with a dielectric material and curing it to form a solid layer.
Surface finishes such as ENIG, HASL, or OSP are applied to the contact pads to improve solderability and protect against oxidation. These finishes are applied using plating or immersion techniques.
The final PCBs undergo rigorous inspection and testing to ensure they meet all performance and reliability standards. Electrical testing, visual inspection, and automated optical inspection (AOI) are used to identify any defects or irregularities.
Application Areas of Multilayer Load PCBs
Multilayer Load PCBs are used in a wide range of electronic applications across various industries. Key application areas include:
Multilayer Load PCBs are essential in telecommunications equipment, such as base stations, routers, and switches. Their ability to handle high electrical loads and complex circuitry ensures reliable and efficient communication.
In the aerospace industry, these PCBs are used in avionics, navigation systems, and communication devices. The high-performance materials and multilayer structure provide the necessary reliability and durability for demanding aerospace applications.
Multilayer Load PCBs are used in medical devices, such as diagnostic equipment, imaging systems, and patient monitoring devices. The ability to integrate complex circuits in a compact form factor makes them ideal for advanced medical technologies.
In the automotive industry, these PCBs are used in engine control units, infotainment systems, and advanced driver-assistance systems (ADAS). The robust design and high load handling capability ensure reliable performance in harsh automotive environments.
Multilayer Load PCBs are critical in high-performance computing applications, such as servers, data centers, and supercomputers. The ability to handle high electrical loads and complex circuitry supports the demanding computational requirements of these systems.
Advantages of Multilayer Load PCBs
Multilayer Load PCBs offer several advantages that make them indispensable for modern electronic applications. These advantages include:
The multilayer structure allows for the integration of complex circuits in a compact form factor, enabling the miniaturization of electronic devices without compromising performance.
Multilayer Load PCBs are designed to handle high electrical loads, making them suitable for applications that require high power and performance.
The use of advanced dielectric materials and precise circuit patterning techniques ensures minimal signal loss and crosstalk, providing accurate and reliable performance.
The multilayer design allows for better distribution of heat, preventing overheating and ensuring reliable operation under high electrical loads.
The rigorous manufacturing process and high-quality materials ensure that Multilayer Load PCBs meet stringent performance and reliability standards, reducing the risk of failures in real-world applications.
FAQ
What materials are commonly used in the manufacturing of Multilayer Load PCBs?
Common materials used in the manufacturing of Multilayer Load PCBs include high-performance core materials such as FR4, polyimide, and composite materials, conductive materials like copper, advanced dielectric materials such as epoxy resins and prepreg, and surface finishes like ENIG, HASL, and OSP. These materials provide the necessary thermal stability, electrical performance, and mechanical strength for high-performance applications.
How do Multilayer Load PCBs improve thermal management in electronic devices?
Multilayer Load PCBs improve thermal management by using high-performance materials and advanced manufacturing techniques to ensure efficient heat dissipation. The multilayer structure allows for better distribution of heat, preventing overheating and ensuring reliable operation under high electrical loads.
Can Multilayer Load PCBs be used in medical devices?
Yes, Multilayer Load PCBs are highly suitable for medical devices. They are used in diagnostic equipment, imaging systems, and patient monitoring devices to integrate complex circuits in a compact form factor. The high reliability and performance of these PCBs support advanced medical technologies.
What are the key advantages of using Multilayer Load PCBs in telecommunications equipment?
The key advantages of using Multilayer Load PCBs in telecommunications equipment include high electrical load handling, enhanced signal integrity, compact design, improved thermal management, and increased reliability. These advantages ensure reliable and efficient communication in demanding telecommunications applications.